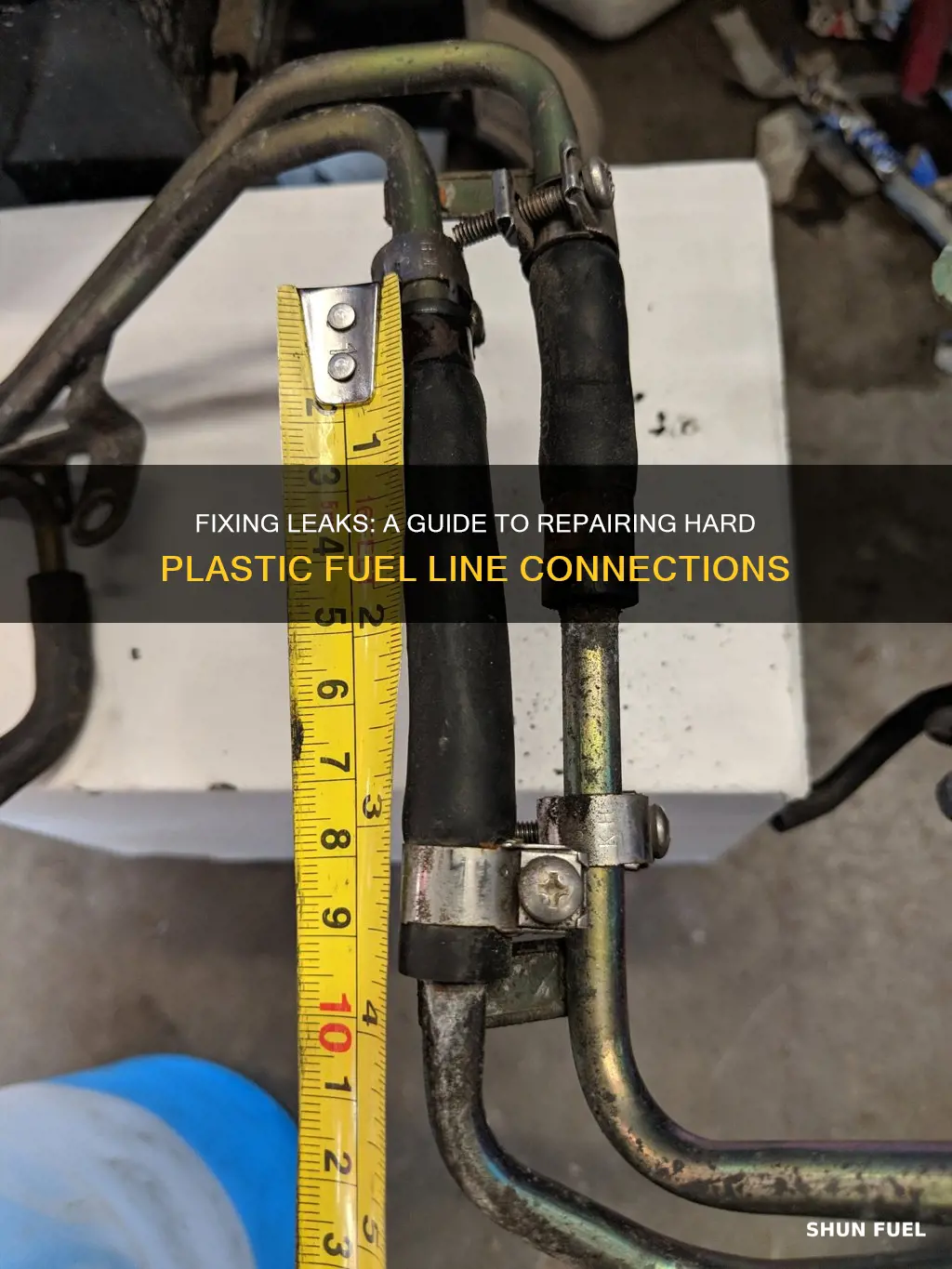
Hard plastic fuel lines are a common component in vehicle fuel systems, but they can be prone to leaking over time due to various factors such as age, wear, and environmental damage. Repairing these connections is a crucial task for vehicle owners and mechanics alike to ensure the vehicle's performance and safety. This guide will provide a step-by-step approach to repairing leaking hard plastic fuel line connections, covering essential tools, materials, and techniques to effectively stop the leak and restore the fuel system's integrity.
What You'll Learn
- Identify Leaks: Inspect fuel lines for cracks, brittleness, or damage
- Clean Connections: Remove old fuel and debris from the connection
- Replace Fittings: Use new fittings and secure with appropriate torque
- Reinforce Lines: Wrap lines with heat shrink sleeves for added protection
- Test System: Ensure no leaks by running a pressure test
Identify Leaks: Inspect fuel lines for cracks, brittleness, or damage
When dealing with hard plastic fuel line connections that are leaking, the first and most crucial step is to identify the source of the leak. This requires a thorough visual inspection of the fuel lines and their connections. Start by examining the fuel lines for any visible signs of damage, cracks, or brittleness. Hard plastic fuel lines can deteriorate over time due to various factors, including age, exposure to heat, and chemical degradation. Look for any discolored or softened areas along the length of the line, as these could indicate areas of weakness or potential failure.
Pay close attention to the connections between the fuel lines and any fittings or adapters. Leaks often occur at these interfaces due to improper installation, corrosion, or material fatigue. Inspect the connections for any signs of leakage, especially around the O-rings or gaskets that seal these joints. Look for any visible damage, such as cracks or tears, in these sealing components. Additionally, check for any signs of corrosion or oxidation on the metal fittings, as this can weaken the connection and lead to leaks.
During your inspection, take note of any areas where the fuel lines are routed through engine compartments or under vehicles. These areas can be prone to physical damage from vibrations, impacts, or rubbing against other components. Inspect these sections carefully for any signs of wear and tear, such as frayed or damaged lines. It's also important to check for any signs of fuel contamination or accumulation, as this can indicate a more serious issue with the fuel system.
If you notice any cracks, brittleness, or damage during your inspection, it's essential to address these issues promptly. Leaks can lead to fuel loss, potential engine damage, and even safety hazards. If the damage is minor, you may be able to repair the fuel line by replacing the affected section or using specialized repair kits designed for hard plastic fuel lines. However, if the damage is extensive or the line is severely compromised, it is best to consult a professional mechanic or automotive specialist for guidance and potential replacement.
Remember, regular maintenance and inspections are key to preventing and addressing issues with hard plastic fuel line connections. By identifying leaks early and taking appropriate action, you can ensure the reliability and safety of your vehicle's fuel system.
Chevy Silverado Fuel Line: 2008 Model Size Guide
You may want to see also
Clean Connections: Remove old fuel and debris from the connection
When dealing with leaking hard plastic fuel line connections, a crucial step in the repair process is ensuring that the connections are clean and free from debris. This step is often overlooked but is essential to ensure a proper and long-lasting fix. Here's a detailed guide on how to clean and prepare the connections:
Step 1: Identify the Leaking Connection
Start by identifying the specific fuel line connection that is leaking. This could be a coupling, a quick-connect fitting, or a clamp. Locate the damaged area and inspect it for any signs of wear, cracks, or debris accumulation. Understanding the source of the leak is the first step towards an effective repair.
Step 2: Remove Old Fuel and Debris
- Drain the Fuel Line: Before cleaning, it is imperative to remove any old fuel from the line to prevent contamination during the cleaning process. Start by draining the fuel from the vehicle's tank. This can be done by using a fuel pump or by gravity, depending on the vehicle's setup. Ensure you follow safety precautions and wear protective gear when handling fuel.
- Rinse the Connection: Once the fuel is drained, use a high-pressure rinse to flush out any remaining fuel and debris from the fuel line. This step ensures that no contaminants remain, which could interfere with the repair. You can use a garden hose with a spray nozzle for this purpose, ensuring you direct the water flow carefully to avoid any damage to the surrounding components.
- Debris Removal: After rinsing, use a small brush or a specialized fuel line cleaning tool to manually remove any stubborn debris or old fuel residue. Pay close attention to the threads, seals, and O-rings, as these areas are prone to collecting debris. Ensure that all surfaces are clean and free from any foreign matter.
Step 3: Inspect and Prepare for Repair
After cleaning, take a moment to inspect the connection thoroughly. Check for any remaining signs of damage or wear that may have contributed to the leak. Ensure that all surfaces are smooth and free from contaminants, as this will allow for a better seal during the repair process. This preparation step is vital to ensure the success of the repair and prevent future leaks.
By following these steps, you can effectively clean the fuel line connections, removing old fuel and debris, and creating a suitable environment for a successful repair. This process is a critical aspect of maintaining a reliable fuel system and should be given careful attention.
F250 Superduty Fuel Line Dimensions: 1999 Model Year Specs
You may want to see also
Replace Fittings: Use new fittings and secure with appropriate torque
When dealing with leaking hard plastic fuel line connections, replacing the fittings is often the most effective solution. This process involves removing the old fittings and installing new ones to ensure a secure and leak-free connection. Here's a step-by-step guide to help you through this repair:
Step 1: Gather the Necessary Tools and Materials
Before you begin, ensure you have the required tools and materials. You'll need a new set of fittings specifically designed for your fuel line, as well as a torque wrench to apply the correct amount of force during installation. It's crucial to use fittings that are compatible with your fuel line material to avoid any potential issues.
Step 2: Disconnect the Fuel Line
Carefully disconnect the fuel line from the existing fittings. Take note of the positioning of the fuel line and any related components to ensure you can reconnect them correctly after the repair. Use the appropriate tools to loosen the fittings and carefully separate the fuel line from the old fittings.
Step 3: Remove the Old Fittings
Once the fuel line is disconnected, remove the old fittings by unscrewing or unclipping them. Be gentle to avoid damaging the surrounding areas. Inspect the fittings for any signs of damage or wear that may have contributed to the leak.
Step 4: Prepare the New Fittings
Take the new fittings and ensure they are clean and free of any debris. Check the fittings for any manufacturing defects or damage. If any issues are found, replace the fittings with new ones. Ensure that the new fittings are the correct size and type for your fuel line.
Step 5: Install the New Fittings
Now, carefully slide the new fittings over the fuel line, ensuring a snug fit. Use the torque wrench to apply the specified torque to each fitting. This step is crucial to guarantee a secure connection. Apply the torque in a clockwise direction, tightening the fittings until they are finger-tight. Avoid over-tightening to prevent damage to the fuel line.
Step 6: Reconnect the Fuel Line
After securing the new fittings, reconnect the fuel line to the fittings. Ensure that the fuel line is properly aligned and securely attached. Tighten any connections using the appropriate tools, being careful not to overtighten.
By following these steps, you can effectively replace the fittings and secure the hard plastic fuel line connections, eliminating the leak and ensuring a reliable fuel supply. Remember to take your time and be meticulous during the process to avoid any further issues.
Unveiling the Causes: Why Fuel Line Leaks Happen
You may want to see also
Reinforce Lines: Wrap lines with heat shrink sleeves for added protection
When dealing with leaking hard plastic fuel lines, one effective method to ensure a secure and long-lasting repair is by reinforcing the lines with heat shrink sleeves. This technique provides an additional layer of protection and strengthens the connection, reducing the chances of future leaks. Here's a step-by-step guide on how to achieve this:
Start by ensuring you have the necessary tools and materials, including heat shrink sleeves, a heat gun or hairdryer, and a sharp utility knife or wire cutter. Clean the fuel line connection thoroughly to remove any dirt, debris, or old adhesive. This step is crucial for a successful repair. Once the area is clean, apply a small amount of fuel line adhesive or tape to the inside of the heat shrink sleeve, being careful not to use too much to avoid excess material. Slide the heat shrink sleeve over the fuel line, ensuring it covers the entire connection, including the threads and any damaged areas. The sleeve should be snugly fitted, providing a tight seal.
Now, it's time to apply heat. Use a heat gun or a high-setting hairdryer to heat the shrink sleeve. Move the heat source along the length of the sleeve, ensuring an even distribution of heat. The heat will cause the sleeve to shrink and conform tightly to the fuel line. Be cautious not to overheat the plastic, as it can become brittle and crack. Allow the sleeve to cool slightly before handling to ensure it remains in place. Once cooled, the sleeve will provide a robust and flexible barrier, protecting the fuel line from potential damage and leaks.
This method is particularly useful for hard-to-reach areas or when the fuel line is exposed to harsh conditions. The heat shrink sleeve acts as a protective barrier, preventing corrosion and physical damage. It also provides a smooth, seamless surface, reducing the risk of fuel contamination. Remember, this technique is a temporary fix, and for long-term solutions, professional advice should be sought to ensure the underlying issues are addressed.
Dodge Truck Fuel Line Sizes: A Comprehensive Guide
You may want to see also
Test System: Ensure no leaks by running a pressure test
When dealing with hard plastic fuel line connections that have developed leaks, a crucial step in the repair process is to ensure that the system is leak-free before reassembling it. This involves a pressure test, which is a comprehensive method to verify the integrity of the fuel lines and connections. Here's a detailed guide on how to perform this test:
Prepare the Test Setup: Begin by setting up a test system that mimics the actual fuel line configuration. This may involve using a test bench or a temporary setup that includes the fuel pump, fuel lines, and the engine's fuel injection system (if applicable). Ensure that the test setup accurately represents the vehicle's fuel system to get reliable results.
Connect the Test Equipment: Attach pressure gauges to the fuel lines at various points, including the connections you suspect might be leaking. These gauges will measure the pressure within the system. Additionally, set up a method to introduce pressure into the system, such as a hand pump or an air compressor, to simulate the fuel pump's operation.
Apply Pressure and Monitor: Gradually increase the pressure in the system while monitoring the gauge readings. Start with a low pressure and slowly build it up to a level that represents normal operating conditions. Keep an eye on the pressure at the connection points, especially the areas where leaks have been observed. If a leak is present, you should notice a drop in pressure or a visible sign of fuel escaping.
Check for Visual Signs of Leaks: While applying pressure, also inspect the fuel lines and connections for any visual indicators of leaks. Look for fuel seepage, wet spots, or any signs of fuel escaping from the connections or along the lines. This visual inspection, combined with the pressure test, will help identify the exact locations of the leaks.
Record and Document: Document the pressure readings and visual observations. Note the pressure at which leaks are detected and the specific locations of the issues. This documentation will be valuable for troubleshooting and ensuring that all leaks are addressed during the repair process.
By following this pressure test procedure, you can effectively identify and locate any remaining leaks in the hard plastic fuel line connections. This step is essential to guarantee a successful repair, ensuring that the fuel system is safe and reliable once the connections are reassembled.
Fuel Line Options for 2009 Silverado: Who's the Best Supplier?
You may want to see also
Frequently asked questions
Leaks in hard plastic fuel lines can be identified by visual inspection. Look for any signs of damage, cracks, or brittleness along the line, especially where it connects to the fuel tank, pump, or engine. You may also notice fuel stains or a hissing sound near the connection points.
Hard plastic fuel lines can deteriorate over time due to various factors. UV radiation from the sun, extreme temperatures, and chemical degradation from fuel can all contribute to the breakdown of the plastic. Additionally, physical damage from vibrations, impacts, or improper installation can lead to cracks and leaks.
Minor leaks can often be temporarily fixed with a fuel line clamp or by wrapping the damaged area with electrical tape. However, for more severe damage or if you're unsure about the repair process, it's recommended to consult a professional mechanic. They have the expertise and tools to ensure a proper and safe repair.
Regular maintenance and inspections can help prevent fuel line leaks. Check the fuel lines for any signs of damage during routine engine inspections. Keep the fuel tank and lines clean to prevent contamination. Ensure that all connections are secure and properly tightened. Using fuel line protectants or covers can also provide an extra layer of protection against UV damage and extreme temperatures.