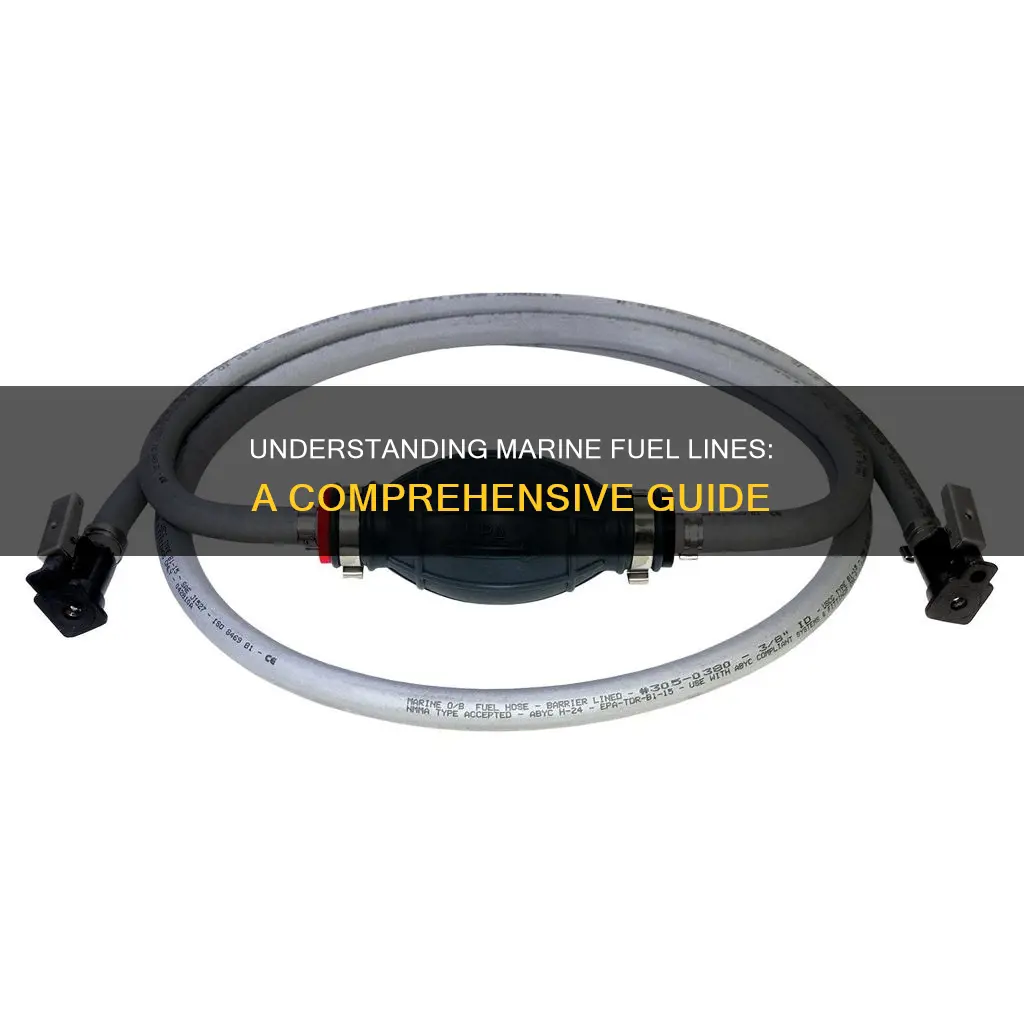
Marine fuel lines are an essential component of any vessel's propulsion system, responsible for transporting fuel from the storage tank to the engine. These lines are designed to withstand the harsh marine environment, including exposure to saltwater, corrosion, and varying temperatures. They are typically made from durable materials such as high-density polyethylene (HDPE) or polypropylene, which offer excellent resistance to abrasion and chemical degradation. The fuel lines are often equipped with specialized fittings and connectors to ensure a secure and leak-free connection, allowing for efficient and reliable fuel delivery to the engine. Understanding the specifications and requirements of marine fuel lines is crucial for maintaining the performance and safety of marine vessels.
What You'll Learn
- Marine Fuel Line Materials: Materials used for fuel lines in boats, such as rubber or plastic
- Fuel Line Routing: Proper installation and routing techniques for marine fuel lines
- Fuel Line Maintenance: Regular care and inspection to prevent leaks and ensure safety
- Fuel Line Fittings: Types of connectors and fittings used in marine fuel systems
- Fuel Line Pressure: Understanding pressure requirements and testing for marine fuel lines
Marine Fuel Line Materials: Materials used for fuel lines in boats, such as rubber or plastic
The choice of material for marine fuel lines is crucial for ensuring the safe and efficient operation of a boat's fuel system. These lines are responsible for transporting fuel from the tank to the engine, and the material used directly impacts performance and longevity. Rubber and plastic are the primary materials used for this purpose, each offering distinct advantages.
Rubber is a traditional and widely used material for marine fuel lines. It is known for its flexibility, which is essential for accommodating the vibrations and movements inherent in a boat's environment. Rubber fuel lines can absorb shocks and vibrations, reducing the risk of damage to the fuel system. Additionally, rubber is resistant to many chemicals, including those found in fuel, which helps prevent degradation and ensures the line's longevity. This material is also relatively easy to install and can be joined using various methods, making it a popular choice for boat owners and mechanics.
On the other hand, plastic fuel lines have gained popularity due to their lightweight and corrosion-resistant properties. Plastic lines are often made from materials like PVC (polyvinyl chloride) or nylon, which offer excellent chemical resistance, ensuring that the fuel remains pure and free from contamination. This is particularly important in marine environments where fuel can be exposed to various chemicals and UV radiation. Plastic lines are also more flexible than rigid metal lines, making them easier to route through a boat's confined spaces. Furthermore, plastic fuel lines are often more cost-effective, especially for larger vessels, as they can be lighter and require less material.
When selecting a material, boat owners and marine engineers must consider factors such as the type of fuel used, the operating conditions, and the overall design of the fuel system. Rubber fuel lines are ideal for boats that require flexibility and are often used in smaller vessels or those with more traditional fuel systems. Plastic lines, with their superior chemical resistance and lightweight nature, are well-suited for modern boats, especially those with high-performance engines or those operating in harsh marine environments.
In summary, the choice between rubber and plastic for marine fuel lines depends on the specific requirements of the boat and its fuel system. Both materials have their advantages, and understanding these can help ensure the optimal performance and safety of a boat's fuel supply. It is essential to consider the unique challenges of marine environments when selecting materials to guarantee the reliability and longevity of the fuel line system.
Poulan PP3516AVX Fuel Line Length: Expert Guide
You may want to see also
Fuel Line Routing: Proper installation and routing techniques for marine fuel lines
Marine fuel lines are an essential component of any vessel's fuel system, responsible for transporting fuel from the storage tank to the engine(s). Proper installation and routing of these lines are critical to ensure efficient and safe operation, as well as to prevent potential issues such as fuel contamination, leaks, and performance degradation. Here's an overview of the key considerations and techniques for fuel line routing:
Material Selection: Choose the right material for the fuel lines based on the type of fuel and operating conditions. Common materials include rubber, vinyl, and synthetic compounds that are resistant to fuel degradation. Ensure the material meets industry standards and is compatible with the fuel type to avoid any adverse reactions.
Diameter and Length: The fuel line diameter should be appropriate for the expected fuel flow rate. A larger diameter line can handle higher volumes, reducing pressure drop and ensuring a steady supply. Measure the length of the line required, considering the distance from the fuel tank to the engine and any potential bends or turns.
Routing Techniques: Proper routing is crucial to prevent damage and ensure optimal performance. Here are some guidelines:
- Keep the lines away from hot surfaces, exhaust systems, and areas prone to vibration to avoid heat damage and potential leaks.
- Route the lines in a straight line as much as possible to minimize bends, which can restrict flow and cause pressure drops.
- Use flexible hoses for easier installation and to accommodate engine movement.
- Secure the lines using appropriate clamps or ties to prevent tangling and ensure they remain in place during operation.
- Consider using a fuel line protector or shield to guard against potential impacts or damage.
Installation Process:
- Start by cleaning the fuel tank and lines to remove any contaminants.
- Inspect the lines for any defects or damage before installation.
- Route the lines carefully, following the manufacturer's guidelines and best practices.
- Ensure all connections are secure and tight to prevent fuel leaks.
- Test the system by starting the engine and monitoring for any unusual noises or fuel supply issues.
Maintenance and Inspection: Regular maintenance is essential to keep the fuel lines in optimal condition. Inspect the lines periodically for signs of wear, cracks, or damage. Check for any fuel leaks and ensure the system is free from debris or contaminants. Proper maintenance will extend the life of the fuel lines and ensure reliable fuel supply.
By following these installation and routing techniques, marine vessel owners and operators can ensure a reliable and efficient fuel system, contributing to the overall performance and longevity of their vessels. Proper fuel line management is a critical aspect of marine maintenance, often overlooked but essential for safe and cost-effective operation.
Fuel Filter Lines: Understanding the Connections and Their Roles
You may want to see also
Fuel Line Maintenance: Regular care and inspection to prevent leaks and ensure safety
The marine fuel line is a critical component of any vessel's fuel system, responsible for transporting fuel from the storage tank to the engine. It is a network of pipes, valves, and fittings that must be maintained to ensure the safe and efficient operation of the vessel. Regular maintenance and inspection of the fuel line are essential to prevent leaks, which can lead to hazardous situations and costly repairs.
One of the primary reasons for regular fuel line maintenance is to identify and address potential issues before they become major problems. Over time, fuel lines can develop cracks, corrosion, or damage from marine life, such as barnacles or algae. These issues can lead to fuel leaks, which may go unnoticed until it's too late. Regular inspections can help detect these problems early on, allowing for prompt repairs or replacements.
Maintenance routines should include a thorough visual inspection of the fuel lines. Look for any signs of damage, such as cuts, punctures, or kinks. Check for corrosion along the length of the lines, especially where they connect to the engine and storage tanks. Use a flashlight to examine tight spaces and ensure no fuel is leaking. Additionally, inspect the fittings and valves for tightness and proper operation. Leaky connections can be a significant source of fuel loss and should be tightened or replaced immediately.
Another crucial aspect of fuel line maintenance is the use of the right tools and materials. When replacing or repairing fuel lines, ensure you use compatible materials that can withstand the corrosive effects of fuel and the marine environment. This includes choosing the appropriate pipe, fittings, and gaskets. It is also essential to follow manufacturer guidelines for installation to ensure a secure and leak-free connection.
In addition to visual inspections, regular maintenance may involve pressure testing the fuel lines. This process involves applying pressure to the system to check for any leaks or weaknesses. It can help identify hidden issues that might not be apparent during a visual inspection. Pressure testing should be conducted by trained professionals who can interpret the results and recommend appropriate actions.
By implementing a regular maintenance schedule, vessel owners and operators can significantly reduce the risk of fuel line failures and ensure the safety and reliability of their marine operations. It is a proactive approach that pays off in the long run, preventing costly downtime and potential hazards associated with fuel leaks.
Clogged Fuel Line: How It Affects Your Car's Performance
You may want to see also
Fuel Line Fittings: Types of connectors and fittings used in marine fuel systems
Fuel lines in marine environments are crucial components of a vessel's fuel system, responsible for transporting fuel from the storage tanks to the engine. These lines are designed to withstand the harsh conditions of the marine environment, including exposure to saltwater, varying temperatures, and vibrations. The integrity of the fuel lines is essential to ensure efficient and safe operation of the engine. To achieve this, the fuel lines are equipped with various types of connectors and fittings that play a critical role in maintaining the system's performance and reliability.
One of the most common types of connectors used in marine fuel systems is the quick-disconnect coupling. These couplings are designed to allow for easy and rapid disconnection of fuel lines, which is particularly useful during maintenance, repairs, or when refueling. Quick-disconnect couplings typically consist of a male and female connector, with a locking mechanism that ensures a secure and tight connection. When disconnected, the fuel flow is immediately stopped, preventing any potential leaks or spills. This type of fitting is often made from durable materials like brass or stainless steel to withstand the corrosive effects of saltwater.
Another essential component is the fuel line adapter, which is used to connect fuel lines of different diameters or to adapt a fuel line to a specific fitting or connector. Adapters are particularly useful when retrofitting older systems or when dealing with non-standard fuel line sizes. They provide a versatile solution, allowing for the use of standard fittings and connectors with various fuel line sizes. These adapters are often made with precision to ensure a tight and secure seal, preventing fuel leaks and maintaining system efficiency.
In addition to these, marine fuel systems also utilize various types of fittings such as elbows, tees, and reducers. Elbows are used to change the direction of the fuel line, allowing for routing around obstacles or to reach specific engine components. Tees provide a branching point in the fuel line, enabling the distribution of fuel to multiple engines or systems. Reducers, on the other hand, are used to change the diameter of the fuel line, often connecting a smaller line to a larger one. These fittings are designed to minimize flow restrictions and ensure optimal fuel delivery.
The choice of connectors and fittings depends on factors such as the vessel's design, engine requirements, and the specific conditions of the marine environment. Marine fuel systems often require specialized fittings that can withstand corrosion, vibrations, and the presence of fuel contaminants. Manufacturers and engineers carefully select these components to ensure the overall reliability and longevity of the fuel system. Proper installation and regular maintenance of these fittings are essential to prevent fuel leaks and maintain the vessel's performance.
Air in Tractor Fuel Line: Causes and Solutions
You may want to see also
Fuel Line Pressure: Understanding pressure requirements and testing for marine fuel lines
The fuel line pressure is a critical aspect of marine fuel systems, ensuring efficient and safe fuel delivery to the engine. It involves understanding the pressure requirements for different fuel types and implementing testing methods to verify the integrity of the fuel lines. When it comes to marine applications, fuel lines play a vital role in transporting fuel from the storage tank to the engine, and maintaining the right pressure is essential for optimal performance.
In marine environments, fuel lines are exposed to various conditions, including vibrations, temperature fluctuations, and the constant movement of the vessel. These factors can impact the pressure within the fuel lines, affecting the engine's operation. For instance, low pressure might result in poor fuel atomization, leading to reduced engine performance and potential starting issues. On the other hand, excessive pressure can cause fuel line damage, especially if the lines are not designed to withstand such forces. Therefore, it is crucial to establish pressure requirements specific to marine fuel lines.
Pressure requirements for marine fuel lines depend on several factors, including the type of fuel, engine specifications, and operating conditions. Different fuels, such as diesel, gasoline, or biofuel, have varying properties and vapor pressures. For example, diesel fuel typically requires a higher pressure to ensure proper atomization and combustion compared to gasoline. Engine manufacturers provide guidelines for the recommended pressure range to optimize performance and prevent engine damage. Operating conditions, such as speed, altitude, and temperature, also influence pressure needs.
To ensure the fuel lines meet these pressure requirements, testing is essential. One common method is pressure testing, where the fuel lines are subjected to controlled pressure to check for leaks, blockages, or structural integrity. This test can be performed using specialized equipment that simulates the engine's fuel pressure. By applying pressure gradually and monitoring the system, technicians can identify any issues with the fuel lines, such as cracks, kinks, or faulty fittings. Regular pressure testing is recommended, especially during maintenance checks, to ensure the fuel system's reliability.
Additionally, visual inspections and non-destructive testing methods can be employed to assess the condition of the fuel lines. Visual inspections allow technicians to identify any visible damage, corrosion, or signs of wear and tear. Non-destructive testing techniques, such as ultrasonic testing or magnetic particle inspection, can detect internal flaws or defects without causing damage to the fuel lines. Combining these testing methods provides a comprehensive evaluation of the fuel line pressure and overall system health.
In summary, understanding and managing fuel line pressure is crucial for marine fuel systems. By considering the specific pressure requirements for different fuels and operating conditions, technicians can ensure optimal engine performance and longevity. Regular testing, including pressure testing and visual inspections, helps identify potential issues and maintains the integrity of the fuel lines, contributing to a safe and efficient marine vessel operation.
Unraveling the Mystery: Understanding Fuel Line Retaining Clips
You may want to see also
Frequently asked questions
Marine fuel line is a specialized type of fuel line designed specifically for use in marine applications, such as boats, ships, and other watercraft. It is engineered to withstand the unique challenges and harsh environments of marine environments, including exposure to saltwater, varying temperatures, and potential vibrations.
Marine fuel lines are constructed with materials that are more resistant to corrosion and degradation caused by saltwater. They often use materials like stainless steel, brass, or specialized polymers that can handle the corrosive effects of seawater. Additionally, marine fuel lines may have different pressure ratings and flow characteristics to accommodate the specific fuel requirements of marine engines.
These fuel lines are primarily used to transport fuel from the storage tank to the engine or generator aboard a vessel. They are an essential component of the fuel system, ensuring efficient and reliable fuel delivery to the engine. Marine fuel lines are also used in various other applications, such as connecting fuel pumps, filters, and injectors in marine engine systems.
Yes, there are a few important factors to consider. Firstly, proper insulation and protection are crucial to prevent damage from saltwater and temperature fluctuations. This may involve using protective sleeves or coatings. Secondly, marine fuel lines should be installed with secure fittings and connections to ensure they can withstand the vibrations and movements experienced during operation. Regular inspection and maintenance are also recommended to identify and replace any worn-out or damaged fuel lines.