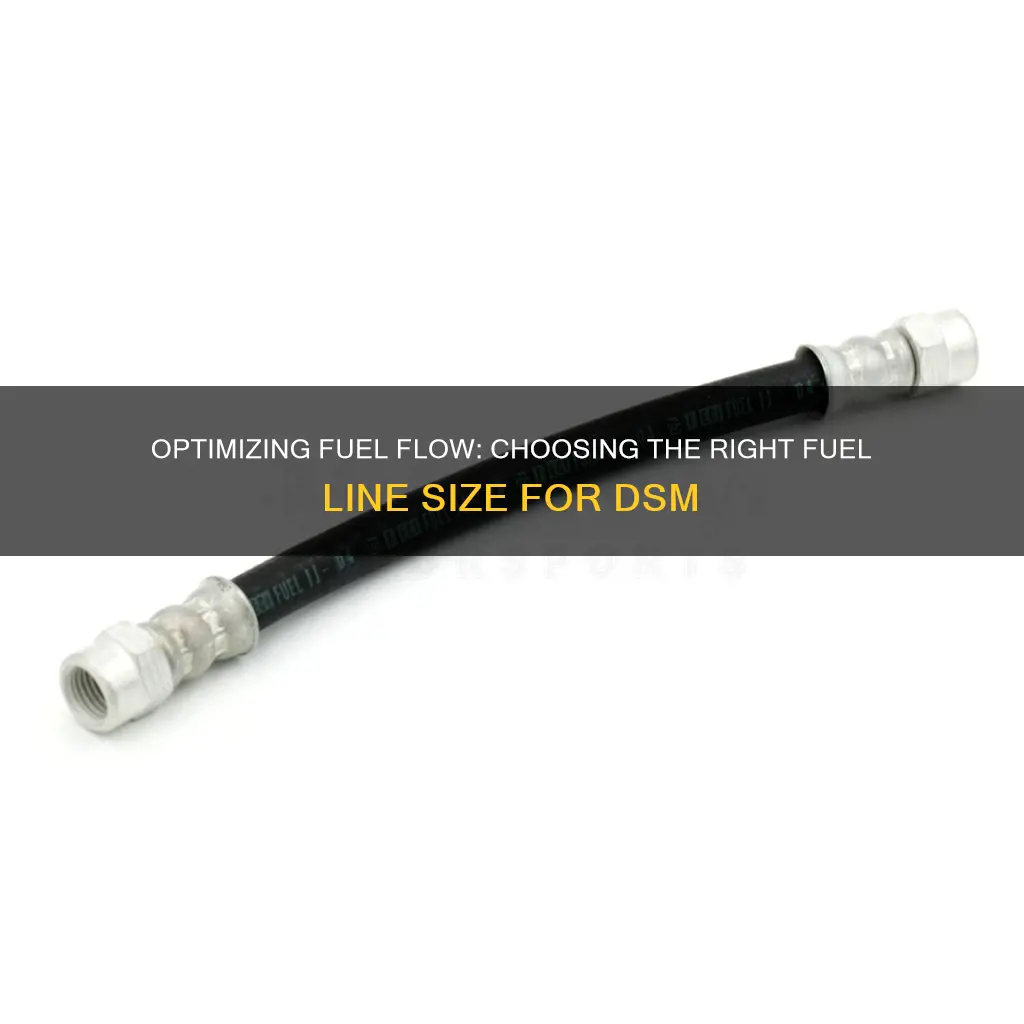
When it comes to modifying a DSM (Dodge Sporty Mustang) for increased performance, one crucial aspect is the fuel system. The size of the fuel line connecting the fuel rail to the engine plays a significant role in ensuring optimal fuel delivery and performance. This paragraph will delve into the considerations and guidelines for determining the appropriate fuel line size for your DSM, covering factors such as engine power, fuel pump specifications, and the importance of proper sizing to avoid performance bottlenecks and ensure reliable operation.
What You'll Learn
- Fuel Line Material: Choose the right material for durability and compatibility
- Rail DSM Diameter: Determine the appropriate diameter based on flow rate and pressure
- Fuel Rail Length: Consider the length of the rail for optimal fuel delivery
- Fuel Line Routing: Plan the route to avoid interference and ensure proper installation
- Fuel Pump Capacity: Match the fuel line size to the pump's output for efficient fueling
Fuel Line Material: Choose the right material for durability and compatibility
When it comes to fuel lines for your DSM (Dodge Shadow or Dodge Magnum), selecting the right material is crucial for ensuring durability and compatibility. The fuel line is a critical component in the fuel delivery system, and using the appropriate material can prevent leaks, ensure efficient fuel flow, and extend the life of your vehicle. Here's a guide to help you choose the right fuel line material:
Durability and Flexibility: Fuel lines need to withstand the challenges of the automotive environment, including temperature fluctuations, vibrations, and fuel pressure. Look for materials that offer excellent durability and flexibility. Rubber or synthetic rubber compounds are commonly used for fuel lines due to their ability to resist cracking and aging. High-quality rubber can handle the rigors of the engine bay and provide long-lasting performance.
Compatibility with Fuel Type: Different types of fuel require specific materials to ensure compatibility and prevent contamination. For gasoline applications, rubber or synthetic rubber-based fuel lines are typically used. These materials are resistant to gasoline evaporation and degradation. If you're dealing with diesel fuel, consider fuel lines made from materials like nylon or braided stainless steel, which offer superior resistance to the corrosive nature of diesel. Always check the manufacturer's recommendations for the specific fuel type your vehicle uses.
Temperature Resistance: Engine compartments can get extremely hot, so it's essential to choose a fuel line material that can withstand high temperatures without degrading. Silicone-based fuel lines are an excellent choice for high-temperature environments as they remain flexible and resistant to heat-induced damage. Ensure that the chosen material can handle the operating temperatures of your engine to avoid premature failure.
Vibration and Movement: Fuel lines need to accommodate engine vibrations and movement during operation. Materials like nylon or braided stainless steel are known for their flexibility and ability to resist kinking or bending out of shape. These materials ensure that the fuel line remains secure and functional even when the engine is in motion.
Installation and Maintenance: Consider the ease of installation and maintenance when selecting fuel line material. Some materials may require specific tools or techniques for a secure fit. Additionally, materials that are easy to inspect and replace if needed can contribute to the overall reliability of your fuel system.
Remember, consulting the vehicle's manual or seeking advice from automotive experts can provide specific recommendations for your DSM model. Choosing the right fuel line material will contribute to a reliable and efficient fuel delivery system, ensuring your vehicle performs optimally.
Understanding Ford's Fuel Line Valve: A Comprehensive Guide
You may want to see also
Rail DSM Diameter: Determine the appropriate diameter based on flow rate and pressure
When determining the appropriate diameter for a fuel line connecting to a Rail DSM (Direct Spark Ignition engine), it is crucial to consider both the flow rate and pressure requirements. The flow rate, measured in liters per minute (L/min), represents the volume of fuel that needs to pass through the line at any given time. Higher flow rates typically demand larger diameters to ensure efficient and uninterrupted fuel delivery. This is because a larger diameter provides a greater cross-sectional area, allowing more fuel to flow simultaneously without causing excessive pressure drops.
Pressure is another critical factor. Fuel lines must be designed to handle the pressure generated by the engine's fuel injection system. This pressure can vary depending on the engine's power output and operating conditions. A higher pressure requires a larger diameter fuel line to accommodate the increased force without compromising performance or safety. The relationship between pressure and diameter is inversely proportional; as pressure increases, the diameter should also increase to maintain optimal flow characteristics.
To calculate the appropriate diameter, engineers often use empirical formulas and tables derived from extensive testing. These resources provide guidelines based on the specific engine's characteristics, such as displacement, compression ratio, and fuel injection parameters. For instance, a common approach is to use the Darcy-Weisbach equation, which relates flow rate, pressure drop, and pipe diameter. By inputting the expected flow rate and pressure, engineers can determine the required diameter to ensure efficient and reliable fuel supply.
In practice, fuel lines for Rail DSM engines are often designed with diameters ranging from 0.5 inches to 1 inch (approximately 12.7 to 25.4 mm). However, this range can vary depending on the specific engine requirements and performance objectives. For high-performance applications or engines with larger displacement, larger diameters might be necessary to meet the demanding flow rate and pressure requirements.
In summary, selecting the correct diameter for a fuel line to Rail DSM involves a careful consideration of flow rate and pressure. Engineers use empirical data and calculations to determine the optimal diameter, ensuring that the fuel line can efficiently deliver the required amount of fuel while withstanding the engine's operating pressures. This attention to detail is vital for maintaining engine performance, reliability, and longevity.
Unveiling the Secrets: Corvette Fuel Line Sizing, 1969 Edition
You may want to see also
Fuel Rail Length: Consider the length of the rail for optimal fuel delivery
When it comes to modifying a DSM (Dodge Shadow/Dodge Magnum) engine for increased performance, one crucial aspect often overlooked is the fuel rail length. The fuel rail is a critical component in the fuel injection system, and its length can significantly impact the engine's performance and reliability. Here's a detailed guide on why and how to consider the fuel rail length for optimal fuel delivery.
The primary function of the fuel rail is to provide a consistent and precise fuel-air mixture to the engine's cylinders. As the name suggests, it acts as a rail or guide for the fuel, ensuring an even distribution. The length of this rail is essential because it determines the distance the fuel has to travel from the fuel pump to the injectors. Longer rails can introduce challenges, such as increased pressure drop and potential fuel starvation at higher engine speeds.
In a DSM engine, the fuel rail is typically located near the front of the engine bay, with multiple injectors strategically positioned to spray fuel into the intake manifold or directly into the cylinders. If the fuel rail is too long, the fuel may not have sufficient time to vaporize properly, leading to poor atomization and reduced engine performance. This can result in a noticeable drop in power and potentially cause engine misfires or rough idling.
To optimize fuel delivery, it is recommended to keep the fuel rail length as short as possible. A shorter rail ensures that the fuel has a minimal distance to travel, reducing the chances of pressure loss and maintaining a consistent fuel-air mixture. This is especially important in high-performance applications where engine speed and power output are maximized.
When modifying your DSM, consider the following: measure the existing fuel rail length and compare it to the manufacturer's specifications. If the rail is too long, explore options like shortening it or using a fuel rail with a shorter design. Additionally, ensure that the fuel pump and injectors are positioned to minimize the fuel line's length, further optimizing the fuel delivery system. Properly sizing the fuel rail length is a critical step in achieving the desired performance gains while maintaining a reliable and efficient engine.
Fuel Line Faults: Common Issues and Solutions
You may want to see also
Fuel Line Routing: Plan the route to avoid interference and ensure proper installation
When planning the fuel line routing for your DSM, it's crucial to consider the specific requirements of your vehicle and the potential challenges of the installation process. The goal is to ensure a smooth and efficient flow of fuel while avoiding any interference with other components. Here's a step-by-step guide to help you plan the optimal route:
- Research and Measurements: Begin by researching the specific fuel line sizes recommended for your DSM model. Different vehicles may have varying requirements, so it's essential to consult the manufacturer's guidelines or seek advice from automotive experts. Measure the available space along the fuel rail and the desired installation points to determine the length and diameter of the fuel line needed. This initial research will provide a clear understanding of the materials and dimensions required.
- Identify Potential Routes: Visualize the engine bay and identify potential paths for the fuel line. Consider the location of the fuel rail, the position of the fuel pump, and the proximity to other critical components. Aim to route the line away from high-pressure areas, such as exhaust manifolds or heat sources, to prevent damage and ensure longevity. Look for areas with sufficient clearance to accommodate the fuel line's diameter without any interference.
- Avoid Interference: One of the critical aspects of fuel line routing is to prevent interference with other engine components. Here are some key points to consider:
- Engine Block: Ensure the fuel line does not run parallel to the engine block, as this can lead to potential damage from heat or vibration.
- Transmission and Drivetrain: Avoid routes that could interfere with the transmission, driveshaft, or any moving parts that may cause wear and tear on the fuel line.
- Air Intake and Exhaust: Keep the fuel line clear of the air intake system and exhaust manifold to prevent fuel contamination and potential fire hazards.
- Secure Mounting: Proper mounting is essential to maintain the fuel line's position and prevent movement, which could lead to leaks or damage. Use appropriate mounting hardware, such as brackets or ties, to secure the line in place. Ensure that the mounting points are accessible for future maintenance and adjustments.
- Flexibility and Routing Techniques: Fuel lines should be routed with some flexibility to accommodate engine movement and vibrations. Use bends and loops strategically to guide the line around obstacles while maintaining a smooth flow. Consider using fuel line protectors or sleeves to safeguard against potential impacts or sharp edges.
By carefully planning the fuel line routing, you can ensure a clean and efficient installation, minimizing the risk of interference and potential issues. Remember to consult the manufacturer's guidelines and seek professional advice if needed to ensure the best results for your DSM's fuel system.
Ford Focus 2001 Fuel Line Breakdown: Essential Components Explained
You may want to see also
Fuel Pump Capacity: Match the fuel line size to the pump's output for efficient fueling
When it comes to optimizing the fueling system in your DSM, understanding the relationship between fuel pump capacity and fuel line size is crucial for efficient and reliable performance. The fuel pump is responsible for delivering the required amount of fuel to the engine, and its output directly impacts the engine's performance and fuel efficiency. Therefore, matching the fuel line size to the pump's capacity is essential to ensure a smooth and uninterrupted fuel supply.
The size of the fuel line determines the rate at which fuel can flow from the pump to the engine. If the fuel line is too small, it may restrict the fuel flow, leading to reduced engine power and potential performance issues. On the other hand, an oversized fuel line can result in unnecessary pressure drops, causing the pump to work harder and potentially reducing its lifespan. The key is to find the optimal size that allows for efficient fuel transfer without causing any restrictions or inefficiencies.
To determine the appropriate fuel line size, you should consider the output capacity of your fuel pump. Modern fuel pumps often have specific flow rates, measured in liters per minute (L/min) or gallons per minute (GPM). For example, a high-performance fuel pump might deliver 400-500 liters per minute. It's essential to match this output with a fuel line that can handle the required flow rate without causing excessive pressure drops. A common rule of thumb is to use a fuel line with an inside diameter that is approximately 1/3 to 1/4 of the pump's flow rate in liters per minute.
For instance, if your fuel pump outputs 450 liters per minute, a fuel line with an inside diameter of around 112.5 mm (4.43 inches) would be suitable. This size ensures that the fuel line can accommodate the pump's capacity while maintaining efficient fuel delivery. It's worth noting that this is a general guideline, and factors such as fuel pressure, engine requirements, and system design should also be considered when selecting the fuel line size.
In summary, matching the fuel line size to the fuel pump's output is a critical aspect of DSM fueling system optimization. By ensuring the fuel line can handle the pump's capacity, you can achieve efficient fueling, improved engine performance, and a longer-lasting fuel system. Always refer to the manufacturer's specifications and consult with experts to determine the precise fuel line size required for your specific DSM setup.
The Strange Sound of Frozen Fuel Lines: A Guide
You may want to see also
Frequently asked questions
The fuel line size for the DSM fuel rail system typically ranges from 3/8" to 1/2" in diameter. The specific size may vary depending on the engine configuration, performance goals, and fuel pump specifications. It's essential to choose a fuel line with sufficient capacity to handle the desired fuel flow rate and pressure.
The length of the fuel line should be carefully calculated to minimize pressure loss and ensure efficient fuel delivery. A common rule of thumb is to keep the fuel line length to a minimum, ideally less than 12 inches. This can be achieved by routing the line directly from the fuel pump to the fuel rail, avoiding unnecessary bends and loops.
Yes, for DSM fuel rail systems, it is generally recommended to use fuel lines made from high-quality materials such as stainless steel or braided steel. These materials offer excellent durability, resistance to fuel degradation, and flexibility, ensuring a reliable fuel supply even under high-performance conditions.
While standard fuel line connectors might work, it's advisable to use fuel rail-specific connectors designed for DSM applications. These connectors often feature a more secure fitting and can withstand higher fuel pressures, ensuring a reliable and leak-free connection between the fuel line and the rail.
The diameter of the fuel line directly affects the fuel flow rate and pressure. Larger diameter fuel lines allow for higher flow rates, which can improve engine performance, especially during high-load conditions. However, it's crucial to balance this with the engine's requirements and ensure that the fuel system can handle the increased fuel volume without compromising efficiency.