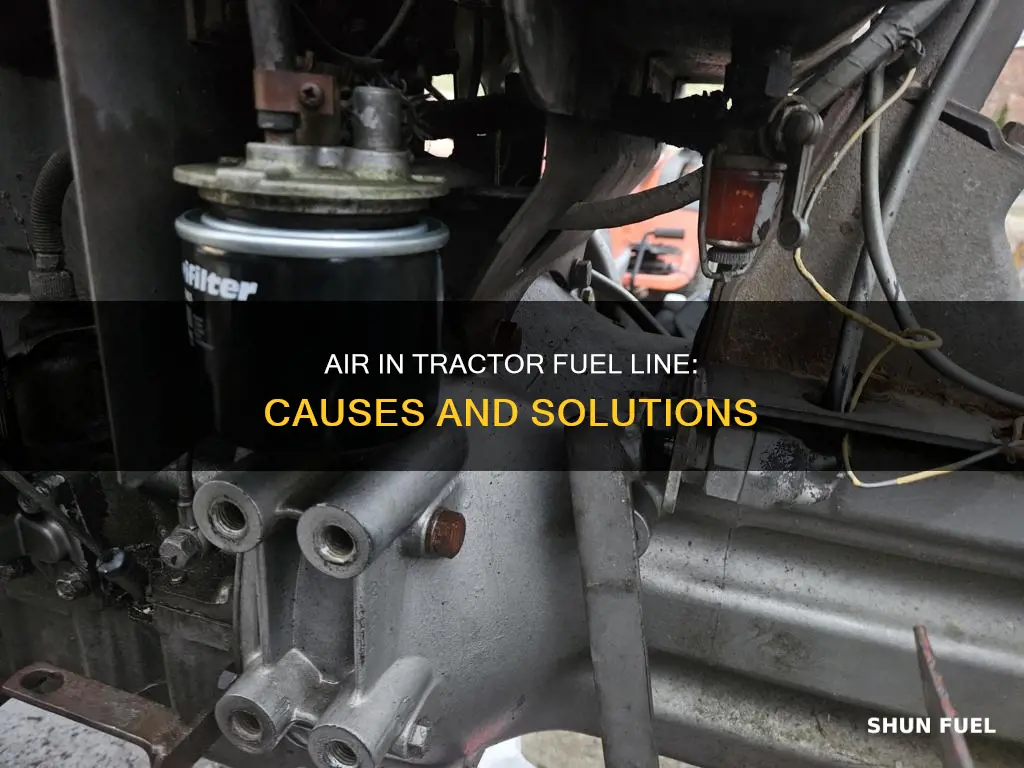
Understanding the causes of air in a fuel line of a tractor is crucial for maintaining its performance and longevity. Air intrusion in the fuel system can lead to various issues, such as reduced engine power, poor fuel efficiency, and even engine damage. This phenomenon often occurs due to several factors, including improper fuel tank ventilation, fuel filter blockages, or issues with the fuel pump. Identifying the root cause of air in the fuel line is essential for implementing effective solutions and ensuring the tractor operates optimally.
What You'll Learn
- Fuel System Design: Design flaws can allow air to enter the fuel line
- Fuel Tank Venting: Inadequate venting can cause air bubbles in the fuel
- Fuel Filter Clogging: Clogged filters may restrict fuel flow, drawing air
- Engine Operation: Running the engine with the fuel cap off can introduce air
- Fuel Pump Issues: Malfunctioning pumps can create air pockets in the fuel line
Fuel System Design: Design flaws can allow air to enter the fuel line
The fuel system of a tractor is a complex network of components designed to deliver fuel efficiently to the engine. However, design flaws in this system can lead to issues, one of the most common being the presence of air in the fuel line. This phenomenon, often referred to as 'air in the fuel,' can cause a range of problems, from reduced engine performance to potential damage to the engine over time. Understanding the causes and implementing preventive measures are crucial for maintaining the tractor's reliability and longevity.
One primary reason air enters the fuel line is due to inadequate fuel system design. The fuel system should be designed to ensure a tight seal between all components to prevent air infiltration. If the design lacks proper sealing mechanisms, such as gaskets or O-rings, air can easily find its way into the system. For instance, a poorly designed fuel filter housing might not have a secure seal, allowing air to bypass the filter and enter the fuel line. Similarly, connections between fuel tanks, pumps, and injectors should be meticulously sealed to maintain the integrity of the fuel system.
Another critical aspect of fuel system design is the inclusion of a fuel return line. This line is responsible for returning excess fuel from the injectors back to the fuel tank, ensuring that the engine receives the precise amount of fuel required for optimal performance. However, if the fuel return line is not properly designed, it can create a pathway for air to enter the system. For example, a kinked or improperly routed fuel return line might allow air to accumulate in the line, leading to air bubbles in the fuel that ultimately find their way into the engine.
Furthermore, the presence of a fuel pump is essential to maintain adequate fuel pressure throughout the system. If the fuel pump is not designed to handle the required fuel volume efficiently, it can lead to air being drawn into the system. This is particularly problematic when the pump is unable to maintain sufficient pressure, causing air to be drawn in to compensate for the lack of fuel. In such cases, the fuel system design might need to be revised to accommodate a more robust pump or to include a pressure regulator to ensure optimal fuel flow.
To mitigate these issues, engineers must pay close attention to the design details of the fuel system. This includes using high-quality materials that can withstand the fuel's properties and environmental conditions, ensuring all connections are secure and sealed, and implementing a well-thought-out fuel return system. Regular maintenance and inspections can also help identify and rectify design flaws, ensuring that air does not become a recurring problem in the fuel line.
Aluminum or Steel: Choosing the Right Fuel Line Material
You may want to see also
Fuel Tank Venting: Inadequate venting can cause air bubbles in the fuel
In the context of tractors and fuel systems, proper ventilation of the fuel tank is crucial to prevent the accumulation of air bubbles, which can lead to various performance issues. When a fuel tank lacks adequate ventilation, it creates a vacuum-like condition, drawing air into the fuel system. This phenomenon is particularly problematic as it can result in a loss of power, erratic engine behavior, and even complete engine stall.
The primary function of a fuel tank vent is to allow air to escape as fuel is dispensed. When the tank is filled, the venting mechanism ensures that any excess air is released, maintaining a balanced pressure within the tank. Over time, if the vent becomes clogged or damaged, it fails to perform this critical function. As a result, air bubbles start to form and accumulate in the fuel, leading to a condition known as 'vapor lock' or 'air lock'.
One common cause of inadequate venting is physical damage to the venting system. This can occur due to collisions, improper installation, or the use of low-quality materials. Additionally, debris, dirt, or even insects can block the vent, preventing air from escaping. In such cases, the fuel tank may appear full, but the actual volume of fuel is significantly reduced due to the presence of air bubbles.
To address this issue, it is essential to inspect and maintain the fuel tank's venting system regularly. Cleaning or replacing the vent can be an effective solution. In some cases, simply removing any debris or blockages can restore proper ventilation. It is also recommended to use fuel stabilizers or additives designed to minimize the formation of air bubbles, especially in older tractors or those with less advanced fuel systems.
Furthermore, ensuring that the fuel tank is tightly sealed and properly mounted can help prevent air from entering the system. Regularly checking for any signs of damage or leaks around the fuel tank and addressing them promptly can contribute to maintaining a healthy fuel system and optimal engine performance. By understanding the importance of fuel tank venting, tractor owners can take proactive measures to avoid the detrimental effects of air bubbles in the fuel.
Fuel Line Spray: Normal or Cause for Concern?
You may want to see also
Fuel Filter Clogging: Clogged filters may restrict fuel flow, drawing air
Fuel filters are an essential component of any engine system, including tractors, as they play a critical role in ensuring the engine receives clean and properly pressurized fuel. Over time, these filters can become clogged, leading to a variety of performance issues, one of which is the introduction of air into the fuel line. This phenomenon is a common problem and can be caused by several factors.
One primary cause of fuel filter clogging is the accumulation of contaminants in the fuel. Fuel itself can contain impurities, especially if it has been stored for an extended period or is of poor quality. Additionally, the fuel system can introduce contaminants, such as water, sediment, or even small debris, which can find their way into the filter over time. These particles gradually build up, narrowing the filter's passages and reducing its effectiveness.
Another factor contributing to fuel filter clogging is the natural wear and tear of the filter material. Filters are designed to trap contaminants, but the materials used may degrade or become less effective over time. This degradation can be accelerated by harsh fuel conditions, high temperatures, or the presence of certain chemicals in the fuel. As the filter's performance diminishes, it may fail to capture larger particles, allowing them to pass through and eventually clog the fuel line.
Regular maintenance and filter replacement are crucial to preventing this issue. Tractor owners should adhere to the manufacturer's recommended service schedule for filter changes. This ensures that the filter is replaced before it becomes overly clogged, maintaining optimal fuel flow and engine performance. It is also essential to use high-quality fuel and to keep the fuel tank and lines clean to minimize the introduction of contaminants.
In summary, fuel filter clogging can lead to air being drawn into the fuel line, causing engine performance problems. This issue is often a result of contaminants in the fuel, the natural wear of the filter, or a lack of proper maintenance. By understanding these causes and implementing regular filter replacement and fuel care practices, tractor operators can ensure their engines run efficiently and reliably.
Nova Fuel Tank Lines: Unlocking Engine Power and Efficiency
You may want to see also
Engine Operation: Running the engine with the fuel cap off can introduce air
Running an engine with the fuel cap off can have detrimental effects on its performance and longevity. When the fuel cap is removed, it creates a vacuum in the fuel tank, which can lead to several issues related to air intake into the fuel system. This is a critical aspect of engine operation that every tractor owner should be aware of.
One of the primary consequences of leaving the fuel cap off is the potential for air to enter the fuel lines. Fuel systems are designed to operate under specific pressure conditions, and the introduction of air can disrupt this delicate balance. Air bubbles in the fuel can cause several problems, including poor engine performance, reduced power output, and even engine misfires. These issues often arise because air is not as efficient a fuel source as gasoline, and its presence can lead to incomplete combustion, resulting in a less powerful and less efficient engine.
The air-fuel mixture in an engine's combustion chamber is crucial for efficient burning. When air enters the fuel lines, it can separate the fuel from its vaporized state, leading to a less concentrated fuel-air mixture. This dilution of the fuel can cause the engine to run lean, resulting in reduced power and potential damage to the engine over time.
To prevent these issues, it is essential to always secure the fuel cap when the tractor is not in use. This simple action ensures that the fuel system remains pressurized, preventing air from entering the fuel lines. Additionally, regular maintenance, such as checking for any fuel system leaks and keeping the fuel tank clean, can further minimize the risk of air intrusion and ensure optimal engine performance.
In summary, leaving the fuel cap off while operating a tractor's engine can lead to air entering the fuel lines, causing a range of performance issues. It is a preventable problem that highlights the importance of proper maintenance and adherence to basic safety protocols when handling heavy machinery.
Understanding the Three Fuel Lines in an Engine: A Comprehensive Guide
You may want to see also
Fuel Pump Issues: Malfunctioning pumps can create air pockets in the fuel line
Fuel pumps play a critical role in ensuring that engines receive the necessary fuel for operation. However, when these pumps malfunction, it can lead to a variety of issues, one of which is the presence of air pockets in the fuel line. This problem is particularly common in tractors, where the fuel system is designed to handle large volumes of fuel and can be susceptible to air intrusion.
The primary cause of air pockets in the fuel line is the failure of the fuel pump to maintain a consistent and adequate pressure. When a pump malfunctions, it may not be able to push fuel through the system effectively, leading to a decrease in pressure. This drop in pressure can cause air to be drawn into the fuel line, especially at points where the pressure is lower, such as near the engine or in the fuel tank.
One of the key signs of a malfunctioning fuel pump is a decrease in engine performance. The engine may stall, lose power, or run roughly, especially when it is under load. This is because the pump is unable to provide the required fuel volume and pressure, leading to a condition known as 'starvation' where the engine does not receive enough fuel to operate efficiently.
To address this issue, it is essential to inspect and maintain the fuel pump regularly. Over time, pumps can wear out due to the harsh conditions they operate in, including extreme temperatures, vibrations, and the presence of contaminants in the fuel. Regular maintenance, such as replacing worn-out components and ensuring the pump is properly lubricated, can help prevent malfunctions.
In cases where a fuel pump has already malfunctioned, the solution involves replacing it with a new, compatible pump. This process requires careful disassembly of the fuel system to access the pump, and it is crucial to follow manufacturer guidelines to ensure proper installation. Additionally, checking for and addressing any other potential issues, such as clogged fuel filters or damaged fuel lines, is essential to prevent the recurrence of air pocket problems.
Rubber Hose Fuel Line Lubrication: Essential Tips for Smooth Operation
You may want to see also
Frequently asked questions
Air intrusion in the fuel line is often caused by a few common issues. One of the primary reasons is a faulty fuel pump or filter, which can lead to air bubbles being drawn into the system. Over time, fuel lines can develop small holes or leaks, allowing air to enter. Additionally, if the fuel tank is not properly sealed, air can seep in, especially if there are any cracks or damage to the tank.
To prevent air from contaminating your tractor's fuel system, regular maintenance is key. Start by checking the fuel filter and replacing it if it's old or clogged. Ensure that the fuel pump is functioning correctly and consider using a fuel stabilizer to maintain the quality of the fuel. Keep an eye on the fuel lines for any signs of damage or wear and promptly address any issues. Properly sealing the fuel tank and using a fuel-specific air bleed kit can also help eliminate air bubbles.
When air is present in the fuel line, you may notice reduced engine performance, such as stalling or difficulty starting. The engine might also hesitate or lose power during operation. To fix this, start by removing the air bleeder valve from the fuel line and opening it to release any trapped air. Ensure you bleed the system properly by running the engine and then shutting it off to allow the air to escape. If the issue persists, it's advisable to consult a professional mechanic to inspect the fuel system for any underlying problems.