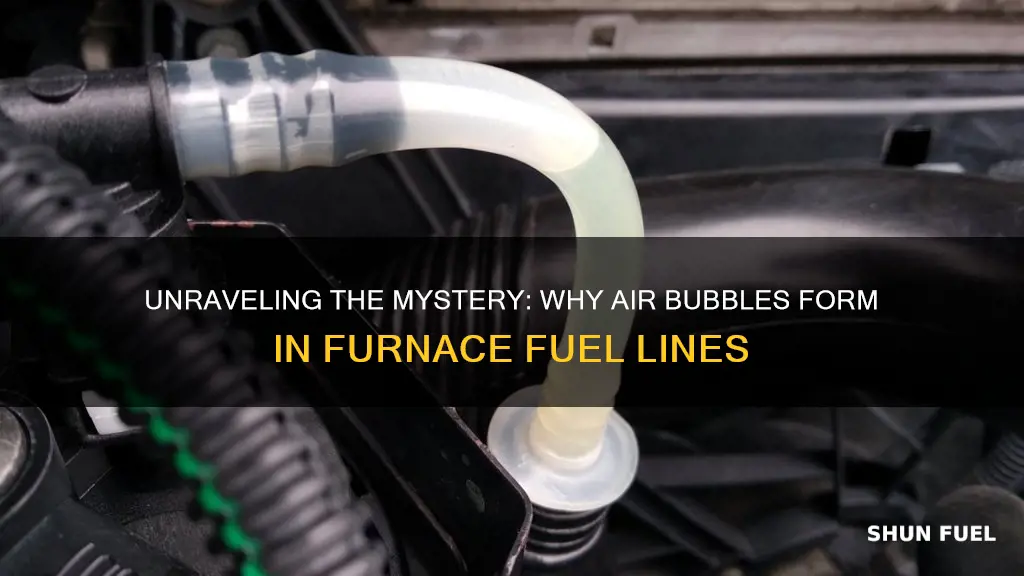
Air bubbles in furnace fuel lines can be a common issue for homeowners and can lead to inefficient heating or even complete failure of the heating system. Understanding the causes of these bubbles is essential for effective troubleshooting and maintenance. This paragraph will explore the various factors that contribute to the formation of air bubbles in furnace fuel lines, including the role of pressure, fuel type, and system design. By identifying these causes, readers can take proactive measures to prevent or address this problem, ensuring a reliable and efficient heating system.
What You'll Learn
- Fuel Type: Different fuels can produce varying amounts of air bubbles due to their unique properties
- Pressure Fluctuations: Rapid changes in pressure can cause air to be drawn into the fuel line
- Line Design: The design of the fuel line, including bends and valves, can affect air bubble formation
- Temperature Variations: Extreme temperature changes can cause fuel to expand or contract, leading to bubbles
- System Maintenance: Regular maintenance, like cleaning filters, can prevent air bubbles by ensuring a smooth flow
Fuel Type: Different fuels can produce varying amounts of air bubbles due to their unique properties
The type of fuel used in a furnace can significantly impact the occurrence and severity of air bubbles in the fuel line. Different fuels have distinct characteristics that affect their interaction with air, leading to varying levels of bubble formation. For instance, natural gas, a common fuel source, is highly compressible and has a low density, which means it can easily dissolve into the fuel line and form bubbles when it expands due to temperature changes or pressure variations. This property makes natural gas a prime candidate for causing air bubbles, especially in systems where the fuel line is exposed to varying temperatures or where there are pressure fluctuations.
On the other hand, liquid fuels like oil or kerosene have different behaviors. When these fuels are poured into the furnace, they tend to create larger bubbles due to their higher surface tension and lower density compared to the surrounding fuel. This can lead to more significant air pocket formation, especially when the fuel is not properly agitated or when the system is not designed to handle such fuels efficiently. The unique properties of liquid fuels, such as their higher viscosity and lower compressibility, contribute to the creation of larger bubbles, which can be more challenging to manage in the fuel line.
Solid fuels, such as wood pellets or coal, also play a role in air bubble formation. When these fuels are burned, they release gases that can condense and form bubbles as they come into contact with the fuel line. This is particularly noticeable in systems where the fuel is not properly pre-heated or where there is a significant temperature difference between the fuel and the surrounding environment. The combustion process of solid fuels can introduce air bubbles, especially if the combustion is not efficient, leading to incomplete burning and the release of unburned gases that may condense and form bubbles in the fuel line.
Furthermore, the design and material of the fuel line itself can influence the amount of air bubbles present. Some materials may be more susceptible to the formation of bubbles due to their inherent properties, such as the ability to retain air or the presence of voids within the material. For example, fuel lines made of certain plastics or metals might have internal structures that allow air to become trapped, leading to increased bubble formation. Understanding the specific fuel type and its properties is crucial in addressing and mitigating air bubble issues in furnace fuel lines.
Fuel Filter Lines: Understanding the Connections and Their Roles
You may want to see also
Pressure Fluctuations: Rapid changes in pressure can cause air to be drawn into the fuel line
Pressure fluctuations in a furnace fuel line can lead to the formation of air bubbles, which can cause significant issues with the system's performance and efficiency. When the pressure in the fuel line rapidly changes, it creates a vacuum effect, especially if the fuel source is under pressure. This sudden change in pressure can cause a temporary low-pressure area, allowing air to be drawn into the fuel line. The air bubbles may form when the air is pulled into the system, especially if the fuel line is not properly sealed or if there are any leaks or openings that allow air to enter.
One common scenario where this occurs is during the startup or shutdown of the furnace. When the system is turned on, the rapid increase in pressure can create a surge, leading to a momentary drop in pressure and the potential for air to be drawn in. Similarly, when the furnace is turned off, the pressure may decrease rapidly, creating a vacuum that can pull air into the fuel line. These pressure changes are often a result of the fuel pump's operation, which can cause sudden variations in pressure as it delivers fuel to the system.
To address this issue, it is crucial to ensure that the fuel line is properly insulated and sealed to minimize the entry of air. Proper sealing can be achieved by using high-quality fuel line materials and ensuring all connections are tight and secure. Additionally, installing a vacuum relief valve can help prevent air from entering the system by releasing excess pressure and allowing air to escape when pressure fluctuations occur.
Regular maintenance and inspection of the fuel line are essential to identify and rectify any potential issues. Over time, fuel lines can develop cracks or leaks, especially in areas where pressure is highest, such as near the pump or at connections. These vulnerabilities can allow air to infiltrate the system, leading to the formation of bubbles and potential performance problems.
In summary, pressure fluctuations, particularly rapid changes, are a significant contributor to air bubbles in furnace fuel lines. Understanding and managing these pressure variations through proper sealing, insulation, and maintenance can help ensure the efficient and safe operation of the heating system, preventing potential damage and performance degradation caused by air bubbles.
Sugar's Sweet Secret: Uncovering Its Impact on Fuel Lines
You may want to see also
Line Design: The design of the fuel line, including bends and valves, can affect air bubble formation
The design of the fuel line plays a crucial role in preventing air bubbles in furnace systems. When designing the fuel line, several factors should be considered to minimize the risk of bubble formation. Firstly, the line's diameter and material are essential. A larger diameter pipe allows for smoother flow, reducing the chances of turbulence and subsequent bubble creation. Additionally, using materials with low thermal expansion, such as stainless steel or copper, can help maintain the pipe's structural integrity and minimize the risk of leaks or blockages that could trap air.
Bends and elbows in the fuel line can also contribute to air bubble issues. Sharp bends or multiple elbows close together can create areas of reduced flow velocity, allowing air to accumulate. To mitigate this, it is recommended to use gradual, large-radius bends and ensure that the line is properly supported to prevent kinking. The placement of valves is another critical aspect. Valves should be positioned to allow for smooth flow and avoid creating dead zones where air can collect. Ball valves, for instance, can be problematic as they may create a pocket of air when closed, especially if the line is not properly vented.
The design should also consider the overall layout and positioning of the fuel line. A straight, vertical run of pipe from the fuel source to the furnace is ideal, as it allows for better flow and reduces the likelihood of air being drawn into the system. Any horizontal sections should be kept to a minimum and properly vented to allow air to escape. Proper ventilation is key to preventing air bubble problems. Venting the system at strategic points, such as near the fuel pump and at the furnace, ensures that any accumulated air can escape, reducing the risk of backflow and bubble formation.
In summary, the design of the fuel line is a critical factor in maintaining a bubble-free furnace system. By considering the pipe's diameter, material, and the use of gentle bends and properly positioned valves, engineers can minimize the chances of air bubble formation. Additionally, a well-planned layout and strategic venting can further contribute to a smooth and efficient fuel delivery process, ensuring optimal performance and safety.
Pipe Thread Sealant: Essential for Fuel Line Maintenance?
You may want to see also
Temperature Variations: Extreme temperature changes can cause fuel to expand or contract, leading to bubbles
Extreme temperature variations can significantly impact the fuel system of a furnace, potentially leading to the formation of air bubbles. When the fuel, such as oil or gas, is exposed to rapid or significant temperature changes, it undergoes thermal expansion or contraction. This phenomenon is a direct result of the fuel's physical properties, where its volume changes with temperature. For instance, when the fuel is heated, it expands, and when it cools, it contracts. These temperature-induced volume changes can have detrimental effects on the fuel's flow and the overall performance of the furnace.
In the context of a fuel line, the expansion and contraction of the fuel can cause several issues. As the fuel expands, it may push air into the line, creating bubbles. Conversely, when the fuel contracts, it can create a vacuum-like effect, drawing air into the system. Both scenarios can lead to the accumulation of air bubbles in the fuel line, which can disrupt the efficient delivery of fuel to the furnace. This disruption can result in reduced combustion efficiency, as the presence of air can dilute the fuel-air mixture, leading to incomplete burning and potential performance issues.
The impact of temperature variations is particularly critical during the startup and shutdown processes of the furnace. When the system is turned on, the fuel may experience rapid temperature changes, leading to expansion and potential bubble formation. Similarly, during shutdown, the fuel can cool down quickly, causing contraction and the potential for air to be drawn into the line. These temperature-related fluctuations can be especially problematic if the fuel line is not properly insulated or if the system is not designed to accommodate such changes.
To mitigate these issues, it is essential to consider the materials and design of the fuel line. Using materials with low thermal expansion coefficients can help minimize the impact of temperature changes. Additionally, proper insulation and the use of flexible hoses can reduce the effects of thermal expansion and contraction. Regular maintenance and inspection of the fuel line can also help identify and address any potential issues caused by temperature variations, ensuring the efficient and safe operation of the furnace.
In summary, extreme temperature changes can cause fuel to expand or contract, leading to the formation of air bubbles in the fuel line. This phenomenon can disrupt the fuel's flow, reduce combustion efficiency, and potentially cause performance issues. Understanding and managing temperature variations are crucial aspects of maintaining a well-functioning furnace system. By implementing appropriate materials, design considerations, and maintenance practices, one can effectively minimize the occurrence of air bubbles and ensure optimal furnace performance.
Ford Focus 2001 Fuel Line Breakdown: Essential Components Explained
You may want to see also
System Maintenance: Regular maintenance, like cleaning filters, can prevent air bubbles by ensuring a smooth flow
System maintenance is a critical aspect of ensuring the efficient and safe operation of your furnace. One of the most common issues that can arise is the presence of air bubbles in the fuel line, which can lead to a variety of problems, including reduced efficiency, increased fuel consumption, and even potential damage to the furnace. Regular maintenance, such as cleaning filters, is a simple yet effective way to prevent these air bubbles and maintain a smooth flow of fuel through the system.
The primary cause of air bubbles in the furnace fuel line is the introduction of air into the system during the fueling process or due to system pressure changes. When air is present in the fuel line, it can lead to a variety of issues. Firstly, air bubbles can cause the fuel to burn inefficiently, as they disrupt the combustion process, leading to incomplete burning and the release of excess carbon monoxide. This not only affects the performance of your furnace but also poses a potential health risk. Secondly, air bubbles can cause the fuel to emulsify, creating a thick, sticky substance that can clog the fuel line and restrict the flow of fuel to the burner. This can result in the furnace shutting down or operating at reduced capacity.
To prevent these issues, regular maintenance is essential. One of the most effective ways to maintain your furnace is by cleaning the filters. Filters are designed to trap dust, dirt, and other particles that can accumulate in the system. Over time, these particles can restrict the flow of fuel, leading to the formation of air bubbles. By regularly cleaning or replacing the filters, you ensure that the fuel has a clear path through the system, reducing the likelihood of air bubbles. This simple task can significantly improve the efficiency and longevity of your furnace.
In addition to cleaning filters, there are other maintenance practices that can help prevent air bubbles. Regularly inspecting the fuel line for any signs of damage or blockages is crucial. Even a small puncture or obstruction can allow air to enter the system. If you notice any issues, it's essential to address them promptly to prevent further complications. Furthermore, ensuring that the fuel pump is functioning correctly is vital. A faulty pump may not be able to maintain the necessary pressure to push fuel through the line, leading to air bubbles.
By implementing a regular maintenance routine, you can significantly reduce the occurrence of air bubbles in your furnace fuel line. This proactive approach not only ensures the efficient operation of your heating system but also contributes to its longevity and reliability. Remember, prevention is often more straightforward and cost-effective than dealing with the consequences of neglecting system maintenance.
Safe and Effective Methods to Thaw Frozen Car Fuel Lines
You may want to see also
Frequently asked questions
Air bubbles in the fuel line can occur due to a few reasons. One common cause is the presence of air in the fuel supply, which can happen when the fuel tank is not properly sealed or when there is a leak in the fuel system. Another reason is the natural expansion and contraction of the fuel line due to temperature changes, leading to the formation of air pockets. Additionally, if the fuel pump is not functioning correctly, it may not be able to push the fuel through the line efficiently, allowing air to enter.
To minimize the occurrence of air bubbles, it is essential to ensure that your fuel system is properly maintained and sealed. Regularly inspect the fuel tank and lines for any signs of damage or leaks, and promptly address any issues. You can also consider installing an air eliminator or vacuum breaker in the fuel line to remove any air pockets. Keeping the fuel system clean and free of debris is crucial, as contaminants can also contribute to bubble formation.
Yes, air bubbles can lead to several problems. One significant issue is a lack of proper fuel combustion, resulting in inefficient heating and potential performance issues with your furnace. Air bubbles can also cause the fuel to ignite unevenly, leading to poor heat output and increased fuel consumption. In some cases, air pockets can cause the furnace to shut off prematurely, as the pilot light may be extinguished due to insufficient fuel supply. Regular maintenance and addressing any air-related concerns can help prevent these complications.