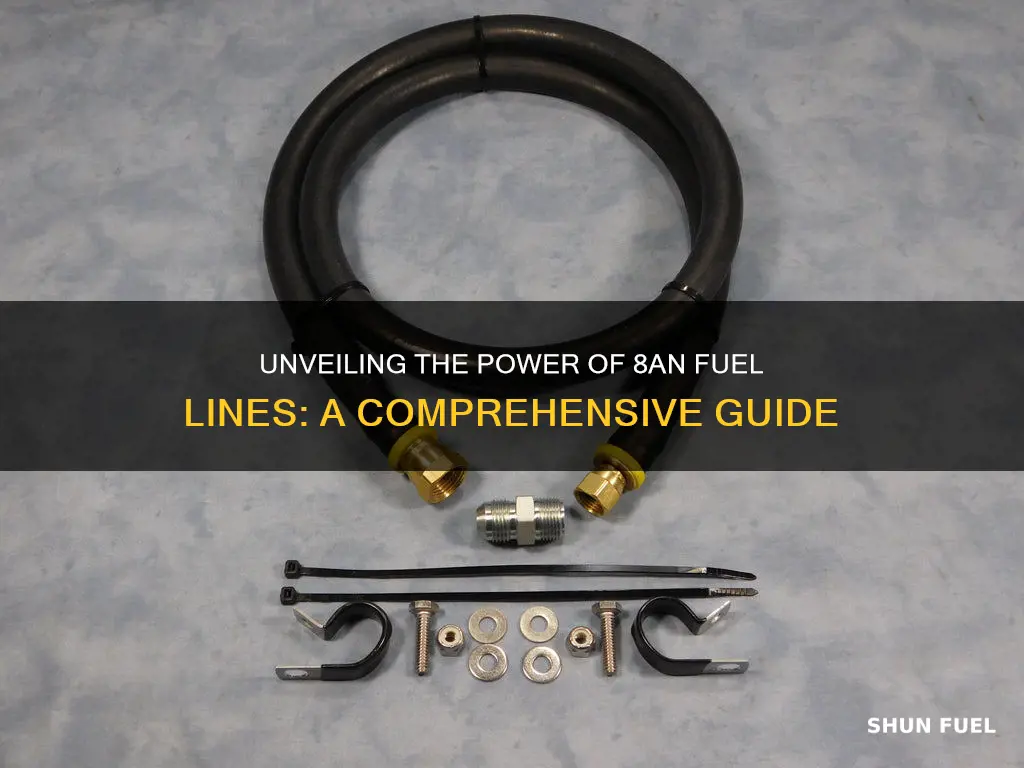
What is an 8AN fuel line? This question delves into the world of automotive components, specifically focusing on a particular type of fuel line. The 8AN fuel line is a crucial part of a vehicle's fuel system, designed to transport fuel from the tank to the engine. It is a high-pressure line, typically made of durable materials like steel or aluminum, and is engineered to withstand the demands of fuel delivery. Understanding the specifications and compatibility of an 8AN fuel line is essential for anyone working on a vehicle's fuel system, ensuring optimal performance and safety.
What You'll Learn
- Fuel Line Material: Different materials like rubber, plastic, or metal are used for fuel lines
- Fuel Line Routing: Proper routing to avoid damage and ensure optimal fuel flow
- Fuel Line Diameter: Size matters; diameter affects pressure and flow rate
- Fuel Line Length: Longer lines require additional considerations for flexibility and support
- Fuel Line Connections: Types of connections like quick-release or threaded
Fuel Line Material: Different materials like rubber, plastic, or metal are used for fuel lines
Fuel lines are an essential component of any vehicle's fuel system, responsible for transporting fuel from the tank to the engine. The choice of material for these lines is crucial, as it directly impacts the performance, durability, and safety of the fuel delivery system. Over the years, various materials have been utilized for fuel lines, each offering unique advantages and disadvantages.
One of the most common materials used for fuel lines is rubber. Rubber is known for its flexibility, which is essential for accommodating the natural expansion and contraction of the fuel lines due to temperature changes. It is also resistant to most fuels, making it a suitable choice for a wide range of vehicles. Rubber fuel lines are often used in classic cars and older vehicles due to their ability to withstand the challenges of aging rubber. However, rubber can be susceptible to cracking over time, especially in harsh environments, which may lead to fuel leaks.
Plastic fuel lines have gained popularity in recent years due to their lightweight nature and resistance to corrosion. Materials like nylon and polyetheretherketone (PEEK) are often used, offering excellent chemical resistance and flexibility. Plastic lines are less prone to cracking compared to rubber, making them a reliable choice for modern vehicles. Additionally, their lightweight design can improve fuel efficiency, which is a significant advantage for many car manufacturers.
Metal fuel lines, typically made from stainless steel or aluminum, are known for their strength and durability. These lines are often used in high-performance vehicles or those operating in extreme conditions. Metal is highly resistant to corrosion and can withstand high temperatures, making it ideal for applications where fuel lines are exposed to harsh environments. However, metal lines are stiffer than rubber or plastic, which might limit their flexibility and make installation more challenging.
The choice of material depends on various factors, including the vehicle's age, intended use, and environmental conditions. Modern vehicles often utilize a combination of rubber and plastic to balance flexibility, durability, and cost-effectiveness. It is essential to select the appropriate material to ensure a reliable fuel supply, prevent leaks, and maintain the overall performance of the vehicle's fuel system.
Camaro Fuel Line Placement: Above or Below Battery Cables?
You may want to see also
Fuel Line Routing: Proper routing to avoid damage and ensure optimal fuel flow
Fuel lines are an essential component of any vehicle's fuel system, responsible for transporting fuel from the tank to the engine. Proper routing of these lines is crucial to ensure optimal fuel flow and prevent damage to the vehicle. Here's a detailed guide on how to route fuel lines effectively:
- Understand the Layout: Begin by thoroughly understanding the layout of your vehicle's engine bay and fuel system. Familiarize yourself with the location of the fuel tank, fuel pump, and engine. Identify any potential obstacles, such as suspension components, exhaust systems, or body panels, that could interfere with fuel line placement. This knowledge will help you plan the most efficient and safe route for the fuel lines.
- Route with Care: When routing the fuel lines, prioritize safety and functionality. Here are some key considerations:
- Keep the lines away from high-temperature areas, such as the exhaust manifold or engine components, to prevent heat damage.
- Avoid sharp bends or kinks that could restrict fuel flow or cause damage over time. Aim for smooth, gradual curves.
- Route the lines away from moving parts like gears or pulleys to prevent damage and ensure smooth operation.
- In vehicles with a manual transmission, ensure the fuel lines are not routed too close to the transmission, as this can lead to potential issues with fuel contamination.
- Secure and Support: Properly secure and support the fuel lines to maintain their integrity. Use appropriate fasteners, such as clips, ties, or brackets, to keep the lines in place. Ensure they are not pinched or crushed, as this can restrict fuel flow. Consider using rubber or plastic sleeves to protect the lines from sharp edges or vibrations. Proper support will also help prevent sagging or excessive movement, which can lead to damage.
- Consider Fuel Type: Different types of fuel may require specific routing considerations. For example, in vehicles with ethanol-blended fuel, it's essential to use fuel lines that can withstand the corrosive nature of ethanol. Always refer to the vehicle's manual or consult a professional to determine the appropriate fuel line specifications for your vehicle's fuel type.
- Regular Inspection: Regularly inspect the fuel lines for any signs of damage, wear, or leaks. Look for cracks, brittleness, or any disconnections. If any issues are found, address them promptly to prevent further damage and potential safety hazards. Proper maintenance and inspection will ensure the long-term reliability of your fuel system.
By following these guidelines, you can ensure that your fuel lines are properly routed, avoiding potential damage and ensuring a steady and efficient fuel supply to the engine. Remember, each vehicle may have unique requirements, so always refer to the manufacturer's instructions for the most accurate and safe routing practices.
Fuel Injector Linearity: A Matter of Efficiency and Precision
You may want to see also
Fuel Line Diameter: Size matters; diameter affects pressure and flow rate
The diameter of a fuel line is a critical factor in determining its performance and efficiency in delivering fuel to an engine. This seemingly simple measurement has a significant impact on the pressure and flow rate of the fuel, which are essential for optimal engine operation. Understanding the relationship between fuel line diameter and these parameters is crucial for anyone working on fuel systems, whether it's for an automotive, marine, or aviation application.
In the context of fuel delivery, pressure is the force that drives fuel through the system. A larger diameter fuel line provides a lower resistance path for the fuel to travel, allowing it to flow more freely. This increased flow rate is beneficial as it ensures that the engine receives the required amount of fuel at the right time, promoting efficient combustion. When the fuel line diameter is too small, the pressure drop across the line increases, leading to reduced flow rates and potential fuel starvation, especially during high-demand situations like acceleration or climbing.
The flow rate, or the volume of fuel passing through the line per unit of time, is directly influenced by the diameter. A larger diameter fuel line offers a greater cross-sectional area, allowing more fuel to pass through in a given time. This is particularly important in high-performance applications where engines require a rapid and precise fuel supply to meet power demands. For instance, in racing cars, a larger diameter fuel line can provide the necessary fuel flow to support the engine's high power output, ensuring optimal performance and responsiveness.
Engineers and technicians must carefully consider the fuel line diameter when designing or modifying fuel systems. The choice of diameter depends on various factors, including engine power, fuel pressure, and the desired flow rate. For high-performance engines, larger diameter fuel lines might be necessary to accommodate the increased fuel demand. Conversely, in applications where weight is a critical factor, such as aircraft or lightweight vehicles, engineers may opt for smaller diameter lines to reduce overall system weight while still maintaining adequate performance.
In summary, the diameter of a fuel line is a critical design consideration that directly impacts the pressure and flow rate of fuel delivery. A larger diameter line offers benefits in terms of flow rate and pressure, ensuring the engine receives the required fuel for efficient operation. Understanding these principles allows for the optimization of fuel systems, catering to the specific needs of different applications and engines.
Air Bubbles in Diesel Fuel Lines: A Cause for Concern?
You may want to see also
Fuel Line Length: Longer lines require additional considerations for flexibility and support
When it comes to fuel lines, the length of the line is a critical factor that can significantly impact the performance and reliability of your vehicle's fuel system. Longer fuel lines, while sometimes necessary for specific vehicle designs or modifications, present unique challenges that require careful consideration. One of the primary concerns with extended fuel lines is ensuring sufficient flexibility to accommodate the natural movement and vibration of the vehicle during operation. Rubber or flexible materials are commonly used in fuel lines to provide this flexibility, allowing the line to bend and stretch without compromising the flow of fuel. However, longer lines may require additional layers of these flexible materials to maintain the necessary flexibility over a greater distance.
As the length of the fuel line increases, the potential for the line to become a source of restriction or obstruction also rises. This is because longer lines can create more opportunities for the line to kink, twist, or rub against other components, leading to reduced flow and potential fuel pressure drops. To mitigate these issues, it is essential to route the fuel line carefully, avoiding sharp bends and tight spaces where it could be pinched or damaged. Proper routing should also consider the vehicle's suspension and moving parts to ensure the fuel line remains clear and undisturbed during operation.
Support and mounting are other critical aspects of longer fuel lines. These lines need to be securely attached to the vehicle's frame or body to prevent excessive movement and potential damage. Proper mounting ensures that the fuel line maintains its intended position and angle, reducing the risk of fuel leaks or contamination. Using appropriate mounting hardware, such as brackets or ties, can help secure the fuel line and provide the necessary support. Additionally, considering the material and construction of the fuel line is vital. Longer lines may require specialized materials that can withstand the increased stress and potential wear over time.
In some cases, longer fuel lines might be necessary for specific vehicle modifications, such as engine swaps or the installation of high-performance fuel pumps. In these scenarios, it becomes even more crucial to address the flexibility, support, and routing challenges. Custom-made fuel lines or those designed for specific applications can be a solution, ensuring that the line meets the unique requirements of the modified vehicle. Regular maintenance and inspections are also essential to identify any signs of wear, damage, or reduced flexibility in longer fuel lines, ensuring the continued safe and efficient operation of the fuel system.
In summary, longer fuel lines demand careful attention to flexibility, support, and routing to ensure optimal performance and longevity. By addressing these considerations, vehicle owners and mechanics can maintain a reliable fuel system, even with extended lines, and minimize the risk of issues related to fuel flow and system integrity. Proper installation, regular maintenance, and the use of high-quality materials can contribute to a well-functioning fuel system, even in vehicles with longer fuel lines.
Fuel Line Flaring: A Double-Edged Decision
You may want to see also
Fuel Line Connections: Types of connections like quick-release or threaded
When it comes to fuel line connections, there are several types of fittings and methods used to ensure a secure and reliable link between the fuel tank and the engine. These connections are crucial for maintaining the integrity of the fuel system and preventing leaks, which can lead to engine performance issues and potential safety hazards. Here's an overview of some common fuel line connection types:
Quick-Release Connections: These are widely used in modern fuel systems due to their convenience and ease of use. Quick-release fittings typically consist of a male end with a threaded or bayonet-style connector and a female end that can be easily attached and detached. The key advantage is the ability to quickly disconnect the fuel line without the need for tools, making it ideal for situations where frequent access to the fuel tank is required, such as during maintenance or when replacing fuel filters. These connections often feature a locking mechanism to ensure they remain secure and prevent accidental disconnection.
Threaded Connections: Threaded fuel line connections are a traditional and reliable method, often used in older vehicles or systems that require a more permanent installation. These connections involve threading the fuel line onto a dedicated port or fitting, which is then secured with a nut or clamp. Threaded connections provide a tight seal and are less prone to leaks compared to quick-release fittings. However, they can be more time-consuming to install and may require specialized tools for tightening the nuts to the correct specifications.
In addition to these two primary types, there are also hybrid connections that combine elements of both quick-release and threaded designs. These hybrid fittings offer the convenience of quick-release connections while providing a more secure and permanent installation. They often feature a threaded male end for easy attachment and a locking mechanism to ensure a tight seal.
The choice of fuel line connection type depends on various factors, including the vehicle's make and model, the fuel system design, and the specific requirements of the application. Modern vehicles often utilize quick-release connections for their convenience, while older or specialized systems may employ threaded connections for their reliability and permanence. It is essential to select the appropriate connection type to ensure a safe and efficient fuel supply to the engine.
Permatex on Fuel Lines: A Carburetor Repair Hack or a No-Go?
You may want to see also
Frequently asked questions
An 8AN fuel line is a specific type of fuel line commonly used in automotive applications, particularly for high-performance engines. It is designed to handle high-pressure fuel and is known for its durability and flexibility. The "8AN" designation refers to the inside diameter of the fuel line, which is typically 8mm.
Compared to standard fuel lines, 8AN lines are thicker and stronger, making them ideal for high-performance vehicles that require increased fuel pressure and flow. They are often made from materials like stainless steel or braided nylon to ensure longevity and resistance to fuel-related chemicals. The 8AN size is a popular choice for modifications and racing applications.
Absolutely! While 8AN fuel lines are often associated with performance and racing, they can be used in everyday vehicles as well. Upgrading to an 8AN line can improve fuel delivery and potentially increase engine performance. However, it's essential to ensure that the vehicle's fuel system can handle the increased pressure and consider consulting a professional for proper installation.