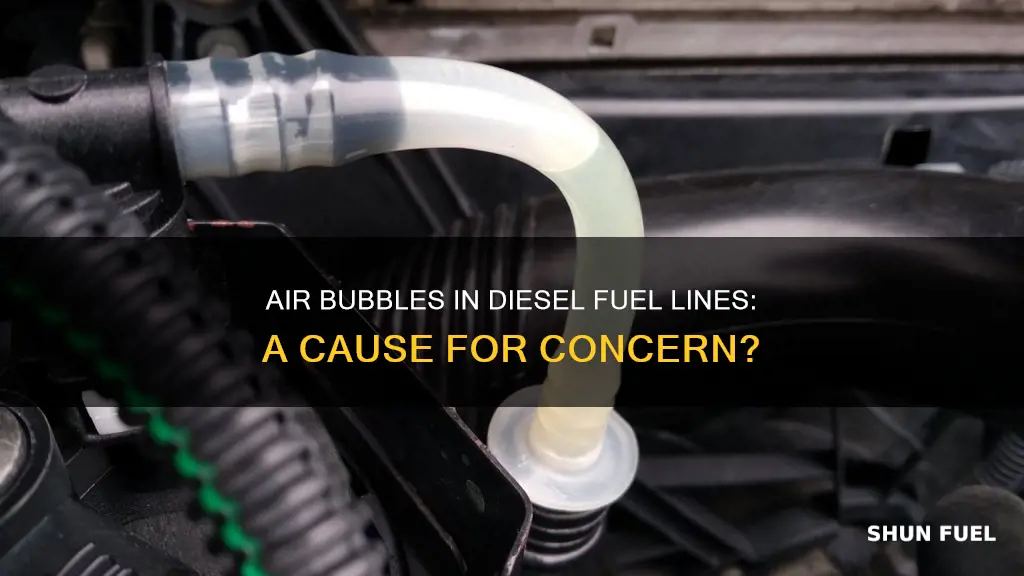
When it comes to diesel fuel lines, the presence of air bubbles can be a cause for concern. While some air in fuel lines is normal and can even help with fuel atomization, excessive air bubbles can lead to performance issues and potential damage to the engine. This paragraph aims to explore the implications of air bubbles in diesel fuel lines, discussing their potential effects on engine performance, fuel efficiency, and overall maintenance. By understanding the role of air bubbles, we can better appreciate the importance of proper fuel line maintenance and the potential benefits of eliminating or minimizing these bubbles.
Characteristics | Values |
---|---|
Air Bubbles in Diesel Fuel Line | It is generally not recommended to have air bubbles in the diesel fuel line. |
Impact on Engine Performance | Air bubbles can lead to reduced engine power, poor fuel efficiency, and even engine misfires. |
Engine Starting Issues | Presence of air bubbles may cause difficulty in starting the engine, especially in cold weather. |
Engine Noise | Air bubbles can cause knocking or pinging sounds in the engine, indicating potential performance issues. |
Fuel System Maintenance | Regularly check for air bubbles and ensure the fuel system is properly maintained to prevent long-term damage. |
Safety Considerations | Air bubbles can lead to fuel starvation, causing the engine to stall, which may be dangerous in certain situations. |
Engine Reliability | Over time, air bubbles can contribute to engine reliability issues and potential breakdowns. |
Engine Diagnostics | Engine diagnostic tools may detect issues related to air bubbles, indicating the need for further investigation. |
What You'll Learn
- Bubble Formation: Air bubbles in diesel fuel lines can be caused by high fuel temperatures or pressure fluctuations
- Performance Impact: Air bubbles can lead to reduced engine performance, increased fuel consumption, and potential engine damage
- Engine Knock: Bubble formation can trigger engine knock, causing rapid combustion and potential engine damage
- Fuel Efficiency: Air bubbles reduce fuel efficiency by causing engine misfires and incomplete combustion
- Maintenance: Regular maintenance, including fuel line inspections, can prevent air bubble issues and ensure optimal engine performance
Bubble Formation: Air bubbles in diesel fuel lines can be caused by high fuel temperatures or pressure fluctuations
The presence of air bubbles in diesel fuel lines is a common issue that can significantly impact engine performance and efficiency. While some air in the fuel is normal and can even be beneficial in small amounts, excessive bubbles can lead to various problems. Understanding the causes of bubble formation is crucial for maintaining a healthy diesel engine.
One primary cause of air bubble formation is high fuel temperatures. Diesel fuel is sensitive to heat, and when it is exposed to elevated temperatures, it can vaporize and create small bubbles. This phenomenon is more pronounced in fuel lines that are not properly insulated or are located in areas with high ambient temperatures. Over time, the repeated heating and cooling of fuel can lead to the formation of air pockets, especially if the fuel system is not designed to handle temperature variations effectively.
Pressure fluctuations in the fuel system also contribute to bubble formation. Diesel engines operate under varying pressure conditions, and sudden changes in pressure can displace air within the fuel lines. This is particularly evident during engine start-up when the fuel system is under rapid pressure changes. As the engine warms up, the fuel expands, and if the system is not sealed properly, air can be drawn in, leading to bubble formation. Additionally, issues with the fuel pump or injectors can cause pressure variations, further exacerbating the problem.
To mitigate these issues, it is essential to ensure that diesel fuel lines are properly insulated to maintain stable fuel temperatures. Using fuel line heaters or implementing temperature control systems can help prevent excessive heat-related bubble formation. Regular maintenance and inspections of the fuel system are also crucial to identify and address any potential issues. For example, checking for leaks, ensuring tight connections, and replacing worn-out components can prevent air infiltration and pressure-related problems.
In summary, air bubbles in diesel fuel lines are primarily caused by high fuel temperatures and pressure fluctuations. By understanding these causes, diesel engine owners and mechanics can take appropriate measures to minimize bubble formation, ensuring optimal engine performance and longevity. Proper insulation, temperature control, and regular maintenance are key to addressing this common issue in diesel fuel systems.
Winterizing Outboard: Fuel Line Disconnect: A Wise Move?
You may want to see also
Performance Impact: Air bubbles can lead to reduced engine performance, increased fuel consumption, and potential engine damage
Air bubbles in the diesel fuel line can have significant performance implications for any diesel engine. When air is introduced into the fuel system, it can lead to a range of issues that directly impact the engine's efficiency and overall performance. One of the primary consequences is a reduction in engine power output. Air bubbles disrupt the smooth flow of fuel, leading to incomplete combustion. This means that the engine doesn't receive the necessary amount of fuel to burn efficiently, resulting in a decrease in power and torque. As a result, the vehicle may feel less responsive and may struggle to accelerate or maintain speed.
The presence of air bubbles can also cause an increase in fuel consumption. When the engine is unable to burn fuel efficiently due to the bubbles, it compensates by using more fuel to achieve the required power output. This leads to higher fuel consumption, which is not only costly but also environmentally detrimental. Over time, this can significantly impact the vehicle's fuel economy, making it less efficient and potentially more expensive to operate.
Moreover, air bubbles in the diesel fuel line can lead to potential engine damage. The introduction of air can cause the fuel to become less lubricating, which is crucial for the engine's internal components. Without proper lubrication, the engine's parts can wear out faster, leading to increased maintenance requirements and potential breakdowns. In extreme cases, air bubbles can cause fuel to enter the engine's cylinders in a non-ideal state, leading to engine knocking or pinging, which can cause permanent engine damage.
To mitigate these performance issues, it is essential to ensure that the diesel fuel line is free from air bubbles. This can be achieved by regularly checking and maintaining the fuel system, including the fuel filter and injectors. Proper fuel system maintenance, such as using fuel stabilizers and ensuring the fuel tank is sealed correctly, can also help prevent the introduction of air bubbles. By addressing these factors, diesel engine owners can ensure optimal performance, fuel efficiency, and longevity of their vehicles.
Fuel Injector Linearity: A Matter of Efficiency and Precision
You may want to see also
Engine Knock: Bubble formation can trigger engine knock, causing rapid combustion and potential engine damage
The presence of air bubbles in the diesel fuel line is a common issue that can lead to several performance problems, with engine knock being one of the most critical. Engine knock, also known as pre-ignition, occurs when the air-fuel mixture in the engine's cylinders ignites prematurely before the piston reaches the top of its compression stroke. This phenomenon can cause significant damage to the engine over time.
When diesel fuel contains air bubbles, the fuel's ability to atomize and mix with air is compromised. During the injection process, these bubbles can disrupt the smooth flow of fuel, leading to uneven distribution. As a result, some areas of the combustion chamber may have a higher concentration of fuel, while others have none, creating a fuel-rich environment. This uneven fuel distribution can lead to the formation of hot spots within the engine, increasing the likelihood of engine knock.
The primary cause of engine knock due to bubble formation is the rapid combustion of the fuel-air mixture. When a fuel bubble encounters a flame or a hot spot, it can ignite, causing a small explosion. These mini-explosions can create a chain reaction, leading to the premature ignition of the main fuel-air mixture. The rapid combustion process generates high temperatures and pressures, which can cause the engine's components to fail, including the piston rings, valves, and even the engine block.
To prevent engine knock caused by air bubbles, it is essential to maintain the fuel system's integrity. Regularly checking for and addressing any fuel system leaks or blockages is crucial. Ensuring that the fuel filter is clean and functioning properly is also vital, as it helps remove any contaminants, including air bubbles, from the fuel before it reaches the engine. Additionally, using a fuel additive designed to improve fuel atomization can help reduce the likelihood of bubble formation and subsequent engine knock.
In summary, air bubbles in the diesel fuel line can have detrimental effects on engine performance and longevity. The formation of these bubbles can trigger engine knock, a condition that leads to rapid combustion and potential engine damage. By understanding the causes and implementing preventive measures, such as maintaining the fuel system and using appropriate additives, diesel engine owners can minimize the risks associated with air bubbles and ensure their engines operate efficiently and reliably.
Unleash the Power: Breaking Fuel Lines: A Quarry Decision
You may want to see also
Fuel Efficiency: Air bubbles reduce fuel efficiency by causing engine misfires and incomplete combustion
Air bubbles in the diesel fuel line can significantly impact engine performance and fuel efficiency. When air bubbles are present in the fuel, they can lead to a variety of issues that directly affect the engine's ability to run efficiently. One of the primary consequences is engine misfires. During the combustion process, the air-fuel mixture must be precise and well-mixed to ensure complete burning. However, when air bubbles are introduced, they can disrupt this process. The bubbles can cause localized areas of low fuel concentration, leading to incomplete combustion in those regions. This results in misfires, where the engine fails to ignite the fuel properly, causing a loss of power and potential performance issues.
The presence of air bubbles can also lead to a decrease in the overall fuel-air mixture quality. As the engine operates, the fuel and air must be continuously mixed and atomized to ensure optimal combustion. Air bubbles can disrupt this mixing process, leading to a less efficient fuel-air ratio. This imbalance can cause the engine to run rich (with an excess of fuel) or lean (with a lack of fuel), both of which are detrimental to performance and fuel efficiency. Rich mixtures can result in unburned fuel being expelled from the exhaust, leading to increased emissions and wasted fuel. Conversely, lean mixtures can cause the engine to run too hot, potentially damaging internal components.
Furthermore, air bubbles can contribute to increased engine wear and tear. When the engine misfires due to air bubbles, the additional stress on the engine components can lead to premature wear. The repetitive impact of misfires can cause damage to the engine's valves, pistons, and other critical parts, resulting in costly repairs or even engine failure. This is especially critical in heavy-duty applications where engines operate under high loads and temperatures.
To maintain optimal fuel efficiency and engine performance, it is essential to ensure that the diesel fuel line is free from air bubbles. This can be achieved through proper fuel system maintenance, including regular checks for leaks, ensuring the fuel pump is functioning correctly, and using fuel additives designed to reduce bubble formation. By minimizing air bubbles, diesel engines can operate more efficiently, reducing fuel consumption and improving overall performance.
GSXR 750 Fuel Line Leaks: Normal or Cause for Concern?
You may want to see also
Maintenance: Regular maintenance, including fuel line inspections, can prevent air bubble issues and ensure optimal engine performance
Regular maintenance is crucial for diesel engines to ensure they operate efficiently and reliably. One often overlooked but essential aspect of this maintenance is the inspection and care of the fuel lines. Diesel fuel lines, like any other component, can develop issues over time, and one common problem is the presence of air bubbles.
Air bubbles in the diesel fuel line can significantly impact engine performance. When these bubbles form, they can restrict the smooth flow of fuel, leading to a decrease in power output and potential engine misfires. This issue is particularly problematic as diesel engines rely on a precise and consistent fuel-air mixture for combustion. Even a small amount of air in the fuel can cause the engine to run poorly, resulting in reduced efficiency and potential long-term damage.
To prevent this, regular maintenance checks should include inspecting the fuel lines for any signs of air bubbles. This can be done by starting the engine and observing for any unusual noises or vibrations, which may indicate the presence of air pockets. Additionally, technicians can use specialized tools to measure the pressure and flow rate of the fuel, helping to identify any blockages or inconsistencies caused by air bubbles.
During these inspections, it is also important to check for any signs of fuel line damage, such as cracks, leaks, or corrosion. Fuel lines are susceptible to wear and tear, and any damage can lead to fuel contamination and the introduction of air bubbles. Replacing or repairing damaged fuel lines is a critical part of maintenance to ensure the engine receives clean, pressurized fuel.
By implementing a regular maintenance routine that includes fuel line inspections, you can effectively prevent air bubble issues. This proactive approach not only ensures the engine operates at its best but also helps extend the lifespan of the vehicle, saving time and money on potential repairs. It is a simple yet vital step in maintaining the health and performance of diesel engines.
Outboard Motor Fuel Line: To Disconnect or Not to Disconnect?
You may want to see also
Frequently asked questions
Air bubbles in the diesel fuel line can occur due to a few reasons. One common cause is the expansion of air when the fuel is heated, especially in hot climates or when the engine is running at high temperatures. This phenomenon is known as thermal expansion. Additionally, fuel lines can sometimes have small air pockets that are not fully purged during the fueling process, leading to the formation of bubbles.
Yes, air bubbles in diesel fuel can cause significant issues. When air enters the fuel system, it can lead to poor engine performance, reduced power, and even engine misfires. Air bubbles can also cause the engine to run roughly and may result in increased fuel consumption. In some cases, air bubbles can even cause the engine to stall or fail to start.
To prevent air bubbles, it is essential to ensure that the fuel system is properly vented and purged. When refueling, make sure to leave the fuel cap open for a few minutes to allow air to enter the tank and displace any existing bubbles. Regularly checking and maintaining the fuel filter can also help, as it can trap small air bubbles and ensure clean fuel delivery.
There are a few indicators that may suggest the presence of air bubbles. Engine hesitation, stalling, or rough idling are common signs. You might also notice a decrease in power and fuel efficiency. In some cases, you may hear a knocking or rattling sound coming from the engine, which could be caused by air bubbles disrupting the fuel-air mixture.