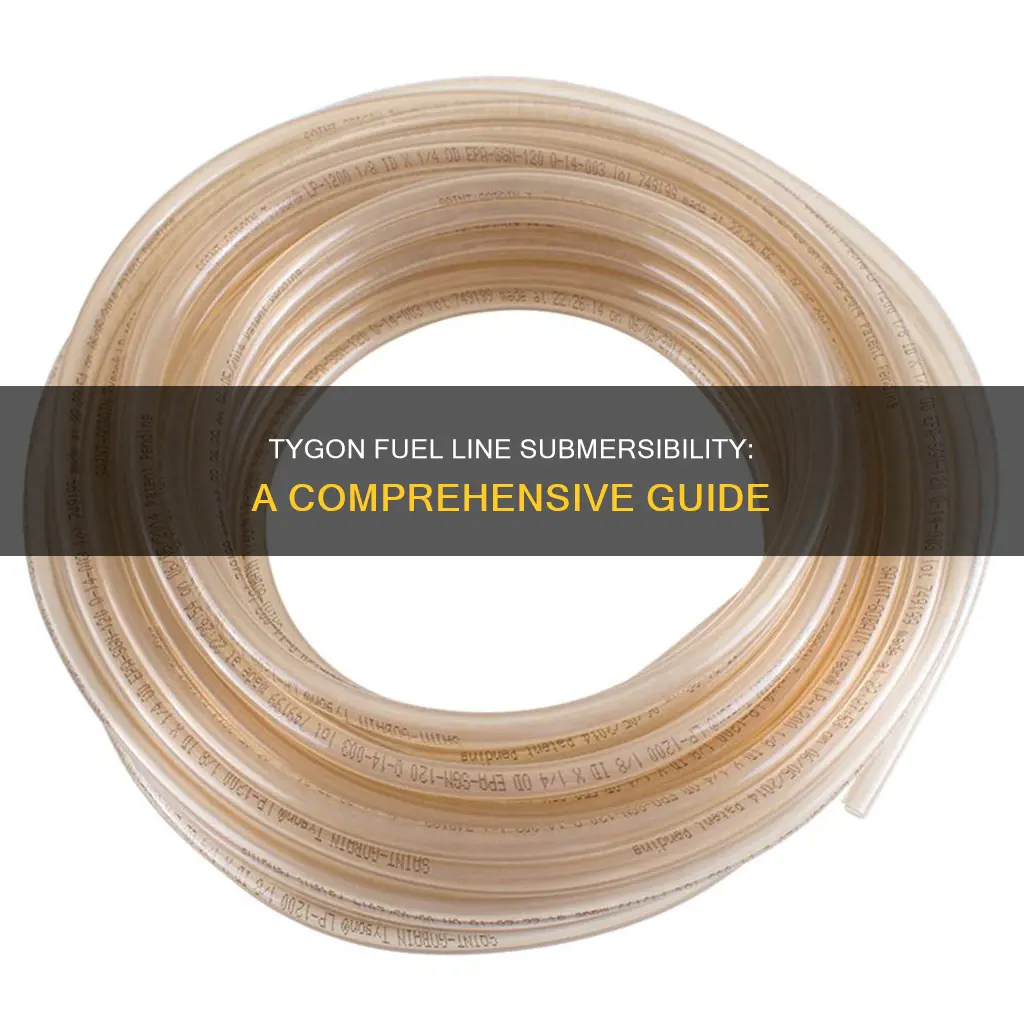
Tygon fuel lines are a popular choice for many applications, but their suitability for submersion in water or other liquids is a common question. Tygon offers a range of fuel lines designed specifically for use in submerged environments, ensuring they can withstand the challenges of fuel transport in various conditions. These lines are engineered to resist degradation from water, making them ideal for use in marine or aquatic settings where traditional fuel lines might not perform optimally. Understanding the specific characteristics of Tygon's submersible fuel lines is essential for anyone looking to ensure the reliability and safety of their fuel systems in demanding environments.
Characteristics | Values |
---|---|
Material | Tygon is a brand name for a range of flexible, transparent, and resistant materials. The specific material used for fuel lines can vary, but common options include Tygon 638, Tygon 638 Plus, and Tygon 638 Flex. |
Temperature Range | Tygon fuel lines are designed to withstand a wide range of temperatures, typically from -40°F to 250°F (-40°C to 121°C). |
Chemical Resistance | These lines are resistant to various chemicals commonly found in fuels, such as gasoline, diesel, ethanol, and biofuels. They can handle exposure to these substances without degradation. |
Flexibility | Tygon fuel lines are known for their flexibility, allowing for easy installation and routing in tight spaces. |
Submersibility | Yes, Tygon fuel lines are generally considered submersible, meaning they can be used in submerged applications without compromising their performance. This makes them suitable for use in boats, marine environments, and other water-related applications. |
Pressure Rating | The pressure rating can vary depending on the specific Tygon material and its formulation. Some lines may be rated for high-pressure applications, while others are designed for low-pressure use. |
Color | Typically, Tygon fuel lines are clear or translucent, allowing for easy inspection of the fuel level and quality. |
Application | These lines are commonly used in fuel systems of vehicles, boats, and other equipment where fuel needs to be transported and delivered efficiently. |
Brand | Tygon is a brand of Saint-Gobain Performance Plastics, a global leader in the production of specialized materials. |
What You'll Learn
- Tygon Fuel Line Material: Tygon is a flexible, chemical-resistant material used for fuel lines
- Submersibility Testing: Submersibility testing ensures the fuel line can withstand water pressure
- Fuel Line Diameter: Tygon fuel lines come in various diameters for different applications
- Temperature Range: Tygon can handle a wide temperature range, making it suitable for various climates
- Chemical Compatibility: Tygon is compatible with a wide range of fuels and chemicals
Tygon Fuel Line Material: Tygon is a flexible, chemical-resistant material used for fuel lines
Tygon is a versatile and widely recognized material in the automotive and marine industries, particularly for its application in fuel lines. This innovative material is renowned for its flexibility and exceptional chemical resistance, making it an ideal choice for various fuel line systems. When it comes to submersible fuel lines, Tygon's properties become even more advantageous.
The flexibility of Tygon is a key feature that sets it apart from traditional fuel line materials. It can easily bend and conform to the unique shapes and contours of different fuel tanks and engines, ensuring a secure and reliable connection. This flexibility is crucial for submersible fuel lines, as it allows for smooth installation and movement, even in tight or confined spaces. Whether it's a boat engine or an underwater vehicle, Tygon's flexibility ensures a snug fit without compromising performance.
Chemical resistance is another critical aspect of Tygon's performance. Fuel lines are exposed to various substances, including gasoline, diesel, and other chemicals, which can lead to degradation and potential leaks over time. Tygon, however, is specifically engineered to withstand these harsh environments. Its chemical-resistant nature prevents deterioration, ensuring that the fuel lines remain intact and functional, even when exposed to different fuel types and additives. This property is essential for maintaining the efficiency and safety of submersible fuel systems.
In the context of submersible applications, Tygon's ability to resist chemicals becomes even more vital. Submersible fuel lines are often exposed to water, oil, and other contaminants, which can cause traditional materials to deteriorate rapidly. Tygon's chemical resistance ensures that the fuel lines remain stable and reliable, even in these challenging conditions. This makes it an excellent choice for marine vessels, underwater equipment, and any application where fuel lines are susceptible to water or chemical exposure.
Furthermore, Tygon's flexibility and chemical resistance contribute to its durability. It can withstand the constant movement and vibrations associated with submersible fuel systems, ensuring a long-lasting solution. This material is designed to maintain its integrity over extended periods, reducing the risk of fuel leaks and system failures. By choosing Tygon fuel lines, users can have confidence in the reliability and longevity of their submersible fuel systems.
In summary, Tygon fuel line material offers a unique combination of flexibility and chemical resistance, making it an excellent choice for submersible applications. Its ability to adapt to various shapes, resist harsh chemicals, and maintain durability ensures a secure and efficient fuel line system. When considering submersible fuel lines, Tygon's properties provide a reliable and long-lasting solution for both automotive and marine environments.
Fuel Line Placement: Optimizing Chainsaw Performance and Safety
You may want to see also
Submersibility Testing: Submersibility testing ensures the fuel line can withstand water pressure
Submersibility testing is a critical process that ensures the integrity and reliability of fuel lines, especially in applications where they might be exposed to water or submerged in liquids. When considering the submersibility of a Tygon fuel line, it is essential to understand the specific requirements and procedures involved in this testing.
The primary goal of submersibility testing is to evaluate the fuel line's ability to function optimally while being exposed to water pressure. This is particularly crucial in industries such as marine, automotive, and industrial, where fuel lines are often subjected to varying levels of water immersion. By conducting this test, engineers and manufacturers can ensure that the fuel line remains intact, maintains its functionality, and does not compromise the overall system's performance.
During the submersibility test, the fuel line is subjected to controlled water pressure, simulating real-world conditions. This involves immersing the line in a water-filled chamber and applying pressure to mimic the forces it might encounter in service. The test parameters, such as pressure levels and duration, are carefully chosen to represent the expected operating conditions. For Tygon fuel lines, which are commonly used for their flexibility and chemical resistance, the testing protocol may include varying water temperatures and flow rates to assess their behavior under different scenarios.
In this test, the fuel line's performance is meticulously observed and recorded. This includes checking for any signs of leakage, damage, or degradation in material properties. The line's flexibility, durability, and ability to retain its shape under pressure are also evaluated. If the Tygon fuel line passes the submersibility test, it demonstrates its suitability for applications requiring water resistance and pressure tolerance.
Submersibility testing is a comprehensive process that provides valuable insights into the fuel line's performance and reliability. It ensures that the chosen material, in this case, Tygon, meets the required standards for submersibility. By adhering to these testing procedures, manufacturers can confidently select the appropriate fuel line for their specific applications, knowing that it can withstand the challenges posed by water immersion and pressure.
Street Avenger Fuel Line: Unleash the Power with the Right Choice
You may want to see also
Fuel Line Diameter: Tygon fuel lines come in various diameters for different applications
Tygon fuel lines are an essential component for any fuel transfer system, offering a range of benefits that make them a popular choice among professionals and enthusiasts alike. One of the key advantages of Tygon is its availability in various diameters, allowing for customization based on specific application requirements.
The diameter of a fuel line is a critical factor in determining its performance and suitability for different tasks. Tygon offers a comprehensive selection of diameters to cater to a wide range of applications. For instance, smaller diameters, typically ranging from 1/4 inch to 3/8 inch, are ideal for high-pressure applications and are commonly used in racing environments where precise fuel delivery is crucial. These smaller lines provide excellent flexibility and can withstand the demands of high-performance engines.
On the other hand, larger diameters, such as 1/2 inch or 3/4 inch, are designed for low-pressure applications and are often used in everyday automotive or marine settings. These larger lines offer increased flow capacity, making them suitable for systems that require a steady and consistent fuel supply. The choice of diameter ensures that the fuel line can handle the required volume and pressure, optimizing the performance of the entire fuel system.
Tygon's versatility in fuel line diameters allows users to select the most appropriate option for their specific needs. Whether it's a high-performance racing application or a standard automotive setup, Tygon provides a tailored solution. This customization ensures that the fuel lines are not only submersible but also optimized for performance, safety, and longevity in various environments.
In summary, Tygon fuel lines offer a unique advantage with their customizable diameters, catering to diverse applications. From high-pressure racing environments to everyday low-pressure systems, Tygon provides a reliable and efficient solution. Understanding the available diameters and their respective applications is essential for anyone looking to optimize their fuel transfer system, ensuring a seamless and safe operation.
Fuel Line Size for Predator Generators: A Quick Guide
You may want to see also
Temperature Range: Tygon can handle a wide temperature range, making it suitable for various climates
Tygon fuel lines are renowned for their versatility and durability, especially when it comes to temperature resistance. This feature is a game-changer for various applications, ensuring optimal performance in diverse climates. The material's ability to withstand a wide temperature range is a significant advantage, catering to both hot and cold environments without compromising its structural integrity.
In regions with extreme temperatures, Tygon's temperature-resistant properties are invaluable. During scorching summers, the fuel lines can handle the heat without warping or degrading, ensuring a consistent and reliable fuel supply. Similarly, in colder climates, Tygon's flexibility and resistance to brittleness in low temperatures make it an ideal choice for fuel lines. This is particularly important in industries where temperature fluctuations are common, such as agriculture, construction, and outdoor power equipment.
The temperature range of Tygon is typically between -40°F (-40°C) to 460°F (240°C), making it suitable for a wide array of applications. This versatility allows for its use in various industries, including automotive, marine, and aviation, where temperature variations are a constant challenge. For instance, in the automotive sector, Tygon fuel lines can be used in both high-performance racing cars and everyday vehicles, ensuring a reliable fuel supply regardless of the climate.
Furthermore, Tygon's temperature resistance contributes to its overall safety and longevity. By withstanding extreme temperatures, the material reduces the risk of fuel leaks, which can be a critical issue in high-temperature environments. This feature also ensures that the fuel lines maintain their structural integrity over time, providing a long-lasting solution for fuel transportation and distribution.
In summary, Tygon's ability to handle a wide temperature range is a key factor in its popularity and versatility. This feature makes it an excellent choice for fuel lines in various climates, ensuring optimal performance and safety in diverse environmental conditions. Whether it's the scorching heat of summer or the freezing cold of winter, Tygon fuel lines are designed to deliver reliable and consistent performance.
Fuel Injection Line Repair: A Step-by-Step Guide to Fixing Leaks
You may want to see also
Chemical Compatibility: Tygon is compatible with a wide range of fuels and chemicals
Tygon fuel lines are renowned for their versatility and compatibility with various substances, making them a popular choice for fuel delivery systems. When it comes to chemical compatibility, Tygon excels, ensuring that it can withstand exposure to a wide array of fuels and chemicals. This feature is particularly crucial in the automotive and industrial sectors, where fuel lines are susceptible to a multitude of substances.
The compatibility of Tygon with different chemicals is a result of its unique composition. Tygon is typically made from a blend of ethylene oxide and propylene oxide, creating a material that is both flexible and durable. This composition allows it to resist degradation and maintain its structural integrity when exposed to various fuels and chemicals. Common fuels that Tygon can handle include gasoline, diesel, jet fuel, and even biofuels, ensuring its applicability in a diverse range of vehicles and machinery.
In addition to fuels, Tygon is also compatible with numerous industrial chemicals. It can withstand exposure to acids, bases, solvents, and even some corrosive substances, making it suitable for use in chemical processing plants, laboratories, and other industrial settings. The material's ability to resist chemical attack ensures that it remains intact and functional, even when exposed to harsh environments.
The compatibility of Tygon with a wide range of substances is further enhanced by its temperature resistance. It can operate effectively across a broad temperature range, from sub-zero temperatures to high heat, ensuring that it remains flexible and functional in various weather conditions. This temperature stability is crucial for maintaining the integrity of fuel lines in extreme environments.
Furthermore, Tygon's compatibility with a wide range of chemicals and fuels makes it a cost-effective solution for fuel delivery systems. Its ability to withstand exposure to various substances reduces the need for frequent replacements, saving both time and money for vehicle owners and industrial operators. This makes Tygon an excellent choice for those seeking a reliable and versatile fuel line material.
Mastering the Art of Removing Saturn SC1 Fuel Line Connectors: A Step-by-Step Guide
You may want to see also
Frequently asked questions
Yes, Tygon fuel lines are designed to be submersible and can withstand exposure to water and other liquids. They are commonly used in fuel delivery systems for boats, jet skis, and other watercraft.
Tygon's submersible fuel lines are made from a special formulation of thermoplastic elastomer, which provides excellent flexibility, durability, and resistance to abrasion. This material ensures the lines can handle the rigors of submerged environments without compromising performance.
Absolutely! Tygon offers a range of submersible fuel lines designed for high-pressure systems. These lines are engineered to maintain their structural integrity and flexibility even under significant pressure, making them ideal for applications where fuel is pumped at higher velocities.
Installation is relatively straightforward. Start by cleaning the fuel line ports and ensuring a tight seal. Then, carefully push the fuel line into the port, ensuring it is fully seated. Use fuel line connectors or clamps to secure the line in place. Always follow the manufacturer's guidelines for proper installation and maintenance to ensure optimal performance and longevity.