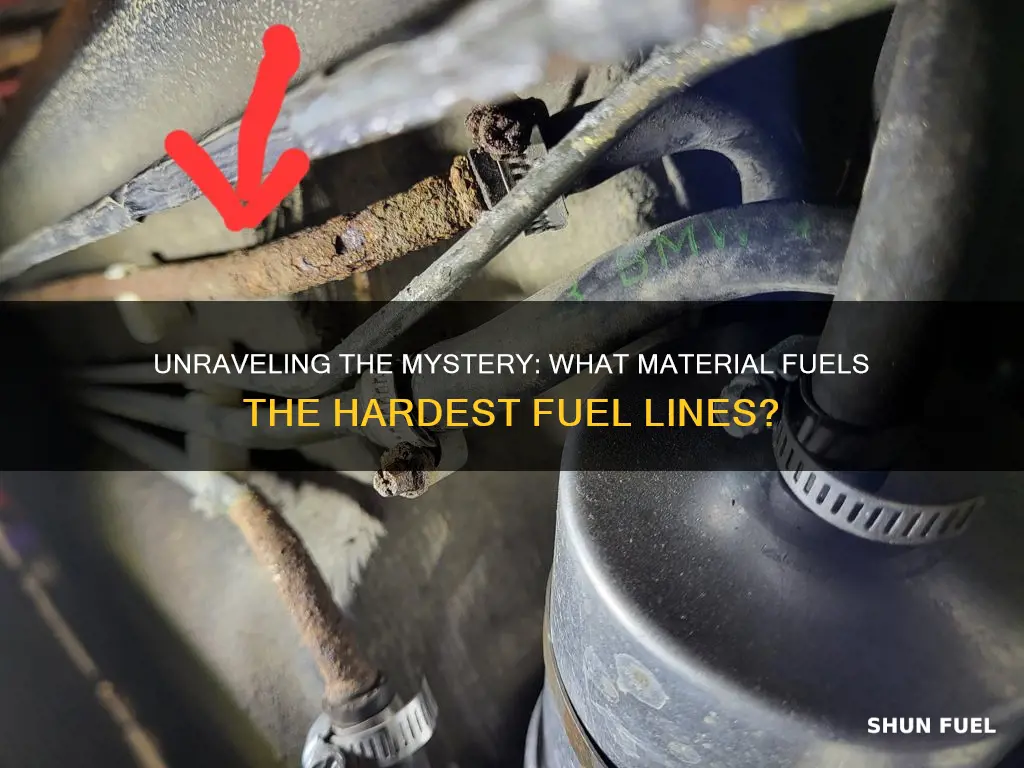
The fuel lines in vehicles are crucial for delivering fuel from the tank to the engine, and the material used for these lines can significantly impact performance and durability. When it comes to the hardest fuel lines, the material of choice is often a high-performance synthetic rubber compound, such as neoprene or EPDM (ethylene propylene diene monomer). These compounds are known for their exceptional resistance to heat, cold, and fuel chemicals, making them ideal for withstanding the demanding conditions inside an engine bay. Additionally, they are flexible, allowing for easy installation and routing, while also maintaining their structural integrity over time. This combination of properties ensures that the fuel lines remain robust and reliable, contributing to the overall efficiency and longevity of the vehicle's fuel system.
Characteristics | Values |
---|---|
Material | The most common material for hard fuel lines is steel, often with a protective coating. |
Hardness | Steel fuel lines are typically made with a high-strength, low-alloy (HSLA) steel, which provides excellent hardness and durability. |
Temperature Resistance | These lines can withstand a wide range of temperatures, from -40°F to 300°F (-40°C to 150°C), making them suitable for various climates and engine operations. |
Flexibility | Despite their hardness, HSLA steel fuel lines offer flexibility to accommodate engine movement and vibrations without cracking or breaking. |
Corrosion Resistance | The steel is often coated with a protective layer, such as zinc or a specialized paint, to prevent corrosion and ensure long-term reliability. |
Pressure Rating | They are designed to handle high-pressure fuel systems, often exceeding 100 psi (pounds per square inch) to meet the demands of modern engines. |
Compatibility | HSLA steel is compatible with a wide range of fuels, including gasoline, diesel, and biofuels, making it a versatile choice for various vehicle applications. |
Cost | While HSLA steel may be more expensive than some alternatives, its durability and longevity can justify the higher cost over time. |
What You'll Learn
- Material Selection: Hard fuel lines are often made from durable materials like steel, brass, or stainless steel
- Reinforcement: Reinforcement techniques like braiding or spiral winding enhance the strength and flexibility of fuel lines
- Temperature Resistance: Fuel lines must withstand extreme temperatures, often with materials like silicone or fluoropolymer
- Pressure Rating: High-pressure fuel lines require materials with specific pressure ratings to ensure safety and performance
- Corrosion Resistance: Materials like stainless steel or coated brass prevent corrosion in harsh environments
Material Selection: Hard fuel lines are often made from durable materials like steel, brass, or stainless steel
When it comes to hard fuel lines, the choice of material is crucial for ensuring durability and reliability in harsh operating conditions. These fuel lines are designed to withstand high pressure, extreme temperatures, and exposure to various chemicals, making the selection of the right material a critical aspect of their construction.
One of the most common materials used for hard fuel lines is steel. Steel offers excellent strength and durability, making it ideal for applications where the fuel line may be subjected to intense pressure and mechanical stress. Carbon steel, in particular, is often chosen due to its high tensile strength and resistance to corrosion. This material can handle the demanding environments found in engines and industrial machinery, ensuring a long-lasting and reliable fuel supply.
Brass is another popular choice for hard fuel lines. This material is known for its superior malleability and ductility, allowing for easier installation and customization. Brass fuel lines are often preferred in situations where flexibility is essential, such as in automotive applications where the fuel lines need to navigate through tight spaces. Despite its flexibility, brass maintains its strength and resistance to wear, making it a reliable option for fuel transportation.
For those seeking even greater corrosion resistance, stainless steel is the material of choice. This alloy contains a minimum of 10.5% chromium, which forms a protective oxide layer on the surface, preventing rust and corrosion. Stainless steel fuel lines are highly resistant to the effects of fuel, oil, and other chemicals, making them ideal for both industrial and marine environments. The added benefit of stainless steel is its ability to maintain its structural integrity over an extended period, ensuring a safe and efficient fuel supply.
In summary, the selection of materials for hard fuel lines is a critical consideration. Steel, brass, and stainless steel are the primary choices, each offering unique advantages. Steel provides strength and durability, brass offers flexibility, and stainless steel ensures superior corrosion resistance. The right material choice will depend on the specific application and environmental conditions, ensuring the fuel lines can withstand the challenges they face.
Unveiling the 1967 Ford LTD's Fuel Line Route
You may want to see also
Reinforcement: Reinforcement techniques like braiding or spiral winding enhance the strength and flexibility of fuel lines
Reinforcement techniques play a crucial role in enhancing the performance and durability of fuel lines, ensuring they can withstand the demanding conditions of automotive environments. One common method is braiding, which involves intertwining multiple strands of material around the fuel line's core. This process creates a strong, flexible structure that can resist wear and tear, making it ideal for fuel lines that need to navigate through tight spaces and endure constant movement. By braiding the fuel line, manufacturers can improve its overall strength without compromising its ability to bend and adjust to different angles.
Spiral winding is another reinforcement technique that significantly contributes to the hardness and reliability of fuel lines. This process involves winding a reinforcing material, such as a metal wire or fabric, around the fuel line in a spiral pattern. The spiral winding provides additional support and protection, especially in areas where the fuel line is prone to damage, such as under the vehicle's body or near sharp edges. This method ensures that the fuel line remains intact and maintains its integrity even when subjected to vibrations and external pressures.
The combination of braiding and spiral winding offers a comprehensive solution to reinforce fuel lines. By intertwining and winding reinforcing materials, manufacturers can create a robust structure that withstands the harsh conditions of fuel transportation. This technique is particularly beneficial for high-performance vehicles or those operating in extreme environments, where fuel lines are exposed to increased stress and potential hazards. The reinforced fuel lines can then efficiently deliver fuel while maintaining their structural integrity.
In addition to the reinforcement techniques, the choice of materials also contributes to the overall hardness and performance of fuel lines. Manufacturers often select materials like high-density polyethylene (HDPE) or reinforced rubber compounds, which offer excellent resistance to fuel degradation and environmental factors. These materials, combined with the reinforcement techniques, ensure that the fuel lines remain flexible yet robust, capable of withstanding the constant expansion and contraction caused by temperature changes.
By employing these reinforcement methods, fuel lines can achieve a balance between flexibility and strength, ensuring they can navigate through the vehicle's frame and engine compartment without compromising performance. The result is a fuel line system that is both durable and efficient, capable of delivering fuel reliably while maintaining its structural integrity over an extended period. This level of reinforcement is essential for maintaining the overall health and longevity of the vehicle's fuel system.
Choosing the Right Fuel Line: Size Matters!
You may want to see also
Temperature Resistance: Fuel lines must withstand extreme temperatures, often with materials like silicone or fluoropolymer
Fuel lines are an essential component of any vehicle's fuel system, responsible for transporting fuel from the tank to the engine. These lines must be designed to withstand the harsh conditions of the engine bay, including extreme temperatures, vibrations, and chemical exposure. One of the most critical aspects of fuel line construction is temperature resistance, as these lines are often subjected to a wide range of temperatures, from freezing cold to scorching hot.
To ensure optimal performance and longevity, fuel lines are typically manufactured using materials that offer excellent temperature resistance. Silicone and fluoropolymer are two popular choices for fuel line construction due to their ability to maintain flexibility and structural integrity across a wide temperature range. Silicone, for instance, is known for its stability and resistance to both high and low temperatures, making it an ideal material for fuel lines. It can withstand temperatures ranging from -60°C to 200°C (-76°F to 392°F), which covers the typical operating conditions of most vehicles. This material's flexibility also ensures that the fuel lines can accommodate the vibrations and movements experienced during vehicle operation.
Fluoropolymer, another excellent temperature-resistant material, offers even more impressive performance. This material can handle temperatures up to 250°C (482°F), making it suitable for high-performance vehicles or those operating in extreme environments. Fluoropolymer's exceptional thermal stability and resistance to chemical degradation make it a preferred choice for fuel lines in racing cars or aircraft, where temperature fluctuations and fuel composition can be more extreme.
The choice of material for fuel lines is crucial to ensure the reliability and safety of the vehicle's fuel system. By using temperature-resistant materials like silicone or fluoropolymer, manufacturers can ensure that fuel lines remain flexible, durable, and capable of withstanding the demanding conditions of the engine bay. This attention to detail in material selection contributes to the overall performance and longevity of the vehicle.
Mastering Carb Fuel Lines: A Comprehensive Guide
You may want to see also
Pressure Rating: High-pressure fuel lines require materials with specific pressure ratings to ensure safety and performance
When it comes to high-pressure fuel lines, the choice of material is critical to ensure the safety and performance of the system. These lines are designed to withstand the intense forces and pressures generated by the engine, and using the right material is essential to prevent failures and potential hazards. The pressure rating of a material is a key factor in determining its suitability for this application.
High-pressure fuel lines are typically exposed to pressures that can range from 100 to 300 psi or even higher, depending on the engine's specifications. To handle these extreme conditions, the material must possess exceptional mechanical properties, including high tensile strength and excellent resistance to deformation. Materials with inadequate pressure ratings may fail, leading to potential engine damage or even dangerous situations where fuel could leak or ignite.
One of the most commonly used materials for high-pressure fuel lines is steel, specifically stainless steel alloys. These alloys, such as 304 or 316 stainless steel, offer superior strength and corrosion resistance, making them ideal for fuel systems. The pressure rating of stainless steel can vary, but it often exceeds the requirements for high-pressure applications, ensuring a safe and reliable performance.
Another popular choice is brass, which provides good strength and durability. Brass alloys, like C260 or C275, are often used in fuel lines due to their ability to maintain structural integrity under pressure. The pressure rating of brass can vary, but it is generally suitable for high-pressure fuel systems, especially when combined with proper design and manufacturing techniques.
In some cases, engineers may opt for composite materials, such as carbon fiber-reinforced polymers (CFRP). These materials offer excellent strength-to-weight ratios and can provide high pressure ratings. However, they are more expensive and may require specialized manufacturing processes, making them less common in standard fuel line applications.
In summary, the pressure rating of a material is a critical consideration when designing high-pressure fuel lines. Materials like stainless steel and brass are commonly used due to their ability to withstand the forces and pressures involved. Proper selection and manufacturing processes ensure that these fuel lines meet the required safety and performance standards, contributing to the overall reliability of the engine system.
Understanding the Fuel Pump Pulse Line: A Vital Component
You may want to see also
Corrosion Resistance: Materials like stainless steel or coated brass prevent corrosion in harsh environments
When it comes to fuel lines, especially those used in harsh environments, corrosion resistance is a critical factor to consider. Corrosion can lead to a variety of issues, including reduced performance, increased maintenance requirements, and even safety hazards. To combat this, engineers and manufacturers often turn to materials that are inherently resistant to corrosion.
One of the most commonly used materials for fuel lines is stainless steel. This material is known for its exceptional corrosion resistance, making it ideal for use in a wide range of applications. Stainless steel is an alloy that contains a minimum of 10.5% chromium, which forms a protective oxide layer on the surface when exposed to oxygen. This layer, often referred to as the 'passivation layer', prevents further corrosion and ensures the material's longevity. The addition of other elements, such as nickel and molybdenum, further enhances its corrosion resistance, making it suitable for even the most demanding environments.
Coated brass is another material that offers excellent corrosion resistance. Brass, an alloy of copper and zinc, is naturally susceptible to corrosion. However, by applying a protective coating, such as a layer of zinc or a specialized alloy, the corrosion resistance of brass can be significantly improved. This coating acts as a barrier, preventing the underlying brass from coming into contact with corrosive substances. The use of coated brass is particularly common in fuel lines for marine and outdoor applications, where exposure to moisture, salt, and other corrosive elements is prevalent.
The choice between stainless steel and coated brass often depends on the specific requirements of the application. Stainless steel is generally more durable and can withstand higher temperatures, making it suitable for high-pressure systems and extreme environments. On the other hand, coated brass offers a cost-effective solution for applications where temperature and pressure are not as critical factors. Its ease of manufacturing and availability make it a popular choice for a wide range of fuel line applications.
In addition to these materials, some manufacturers also utilize specialized coatings and alloys to enhance corrosion resistance. For instance, Teflon-coated fuel lines are used in high-temperature applications, providing excellent resistance to heat and corrosion. Similarly, stainless steel alloys with higher levels of chromium and nickel, such as 316L, are employed in critical applications where maximum corrosion resistance is required.
In summary, when designing fuel lines for harsh environments, corrosion resistance is a key consideration. Materials like stainless steel and coated brass offer reliable protection against corrosion, ensuring the longevity and performance of the fuel lines. The choice of material depends on the specific application, with each material offering unique advantages in terms of durability, cost, and environmental resistance.
Houston Fuel Lines: Uncovering Hidden Issues and Solutions
You may want to see also
Frequently asked questions
The most common material for hard fuel lines is steel, specifically a type of carbon steel known as "hardened steel." This material is chosen for its durability and ability to withstand high pressure and temperatures, making it ideal for fuel lines in engines and other high-performance applications.
Hardened steel offers several advantages over other materials like aluminum or plastic. It has excellent tensile strength, which means it can handle the forces exerted by fuel under pressure without deforming or breaking. Additionally, steel's high melting point ensures it can withstand the heat generated by fuel combustion.
Yes, while steel is the most prevalent, some manufacturers also use brass or bronze for fuel lines in certain applications. These materials are often preferred for their corrosion resistance and ability to maintain a consistent diameter over time. However, steel remains the go-to choice for its superior strength and cost-effectiveness.