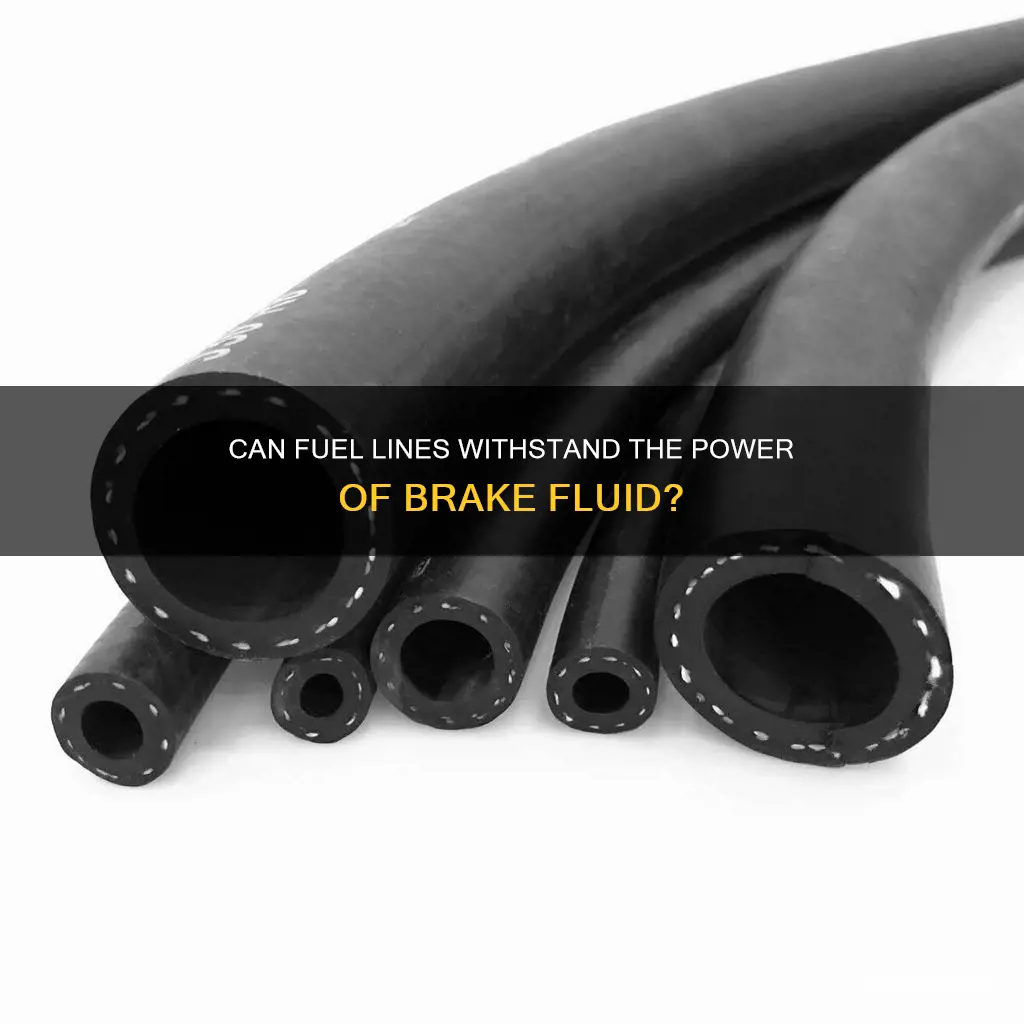
The compatibility of fuel lines with brake fluid is a critical consideration in vehicle maintenance. When choosing the right materials for fuel lines, it's essential to understand their resistance to brake fluid, as prolonged exposure can lead to degradation and potential system failures. This paragraph will explore the factors that determine the resistance of fuel lines to brake fluid and the implications of their interaction.
What You'll Learn
- Material Compatibility: Is the fuel line made from materials that resist brake fluid degradation
- Flexibility: Can the fuel line flex without compromising its resistance to brake fluid
- Pressure Resistance: Does the fuel line withstand pressure changes caused by brake fluid
- Temperature Tolerance: Can the fuel line handle temperatures affected by brake fluid
- Longevity: Will the fuel line remain resistant to brake fluid over its lifespan
Material Compatibility: Is the fuel line made from materials that resist brake fluid degradation?
When considering the compatibility of fuel lines with brake fluid, it is crucial to examine the materials used in their construction. The primary concern is whether the fuel line material can withstand the corrosive effects of brake fluid over time. Brake fluid, often containing glycol ethers or silicone-based compounds, can have detrimental effects on certain materials, leading to degradation, swelling, or even chemical breakdown.
One of the key materials used in fuel lines is rubber, which is commonly chosen for its flexibility and durability. However, not all rubber compounds are created equal in terms of compatibility with brake fluid. Natural rubber, for instance, is susceptible to attack by brake fluid, causing it to become brittle and crack over time. This can result in fuel leaks and potential safety hazards. On the other hand, synthetic rubbers, such as neoprene or butyl rubber, offer improved resistance to brake fluid degradation due to their enhanced chemical stability.
Another important consideration is the use of plastic materials in fuel lines. Some plastics, like polyvinyl chloride (PVC) or certain types of thermoplastic elastomers, have shown promising resistance to brake fluid. These materials are less likely to swell or dissolve when exposed to brake fluid, making them suitable for fuel line applications. However, it is essential to ensure that the specific plastic used meets the required standards and is compatible with the particular brake fluid formulation.
In addition to rubber and plastic, metal fuel lines are also an option, particularly in high-performance or racing applications. Metal, such as stainless steel, offers excellent resistance to corrosion and chemical attack, making it highly compatible with brake fluid. While metal fuel lines may be more rigid compared to their rubber or plastic counterparts, they provide a reliable and long-lasting solution for fuel transport in vehicles with brake systems.
To ensure optimal performance and longevity, it is imperative to select fuel lines made from materials that have been specifically engineered to resist brake fluid degradation. Manufacturers often provide compatibility information or recommendations for their products, ensuring that the chosen fuel line is suitable for the specific brake fluid used in the vehicle. By carefully considering the material compatibility, vehicle owners and mechanics can make informed decisions to maintain the integrity of the fuel system and overall vehicle safety.
Understanding CPE Fuel Line: A Comprehensive Guide
You may want to see also
Flexibility: Can the fuel line flex without compromising its resistance to brake fluid?
The compatibility of a fuel line with brake fluid is a critical consideration in vehicle maintenance, especially for those with modified or classic cars. When it comes to the flexibility of the fuel line, it is essential to understand how this feature interacts with its resistance to brake fluid.
Flexibility is a key requirement for fuel lines, as they need to accommodate various engine movements and vibrations during operation. The ability to flex without kinking or bending excessively is crucial to ensure a consistent and reliable fuel supply to the engine. However, this flexibility must not compromise the material's resistance to brake fluid, which can be a corrosive and damaging substance.
Brake fluid is designed to transmit force through the braking system, and it contains additives that can be harmful to certain materials over time. When selecting a fuel line, engineers must choose materials that can withstand the chemical properties of brake fluid while still allowing for the necessary flexibility. This balance is often achieved through the use of specialized rubber compounds or synthetic materials that offer both durability and pliability.
One approach to achieving this balance is to incorporate a fuel line with a flexible inner core and a protective outer layer. The inner core provides the necessary flexibility to accommodate engine movements, while the outer layer ensures that the fuel line remains resistant to the corrosive effects of brake fluid. This design allows for a longer lifespan and improved performance, ensuring that the fuel system remains reliable even in demanding conditions.
In summary, the flexibility of a fuel line is essential for its functionality, but it must be carefully managed to maintain its resistance to brake fluid. By selecting appropriate materials and design considerations, engineers can create fuel lines that offer both flexibility and durability, ensuring a safe and efficient fuel supply to the engine. This is particularly important in high-performance vehicles or those with modified braking systems.
NPT Sizes: Unraveling the Mystery of 5/16 Fuel Lines
You may want to see also
Pressure Resistance: Does the fuel line withstand pressure changes caused by brake fluid?
When considering the compatibility of fuel lines with brake fluid, it's crucial to understand the specific requirements and challenges posed by the interaction between these two substances. One critical aspect is the pressure resistance of the fuel line, which is directly influenced by the presence of brake fluid.
Brake fluid operates under high-pressure conditions within the braking system, and any fuel line used in conjunction with this fluid must be designed to withstand these pressure changes. The fuel line's ability to resist pressure variations is essential to ensure the safe and efficient operation of the vehicle. If the fuel line is not pressure-resistant, it may lead to potential issues such as fuel leakage, contamination, or even system failure.
The pressure resistance of a fuel line is typically determined by its construction and material properties. High-quality fuel lines are often made from materials like stainless steel or reinforced rubber compounds, which offer excellent durability and flexibility. These materials can withstand the fluctuating pressures caused by brake fluid, ensuring that the fuel remains contained and delivered to the engine without any leaks or spills.
Furthermore, the design of the fuel line connectors and fittings plays a vital role in maintaining pressure resistance. Proper sealing and sealing materials that can handle the chemical properties of brake fluid are essential to prevent any compromise in pressure integrity. Manufacturers often employ specialized sealing compounds or gaskets to ensure a secure and leak-free connection between the fuel line and other components.
In summary, the pressure resistance of the fuel line is a critical factor in ensuring the compatibility of brake fluid and fuel systems. By utilizing materials and designs that can withstand pressure changes, engineers can create a robust and reliable fuel delivery system, contributing to the overall safety and performance of the vehicle.
Fixing a Stuck Fuel Line: A Step-by-Step Guide
You may want to see also
Temperature Tolerance: Can the fuel line handle temperatures affected by brake fluid?
The compatibility of fuel lines with brake fluid is a critical consideration in vehicle maintenance, especially when it comes to temperature tolerance. Brake fluid plays a vital role in the braking system, and its temperature can significantly impact the performance and longevity of various components, including the fuel lines. When designing or selecting fuel lines for vehicles, engineers must carefully evaluate the temperature range that these lines can withstand, particularly in the context of brake fluid.
Brake fluid, often a glycol-ether-based liquid, has a relatively low boiling point, which means it can vaporize at elevated temperatures. This vaporization can lead to the formation of air bubbles, which, when present in the brake fluid, can compromise the braking system's efficiency and safety. The fuel lines, being in close proximity to the brake fluid reservoir and often running alongside the brake lines, must be able to withstand the temperatures associated with brake fluid operation without compromising their structural integrity or allowing the ingress of air.
The temperature tolerance of fuel lines is a complex factor to consider. On one hand, fuel lines need to be robust enough to handle the high temperatures generated during intense braking, especially in racing or high-performance vehicles. These temperatures can cause the brake fluid to reach its boiling point, leading to potential issues like vapor lock, where the fuel lines become filled with air bubbles, hindering the fuel supply to the engine. On the other hand, fuel lines must also be able to resist the cold temperatures that can occur during rapid deceleration or in colder climates, preventing the brake fluid from freezing and losing its effectiveness.
To address this challenge, manufacturers often use specialized materials for fuel lines that can withstand the extreme temperature variations associated with brake fluid. These materials are carefully selected to ensure they remain flexible and resistant to degradation even when exposed to the high temperatures of brake fluid. Additionally, the design of the fuel lines may incorporate features like insulation or protective coatings to further enhance their temperature tolerance.
In summary, the temperature tolerance of fuel lines in the context of brake fluid is a critical aspect of vehicle design and maintenance. Engineers must ensure that these lines can handle the temperature extremes associated with brake fluid operation without compromising their functionality or safety. By selecting appropriate materials and designs, it is possible to create fuel lines that are resistant to the effects of brake fluid, ensuring optimal performance and longevity in various vehicle applications.
Powerful Engine Demands: Choosing the Right Fuel Line for 700 HP
You may want to see also
Longevity: Will the fuel line remain resistant to brake fluid over its lifespan?
The compatibility of fuel lines with brake fluid is a critical consideration for vehicle maintenance, especially in older or modified cars where these two systems may come into close contact. When researching the suitability of a fuel line for your vehicle, it's essential to understand its long-term resistance to brake fluid. This is because brake fluid can be highly corrosive and, over time, can degrade the materials used in fuel lines, leading to potential leaks and system failures.
The longevity of a fuel line's resistance to brake fluid depends on several factors, including the type of material used, the quality of the manufacturing process, and the specific formulation of the brake fluid. Some fuel lines are designed with materials that are inherently resistant to brake fluid, such as certain types of rubber or synthetic compounds. These materials are chosen for their ability to withstand the chemical properties of brake fluid, ensuring that the fuel line remains intact and functional over the vehicle's lifespan.
One key aspect to consider is the aging process of the fuel line. Over time, even the most resistant materials can degrade, especially if exposed to high temperatures, UV radiation, or other environmental factors. For instance, rubber fuel lines may become brittle and crack as they age, losing their ability to resist brake fluid. This is why it's crucial to regularly inspect fuel lines, especially in older vehicles, to identify any signs of wear and tear that could compromise their integrity.
To ensure the longevity of your fuel line's resistance to brake fluid, consider the following:
- Material Selection: Choose fuel lines made from materials specifically designed to resist brake fluid. These could include synthetic rubbers, such as EPDM (ethylene propylene diene monomer) rubber, or specialized compounds like nitrile rubber.
- Regular Inspections: Periodically check the fuel lines for any signs of damage, such as cracks, brittleness, or discoloration. Early detection can prevent potential issues.
- Brake Fluid Compatibility: Ensure that the brake fluid used in your vehicle is compatible with the chosen fuel line material. Some manufacturers provide specific recommendations to ensure optimal performance and longevity.
- Environmental Factors: Consider the operating conditions of your vehicle. Extreme temperatures or exposure to sunlight can accelerate the degradation of fuel lines, so take these into account when selecting materials.
In summary, the resistance of a fuel line to brake fluid is a critical aspect of vehicle maintenance, especially regarding longevity. By choosing the right materials, conducting regular inspections, and considering environmental factors, you can ensure that your fuel lines remain resistant to brake fluid over their lifespan, contributing to the overall reliability and safety of your vehicle.
Effective Methods to Remove Rust from Fuel Lines: A Comprehensive Guide
You may want to see also
Frequently asked questions
Yes, the fuel lines are typically made of materials that are resistant to brake fluid. Common materials used for fuel lines include steel, stainless steel, and various types of rubber or synthetic compounds that can withstand the corrosive effects of brake fluid.
Brake fluid can have a detrimental effect on fuel lines if the lines are not compatible with the fluid. Over time, brake fluid can cause corrosion, degradation, and even cracking of the fuel line material, leading to potential fuel leaks and system failures.
Signs of fuel line damage due to brake fluid exposure may include fuel leaks, engine misfires, reduced engine performance, or a sweet odor around the engine bay. If you notice any of these symptoms, it is essential to inspect the fuel lines for any signs of damage or deterioration.
It is not recommended to use the same fuel line for both fuel and brake systems due to the different chemical compositions and properties of these fluids. Using the correct fuel line material specific to each system is crucial to ensure safety and optimal performance.