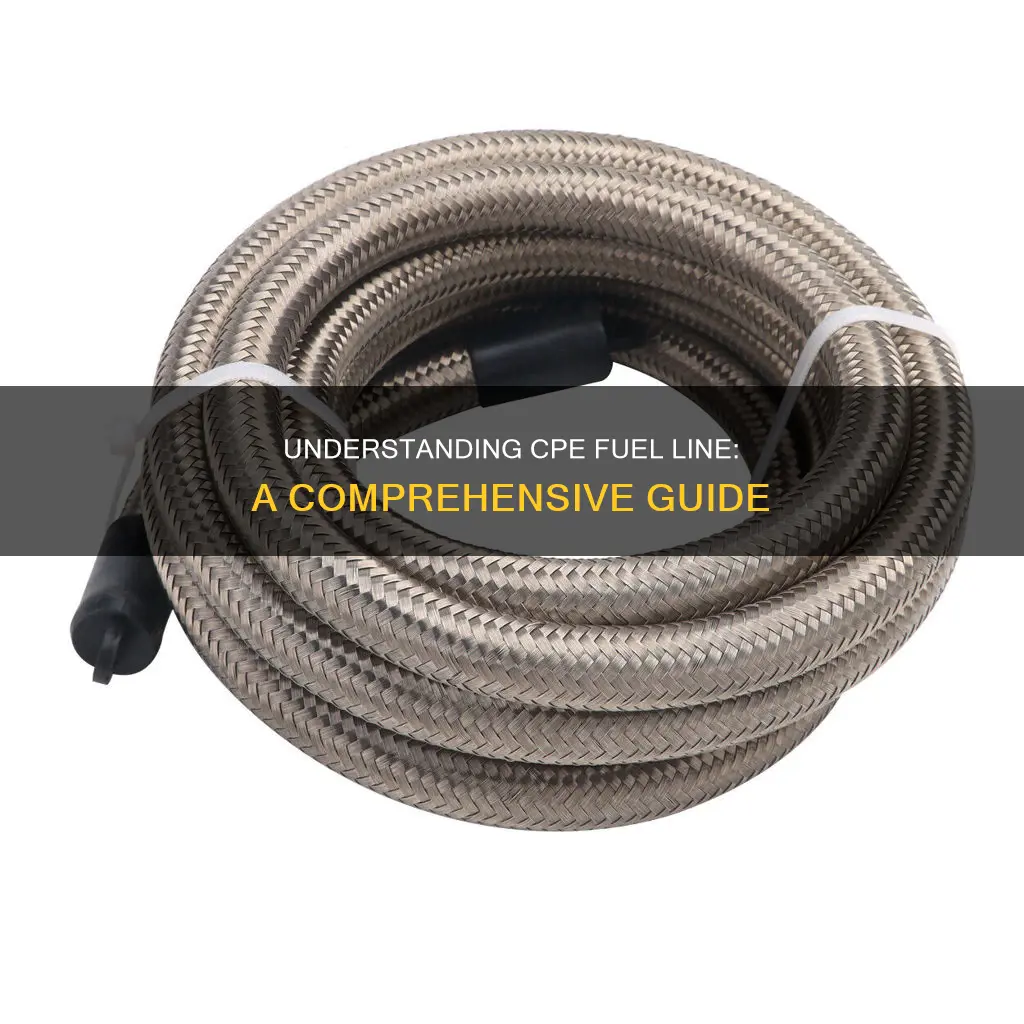
CPE fuel line, or Composite Pressure Equalizing Fuel Line, is a specialized type of fuel line used in the automotive industry. It is designed to transport fuel from the fuel tank to the engine while maintaining optimal pressure and ensuring a consistent fuel supply. CPE fuel lines are made from a composite material that combines a flexible inner layer with a sturdy outer covering, providing durability and resistance to fuel-related chemicals. This design allows for efficient fuel flow while minimizing the risk of leaks and ensuring a reliable power source for the engine. Understanding the role and benefits of CPE fuel lines is essential for vehicle maintenance and performance optimization.
What You'll Learn
- Definition: CPE fuel line is a specific type of fuel line used in aircraft, designed to withstand high-pressure fuel systems
- Materials: These lines are typically made from materials like nylon, PVC, or rubber, chosen for their durability and flexibility
- Design: The design includes features like reinforced walls and protective coatings to prevent fuel leaks and ensure safety
- Installation: Proper installation is crucial, involving precise fitting and secure attachment to the fuel system
- Maintenance: Regular inspection and maintenance are essential to ensure the line's integrity and prevent fuel system failures
Definition: CPE fuel line is a specific type of fuel line used in aircraft, designed to withstand high-pressure fuel systems
CPE fuel lines are an essential component in the intricate network of an aircraft's fuel system, playing a critical role in ensuring the safe and efficient operation of high-pressure fuel systems. These fuel lines are specifically engineered to meet the rigorous demands of aviation, where reliability and performance are paramount. The 'CPE' in this context stands for 'Cross-Linked Polyethylene,' a material known for its exceptional strength and flexibility, making it ideal for withstanding the extreme conditions found in aircraft fuel systems.
In the context of aviation, fuel lines are exposed to high-pressure environments, often operating at pressures that can exceed 3000 psi. This high pressure is necessary to ensure that fuel is delivered efficiently to the aircraft's engines, especially during takeoff and climb phases. CPE fuel lines are designed to handle these extreme conditions, providing a robust and reliable connection between the fuel tank and the engine. The material's cross-linking process enhances its structural integrity, making it resistant to cracks and leaks, which could potentially lead to dangerous situations.
The construction of CPE fuel lines involves a meticulous process. The material is carefully selected and processed to ensure it meets the required specifications. The cross-linking process, a unique feature of CPE, involves chemically bonding the polymer chains, creating a highly durable and flexible structure. This process not only enhances the material's strength but also makes it resistant to environmental factors such as temperature changes and UV radiation, which are common challenges in outdoor aviation applications.
One of the key advantages of CPE fuel lines is their ability to maintain structural integrity under high pressure. This is crucial in preventing fuel leaks, which could have severe consequences for flight safety. The material's flexibility also allows it to withstand the vibrations and movements experienced during flight, ensuring a consistent and secure connection. Furthermore, CPE fuel lines are often designed with a smooth interior surface, reducing the risk of fuel contamination and ensuring optimal fuel flow.
In summary, CPE fuel lines are a specialized type of fuel line, meticulously designed to meet the demanding requirements of aircraft fuel systems. Their construction and material properties make them an indispensable component in aviation, ensuring the safe and efficient operation of high-pressure fuel systems. By understanding the unique characteristics of CPE fuel lines, engineers and aviation professionals can appreciate the critical role they play in maintaining the integrity and safety of aircraft operations.
Fuel Line for Your 96 Civic: A Guide to Finding the Right Fit
You may want to see also
Materials: These lines are typically made from materials like nylon, PVC, or rubber, chosen for their durability and flexibility
CPE fuel lines are an essential component in the automotive industry, specifically for vehicles that require a reliable and flexible fuel delivery system. These lines are designed to transport fuel from the tank to the engine, ensuring a continuous and efficient supply of gasoline or diesel. The choice of materials for CPE fuel lines is crucial, as it directly impacts their performance, durability, and overall reliability.
The primary materials used for manufacturing CPE fuel lines are nylon, PVC (polyvinyl chloride), and rubber. Each of these materials offers unique properties that make them suitable for this application. Nylon, for instance, is known for its exceptional strength and flexibility. It can withstand high pressure and temperature variations, making it ideal for fuel lines that need to operate in demanding environments. Nylon's resistance to abrasion and chemicals further enhances its suitability for long-term use in fuel systems.
PVC, another popular choice, provides excellent chemical resistance and durability. It is lightweight and offers good flexibility, allowing for easy installation and routing within the vehicle's engine compartment. PVC fuel lines are often preferred for their cost-effectiveness and ease of maintenance.
Rubber, a traditional material for fuel lines, offers superior flexibility and resilience. It can absorb vibrations and reduce noise, ensuring a smooth and quiet fuel delivery. Rubber's natural flexibility also helps in accommodating temperature changes without compromising performance. However, rubber may not be as durable as nylon or PVC in certain harsh conditions, so it is often used in combination with other materials to create a balanced fuel line system.
The choice of these materials is driven by the need for durability, flexibility, and resistance to the corrosive effects of fuel. Nylon, PVC, and rubber each bring unique advantages to the table, ensuring that CPE fuel lines can withstand the rigors of everyday use, providing a reliable fuel supply to the engine. This careful selection of materials is a testament to the engineering precision required in the automotive industry.
Fuel Line Freeze: A Guide to Winter Car Care
You may want to see also
Design: The design includes features like reinforced walls and protective coatings to prevent fuel leaks and ensure safety
The design of a CPE (Cold Process Emulsion) fuel line is a critical aspect of its functionality and safety. This type of fuel line is specifically engineered to handle the unique challenges associated with cold process emulsion fuels, which are commonly used in certain industrial and marine applications. One of the key design features is the reinforcement of the walls. These walls are constructed using robust materials such as high-density polyethylene (HDPE) or polyvinyl chloride (PVC), which are known for their excellent impact resistance and durability. Reinforced walls help to withstand the pressure and potential vibrations that may occur during fuel transportation and usage, reducing the risk of damage or leaks.
Protective coatings are another essential element of the design. These coatings are applied to the interior and exterior surfaces of the fuel line to provide an additional layer of defense against corrosion and fuel degradation. The interior coating, often made of a specialized rubber or plastic compound, prevents the fuel from coming into direct contact with the metal, thus minimizing the risk of fuel contamination and ensuring the integrity of the fuel over time. The exterior coating, typically a durable polymer, offers protection against environmental factors such as UV radiation, chemicals, and physical impacts, further enhancing the fuel line's longevity.
In addition to these features, the design also incorporates a smooth interior surface to facilitate the flow of fuel while minimizing friction and turbulence. This design choice helps to maintain the fuel's quality and consistency, ensuring optimal performance. Furthermore, the fuel line may include specialized fittings and connectors that are designed to withstand high-pressure environments and provide secure attachments to fuel tanks and engines. These fittings are often made of brass or stainless steel to ensure compatibility with various fuel types and to prevent corrosion.
The overall design philosophy behind CPE fuel lines is to create a robust and reliable system that can handle the specific demands of cold process emulsion fuels. By incorporating reinforced walls, protective coatings, and specialized components, these fuel lines are engineered to prevent fuel leaks, maintain fuel quality, and ensure the safety of both the fuel and the surrounding environment. This level of design detail is crucial in industries where fuel handling and transportation are critical to operations.
Understanding Fuel Pickup Lines for Outboard Motors: A Comprehensive Guide
You may want to see also
Installation: Proper installation is crucial, involving precise fitting and secure attachment to the fuel system
The CPE fuel line, a critical component in the automotive industry, is designed to transport fuel from the tank to the engine, ensuring a steady and efficient supply of power. Proper installation is paramount to guarantee optimal performance and safety. When installing a CPE fuel line, the first step is to ensure you have the right tools and materials, including the appropriate size and type of fuel line, fittings, and clamps. It is essential to inspect the fuel system for any signs of damage or wear before beginning the installation process.
Precision is key during the installation process. Start by locating the fuel tank and identifying the fuel line's entry point. Carefully route the CPE fuel line, ensuring it follows the manufacturer's recommended path, which often involves running it along the frame or under the vehicle's body to minimize potential damage. The line should be securely attached to the fuel tank using the provided fittings and clamps, ensuring a tight and leak-free connection.
Secure attachment is vital to prevent fuel leaks and maintain system integrity. Tighten the fittings and clamps according to the manufacturer's specifications, being careful not to overtighten, as this can damage the fuel line. It is recommended to use a torque wrench for this step to ensure the correct amount of force is applied. Once the fuel line is attached to the tank, it should be checked for any signs of movement or looseness, and adjustments should be made to ensure a stable and secure fit.
Moving on to the engine, the fuel line must be connected to the fuel pump and the engine's fuel rail or injectors. This requires precise alignment of the fuel line with the engine's fuel system, ensuring that the line's diameter and length are compatible with the engine's requirements. The connection should be made using the appropriate fittings, and the line should be clamped securely to the engine block or frame to prevent movement during operation.
In summary, the installation of a CPE fuel line demands attention to detail and a systematic approach. Proper routing, secure attachment to both the fuel tank and the engine, and precise fitting connections are essential to ensure the fuel system's reliability and performance. Regular maintenance and inspections should also be conducted to identify and address any potential issues, ensuring the longevity and safety of the vehicle's fuel system.
Grease's Fuel Line Fitting: A Comprehensive Guide
You may want to see also
Maintenance: Regular inspection and maintenance are essential to ensure the line's integrity and prevent fuel system failures
The CPE fuel line, a critical component in the fuel system of many vehicles, requires regular maintenance and inspections to ensure its longevity and prevent potential fuel system failures. This component is responsible for delivering fuel from the fuel tank to the engine, and any issues with it can lead to poor engine performance, reduced fuel efficiency, and even engine stalls. Therefore, it is crucial to establish a maintenance routine to keep this system in optimal condition.
One of the primary maintenance tasks for the CPE fuel line is regular visual inspections. Over time, fuel lines can develop cracks, leaks, or damage due to various factors such as age, temperature fluctuations, and chemical degradation. Inspecting the fuel line for any visible signs of wear and tear is essential. Look for cracks, kinks, brittleness, or any signs of corrosion along the line's path. Additionally, check for any signs of fuel leakage around the connections and fittings. Even a small leak can lead to significant issues over time, so any detected leaks should be addressed immediately.
Another critical aspect of maintenance is ensuring that the fuel line is properly secured and free from any obstructions. The fuel line should be securely fastened to the fuel tank and engine using appropriate clamps and brackets. Regularly check these fasteners to ensure they are tight and secure. Also, inspect the area around the fuel line for any debris or obstructions that might cause the line to rub or become damaged. Keeping the fuel line clear of any potential hazards is vital to prevent damage and ensure the system's reliability.
In addition to visual inspections, it is recommended to use a fuel line inspection tool, such as a fuel line brush, to clean and inspect the interior of the fuel line. This tool can help remove any built-up fuel residue, debris, or contaminants that may have accumulated over time. Cleaning the fuel line ensures that the fuel is of high quality and that the engine receives the best possible fuel supply. It also helps to prevent the formation of deposits that could restrict fuel flow and cause performance issues.
Furthermore, regular maintenance should include checking the fuel filter, as it plays a vital role in maintaining the health of the fuel line and the entire fuel system. A clogged or dirty fuel filter can restrict fuel flow, leading to engine problems. It is advisable to replace the fuel filter at regular intervals or when it shows signs of wear. This simple maintenance task can significantly contribute to the overall performance and longevity of the CPE fuel line.
In summary, regular inspection and maintenance of the CPE fuel line are crucial for vehicle owners to ensure the integrity of the fuel system and prevent unexpected failures. By performing visual inspections, securing the fuel line properly, using inspection tools, and maintaining a clean fuel filter, vehicle owners can keep their fuel lines in excellent condition. This proactive approach to maintenance will help ensure reliable engine performance and peace of mind for drivers.
Backwards Fuel Lines: A Recipe for Disaster
You may want to see also
Frequently asked questions
CPE stands for Carbon-Packed Ethanol, which is a type of fuel additive designed to improve engine performance and fuel efficiency. The CPE fuel line refers to the fuel delivery system that incorporates this additive. It is a specialized fuel line that is engineered to handle the unique properties of CPE, ensuring optimal fuel flow and combustion in engines.
CPE fuel lines are specifically formulated to accommodate the higher ethanol content in CPE fuel. Regular fuel lines may not be compatible with CPE due to the potential for ethanol to cause corrosion or degradation over time. CPE fuel lines are made from materials that can withstand the corrosive effects of ethanol, ensuring the longevity and reliability of the fuel delivery system.
Using CPE fuel line offers several advantages. Firstly, it can enhance engine performance by promoting better fuel atomization and combustion, resulting in increased power and efficiency. Secondly, CPE fuel lines are designed to reduce fuel system deposits, ensuring cleaner and smoother operation. Additionally, the ethanol-resistant properties of CPE fuel lines help prevent fuel-related issues associated with ethanol blends.
CPE fuel line is typically recommended for use with engines designed to run on ethanol-blended fuels. It is important to consult the engine manufacturer's guidelines or specifications to ensure compatibility. Some engines may require specific adaptations or modifications to accommodate CPE fuel lines effectively. Always refer to the manufacturer's recommendations for the best results.