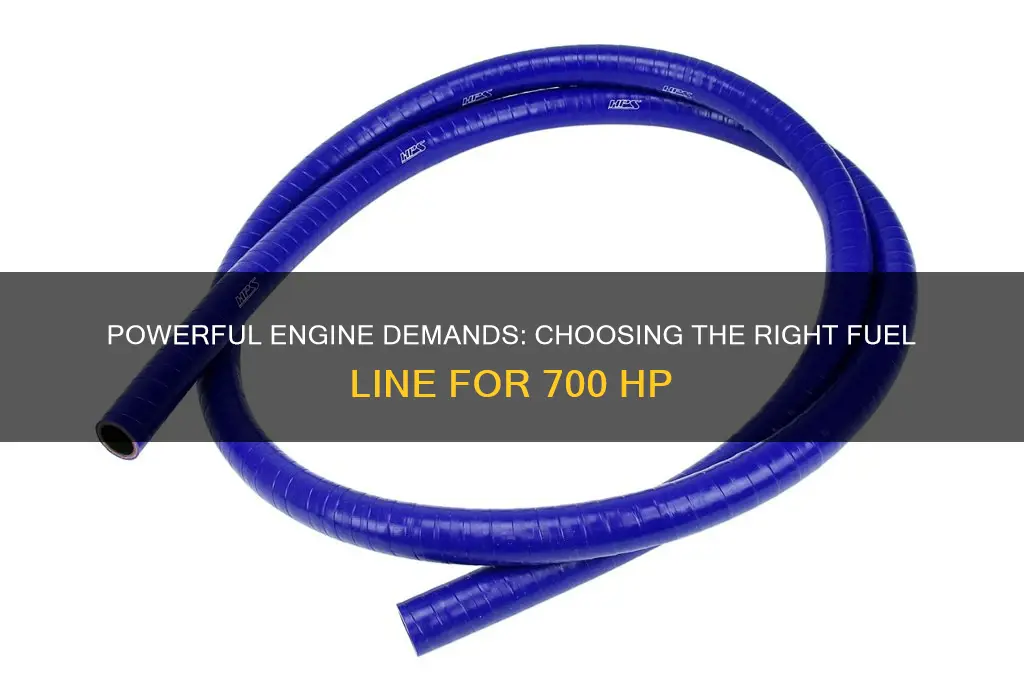
When building a high-performance engine capable of producing 700 horsepower, one of the critical components to consider is the fuel line. The size of the fuel line is crucial to ensure that the engine receives the necessary fuel flow to meet its power demands. Choosing the right size fuel line involves balancing performance, reliability, and cost. This article will explore the factors to consider when selecting the appropriate fuel line size for a 700-hp engine, including flow rate requirements, pressure considerations, and the impact of fuel type and engine configuration.
Characteristics | Values |
---|---|
Fuel Line Diameter | Typically 3/8" to 1/2" for 700 HP engines. |
Length | Varies based on engine placement and configuration. A rule of thumb is 1-2 feet per foot of engine displacement. |
Material | High-quality steel or stainless steel for durability and corrosion resistance. |
Pressure Rating | At least 150-200 psi to handle high-performance fuel injection. |
Flexibility | Adequate flexibility to accommodate engine movement during operation. |
Compatibility | Ensure compatibility with the fuel pump and injectors. |
Clamping | Securely clamp the fuel line to prevent leaks and ensure a tight fit. |
Color | Often red or blue for easy identification. |
Brand | Reputable brands like Holley, Edelbrock, or FuelTech offer specific fuel line kits for high-HP applications. |
What You'll Learn
- Engine Power: Choose fuel line size based on engine power output
- Flow Rate: Ensure the line can handle the required fuel flow rate
- Pressure: Consider pressure requirements for optimal performance
- Material: Select appropriate material for durability and flexibility
- Length: Measure and select the correct length for the fuel line
Engine Power: Choose fuel line size based on engine power output
When it comes to fueling high-performance engines, such as those producing 700 horsepower, the choice of fuel line size is critical to ensure optimal performance and safety. Engine power output is a key factor in determining the appropriate fuel line diameter. Higher horsepower engines require more fuel, and the fuel line must be able to handle the increased flow rate without compromising efficiency or safety.
The general rule of thumb is that the fuel line size should be proportional to the engine's power output. For a 700 hp engine, a larger fuel line diameter is necessary to accommodate the higher fuel demand. A common recommendation is to use a fuel line with a diameter of at least 3/8 inches for engines in this power range. This size ensures that the fuel can flow efficiently, providing the engine with the necessary fuel supply to meet its power requirements.
To understand why this is important, consider the relationship between engine power and fuel flow. Higher horsepower engines often have increased compression ratios and faster combustion rates, which require a more robust fuel delivery system. A smaller fuel line may restrict fuel flow, leading to reduced performance, engine misfires, or even damage due to inadequate fuel supply. Therefore, choosing the right fuel line size is essential to maintain the engine's performance and longevity.
It's worth noting that other factors, such as fuel pressure, pump capacity, and the overall fuel system design, also play a role in determining the optimal fuel line size. However, starting with the engine's power output as a baseline is a good starting point for selecting the appropriate fuel line diameter. Consulting with engine manufacturers or fuel system experts can provide further guidance tailored to specific engine requirements.
In summary, when dealing with a 700 hp engine, selecting a fuel line with an appropriate diameter is crucial. A larger fuel line size ensures efficient fuel delivery, supporting the engine's high power output. By considering the engine's power characteristics, you can make an informed decision to optimize performance and ensure the fuel system's reliability.
Mastering Fuel Line Sizing: The Ultimate Guide to 3/8" Fuel Line Fitting
You may want to see also
Flow Rate: Ensure the line can handle the required fuel flow rate
When dealing with high-performance engines, such as those producing 700 horsepower, the choice of fuel line size is critical to ensure optimal performance and reliability. The flow rate, which refers to the volume of fuel delivered per unit of time, plays a pivotal role in determining the appropriate fuel line diameter.
To calculate the required flow rate, consider the engine's fuel requirements. A 700 hp engine typically demands a substantial amount of fuel, often in the range of 50-100 gallons per minute (gpm) or more, depending on various factors like engine load, speed, and efficiency. For instance, a high-performance racing engine might require 80-100 gpm during peak power delivery.
The flow rate is directly influenced by the engine's fuel injection system and the desired fuel pressure. Higher fuel pressure can increase the flow rate, but it must be balanced with the fuel line's capacity to handle the pressure without excessive wear or fuel leakage. As a rule of thumb, the fuel line should be able to accommodate at least 1.5 to 2 times the required flow rate to account for transient conditions and ensure a steady supply of fuel.
To determine the appropriate fuel line size, refer to the manufacturer's specifications and guidelines. Fuel lines are typically rated in inches per second (IPS) or gallons per minute (gpm) per pound per square inch (psi). For a 700 hp engine, you might consider a fuel line with a flow rate capacity of 100-150 gpm at a pressure of 60-80 psi. This ensures that the fuel line can handle the engine's demands without compromising performance or safety.
In summary, when selecting a fuel line for a 700 hp engine, focus on the flow rate to guarantee efficient fuel delivery. The line should be capable of handling the engine's peak flow rate requirements, considering factors like fuel pressure and transient conditions. Consulting manufacturer guidelines and industry standards will help you make an informed decision to optimize your high-performance engine's performance.
Unraveling the Mystery: Understanding Fuel Line Retaining Clips
You may want to see also
Pressure: Consider pressure requirements for optimal performance
When dealing with high-performance engines, such as those producing 700 horsepower, the fuel system plays a critical role in ensuring optimal performance and reliability. One crucial aspect to consider is the pressure requirements within the fuel lines. Pressure is a key factor that can significantly impact the efficiency and power output of your engine.
The pressure in the fuel lines is essential for delivering fuel to the engine at the right rate and ensuring a consistent flow. In high-performance applications, where fuel demands are higher, the pressure must be carefully managed. Insufficient pressure can lead to poor atomization of the fuel, resulting in inefficient combustion and reduced power. On the other hand, excessive pressure can cause fuel to spray too finely, leading to potential issues like fuel accumulation in the intake manifold, which can cause engine misfires or even damage.
To determine the appropriate pressure, it is crucial to consider the engine's specific requirements and operating conditions. Engine manufacturers often provide guidelines or specifications for the recommended fuel pressure range. These specifications are typically based on extensive testing and are designed to optimize performance while ensuring the engine operates safely. For a 700 hp engine, the pressure requirements might vary depending on the engine type, displacement, and other factors.
Measuring and monitoring fuel pressure is essential to ensure it meets the engine's needs. This can be done using a fuel pressure gauge, which provides real-time feedback on the pressure within the fuel lines. By regularly checking the pressure, you can identify any deviations from the optimal range and make adjustments accordingly. Proper calibration of the fuel pressure can be achieved through adjustments to the fuel pump, pressure regulator, or fuel injectors.
In summary, when designing or modifying a fuel system for a 700 hp engine, pressure considerations are vital. Achieving the correct pressure ensures efficient fuel delivery, optimal combustion, and maximum power output. It requires careful measurement, calibration, and adherence to the engine manufacturer's recommendations to fine-tune the fuel pressure for the specific application. Regular maintenance and monitoring of fuel pressure will contribute to the overall performance and longevity of the high-performance engine.
Unveiling the Mystery: What Are Fuel Line Connectors Called?
You may want to see also
Material: Select appropriate material for durability and flexibility
When it comes to fuel lines for high-performance engines, such as those producing 700 horsepower, the choice of material is critical to ensure optimal performance and longevity. The material selection should prioritize durability and flexibility to withstand the demanding conditions of such powerful engines.
One of the most commonly used materials for fuel lines in high-performance applications is stainless steel. This material offers excellent resistance to corrosion, which is crucial when dealing with fuel, especially in high-temperature environments. Stainless steel's durability ensures that the fuel line can handle the pressure and heat generated by the engine, making it a reliable choice. Additionally, its flexibility allows for easy installation and routing, accommodating the engine's various movements during operation.
Another option is braided stainless steel, which provides an even higher level of flexibility while maintaining the necessary strength. This material is often used in high-performance racing applications due to its ability to withstand extreme conditions. The braiding technique used in its construction allows for a more flexible and durable fuel line, reducing the risk of damage from engine vibrations and movement.
For those seeking a more cost-effective solution, high-density polyethylene (HDPE) can be a suitable alternative. HDPE is known for its flexibility and resistance to fuel degradation. It is a lightweight material, making it easier to install and route, and its durability ensures it can handle the rigors of high-performance engines. However, it's important to note that HDPE may not be as resistant to extreme temperatures as stainless steel, so careful consideration of the operating environment is essential.
In summary, when selecting the material for fuel lines in a 700 hp engine, prioritize durability and flexibility. Stainless steel and its braided variants offer excellent corrosion resistance and strength, making them ideal for high-performance applications. Alternatively, HDPE provides flexibility and cost-effectiveness, but may require additional considerations for temperature-sensitive environments. The choice should be based on the specific requirements of the engine and the operating conditions to ensure optimal performance and longevity.
Choosing the Right Rubber for Your Fuel Line: A Guide
You may want to see also
Length: Measure and select the correct length for the fuel line
When it comes to fuel lines for high-performance engines, such as those producing 700 horsepower, the length of the fuel line is a critical factor to consider. The goal is to ensure efficient and reliable fuel delivery while minimizing pressure drop and potential issues. Here's a detailed guide on how to measure and select the correct length for your fuel line:
Measuring the Required Length: Start by identifying the source of the fuel and its location. Typically, the fuel pump is positioned near the engine, and the fuel tank is usually located further away. Measure the distance between these two points. Consider the path the fuel line will take, including any bends, turns, or obstacles it might encounter. It's essential to allow for a slight margin of error, as you want to ensure the line is long enough to accommodate any potential movement or expansion during engine operation.
Calculating the Length: Once you have the initial measurement, calculate the length required. A good rule of thumb is to add a 10-15% buffer to your measured distance. This extra length accounts for any unforeseen challenges and ensures a secure installation. For example, if your measured distance is 10 feet, you might consider a fuel line length of 11-12 feet. This additional length will provide a more flexible and reliable setup.
Considering Fuel Flow and Pressure: The length of the fuel line also impacts the flow rate and pressure. Longer lines can lead to a decrease in pressure, which might affect the engine's performance. For high-hp applications, it's crucial to maintain optimal pressure to ensure efficient fuel delivery. If the line is too long, you may need to consider using a fuel pressure regulator to maintain the required pressure levels.
Selecting the Right Fuel Line: After determining the required length, you can choose the appropriate fuel line. Fuel lines are typically made of materials like steel, aluminum, or specialized rubber compounds. The choice depends on factors such as temperature resistance, flexibility, and durability. For high-hp engines, a sturdy and flexible material is ideal to withstand the demands of powerful performance. Ensure the fuel line has the necessary fittings and connectors to securely attach it to the fuel pump, tank, and other components.
Remember, proper fuel line installation is vital for the overall performance and longevity of your high-powered engine. Taking the time to measure and select the correct length will contribute to a reliable fuel delivery system, ensuring your 700-hp machine runs smoothly and efficiently.
Unveiling the Material Secrets of Plastic Fuel Lines
You may want to see also
Frequently asked questions
For a 700 HP engine, a fuel line diameter of 1/2 inch to 3/4 inch is generally recommended. This size ensures efficient fuel delivery to meet the high power output, minimizing pressure drop and maintaining optimal performance.
Using a smaller fuel line (e.g., 1/4 inch) is not advisable for a 700 HP engine. The increased fuel flow and pressure demands of a high-performance engine require a larger diameter line to handle the volume and pressure effectively.
The length of the fuel line is crucial for performance. Longer lines may introduce unnecessary restrictions and pressure losses, impacting fuel delivery. It's recommended to keep the fuel line as short as possible, ideally less than 10 feet, to ensure optimal performance.
Yes, for high-hp engines, fuel lines made from high-pressure-rated materials like stainless steel or braided steel are preferred. These materials offer better flexibility, durability, and resistance to fuel degradation, ensuring reliable performance under demanding conditions.