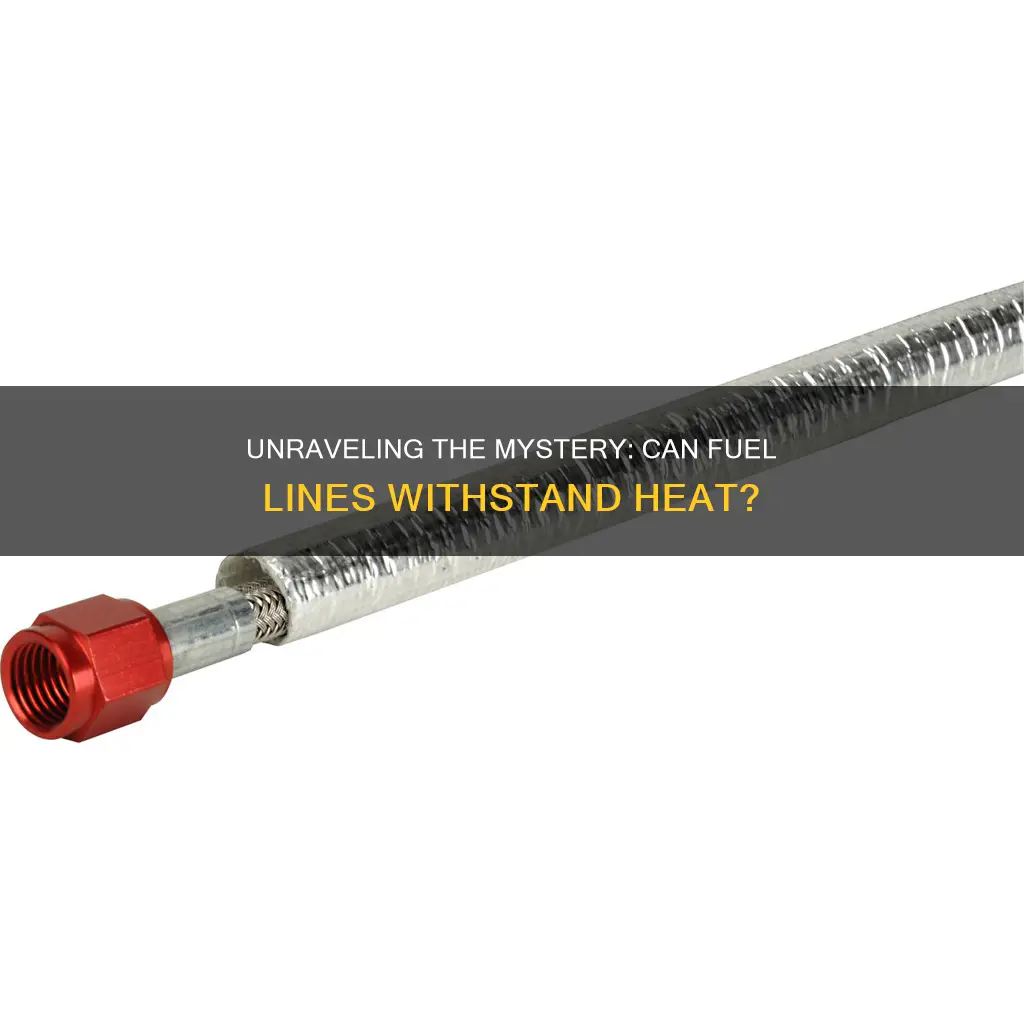
The fuel line is a critical component in any vehicle's engine, responsible for transporting fuel from the tank to the engine. However, the fuel line is often exposed to high temperatures, which can cause it to degrade over time. This degradation can lead to fuel leaks, engine misfires, and other performance issues. Therefore, it is essential to understand whether the fuel line is heat resistant and how it can withstand the extreme temperatures encountered during vehicle operation. This knowledge is crucial for ensuring the longevity and reliability of the vehicle's fuel system.
Characteristics | Values |
---|---|
Material | Stainless steel, aluminum, or high-temperature plastics |
Temperature Range | Typically up to 250°F (121°C) for standard fuel lines, but can vary |
Flexibility | Able to withstand vibrations and movement without cracking |
Corrosion Resistance | Resistant to fuel-related chemicals and oils |
Durability | Long-lasting and can handle high-pressure environments |
Compatibility | Designed to work with specific fuel types (gasoline, diesel, etc.) |
Installation | Easy to install and replace |
Color | Often black or blue to indicate high-temperature applications |
Standards | Meets industry standards for fuel system components |
What You'll Learn
- Fuel Line Material: Choose heat-resistant materials like stainless steel or high-temperature plastics
- Temperature Limits: Ensure fuel lines can withstand operating temperatures, including extreme heat and cold
- Flexibility: Heat-resistant fuel lines should maintain flexibility even under high temperatures
- Vibration Resistance: Heat-resistant fuel lines should withstand engine vibrations without cracking or leaking
- Compliance: Adhere to industry standards and regulations for heat resistance in fuel lines
Fuel Line Material: Choose heat-resistant materials like stainless steel or high-temperature plastics
When it comes to fuel lines in vehicles, especially those used in high-performance engines or racing applications, the choice of material is critical. The primary concern is ensuring that the fuel lines can withstand the extreme temperatures and conditions encountered during operation. This is where the concept of heat resistance comes into play, and it's a crucial factor to consider when selecting the right material for fuel lines.
Heat-resistant materials are essential to ensure the longevity and reliability of fuel lines. These materials can endure the intense heat generated by engines, especially during prolonged high-performance driving or racing. The goal is to prevent fuel line degradation, which could lead to fuel leaks, reduced engine performance, and potential safety hazards.
One of the most commonly used heat-resistant materials for fuel lines is stainless steel. This metal alloy is renowned for its exceptional durability and resistance to corrosion and heat. Stainless steel fuel lines can handle high temperatures without compromising their structural integrity. They are often preferred in racing applications and high-performance vehicles due to their ability to withstand the rigors of extreme driving conditions. The use of stainless steel ensures that the fuel lines remain flexible yet robust, allowing for smooth operation even under intense heat.
Another option for heat-resistant fuel lines is high-temperature plastics. These specialized polymers are engineered to maintain their shape and flexibility even at elevated temperatures. High-temperature plastics offer a lightweight and cost-effective alternative to metal fuel lines. They are often used in applications where weight reduction is crucial, such as in racing or aircraft fuel systems. These plastics are designed to resist fuel degradation and provide long-term reliability, making them a popular choice for modern vehicles.
In summary, when dealing with fuel lines, it is imperative to choose materials that can withstand heat. Stainless steel and high-temperature plastics are excellent options, each offering unique advantages. Stainless steel provides superior heat resistance and durability, making it ideal for demanding applications. On the other hand, high-temperature plastics offer lightweight and cost-effective solutions without compromising heat resistance. Selecting the right material ensures the fuel lines remain functional and safe, contributing to the overall performance and reliability of the vehicle.
Nylon Fuel Line Repair: Quick Tips for a Successful Fix
You may want to see also
Temperature Limits: Ensure fuel lines can withstand operating temperatures, including extreme heat and cold
When it comes to fuel lines, ensuring they can withstand varying temperatures is crucial for the safe and efficient operation of any vehicle or machinery. Extreme heat and cold can put significant stress on these components, and failure to meet temperature limits can lead to costly repairs and potential safety hazards.
In high-temperature environments, fuel lines must be designed to resist heat degradation. This includes using materials that can withstand the intense heat without becoming brittle or losing their structural integrity. For instance, some fuel lines are made from high-temperature-resistant materials like stainless steel or specialized polymers that maintain their flexibility and strength even when exposed to extreme heat. These materials are carefully selected to ensure they can handle the operating temperatures of the engine or machinery they are designed for.
On the other hand, cold temperatures also present unique challenges. During winter, fuel lines can become brittle and more susceptible to damage due to the extreme cold. This is especially critical in regions with harsh winters. To combat this, manufacturers often use flexible materials that retain their pliability in cold conditions. These materials can bend and move with the vehicle's components without cracking or breaking, ensuring a continuous and reliable fuel supply.
The temperature limits for fuel lines are typically specified by the manufacturer and are essential to follow. Operating outside these limits can result in fuel line damage, reduced performance, and even fuel leaks. For example, if a fuel line is subjected to temperatures below its recommended minimum, it may become brittle and crack, leading to fuel leaks and potential fire hazards. Conversely, if the temperature exceeds the maximum limit, the fuel line could melt or deform, causing fuel system failure.
To ensure optimal performance and longevity, it is imperative to choose fuel lines that are specifically designed to meet the temperature requirements of the application. Regular inspections and maintenance can also help identify any potential issues, allowing for timely replacements before temperature-related damage occurs. By understanding and addressing temperature limits, you can ensure the reliability and safety of your fuel system.
Unveiling the Mystery: Why Air Intrudes in Fuel Lines
You may want to see also
Flexibility: Heat-resistant fuel lines should maintain flexibility even under high temperatures
When it comes to automotive performance and safety, the role of fuel lines is often overlooked, but their importance cannot be overstated. One critical aspect of these fuel lines is their heat resistance, a feature that ensures the system's longevity and reliability, especially in high-performance vehicles. The primary concern with fuel lines is their ability to withstand elevated temperatures without compromising their structural integrity. This is particularly crucial in engines where the fuel lines are exposed to intense heat from the engine block, exhaust systems, and even nearby components like the catalytic converter.
Heat-resistant fuel lines are designed to maintain their flexibility and structural integrity under extreme conditions. This flexibility is essential because it allows the fuel lines to move and bend without breaking or becoming brittle. In high-performance vehicles, where acceleration and deceleration are rapid and frequent, the fuel lines must be able to adapt to these changes without failing. For instance, during high-speed driving, the fuel lines need to withstand the stress of rapid changes in engine load, which can generate significant heat.
The construction of heat-resistant fuel lines involves the use of specialized materials that can endure high temperatures without losing their flexibility. These materials are often a blend of synthetic rubbers and plastics, carefully selected for their thermal stability and resistance to fuel degradation. The inner lining of these fuel lines might be made from materials like fluoropolymers or PTFE (polytetrafluoroethylene), which provide excellent heat resistance and prevent fuel leakage. The outer layer could be a durable, flexible material like silicone or a specialized rubber compound, ensuring the line can withstand mechanical stress and environmental factors.
In addition to the choice of materials, the design of the fuel lines also plays a significant role in their heat resistance. Engineers often incorporate features like braided reinforcement, which adds strength and flexibility, especially in high-stress areas. The braids can be made from stainless steel or other heat-resistant metals, ensuring the line remains intact even when exposed to extreme temperatures. Furthermore, the routing of the fuel lines is crucial; they should be positioned away from hot surfaces and protected by insulation or heat shields to minimize direct exposure to high temperatures.
Maintaining flexibility under high temperatures is a critical aspect of fuel line design, as it ensures the system's reliability and longevity. Heat-resistant fuel lines are a vital component in any vehicle, especially those with high-performance engines, where they must endure rapid temperature fluctuations and mechanical stress. By using the right materials and design techniques, manufacturers can ensure that fuel lines remain flexible, preventing potential issues like fuel leaks, engine misfires, and even fire hazards. This attention to detail in fuel line construction is a testament to the engineering prowess required to build high-performance vehicles.
Strikemaster Lazer Mag Express: Optimizing Fuel Line Dimensions
You may want to see also
Vibration Resistance: Heat-resistant fuel lines should withstand engine vibrations without cracking or leaking
When it comes to vehicle performance and longevity, the fuel system plays a critical role, and one of the key components is the fuel line. These lines are responsible for transporting fuel from the tank to the engine, and their integrity is vital to ensure optimal power delivery and prevent engine issues. One of the most challenging aspects of fuel lines is their exposure to extreme conditions, including heat and vibrations.
Vibration resistance is a crucial factor in the design and selection of heat-resistant fuel lines. Engine vibrations can be intense and constant, especially during high-performance driving or when operating in rough terrain. Over time, these vibrations can cause the fuel lines to crack or develop leaks, leading to potential engine misfires, reduced performance, and even costly repairs. To combat this, manufacturers and engineers focus on creating fuel lines that can withstand the rigors of the engine's environment.
Heat-resistant fuel lines are designed with materials that offer exceptional durability. These materials are carefully chosen to maintain their structural integrity under high temperatures and mechanical stress. Common materials used include high-temperature plastics, such as polyetheretherketone (PEEK) and polyimide, which provide excellent heat resistance and flexibility. Additionally, some fuel lines incorporate metal braids or reinforcements to enhance their strength and ability to resist vibrations.
The manufacturing process also plays a significant role in ensuring vibration resistance. Advanced techniques, such as braiding or spiraling the heat-resistant material, create a flexible yet robust structure. This design allows the fuel line to absorb and distribute vibrations evenly, preventing localized stress points that could lead to cracks or leaks. By withstanding the engine's vibrations, these fuel lines ensure a consistent and reliable fuel supply, contributing to improved engine performance and longevity.
In summary, vibration resistance is a critical aspect of heat-resistant fuel lines, ensuring they can endure the harsh conditions within an engine bay. By utilizing advanced materials and manufacturing techniques, these fuel lines provide the necessary durability to withstand vibrations without compromising their heat resistance. This attention to detail in fuel line design is essential for maintaining optimal engine performance and reliability, especially in demanding driving conditions.
Turbo LS Fuel Line Sizing: Expert Guide for Optimal Performance
You may want to see also
Compliance: Adhere to industry standards and regulations for heat resistance in fuel lines
Compliance with industry standards and regulations is crucial when it comes to ensuring the heat resistance of fuel lines. These standards are in place to guarantee the safety and reliability of fuel systems in various applications, from automotive to aviation. Adhering to these guidelines is essential to prevent potential hazards associated with fuel line failures, such as fuel leaks, fires, or engine malfunctions.
One of the primary industry standards for heat resistance in fuel lines is set by the Society of Automotive Engineers (SAE). The SAE J2041 standard provides guidelines for the design, material selection, and performance requirements of fuel lines. This standard ensures that fuel lines can withstand the expected temperature ranges and operating conditions in different vehicles. Manufacturers and engineers must refer to this standard to select appropriate materials and design fuel lines that meet the required heat resistance.
In addition to the SAE standard, other industry regulations and guidelines should be considered. For example, the American Society for Testing and Materials (ASTM) offers various standards related to fuel system components, including fuel lines. ASTM D4970 is a relevant standard that specifies the requirements for the design, manufacture, and testing of fuel lines for automotive applications. Compliance with ASTM standards ensures that fuel lines are constructed using high-quality materials and processes, providing excellent heat resistance.
When designing or selecting fuel lines, it is essential to consider the specific operating conditions and temperature ranges. Different applications, such as racing cars or aircraft, may have unique requirements. For instance, high-performance engines or aircraft operating at extreme altitudes might demand fuel lines with superior heat resistance to handle the intense heat and pressure. Engineers should consult the relevant industry standards and regulations to ensure compliance and select the appropriate materials and design specifications.
Furthermore, regular inspections and maintenance are vital to maintaining compliance with heat resistance standards. Over time, fuel lines can degrade due to heat, fuel contamination, or other factors. Inspecting fuel lines for signs of wear, cracks, or damage is essential, especially in high-temperature environments. Regular maintenance and replacement of fuel lines according to manufacturer recommendations help ensure continued compliance with heat resistance standards and prevent potential failures.
Optimizing Fuel Delivery: Choosing the Right Size for Your Viva HC
You may want to see also
Frequently asked questions
A fuel line heat shield is a protective covering designed to safeguard the fuel lines from excessive heat, which can cause damage and potential fuel leaks. It is commonly used in high-performance vehicles or those operating in environments with extreme temperatures.
Heat resistance in fuel lines is crucial as it prevents the material from degrading or becoming brittle when exposed to high temperatures. This ensures that the fuel lines remain flexible, maintain their structural integrity, and continue to function optimally over an extended period.
While some fuel lines may use standard materials that can withstand moderate heat, specialized heat-resistant materials like stainless steel, high-temperature plastics, or braided silicone are often employed to ensure optimal performance and durability in demanding conditions.
Yes, signs of inadequate heat resistance include fuel leaks, reduced fuel pressure, engine misfires, or visible damage to the fuel line. These issues may arise when the fuel line material cannot withstand the heat, leading to potential safety hazards and performance problems.
Regular inspections are recommended, especially for vehicles operating in harsh conditions or those with high-performance engines. It is advised to check the fuel lines for any signs of damage or wear and ensure they meet the required heat resistance standards to prevent unexpected failures.