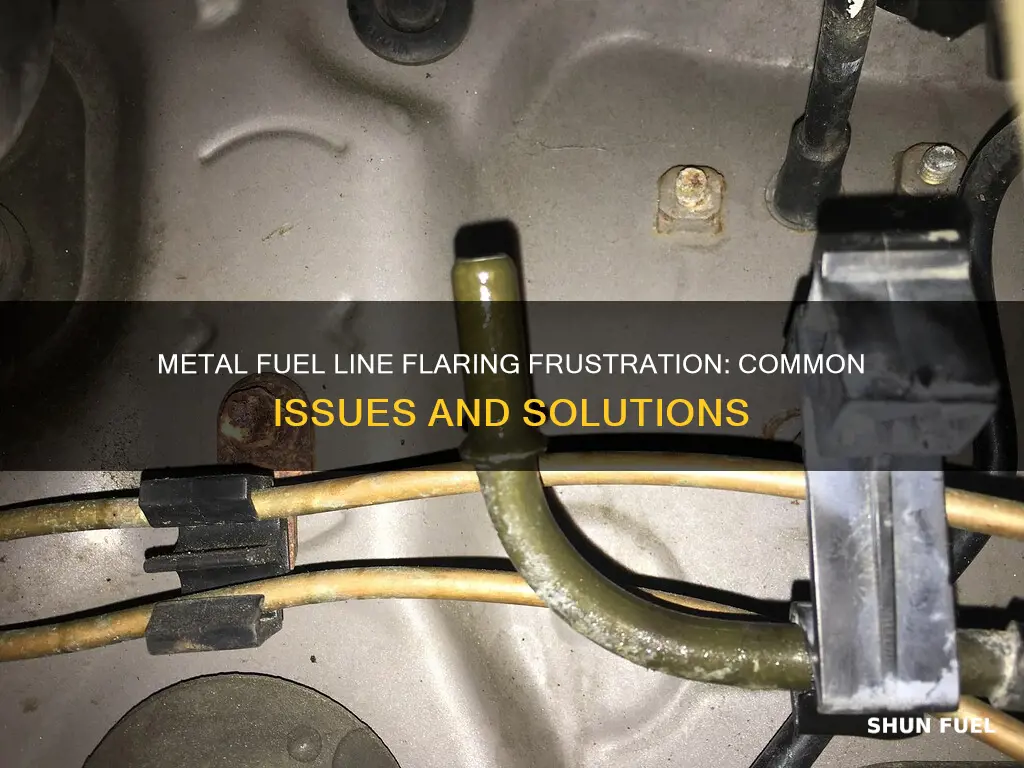
Metal fuel lines are an essential component of any vehicle's fuel system, and ensuring they are properly connected and sealed is crucial for optimal performance and safety. However, many car owners and mechanics have encountered a common issue: fuel lines that won't flare, despite repeated attempts. This problem can be frustrating and often leaves people wondering what went wrong. The process of flaring metal fuel lines involves bending and shaping the metal to create a tight, sealed connection. This is typically done using specialized tools and techniques to ensure a secure and leak-free connection. Understanding the reasons why flaring might fail can help in troubleshooting and finding effective solutions to this common automotive challenge.
What You'll Learn
- Material Compatibility: Ensure fuel line material is compatible with fuel type
- Temperature Sensitivity: Fuel lines may expand or contract with temperature changes
- Pressure Considerations: Excessive pressure can damage fuel lines
- Installation Technique: Flare fitting installation requires skill and precision
- Fuel Line Diameter: Choose the correct diameter for optimal flow and fit
Material Compatibility: Ensure fuel line material is compatible with fuel type
When it comes to fuel lines, material compatibility is a critical factor that can significantly impact the performance and longevity of your fuel system. The primary concern here is ensuring that the material of the fuel line is compatible with the type of fuel it will carry. Different fuels have unique chemical properties, and using the wrong material can lead to various issues, including corrosion, fuel degradation, and even system failure.
For instance, metal fuel lines, while strong and durable, may not be the best choice for all fuel types. Metal lines can be susceptible to corrosion when exposed to certain fuels, especially those containing ethanol or methanol. These fuels can accelerate the breakdown of metal, leading to leaks and potential engine damage. On the other hand, some fuels, like aviation gasoline, may not cause immediate corrosion but can still affect the fuel line's performance over time.
To address this, it's essential to choose the right material for your fuel line based on the fuel type. For example, rubber or synthetic materials are often preferred for their compatibility with a wide range of fuels. These materials are resistant to corrosion and can withstand the chemical properties of various fuels without breaking down. Additionally, the inner lining of the fuel line should also be considered, as it can be made of different materials that interact with the fuel, ensuring optimal performance.
When selecting fuel lines, it's crucial to consult the manufacturer's guidelines or seek expert advice to determine the most suitable material for your specific fuel type. This ensures that your fuel system operates efficiently and safely, minimizing the risk of fuel-related issues. Understanding the compatibility of materials with different fuels is a vital step in preventing problems like fuel line failure, which can be costly and dangerous.
In summary, material compatibility is a key consideration when dealing with fuel lines. By choosing the right material that is compatible with the fuel type, you can ensure the longevity and reliability of your fuel system, reducing the chances of encountering issues related to fuel line flare or performance.
WRX Fuel Line: Discover the Perfect OEM Size
You may want to see also
Temperature Sensitivity: Fuel lines may expand or contract with temperature changes
The performance and longevity of your fuel system can be significantly impacted by the temperature sensitivity of metal fuel lines. These lines are crucial for delivering fuel from the tank to the engine, and their flexibility is essential to accommodate the natural expansion and contraction that occurs with temperature fluctuations. When temperatures drop, metal fuel lines can become stiff and rigid, making it difficult for them to flare or connect properly. This issue is particularly common in colder climates or during seasonal changes. The solution lies in understanding the material properties of the fuel lines and implementing appropriate measures to mitigate temperature-related problems.
One effective approach is to use fuel lines made from materials that offer better flexibility and resistance to temperature changes. For instance, rubber or synthetic rubber compounds can provide the necessary flexibility without compromising strength. These materials can absorb temperature variations more effectively, ensuring that the fuel lines remain pliable and capable of flaring successfully. Additionally, consider the installation process; proper crimping or flaring techniques should be employed to create a secure and reliable connection.
Another strategy is to insulate the fuel lines, especially those exposed to extreme temperature variations. Insulation materials like rubber or foam can help maintain the temperature of the fuel lines, reducing the impact of external temperature changes. This simple yet effective measure can prevent the lines from becoming too rigid or too flexible, ensuring consistent performance. Furthermore, regular maintenance and inspections are vital. Over time, fuel lines may degrade or develop cracks, especially in areas prone to temperature extremes. Inspecting the lines periodically can help identify any issues early on, allowing for timely repairs or replacements.
In colder climates, it is beneficial to park vehicles in garages or use fuel line heaters to maintain a consistent temperature around the fuel lines. This proactive approach can prevent the lines from freezing and becoming stiff, ensuring that the flaring process remains efficient and effective. By addressing temperature sensitivity, you can ensure that your metal fuel lines function optimally, providing a reliable fuel supply to your engine without the frustration of failed connections.
Engine Trouble: What Happens When Your Fuel Line Seals Fail
You may want to see also
Pressure Considerations: Excessive pressure can damage fuel lines
When working with metal fuel lines, it's crucial to understand the impact of pressure. Excessive pressure can lead to several issues, including damage to the fuel lines themselves. This is a critical consideration for any mechanic or DIY enthusiast looking to modify or repair fuel lines.
The primary concern with high pressure is the potential for the metal to become brittle and prone to cracking. Metal fuel lines are designed to withstand a certain amount of pressure, but when this pressure exceeds the line's capacity, it can lead to structural failure. Over time, the repeated application of excessive pressure can cause the metal to fatigue, resulting in cracks or even complete rupture. These cracks can then lead to fuel leaks, which are not only dangerous but also environmentally harmful.
To prevent such damage, it's essential to operate within the recommended pressure limits for your specific fuel line system. These limits are typically provided by the manufacturer and are designed to ensure the safe and efficient operation of the fuel system. When working with fuel lines, always refer to the manufacturer's guidelines and specifications to ensure you are using the correct tools and techniques.
Additionally, it's important to consider the type of fuel being used. Different fuels have varying properties, and some may require specific pressure conditions to ensure safe and efficient operation. For instance, high-octane fuels might require higher pressure to maintain their combustion properties, while lower-octane fuels may need to be handled with lower pressure to prevent engine knock. Understanding the fuel's characteristics and adjusting the pressure accordingly is vital for the longevity of the fuel lines and the overall performance of the vehicle.
In summary, when dealing with metal fuel lines, always be mindful of the pressure. Excessive pressure can cause damage, leading to potential safety hazards and costly repairs. By adhering to the manufacturer's guidelines and understanding the fuel's requirements, you can ensure that your fuel lines remain in optimal condition, providing reliable performance for years to come.
Fuel Line Sizing for Older Mercury Outboards: A Guide
You may want to see also
Installation Technique: Flare fitting installation requires skill and precision
The process of flaring metal fuel lines is a precise and intricate task that demands a high level of skill and attention to detail. It is not a simple job that can be accomplished by beginners or those without proper training. Flaring involves creating a smooth, seamless connection between two metal tubes, ensuring a tight seal to prevent fuel leaks and maintain system efficiency. This technique requires a deep understanding of the materials and the ability to manipulate them without causing damage.
When installing flare fittings, the installer must first ensure that the metal surfaces are clean and free of any debris or contaminants. Even a small speck of dirt can compromise the integrity of the joint. The next step is to carefully measure and mark the locations for the flares, ensuring they are aligned correctly to accommodate the fitting. This precision is crucial, as any misalignment can lead to an improper fit and potential fuel leaks.
The actual flaring process involves using specialized tools such as a flaring tool or a mandrel. These tools are designed to shape the metal tubes into a precise flare, creating a smooth, tapered surface that allows for a secure connection. The installer must apply the right amount of force and follow a specific technique to achieve the desired flare without distorting the material. This step requires a steady hand and a keen eye for detail to ensure the flare is uniform and consistent.
After flaring, the installer must inspect the joint thoroughly. The flare should be smooth and free of any sharp edges or imperfections. Any deviations from the expected flare profile can indicate a poorly executed installation, which may lead to fuel leaks or reduced system performance. Additionally, the installer should check for any signs of damage to the metal surfaces, ensuring that the flaring process did not cause any permanent deformation.
In summary, flare fitting installation is a skill-intensive task that demands precision and a methodical approach. It requires a combination of technical knowledge, hand-eye coordination, and the use of specialized tools. Proper training and practice are essential to mastering this technique, ensuring that fuel lines are installed correctly and securely, minimizing the risk of leaks and maximizing the efficiency of the fuel system.
Unleash the Power: Discover the Magic of PTFE Fuel Lines
You may want to see also
Fuel Line Diameter: Choose the correct diameter for optimal flow and fit
When it comes to fuel lines, the diameter plays a crucial role in ensuring optimal performance and a secure fit. The correct diameter is essential for efficient fuel flow and to prevent any potential issues that may arise from an improper fit. Here's a detailed guide on how to choose the right diameter for your metal fuel lines:
The first step is to understand the purpose of the fuel line. Fuel lines are responsible for transporting fuel from the tank to the engine, and the diameter determines the flow rate and pressure. A larger diameter allows for higher flow rates, which is beneficial for engines that require a substantial amount of fuel, such as high-performance vehicles or those with large displacement engines. On the other hand, smaller diameters are suitable for applications where fuel efficiency and reduced pressure drop are priorities.
To determine the correct diameter, you need to consider the engine's requirements and the type of fuel being used. Refer to the engine manufacturer's specifications or consult a fuel system design guide. These resources will provide information on the recommended fuel line diameters for specific engine models and fuel types. For instance, high-performance engines often require larger diameters to accommodate the increased fuel demand and ensure a steady supply during acceleration.
Measuring the existing fuel lines can be a practical approach to finding the right diameter. If you're replacing or modifying the fuel lines, it's essential to match the new lines with the original dimensions. You can use a caliper to measure the inside diameter of the old lines, ensuring a precise fit. Alternatively, you can consult a fuel line sizing chart, which provides a comprehensive guide for various engine types and fuel line materials. These charts will help you select the appropriate diameter based on the engine's power output and fuel requirements.
Additionally, consider the material of the fuel lines. Metal fuel lines offer durability and heat resistance, making them suitable for high-performance applications. When choosing the diameter, keep in mind that metal lines may have slightly different flow characteristics compared to rubber or plastic lines. It's crucial to select a diameter that complements the material and ensures a secure, leak-free connection.
In summary, selecting the correct fuel line diameter is a critical aspect of fuel system design. It ensures efficient fuel delivery, optimal engine performance, and a reliable connection. By considering the engine's specifications, measuring existing lines, and consulting relevant resources, you can make an informed decision when choosing the diameter for your metal fuel lines. This approach will contribute to a well-functioning fuel system and enhance the overall performance of your vehicle.
Tygon Fuel Line: Top Sources for Purchase
You may want to see also
Frequently asked questions
Metal fuel lines can be challenging to flare due to their rigid nature and the potential for damage during the flaring process. One common issue is that metal lines are often thicker and more rigid than the typical fuel lines used in vehicles, making them less flexible and more prone to kinking or bending. Additionally, metal lines may have a higher risk of puncturing or damaging the surrounding components during installation.
There are several reasons why flaring metal fuel lines might be difficult. Firstly, the material's hardness can make it resistant to the flaring process, especially if the metal is not properly prepared or pre-heated. Secondly, the design of the fuel line itself, such as sharp bends or tight radii, can hinder the flaring process. Lastly, improper tool usage or technique during flaring can lead to uneven or incomplete flares, causing the lines to fail to connect properly.
Yes, there are alternative methods to consider when dealing with metal fuel lines. One approach is to use specialized tools like hydraulic flare machines, which can apply significant force to the lines, making them more malleable. Another method is to employ a process called "braising," where the metal lines are heated and then cooled, making them more pliable. Additionally, some manufacturers offer pre-flared metal fuel lines, which can simplify the installation process.
To ensure a successful flaring process, it's essential to start with high-quality materials and properly prepare the metal lines. This may include cleaning and deburring the ends of the lines to remove any sharp edges. Pre-heating the metal can also make it more pliable. Using the correct flaring tools and techniques, such as applying the right amount of force and ensuring a consistent flare, is crucial. Finally, always follow the manufacturer's guidelines and recommendations for your specific fuel line type.