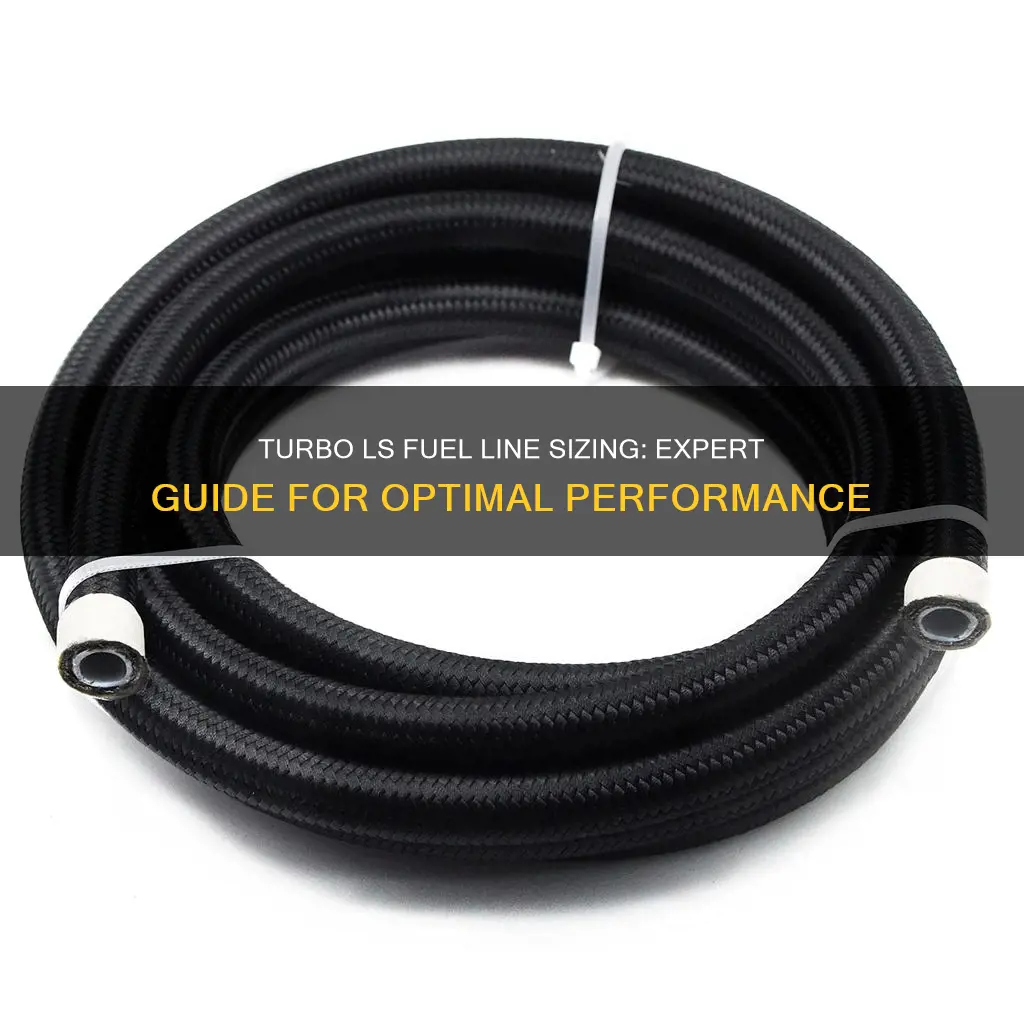
When it comes to turbocharging a LS engine, selecting the right fuel line size is crucial for optimal performance and reliability. The LS engine, known for its power and versatility, requires a fuel line that can handle the increased pressure and flow rates associated with turbocharging. In this guide, we'll explore the factors to consider when choosing the appropriate fuel line size for your LS turbo setup, ensuring you get the most out of your engine while maintaining safety and efficiency.
What You'll Learn
- Fuel Line Material: Choose the right material for durability and performance
- Line Diameter: Determine the appropriate diameter based on flow rate and pressure
- Length Considerations: Account for the vehicle's layout and engine position
- Clamping Options: Select the best clamps for a secure fit
- Compatibility: Ensure the fuel line is compatible with the Turbo LS engine
Fuel Line Material: Choose the right material for durability and performance
When it comes to fuel lines for a turbocharged LS engine, choosing the right material is crucial for ensuring optimal performance and longevity. The fuel line is responsible for delivering fuel from the tank to the engine, and any compromise in its quality can lead to issues such as fuel leaks, reduced power, and even engine damage. Here's a detailed guide on selecting the appropriate material for your fuel line:
Durability and Flexibility: The primary consideration for fuel line material is durability. Turbocharged engines produce more power and put additional stress on the fuel system. Therefore, the fuel line must be able to withstand high pressure, temperature fluctuations, and mechanical vibrations. Look for materials that offer excellent resistance to wear and tear. Rubber or synthetic rubber compounds are commonly used due to their flexibility and ability to absorb vibrations. These materials can handle the dynamic nature of a turbocharged engine without cracking or deteriorating over time.
Resistance to Fuel Contamination: Another critical aspect is the material's resistance to fuel contamination. Turbocharged LS engines often use higher-octane fuels, and any impurities or contaminants in the fuel can lead to engine knock and performance issues. Choose fuel line materials that are compatible with the fuel type you are using. For example, if you're running ethanol-blended fuel, ensure the fuel line material is resistant to ethanol's corrosive properties. Some materials, like stainless steel braids, offer excellent resistance to fuel contamination and provide a long-lasting solution.
Flexibility and Route Considerations: The fuel line needs to be flexible enough to navigate through the engine bay and various engine components without causing damage or restriction. Consider the route the fuel line will take and choose a material that allows for easy bending and routing. Flexible rubber or silicone hoses with a stainless steel inner braiding offer the best combination of flexibility and strength. Ensure that the fuel line can accommodate any engine modifications or modifications you plan to make in the future.
Temperature and Pressure Resistance: Turbocharged engines generate a significant amount of heat, so the fuel line material should be able to withstand elevated temperatures without degradation. Look for materials with high-temperature resistance, such as silicone or specialized rubber compounds. Additionally, consider the fuel pressure in your system. Some fuel lines come with pressure-rated hoses to handle the increased pressure associated with turbocharging.
Compatibility and Ease of Installation: Opt for fuel line materials that are compatible with your engine's existing components. This includes ensuring the correct inner diameter (ID) and outer diameter (OD) to fit the fuel pump, filter, and other connections. The material should also be easy to install, allowing for a secure and leak-free connection. Many manufacturers offer fuel line kits specifically designed for turbocharged LS engines, making the installation process straightforward.
By carefully selecting the right fuel line material, you can ensure that your turbocharged LS engine receives the fuel it needs efficiently and reliably. This choice will contribute to the overall performance, longevity, and satisfaction of your modified vehicle. Remember to consult with experts or refer to manufacturer guidelines for specific recommendations based on your engine setup.
John Deere Fuel Line Size 72: What You Need to Know
You may want to see also
Line Diameter: Determine the appropriate diameter based on flow rate and pressure
When it comes to fueling a turbocharged engine, such as the LS engine, the fuel line diameter is a critical factor that can significantly impact performance and reliability. The size of the fuel line determines the amount of fuel that can flow through it per unit of time, which directly affects the engine's power output and overall efficiency. Here's a detailed guide on how to determine the appropriate line diameter based on flow rate and pressure considerations:
Flow Rate: The flow rate of fuel is a crucial parameter, especially in high-performance applications. Turbocharged engines often require a precise and consistent fuel supply to maintain optimal performance. The flow rate is typically measured in gallons per minute (GPM) or liters per minute (LPM). To determine the required line diameter, you need to consider the engine's fuel requirements. For instance, a high-performance LS engine might demand a flow rate of 20-30 GPM during peak power conditions. As a rule of thumb, a larger line diameter can handle higher flow rates, ensuring that the engine receives the necessary fuel volume without restriction.
Pressure: Fuel pressure is another critical aspect that influences line diameter selection. Turbocharged engines often operate at elevated pressures to ensure efficient atomization and combustion. The pressure can vary depending on the engine's design and tuning. Generally, a higher pressure requires a larger line diameter to accommodate the increased force. For example, if your LS engine operates at 60-80 psi, you might need a larger line diameter compared to a system operating at lower pressures. This is because a smaller line would restrict the fuel flow, leading to potential performance losses.
Calculating the Optimal Diameter: To find the appropriate line diameter, you can use the following approach: Start by considering the maximum expected flow rate and pressure in your specific application. Then, refer to fuel line sizing charts or tables, which provide recommendations based on these parameters. These charts often suggest line diameters for different flow rates and pressure ranges. For instance, a 1/4-inch fuel line might be suitable for lower flow rates and pressures, while a 3/8-inch line could handle higher demands. It's essential to choose a diameter that provides a balance between flow capacity and pressure drop.
In summary, determining the correct fuel line diameter for a turbo LS engine involves considering both flow rate and pressure requirements. By matching the line size to the engine's needs, you can ensure efficient fuel delivery, optimize power output, and maintain a reliable fueling system. Remember that proper sizing is crucial to avoid restrictions and potential performance issues.
Understanding the Linear Fuel Mass Model: A Comprehensive Guide
You may want to see also
Length Considerations: Account for the vehicle's layout and engine position
When determining the appropriate fuel line size for a Turbo LS engine, it's crucial to consider the vehicle's layout and engine position. The layout of your vehicle can significantly impact the length of the fuel line required. For instance, if your Turbo LS engine is positioned in the front of the vehicle, you'll need to account for the distance between the fuel tank, typically located in the rear, and the engine. This distance can vary depending on the specific make and model of your car. Longer fuel lines may be necessary to ensure a steady and efficient fuel supply to the engine.
The engine's position relative to the vehicle's chassis is another critical factor. If the engine is mounted in a mid-engine configuration, the fuel line will need to traverse a more complex path, potentially crossing over other components or requiring additional bends. In contrast, a front-engine layout may offer more straightforward routing options. Understanding the vehicle's architecture will help you visualize the optimal fuel line path and ensure it doesn't interfere with other systems or cause unnecessary strain on the fuel line.
Additionally, consider the vehicle's overall design and any unique features. Some cars have unconventional fuel tank placements or engine compartments that can affect the fuel line's length and routing. For example, a vehicle with a low-slung engine bay might require shorter fuel lines to accommodate the limited space. Conversely, a vehicle with a high-mounted engine may allow for longer fuel lines.
To ensure optimal performance and reliability, it's essential to measure the actual distance between the fuel source and the engine. This can be done by physically inspecting the vehicle or using detailed diagrams provided by the manufacturer. By accurately assessing the length required, you can select the appropriate fuel line size, ensuring a consistent fuel supply to the Turbo LS engine.
Remember, the goal is to provide a fuel line that is long enough to reach the engine without being overly long, as excessive length can lead to fuel pressure issues and reduced performance. Proper consideration of the vehicle's layout and engine position will help you make an informed decision when choosing the correct fuel line size for your Turbo LS setup.
Fuel Rail Basics: Understanding the Line for Optimal Performance
You may want to see also
Clamping Options: Select the best clamps for a secure fit
When it comes to installing a fuel line for a Turbo LS engine, choosing the right clamping options is crucial for a secure and reliable setup. The goal is to ensure a tight seal that prevents fuel leaks while allowing for flexibility to accommodate the engine's movement during operation. Here's a breakdown of the clamping considerations:
Clamp Types:
There are several types of clamps commonly used for fuel lines:
- Metal Clamps: These are durable and offer excellent holding power. They are often made from stainless steel or aluminum, ensuring longevity even in harsh environments. Metal clamps are ideal for high-pressure fuel lines as they provide a robust seal. However, they can be more aggressive in their grip, potentially causing damage to the fuel line if not properly sized.
- Rubber Clamps: Rubber clamps offer a more flexible and vibration-damping solution. They are gentler on the fuel line and provide a secure hold without the risk of damage. Rubber clamps are often used in conjunction with metal clamps for added security. This combination is especially useful when dealing with fuel lines that have a tendency to vibrate or move during engine operation.
- Elastomeric Clamps: These clamps are made from a flexible material that provides a secure grip while allowing for some movement. They are less aggressive than metal clamps and are often used in applications where the fuel line needs to accommodate slight engine movement. Elastomeric clamps are a good choice for fuel lines that are not under extreme pressure.
Clamping Force:
The clamping force should be sufficient to create a tight seal but not so aggressive that it causes damage to the fuel line. A good rule of thumb is to use a clamp that applies a force of around 10-15% of the fuel line's diameter. This ensures a secure hold without putting excessive stress on the material.
Clamping Placement:
Clamps should be placed at regular intervals along the fuel line to ensure even pressure distribution. Typically, you'll want to place a clamp every 6-12 inches. Avoid placing clamps too close to bends or elbows in the fuel line, as this can restrict flow and cause stress concentrations. Additionally, ensure that clamps are not positioned where they could interfere with other components or cause damage during engine operation.
Customizing Clamps:
In some cases, you might need to customize the clamp size or shape to fit the specific fuel line and engine configuration. This can be done using clamp adapters or by fabricating custom clamps. When customizing, ensure that the clamp material is compatible with the fuel line material to avoid any potential corrosion or degradation issues.
Aluminum or Steel: Choosing the Right Fuel Line Material
You may want to see also
Compatibility: Ensure the fuel line is compatible with the Turbo LS engine
When it comes to Turbo LS engines, ensuring the compatibility of the fuel line is crucial for optimal performance and longevity. The Turbo LS engine, known for its powerful output and high-performance capabilities, requires a fuel line that can handle the demands of this high-output system. Compatibility is key to maintaining the engine's efficiency and reliability.
The first step in selecting the right fuel line is to understand the engine's requirements. Turbo LS engines often utilize a high-pressure fuel system, which demands a fuel line that can withstand increased pressure and temperature. The fuel line should be designed to handle the specific flow rates and pressures associated with this engine type. It is essential to choose a fuel line that meets or exceeds the manufacturer's specifications to ensure a proper fit and performance.
One critical aspect of compatibility is the material of the fuel line. Different materials have varying levels of flexibility, durability, and resistance to heat and pressure. For Turbo LS engines, a fuel line made from high-quality, heat-resistant materials is ideal. Materials like stainless steel or high-temperature-rated plastics can ensure the line can withstand the engine's operating conditions without degradation or failure. These materials also provide excellent flexibility, allowing for easier installation and routing within the engine bay.
Additionally, the fuel line's diameter or size is a critical factor in compatibility. The Turbo LS engine requires a specific fuel flow rate to meet its power demands. A fuel line with an appropriate diameter ensures that the fuel can flow efficiently and at the required pressure. Common sizes for Turbo LS fuel lines range from 3/8" to 1/2" ID (inside diameter), depending on the engine's configuration and performance requirements. It is essential to consult the engine's manual or seek professional advice to determine the exact size needed for your specific Turbo LS setup.
Furthermore, considering the fuel line's routing and installation is vital. Turbo LS engines often have limited space, so the fuel line must be compatible with the engine bay's layout. The line should be able to route around various components without causing interference or damage. Proper installation, including the use of compatible fittings and clamps, ensures a secure and leak-free connection. By paying attention to these compatibility factors, you can ensure that the fuel line is tailored to the Turbo LS engine's needs, resulting in improved performance and a longer-lasting fuel system.
Kawasaki Engine Fuel Line Diameter: A Comprehensive Guide
You may want to see also
Frequently asked questions
For a Turbo LS engine, a common recommendation is to use a 1/4-inch fuel line. This size is often considered a standard for high-performance applications and can handle the increased fuel flow required by the turbocharger.
While it is possible to use a smaller fuel line, it is generally not recommended. A smaller line might restrict fuel flow, leading to potential performance issues and reduced power. Opting for a 1/4-inch line ensures sufficient fuel delivery to the engine.
The ideal fuel line size depends on various factors, including the engine's power output, fuel pump specifications, and overall system design. Consulting with an experienced mechanic or referring to a reputable performance guide specific to your Turbo LS build is advisable to ensure you choose the correct size for optimal performance and safety.