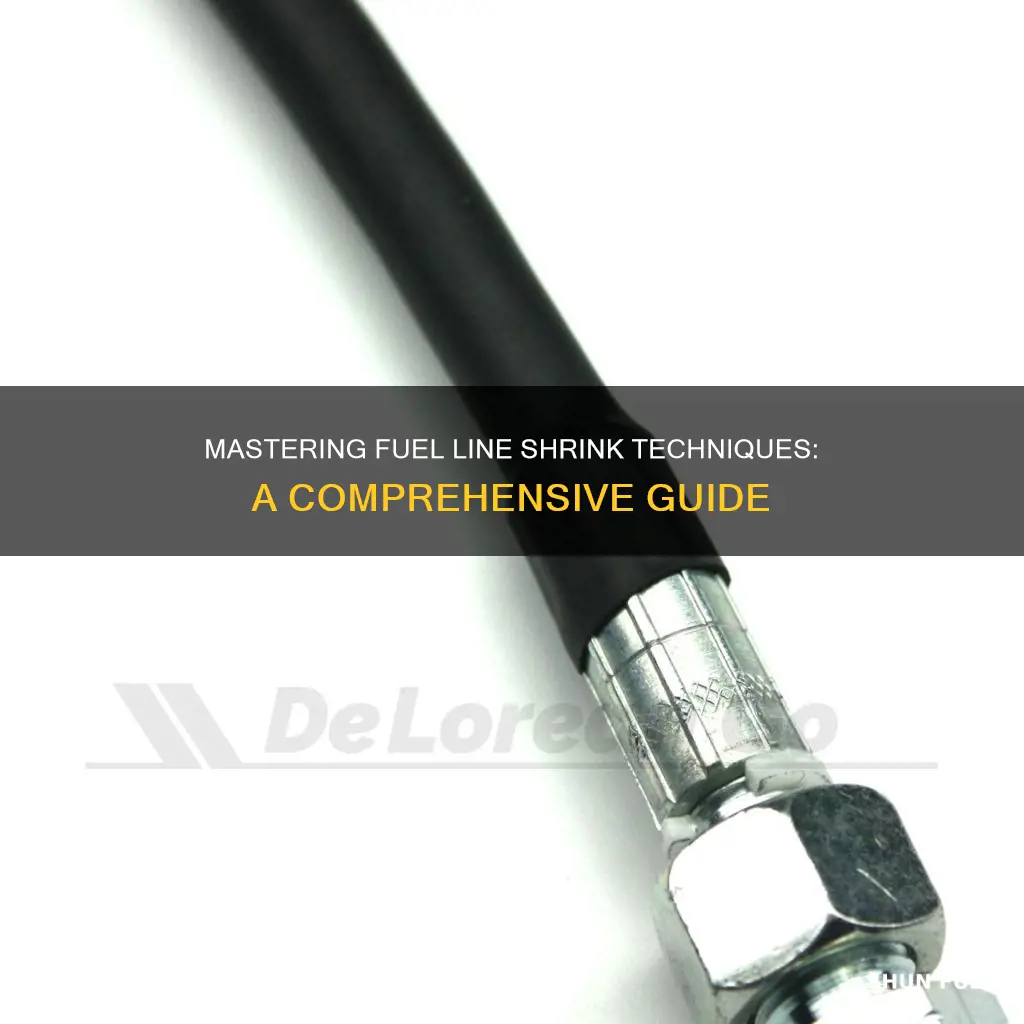
Shrinking fuel lines is a crucial step in ensuring the efficient and safe operation of any vehicle's fuel system. This process involves reducing the size of the fuel lines to optimize fuel flow and pressure, which can enhance performance and improve overall engine efficiency. It is a common practice in automotive maintenance, especially when dealing with older vehicles or those with modified engines. By carefully shrinking the fuel lines, mechanics can prevent fuel leaks, improve engine performance, and ensure that the vehicle's fuel system operates at its best. This guide will provide a detailed overview of the process, including the necessary tools, techniques, and safety precautions to ensure a successful and safe fuel line shrinking operation.
What You'll Learn
- Fuel Line Material: Choose the right material for your fuel line, considering compatibility and durability
- Clamping and Support: Secure the fuel line with proper clamps and supports to prevent movement
- Bending and Routing: Route the fuel line away from heat sources and sharp bends to avoid damage
- Pressure Testing: Conduct pressure tests to ensure the fuel line can withstand fuel pressure without leaking
- Maintenance and Inspection: Regularly inspect and maintain the fuel line to prevent wear and tear
Fuel Line Material: Choose the right material for your fuel line, considering compatibility and durability
When it comes to choosing the right material for your fuel line, compatibility and durability are key factors to ensure the safe and efficient operation of your vehicle's fuel system. The fuel line is a critical component that connects the fuel tank to the engine, and using the appropriate material is essential to prevent leaks, ensure proper fuel flow, and maintain the overall performance of your vehicle.
One of the most commonly used materials for fuel lines is rubber, which offers excellent flexibility and resistance to abrasion. Natural rubber is a popular choice due to its inherent flexibility and ability to withstand the corrosive effects of fuel. It is also relatively easy to install and can accommodate slight movements in the vehicle's structure. However, it's important to note that natural rubber may not be as durable as other materials, especially in extreme temperature conditions. To enhance its durability, rubber fuel lines are often reinforced with layers of steel or synthetic fibers, providing added strength and protection against punctures.
For applications requiring higher temperature resistance and increased flexibility, synthetic rubber compounds, such as neoprene or EPDM (ethylene propylene diene monomer), are excellent alternatives. These materials offer superior resistance to heat and chemicals, making them ideal for high-performance vehicles or those operating in harsh environments. Synthetic rubber fuel lines are known for their ability to maintain flexibility even in sub-zero temperatures, ensuring reliable fuel delivery to the engine.
Another popular choice for fuel lines is braided stainless steel. This material is highly durable and resistant to corrosion, making it suitable for long-term use in fuel systems. The stainless steel braid provides excellent flexibility, allowing the fuel line to navigate through tight spaces and engine compartments without kinking or bending. Additionally, the braided design offers a smooth inner surface, reducing the risk of fuel contamination and ensuring optimal fuel flow.
When selecting the material, it is crucial to consider the specific requirements of your vehicle and the operating conditions it will endure. Factors such as temperature extremes, exposure to sunlight, and the presence of chemicals in the fuel should be taken into account. Consulting the vehicle's manual or seeking advice from automotive experts can provide valuable guidance on the recommended fuel line materials for your particular make and model.
In summary, choosing the right fuel line material involves a careful consideration of compatibility and durability. Natural rubber offers flexibility, while synthetic rubber provides enhanced temperature resistance. Braided stainless steel ensures long-lasting performance and corrosion resistance. By selecting the appropriate material, you can ensure a reliable and efficient fuel system for your vehicle, promoting optimal engine performance and longevity.
Fuel Line Liter Valve: Location and Function
You may want to see also
Clamping and Support: Secure the fuel line with proper clamps and supports to prevent movement
When working on shrinking a fuel line, proper clamping and support are crucial to ensure the line remains secure and doesn't move or vibrate, which could lead to potential issues. Here's a detailed guide on how to achieve this:
Clamping the Fuel Line: Start by identifying the appropriate clamp for your specific fuel line. Clamps come in various sizes and materials, so it's essential to choose one that fits the diameter of your fuel line and is compatible with the material. For fuel lines, rubber or plastic clamps are commonly used. Slide the clamp onto the fuel line, ensuring it covers the entire length of the section you want to secure. The clamp should be snug, but not overly tight, as this can restrict flow. Use a pair of pliers or a clamp tool to adjust the clamp until it is secure and in place. It's important to check the manufacturer's guidelines for the correct clamping force to avoid damaging the fuel line.
Supporting the Fuel Line: Proper support is essential to prevent the fuel line from sagging or being subjected to excessive stress. Start by identifying potential support points along the route of the fuel line. These points could be engine mounts, frame rails, or other structural components. Secure the fuel line to these support points using ties or brackets. Ensure that the ties are tight and prevent any movement of the fuel line. For longer sections, consider using multiple support points to distribute the load evenly. Avoid securing the fuel line too tightly, as this can restrict flow and cause damage over time.
When clamping and supporting the fuel line, it's crucial to maintain a consistent and secure fit. Regularly inspect the clamps and supports to ensure they remain intact and effective. Over time, clamps can loosen due to vibration and movement, so periodic checks are essential. Additionally, be mindful of any modifications or repairs made to the vehicle, as these may require adjustments to the fuel line's position and support.
Remember, the goal is to provide a secure and stable environment for the fuel line, minimizing any potential movement that could lead to issues. Proper clamping and support will contribute to the overall reliability and longevity of your fuel system.
Mini Cooper's Torque Stage: Unlocking Power with Fuel Lines
You may want to see also
Bending and Routing: Route the fuel line away from heat sources and sharp bends to avoid damage
When working with fuel lines, proper bending and routing are crucial to ensure the system's longevity and performance. One of the primary considerations is to route the fuel line away from heat sources and sharp bends to avoid potential damage. Heat can cause the fuel line to expand and contract, leading to cracks or leaks over time. Therefore, it's essential to identify and avoid any areas that generate significant heat, such as exhaust systems, engine compartments, or even hot surfaces near the vehicle's body. By keeping the fuel line at a safe distance from these heat sources, you minimize the risk of thermal stress and potential failure.
Bending the fuel line should be done with care to prevent sharp bends that could restrict flow or cause damage. The ideal bending radius for fuel lines is typically around 2 to 3 times the diameter of the line. This ensures that the line can flex without kinking or putting excessive pressure on the material. When bending, it's recommended to use a fuel line bending tool or a similar device to achieve a smooth and consistent bend. This tool helps to maintain the line's integrity and reduces the chances of creating sharp bends that might compromise the fuel flow.
Avoiding sharp bends is particularly important when the fuel line needs to pass through tight spaces or around obstacles. In such cases, consider using a fuel line bracket or a similar support to guide the line and maintain its shape. This not only helps in preventing sharp bends but also ensures that the line remains secure and in place, reducing the likelihood of accidental damage. Additionally, routing the fuel line in a way that allows for some flexibility can help accommodate minor vibrations or movements without causing stress on the line.
In summary, when shrinking or working with fuel lines, it is imperative to pay close attention to bending and routing techniques. By routing the fuel line away from heat sources and sharp bends, you can significantly reduce the risk of damage and ensure the system's reliability. Proper bending techniques, including the use of appropriate tools and maintaining a suitable bending radius, are essential to avoid kinking or putting unnecessary strain on the fuel line material. Following these guidelines will contribute to a well-maintained fuel system, providing efficient and safe operation.
Understanding R3 Fuel Line: A Comprehensive Guide
You may want to see also
Pressure Testing: Conduct pressure tests to ensure the fuel line can withstand fuel pressure without leaking
Pressure testing is a critical step in ensuring the integrity and reliability of your fuel system, especially when dealing with fuel lines that have been shrunk or modified. This process involves subjecting the fuel line to specific pressure conditions to verify its ability to contain fuel without any leaks. Here's a detailed guide on how to conduct pressure testing for this purpose:
Preparation: Before initiating the pressure test, ensure you have the necessary tools and equipment. You'll need a pressure gauge, a source of compressed air or nitrogen, and a container to collect any fuel that may leak during the test. It is also advisable to have a second person assist you, especially when working with high-pressure systems.
Test Setup: Start by disconnecting the fuel line from the fuel tank and any other connected components. Securely attach the pressure gauge to the fuel line, ensuring it is positioned where the pressure can be accurately measured. Then, connect the compressed air or nitrogen source to the opposite end of the fuel line. The goal is to create a controlled environment where you can simulate the fuel pressure conditions the line will encounter in a real-world scenario.
Pressure Application: Gradually increase the pressure in the fuel line using the compressed air or nitrogen source. Start with a lower pressure and gradually build up to the expected fuel system pressure. This gradual approach allows you to identify any potential issues early on. As the pressure increases, closely monitor the fuel line for any signs of leakage. Pay attention to any unusual noises, vibrations, or visual indicators of a potential leak.
Leak Detection: During the pressure test, be vigilant for any signs of fuel escaping from the line. Leaks can occur at connections, fittings, or even where the fuel line has been shrunk onto a surface. If a leak is detected, immediately release the pressure and inspect the affected area. Use a soapy water solution to create a visual indicator of leaks, as bubbles will form at the source of the leak. This method is an effective way to pinpoint the exact location of any issues.
Documentation and Analysis: Document the pressure levels at which leaks occur, if any. Record the time taken to reach those pressure levels. This data will help you understand the fuel line's performance and identify any weaknesses. If no leaks are found, the fuel line has successfully passed the pressure test, and you can proceed with the installation or further modifications.
By following these steps, you can ensure that the fuel line is capable of withstanding the required fuel pressure without compromising its integrity. Pressure testing is an essential safety measure, especially when working with fuel systems, as it helps prevent potential hazards associated with fuel leaks.
Understanding the Fuel Tank Return Line: A Comprehensive Guide
You may want to see also
Maintenance and Inspection: Regularly inspect and maintain the fuel line to prevent wear and tear
Regular maintenance and inspection of the fuel line are crucial to ensure optimal performance and longevity of your vehicle's fuel system. Over time, fuel lines can experience wear and tear due to various factors such as age, temperature fluctuations, and exposure to contaminants. Neglecting this maintenance can lead to fuel leaks, reduced engine performance, and potential safety hazards. Here's a comprehensive guide on how to maintain and inspect your fuel line to prevent these issues:
Start by familiarizing yourself with the location of the fuel line in your vehicle. Fuel lines are typically made of rubber or a flexible material and are responsible for transporting fuel from the tank to the engine. They are often located beneath the vehicle, running along the frame, and may be secured with clips or brackets. Inspecting the fuel line regularly allows you to identify any signs of damage or deterioration. Look for cracks, splits, or bulges in the rubber material, as these could indicate wear and tear. Also, check for any signs of corrosion or rust, especially if the fuel line is exposed to the elements.
A simple yet effective maintenance practice is to use a fuel line cleaner. Over time, fuel can accumulate in the line, leading to contamination and potential blockages. Using a fuel line cleaner can help remove these contaminants and ensure the line remains clear and functional. Follow the instructions provided with the cleaner, typically involving a flushing process to remove any built-up debris. This process can be done at home or by a professional mechanic.
During your inspections, pay close attention to the connections and fittings of the fuel line. These points are susceptible to corrosion and leakage. Check for any signs of corrosion around the fittings and ensure they are tight and secure. If you notice any corrosion, consider replacing the affected fittings to prevent potential leaks. Additionally, inspect the fuel line for any signs of damage near the engine bay, as the high-temperature environment can accelerate wear and tear.
Regularly checking the fuel line's flexibility and movement is essential. Over time, the line may become stiff or brittle, making it difficult to maneuver. This can be a result of age or exposure to extreme temperatures. If you notice any rigidity, consider replacing the fuel line to ensure proper fuel flow. It's also a good practice to inspect the fuel line for any signs of damage when performing routine engine maintenance, such as oil changes.
In summary, maintaining and inspecting your fuel line is a critical aspect of vehicle care. By regularly checking for damage, contamination, and wear, you can prevent potential issues and ensure your engine receives the fuel it needs to operate efficiently. Remember, early detection of any problems can save you from costly repairs and ensure the longevity of your vehicle's fuel system.
Honda CM450C Fuel Line Sizing: A Comprehensive Guide
You may want to see also
Frequently asked questions
Shrinking a fuel line is a process used to repair or replace damaged fuel lines. It involves reducing the diameter of the line to create a tight seal around the fuel pipe, ensuring a secure and leak-free connection.
Common signs include fuel leaks, engine misfires, reduced performance, or strange noises from the fuel system. If you suspect any issues, it's best to inspect the fuel lines for damage, cracks, or corrosion.
You'll need a fuel line shrinking tool kit, which typically includes a heat source (like a heat gun or torch), a fuel line shrinking tube or sleeve, and a pair of pliers or a fuel line cutter. Ensure you have the appropriate size and length of the shrinking tube for the fuel line.
Yes, you can shrink a fuel line in place. This method requires careful alignment and precise shrinking to avoid damaging the surrounding components. It's a more advanced technique and should be done with caution.
Always work in a well-ventilated area and wear protective gear, including gloves and safety goggles. Ensure the engine is off and the fuel supply is disconnected before starting the shrinking process. Be cautious with heat sources to prevent burns, and follow manufacturer guidelines for specific fuel line materials.