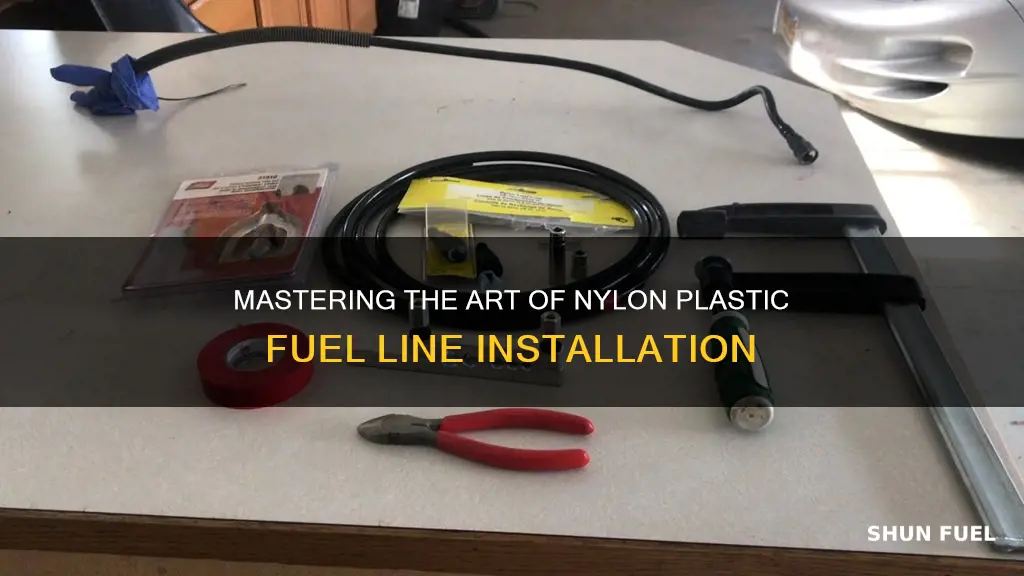
Nylon plastic fuel lines are an essential component in the automotive industry, offering a lightweight and durable alternative to traditional rubber hoses. This guide will provide a comprehensive overview of how to install and maintain nylon plastic fuel lines, ensuring optimal performance and longevity. From understanding the different types of nylon fuel lines available to learning the proper installation techniques, this resource will equip you with the knowledge needed to make informed decisions and ensure a reliable fuel delivery system in your vehicle.
What You'll Learn
- Materials and Tools: Gather necessary supplies like nylon fuel lines, connectors, and crimping tools
- Preparation: Clean and inspect the fuel line and fittings for damage or debris
- Installation: Route the line, secure with clips, and connect to fuel source
- Testing: Check for leaks and ensure proper flow using a pressure gauge
- Maintenance: Regularly inspect and replace worn-out lines to prevent fuel leaks
Materials and Tools: Gather necessary supplies like nylon fuel lines, connectors, and crimping tools
When embarking on a project to replace or repair your fuel lines with nylon plastic, it's crucial to gather the right materials and tools to ensure a successful and safe installation. Here's a comprehensive guide on what you need:
Materials:
- Nylon Fuel Lines: Choose nylon fuel lines that are compatible with your vehicle's fuel type. Different types of nylon are available, so select one suitable for gasoline or diesel applications. Consider the length required to connect the fuel source to the engine.
- Connectors: These are essential for joining the fuel lines to the fuel pump, injectors, and other components. Select connectors that match the diameter of your nylon fuel lines. Common types include barbed connectors, compression fittings, or quick-connect fittings, depending on your preference and the system's design.
- Hose Clamps: Hose clamps are used to secure the fuel lines to the engine and other surfaces, ensuring a tight and leak-free connection. Opt for stainless steel or heavy-duty metal hose clamps for durability.
Tools:
- Crimping Tool: A crimping tool is essential for installing connectors securely. It applies pressure to the connector's end, creating a tight seal with the fuel line. Ensure you have a crimping tool suitable for the connector type you've chosen.
- Pipe Cutter or Utility Knife: These tools will help you cut the nylon fuel lines to the desired length. A pipe cutter is ideal for a clean and precise cut, but a utility knife can be used as a backup.
- Pliers: Pliers are handy for gripping and manipulating small components, especially when working with connectors and fuel line fittings.
- Fuel Line Brush: A specialized brush designed for fuel lines can help remove any debris or old fuel residue during the installation process.
- Safety Gear: Don't forget to wear safety gear, including gloves and eye protection, to safeguard yourself during the project.
Having all these materials and tools ready will ensure you can tackle the fuel line replacement or repair task efficiently and effectively. It's always a good idea to double-check the compatibility of the parts and tools with your specific vehicle and fuel system to avoid any complications during the installation process.
Mercury Verado Fuel Line Removal: A Step-by-Step Guide
You may want to see also
Preparation: Clean and inspect the fuel line and fittings for damage or debris
Before you begin any work on the nylon plastic fuel line, it's crucial to ensure a clean and safe working environment. Start by disconnecting the fuel line from the fuel tank and the engine. This step is essential for safety and to prevent any accidental fuel spills. Once disconnected, place the fuel line in a well-ventilated area or even outdoors to allow any remaining fuel to evaporate. This process is important to avoid any potential hazards during the cleaning and inspection process.
Next, you'll need to clean the fuel line. Over time, fuel lines can accumulate debris, varnish, and other contaminants. To clean it, you can use a fuel line cleaner, which is typically a concentrated chemical solution. Pour the cleaner into a bucket and immerse the fuel line in it, ensuring it's fully submerged. Allow the cleaner to work for the recommended time, which usually ranges from 15 minutes to an hour, depending on the product. After the specified time, use a stiff brush or a specialized fuel line brush to scrub the interior of the line, removing any built-up contaminants. Rinse the fuel line thoroughly with clean water to eliminate any remaining cleaner and debris.
While cleaning, it's also a good opportunity to inspect the fuel line for any signs of damage or wear. Look for cracks, splits, or any discolouration in the nylon material. Check for any signs of deterioration, especially around the fittings and bends, as these areas are more susceptible to damage. Inspect the fuel line for any blockages or obstructions. If you notice any debris or foreign objects inside the line, remove them carefully. Ensure that the fuel line is straight and free-flowing, as any kinks or twists can affect fuel delivery and engine performance.
For the fittings, inspect them for any signs of corrosion or damage. Check the threads and ensure they are tight and secure. If any fittings are damaged or corroded, it's best to replace them to ensure a reliable fuel supply. After cleaning and inspecting, rinse the fuel line again to remove any cleaning solution and debris. Allow it to air dry completely before reinstalling it. Proper preparation and inspection are key to ensuring the longevity and functionality of your nylon plastic fuel line.
Fuel Lines for 2005 Yukon: Expert Sources Revealed
You may want to see also
Installation: Route the line, secure with clips, and connect to fuel source
When installing a nylon plastic fuel line, proper routing and securement are crucial to ensure a safe and efficient fuel supply. Here's a step-by-step guide to help you through the process:
Routing the Line: Begin by carefully planning the path of the fuel line. It should be routed away from heat sources, vibrations, and potential impact areas to prevent damage. Consider the vehicle's layout and choose a route that allows for easy access during maintenance. Ensure the line is not twisted or kinked, as this can restrict fuel flow and cause potential issues. Use appropriate supports or brackets to keep the line in place and maintain its integrity.
Securing with Clips: Nylon fuel lines often come with metal or plastic clips designed to secure the line in place. These clips should be attached at regular intervals along the route. Start by identifying the key areas where the line needs support, such as near the engine, under the dashboard, or around sharp bends. Slide the clips over the fuel line and ensure they are firmly in place. The clips should be tight enough to hold the line securely but not so tight that they cause any damage or restrict the line's flexibility.
Connecting to Fuel Source: The final step is to connect the nylon fuel line to the fuel source, typically the fuel tank or the engine's fuel injection system. Start by identifying the correct fittings and adapters required for your specific setup. Clean the fuel line ends and the corresponding fittings to ensure a proper connection. Slide the fittings onto the fuel line and tighten them securely. Use the appropriate tools to ensure a tight seal and prevent any fuel leaks. Double-check all connections to ensure they are secure and properly aligned.
Remember, when working with fuel lines, it's essential to follow manufacturer guidelines and safety protocols. Always wear protective gear, especially when handling fuel, and ensure proper ventilation in the work area. By following these detailed steps, you can ensure a successful installation, providing a reliable and efficient fuel supply for your vehicle.
97 Chevy K1500 Fuel Line Sizes: A Guide
You may want to see also
Testing: Check for leaks and ensure proper flow using a pressure gauge
When working with nylon plastic fuel lines, it's crucial to perform thorough testing to ensure they are leak-free and functioning correctly. One essential method is using a pressure gauge to check for leaks and verify proper flow. Here's a step-by-step guide on how to conduct this test:
Preparation: Before starting, ensure you have the necessary tools, including a pressure gauge, a source of compressed air or nitrogen, and a cleaning agent suitable for fuel lines. It's also advisable to wear protective gear, such as gloves and safety goggles, to avoid any potential hazards.
Step 1: Connect the Pressure Gauge: Start by connecting the pressure gauge to the fuel line. Ensure a secure and tight connection to avoid any potential leaks during the testing process. You can use specialized fittings or adapters if needed.
Step 2: Apply Pressure: Introduce compressed air or nitrogen into the fuel line using the pressure source. Gradually increase the pressure to a level that is safe for the system and within the recommended operating range. Typically, a pressure of 50-100 psi (pounds per square inch) is a good starting point, but consult the fuel line's specifications for precise guidelines.
Step 3: Inspect for Leaks: While maintaining the applied pressure, visually inspect the fuel line for any signs of leaks. Check all connections, fittings, and joints for any visible moisture, fuel accumulation, or bubbles. Pay close attention to areas where the line connects to the fuel tank, pump, or other components. Leaks can occur due to damaged lines, improper connections, or compromised seals.
Step 4: Flow Testing: After confirming there are no leaks, proceed with flow testing. This step ensures that the fuel line can handle the required flow rate without restrictions. Gradually increase the pressure further and observe the fuel flow. A properly functioning nylon plastic fuel line should allow for smooth and consistent fuel flow without any blockages or pressure drops. If you notice any fluctuations or reduced flow, it may indicate a potential issue with the line or its connections.
Step 5: Record and Adjust: Document the pressure and flow rates during the test. Compare these values with the manufacturer's specifications to ensure they fall within the acceptable range. If any deviations are observed, consider adjusting the pressure or inspecting the fuel line for potential obstructions or damage.
Remember, proper testing is critical to maintaining the integrity of your fuel system. By following these steps and using a pressure gauge, you can effectively identify and address any potential issues with nylon plastic fuel lines, ensuring optimal performance and safety.
PTFE Tape: A Reliable Seal for Automotive Fuel Lines?
You may want to see also
Maintenance: Regularly inspect and replace worn-out lines to prevent fuel leaks
Regular maintenance of the fuel lines in your vehicle is crucial to ensure optimal performance and prevent potential issues. Nylon plastic fuel lines are a common choice for their durability and flexibility, but even these robust components require careful attention over time. Here's a guide on how to maintain your nylon plastic fuel lines effectively:
Visual Inspection: Start by regularly inspecting the fuel lines for any signs of wear and tear. Visual checks are essential to identify potential problems early on. Look for cracks, brittleness, or any visible damage along the length of the lines. Inspect the connections and fittings as well; ensure they are secure and free from corrosion or leaks. Pay attention to areas where the lines are more susceptible to damage, such as under the vehicle or near heat sources.
Flexibility and Movement: Nylon plastic fuel lines should maintain their flexibility, allowing for movement as the vehicle's components shift during operation. Check if the lines can move freely without excessive rigidity or stiffness. If you notice any lines that are no longer flexible and seem to have lost their shape, it may indicate internal damage or degradation.
Leak Prevention: The primary goal of regular maintenance is to prevent fuel leaks, which can be dangerous and costly. Inspect the lines for any signs of fuel seepage or moisture. Moisture in the fuel lines can lead to corrosion and potential engine damage. If you detect any leaks, it is imperative to replace the affected lines immediately. Even small cracks or punctures can result in significant fuel loss over time.
Replacement and Timing: Nylon plastic fuel lines typically have a lifespan, and regular replacements are recommended to avoid unexpected failures. Consider the age of the lines and the vehicle's usage. As a general rule, it's advisable to replace fuel lines every 5-7 years, or sooner if you notice any issues during inspections. Keep a record of your inspections and replacements to ensure you stay on top of this critical maintenance task.
Professional Assistance: While regular visual inspections can be performed by vehicle owners, it is beneficial to have a professional mechanic inspect the fuel lines during routine service intervals. Mechanics have the expertise to identify subtle issues that may not be immediately apparent. They can also ensure that all connections are secure and that the lines are properly routed to avoid damage.
Mercury Outboard 225: Venting Fuel Lines for Optimal Performance
You may want to see also
Frequently asked questions
Nylon plastic fuel lines are commonly used in automotive applications for fuel delivery systems. They offer several advantages over traditional rubber hoses. Nylon is known for its excellent resistance to fuel degradation, ensuring longer hose life and maintaining the quality of the fuel. It also provides better flexibility and durability, making it suitable for tight spaces and harsh environments.
Installation of nylon fuel lines is relatively straightforward. Start by cleaning the areas where the lines will be connected to ensure a secure fit. Use a fuel line cutter to achieve precise lengths. Then, slip the fuel line over the fuel fitting or adapter, ensuring a snug fit. Secure the line with clamps or ties, allowing for some slack to accommodate movement. Finally, route the line through the designated path, ensuring it is not pinched or damaged.
Nylon fuel lines are generally compatible with most common fuels used in vehicles, including gasoline, diesel, and ethanol blends. However, it's essential to check the specific fuel type and its properties. Some fuels, like high-octane gasoline or certain types of biofuels, may have unique requirements. Always refer to the manufacturer's guidelines or consult an expert to ensure compatibility.
Yes, nylon fuel lines can handle high-pressure systems, making them suitable for applications requiring increased pressure, such as turbochargers or superchargers. Nylon's ability to maintain flexibility under pressure and its resistance to fuel degradation make it an excellent choice for high-performance vehicles. However, it's crucial to select the appropriate diameter and thickness to handle the specific pressure requirements of your system.