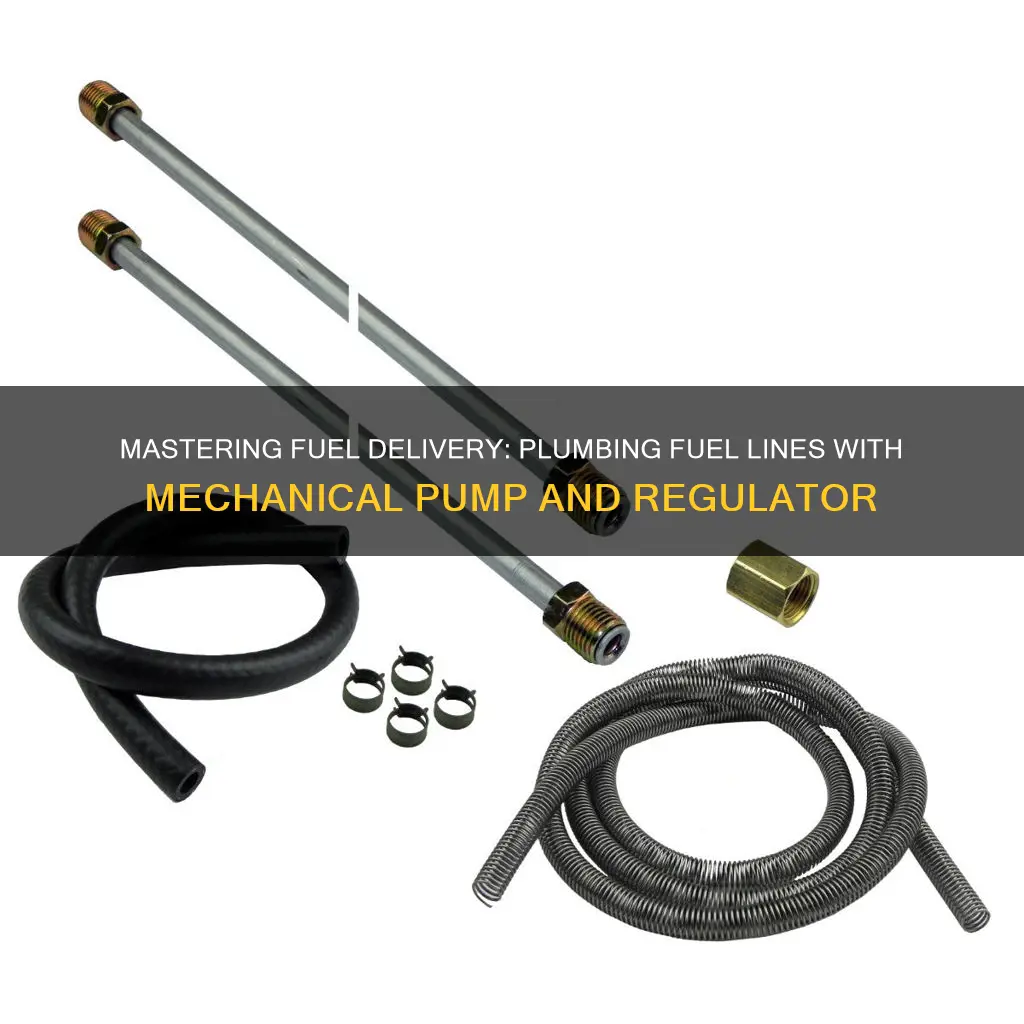
Plumbing fuel lines is a crucial step in any vehicle's maintenance routine, especially when using a mechanical pump and regulator system. This process involves carefully routing fuel from the tank to the engine, ensuring a steady and controlled supply of fuel for optimal performance. The task requires precision and an understanding of the system's components to ensure a reliable and safe fuel delivery mechanism. By following a step-by-step guide, you can effectively plumb fuel lines, ensuring your vehicle's engine receives the necessary fuel for efficient operation.
What You'll Learn
- Fuel Tank Setup: Ensure proper fuel tank installation and secure fuel lines
- Pump Installation: Mount the mechanical pump securely and connect fuel lines
- Regulator Placement: Position the regulator near the pump for optimal performance
- Line Routing: Route fuel lines away from heat sources and potential hazards
- Testing and Adjustments: Test the system, adjust pressure, and fine-tune for efficiency
Fuel Tank Setup: Ensure proper fuel tank installation and secure fuel lines
When setting up a fuel tank system with a mechanical pump and regulator, proper installation and secure fuel lines are crucial to ensure optimal performance and safety. Here's a step-by-step guide to achieving this:
Tank Installation: Begin by carefully installing the fuel tank in the designated location. Ensure it is securely mounted and aligned correctly. The tank should be positioned to allow easy access for maintenance and refuelling. Use appropriate mounting hardware to attach the tank to the vehicle's frame or structure, ensuring it remains stable and vibration-free during operation.
Fuel Line Routing: Route the fuel lines carefully, following the manufacturer's guidelines and local regulations. The lines should be positioned to avoid any potential damage or interference with moving parts. Keep the lines as straight and short as possible to minimize the risk of kinking or stress on the connections. Use appropriate fuel line clips or ties to secure the lines in place, ensuring they are not pinched or restricted.
Pump and Regulator Placement: Install the mechanical pump and regulator in a location that provides easy access for maintenance. Position them near the fuel tank to ensure efficient fuel transfer. Secure the pump and regulator using mounting brackets or straps to prevent movement and ensure they remain in place during operation.
Fuel Line Connections: Connect the fuel lines to the pump, regulator, and tank using appropriate fittings and adapters. Ensure all connections are tight and secure. Check for any leaks by applying a small amount of fuel to the connections and observing for any drips. If a leak is detected, tighten the connections or replace the fittings as necessary.
Testing and Inspection: After the installation, test the system by starting the engine and monitoring the fuel flow. Check for any unusual noises or vibrations, which may indicate issues with the fuel lines or connections. Inspect the entire setup for any signs of damage or wear, especially at bends and fittings. Regularly maintain and inspect the fuel tank and lines to ensure optimal performance and prevent potential issues.
Remember, proper installation and secure fuel line management are essential for the reliable operation of your fuel system. Always refer to the manufacturer's instructions and local regulations for specific requirements and safety guidelines.
Mastering the Art of Two-Line Fuel System Conversion: A Comprehensive Guide
You may want to see also
Pump Installation: Mount the mechanical pump securely and connect fuel lines
When installing a mechanical pump, it's crucial to ensure a secure and stable setup to guarantee optimal performance and prevent any fuel leaks. Here's a step-by-step guide to mounting the pump and connecting the fuel lines:
Mounting the Pump:
- Choose a suitable location for the pump, typically near the fuel tank or the engine bay. Ensure it is easily accessible for maintenance and has enough clearance for the pump's components.
- Secure the pump using mounting brackets or straps. Tighten the fasteners firmly to provide a solid foundation for the pump's operation. Ensure the pump is level and aligned properly to avoid any unnecessary strain on the connections.
- Consider using vibration-damping materials or rubber mounts to absorb engine vibrations, especially if the pump is installed in a location that is prone to movement. This step is essential to prevent excessive wear and tear on the pump and fuel lines.
Connecting Fuel Lines:
- Identify the fuel inlet and outlet ports on the pump. These ports will be connected to the fuel lines, which will carry the fuel from the tank to the pump and then to the engine.
- Cut the fuel lines to the appropriate length, ensuring a few extra inches for flexibility and ease of installation. Strip the insulation from the ends of the lines using a line cutter or a utility knife.
- Connect the fuel lines to the pump's inlet and outlet ports using fuel line connectors or clamps. Tighten the connections securely, but be careful not to overtighten, as this can cause damage to the lines. Ensure a tight seal to prevent any fuel leakage.
- Route the fuel lines through the engine bay, keeping them as straight and short as possible. Use fuel line brackets or ties to secure the lines and prevent them from coming loose or interfering with other components.
- Check for any signs of fuel leakage at each connection point. If any leaks are detected, tighten the connections or use thread seal tape to ensure a secure bond.
Remember, proper mounting and secure connections are vital to the pump's longevity and the overall fuel system's reliability. Always refer to the pump's manual for specific instructions and recommendations regarding mounting and fuel line connections.
Mastering Fuel Line Maintenance: A Step-by-Step Guide to Clearing Clogs
You may want to see also
Regulator Placement: Position the regulator near the pump for optimal performance
When setting up a fuel system with a mechanical pump and regulator, the placement of the regulator is a critical factor in ensuring optimal performance and efficiency. The ideal position for the regulator is directly adjacent to the fuel pump. This proximity is essential for several reasons. Firstly, it minimizes the length of the fuel lines, which reduces the potential for fuel pressure loss due to the inherent resistance of the lines. Longer lines can lead to decreased performance and increased fuel consumption, especially at higher engine speeds. By keeping the lines short, you maintain a more consistent and robust fuel supply.
Secondly, placing the regulator near the pump allows for better control over the fuel pressure. The regulator's primary function is to maintain a steady pressure within the fuel system, ensuring that the engine receives the correct amount of fuel at the right pressure. When the regulator is close to the pump, it can quickly respond to any pressure fluctuations, making real-time adjustments to keep the pressure stable. This is crucial for optimal engine performance, as it prevents issues like engine stalling, misfires, and reduced power output caused by improper fuel pressure.
Additionally, the physical proximity of the regulator to the pump simplifies the plumbing process. With the regulator nearby, you can route the fuel lines more efficiently, reducing the need for excessive bends and twists. This not only improves the overall aesthetics of the fuel system but also ensures that the lines are less prone to damage from vibrations or other mechanical stresses. A neat and well-organized plumbing layout can also make future maintenance and troubleshooting easier.
In summary, positioning the regulator near the fuel pump is a fundamental practice in fuel system plumbing. It ensures efficient fuel delivery, maintains optimal pressure, and simplifies the overall setup. By adhering to this placement guideline, you can achieve a well-performing and reliable fuel system for your mechanical pump and regulator application. Remember, the goal is to create a seamless and responsive fuel supply, and the regulator's placement is a key component in achieving that.
Unveiling the Mystery: What's in the Fuel Line to Reduce NOx Emissions?
You may want to see also
Line Routing: Route fuel lines away from heat sources and potential hazards
When plumbing fuel lines for a mechanical pump and regulator system, proper line routing is crucial to ensure the safety and efficiency of the fuel delivery. One of the most important considerations is to route the fuel lines away from heat sources and potential hazards. This practice helps prevent fuel line damage, reduces the risk of fuel leaks, and minimizes the chances of fire or explosion.
Heat sources, such as exhaust systems, engine compartments, and even nearby electrical wiring, can cause fuel lines to expand and contract rapidly, leading to potential damage. High temperatures can cause fuel lines to degrade over time, resulting in cracks or leaks. Additionally, fuel lines should be kept away from moving parts, such as gears and pulleys, to avoid damage and potential fuel contamination.
To ensure safe routing, it is recommended to follow these guidelines:
- Keep fuel lines at least 6 inches away from hot surfaces or components. This distance provides a safe buffer to prevent heat-related damage.
- Route fuel lines in a manner that avoids sharp bends or kinks. Sharp bends can restrict fuel flow and create stress points, leading to potential leaks.
- Use appropriate protective materials, such as heat shields or insulation, to shield fuel lines from direct contact with hot surfaces.
- Consider the location of potential hazards, such as under the vehicle or near the engine, and route the lines accordingly to avoid these areas.
In addition to heat sources, it is essential to be mindful of other potential hazards. For example, fuel lines should be kept away from sharp edges, protruding objects, or areas with high vibration. These factors can cause wear and tear on the fuel lines, leading to potential failures. Proper routing will also help in maintaining a neat and organized system, making future maintenance and troubleshooting easier.
By following these routing practices, you can ensure that your fuel lines are protected from various hazards, contributing to a reliable and safe fuel delivery system. Proper line routing is a critical aspect of plumbing fuel lines, and it should be given careful attention to ensure the long-term performance and safety of the mechanical pump and regulator setup.
Metallic Fuel Line Maintenance: A Step-by-Step Guide to Cleaning
You may want to see also
Testing and Adjustments: Test the system, adjust pressure, and fine-tune for efficiency
Once the fuel lines are plumbed and the mechanical pump and regulator are installed, it's crucial to thoroughly test and adjust the system to ensure optimal performance and safety. This process involves a series of steps to verify the functionality of the components and fine-tune the system for efficiency.
Initial Testing: Begin by starting the engine and allowing it to run. Monitor the fuel flow and pressure using a gauge connected to the regulator's outlet. The pressure should be within the specified range for your engine's requirements. Check for any leaks at the connections and ensure that the pump operates smoothly without any unusual noises. This initial test will give you a baseline understanding of the system's performance.
Pressure Adjustment: If the initial test reveals pressure fluctuations or inconsistencies, adjustments are necessary. Locate the pressure-regulating valve, often found near the regulator. Use a screwdriver or an appropriate tool to turn the valve clockwise to increase pressure or counterclockwise to decrease it. Make small adjustments and retest the system after each change. The goal is to find the optimal pressure setting that ensures a steady fuel supply without causing excessive wear on the engine components.
Fine-Tuning for Efficiency: After achieving the correct pressure, focus on fine-tuning the system for efficiency. This step may require some trial and error. Check the fuel flow rate and ensure it matches the engine's requirements. Adjust the pump's speed if possible, as a faster pump might improve efficiency but could also lead to increased noise and wear. Consider using a fuel filter to further refine the fuel quality and potentially enhance engine performance. Regularly clean or replace the filter to maintain optimal efficiency.
Safety Checks: Throughout the testing and adjustment process, prioritize safety. Ensure that all connections are secure and tight to prevent fuel leaks. Verify that the fuel lines are not damaged or kinked, as this can restrict flow and cause pressure issues. Regularly inspect the system for any signs of wear or damage, especially after prolonged use or exposure to harsh conditions.
By following these testing and adjustment procedures, you can ensure that your fuel system is reliable, efficient, and safe for your mechanical pump and regulator setup. Regular maintenance and monitoring will also contribute to the long-term performance and longevity of your engine.
Mastering the Art of Removing Fuel Line Fittings: Tips and Tricks
You may want to see also
Frequently asked questions
To begin the plumbing process, you will require a set of tools including a wrench, pliers, a fuel line cutter, and a fuel filter. Additionally, you'll need the appropriate fuel lines, fittings, and a mechanical pump with a regulator. Ensure you have the correct sizes and types of components for your specific application.
Start by mounting the pump securely, ensuring it is level and aligned with the fuel source. Connect the inlet line from the pump to the fuel tank using a suitable fitting. Then, route the outlet line from the pump to the regulator, allowing for a slight bend to avoid sharp angles. Securely fasten the regulator to the fuel line, ensuring a tight connection. Finally, test the system for leaks and adjust the regulator settings according to the manufacturer's guidelines.
One common issue is fuel line leaks, which can be caused by improper connections or damaged lines. Check for tight fittings and replace any compromised fuel lines. Another problem is air bubbles in the system, leading to reduced flow or pump failure. Bleed the system by running the pump and opening the fuel line to release any trapped air. If the pump doesn't prime, ensure it is primed correctly and check for any blockages in the lines. Regular maintenance and inspection can help prevent and identify potential issues.