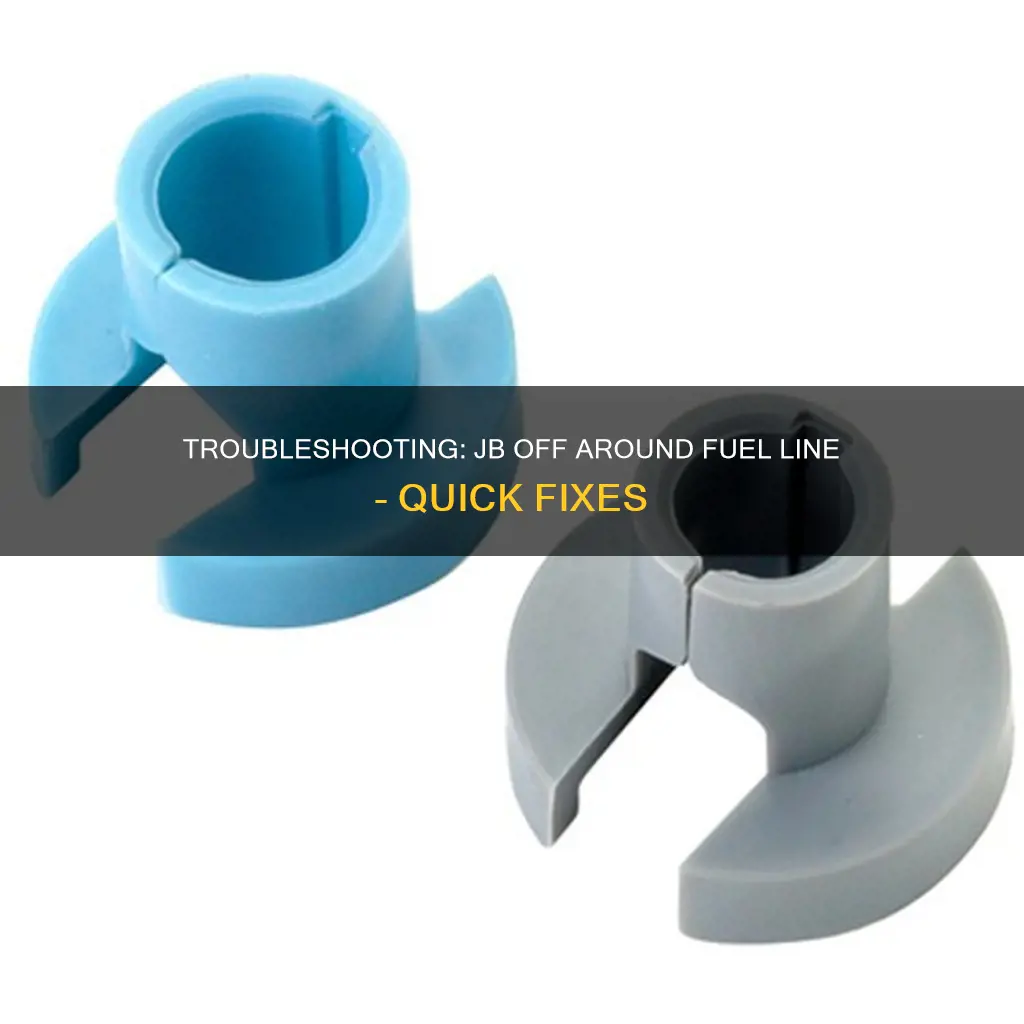
If you're dealing with a stubborn JB (presumably referring to a specific component or issue related to a vehicle or machinery) that's causing problems around the fuel line, it's important to approach the problem methodically. Start by identifying the exact cause of the issue, whether it's a blockage, a leak, or a malfunction. Then, gather the necessary tools and materials, such as a fuel line cleaner, a replacement part if needed, and a reliable method for testing the fuel line. Carefully inspect the fuel line for any visible damage or obstructions, and use appropriate techniques to clear any blockages or remove debris. If the problem persists, consider consulting a professional mechanic who can provide expert advice and ensure the issue is resolved safely and effectively.
What You'll Learn
Identify the exact location of the JB weld or clamp around the fuel line
To effectively remove a JB weld or clamp from around a fuel line, it's crucial to first identify the precise location of the repair. This step is essential to ensure you don't cause further damage to the fuel line or other components during the removal process. Here's a detailed guide on how to pinpoint the exact spot:
- Inspect the Fuel Line Route: Begin by thoroughly inspecting the fuel line's route throughout the vehicle. Fuel lines are typically located near the engine, running along the frame rails, and extending towards the fuel tank and various fuel-fed components. Look for any visible signs of damage, corrosion, or previous repairs. Identifying these areas can help you narrow down the potential location of the JB weld or clamp.
- Check for Access Points: Locate the access points to the fuel line. These are usually located near the engine bay, under the hood, or along the vehicle's underbody. Access points might include fuel line fittings, clamps, or other mounting hardware. Carefully examine these areas for any signs of a JB weld or clamp. Pay attention to the orientation and position of these components, as they may provide clues about the location of the repair.
- Use Diagnostic Tools (Optional): In some cases, you might consider using diagnostic tools like a fuel pressure gauge or a fuel line inspection camera. These tools can help you identify the exact point where the JB weld or clamp was applied. For instance, a fuel pressure gauge can help you locate the section of the fuel line where pressure drops, indicating a potential blockage or repair site.
- Refer to Vehicle Manual: Consult your vehicle's owner's manual, as it often includes detailed diagrams of the fuel system. These diagrams can provide valuable insights into the layout and positioning of the fuel lines, fittings, and potential access points. Look for illustrations that show the fuel line's path and any identified repair locations.
- Remove Excessive Clamps or Welds: Once you've identified the exact location, carefully remove any excessive clamps or JB welds that are not necessary for the repair. This step ensures that you're not causing unnecessary damage to the fuel line during the removal process. Use the appropriate tools, such as a clamp removal tool or a carefully applied heat source, to avoid damaging the fuel line.
By following these steps, you can accurately identify the location of the JB weld or clamp around the fuel line, setting the stage for a successful and safe removal process.
Exploring the Potential of Linear Work as Fuel Line
You may want to see also
Use a fuel line cutter to carefully remove the JB weld
If you're dealing with a stubborn JB Weld repair around a fuel line and need to remove it, using a fuel line cutter can be an effective method. Here's a step-by-step guide to help you through the process:
Start by ensuring you have the right tools for the job. A fuel line cutter is specifically designed to cut through fuel lines without causing damage. It's important to use a tool that is appropriate for the diameter of your fuel line to ensure a clean and precise cut. You can find these tools at automotive supply stores or online.
Before you begin, make sure the engine is off and the vehicle is in a stable position. This is crucial for safety and to avoid any accidental fuel leaks. Locate the JB Weld repair area, ensuring you can access the fuel line without causing any damage to other components.
Now, carefully position the fuel line cutter along the fuel line, just above the JB Weld. Apply firm pressure and make a clean cut through the fuel line. Take your time to ensure you don't cut too deep, as this could lead to further complications. The goal is to remove the JB Weld without affecting the surrounding fuel line.
Once the fuel line is cut, you'll have access to the JB Weld. Carefully remove the excess material, ensuring you don't damage the fuel line further. You might need to use a small wire brush or a similar tool to gently scrub away the JB Weld. Be thorough but gentle to avoid any potential damage.
After removing the JB Weld, inspect the fuel line for any signs of damage. If there are any small tears or imperfections, consider replacing the section of the fuel line to ensure optimal performance and safety. Properly dispose of the removed JB Weld and fuel line section, following local regulations for waste disposal.
Fitting the Right Fuel Line: 1979 F150 Fuel Line Size Guide
You may want to see also
Clean the area thoroughly to ensure no residue remains
To effectively remove JB Weld (a two-part epoxy adhesive) from around a fuel line, it's crucial to start by thoroughly cleaning the area. This step is essential to ensure that no residue remains, which could potentially cause further issues or contamination. Here's a detailed guide on how to achieve this:
Step 1: Gather the Right Tools and Materials
Before you begin, ensure you have the necessary tools and materials. You'll need a sharp blade or a thin tool to carefully scrape off any remaining JB Weld. Additionally, have a high-quality solvent or cleaner specifically designed for removing adhesives. Some effective options include acetone, isopropyl alcohol, or a specialized adhesive remover.
Step 2: Scrape Off Excess JB Weld
Carefully inspect the area around the fuel line where the JB Weld was applied. Use the sharp blade or tool to gently scrape off any excess JB Weld that has hardened and dried. Be meticulous and patient to avoid damaging the fuel line or surrounding components. Work in small sections to ensure you don't miss any residue.
Step 3: Apply the Solvent
Once you've removed as much JB Weld as possible, it's time to clean the area. Apply a generous amount of the chosen solvent to a clean cloth or rag. Rub the cloth over the affected area, ensuring that the solvent comes into contact with any remaining residue. Allow the solvent to sit for a few minutes to soften and dissolve the adhesive.
Step 4: Scrub and Rinse
After the solvent has had time to work, use a brush or a clean cloth to scrub the area thoroughly. This step helps to lift any remaining JB Weld particles. Rinse the area with clean water to remove the solvent and any dissolved adhesive. Ensure that all traces of the solvent and JB Weld are washed away.
Step 5: Dry and Inspect
Allow the area to dry completely. Once dry, inspect the region to ensure that no JB Weld residue remains. If any residue is still present, repeat the cleaning process until it is fully removed. Thorough cleaning is vital to prevent any potential issues with the fuel line's functionality and to maintain a clean and safe environment.
Mastering the Art of Fuel Line Removal: A Guide for 2000 GMC Jimmy Owners
You may want to see also
Apply a suitable adhesive or epoxy to secure the fuel line
To effectively address the issue of JB Weld or similar temporary adhesives around a fuel line, it's crucial to use a suitable adhesive or epoxy that can securely bond to the fuel line material without compromising its integrity. Here's a step-by-step guide on how to achieve this:
Step 1: Choose the Right Adhesive or Epoxy
Select an adhesive or epoxy specifically designed for fuel line applications. These products are formulated to withstand the corrosive effects of fuel and the high temperatures encountered in engine compartments. Look for adhesives that are compatible with the material of your fuel line, such as rubber or plastic.
Step 2: Clean the Fuel Line
Before applying the adhesive, ensure the fuel line is clean and free of any debris, old adhesive residue, or contaminants. Use a mild detergent or a specialized fuel line cleaner to remove any existing adhesive. Rinse the fuel line thoroughly with water to eliminate any cleaning agent residue.
Step 3: Prepare the Adhesive Application
Follow the manufacturer's instructions for preparing the adhesive. This may involve mixing two components, such as an activator and a resin, to create a strong bonding agent. Ensure you have the correct ratio and mix the components thoroughly to avoid weak bonding.
Step 4: Apply the Adhesive
Carefully apply the adhesive to the fuel line, focusing on the area where JB Weld was used. Apply a generous amount, ensuring complete coverage of the fuel line surface. Use a small brush or your fingers to spread the adhesive evenly, taking care not to get it on the surrounding components.
Step 5: Secure the Fuel Line
Once the adhesive is applied, allow it to set according to the manufacturer's instructions. This may involve waiting for a specified time or until the adhesive becomes tacky. During this time, handle the fuel line with care to avoid disturbing the adhesive. After the adhesive has set, reattach the fuel line to the engine or other components, ensuring it is securely fastened.
Step 6: Test and Verify
Start the engine and check for any leaks or unusual noises. Ensure that the fuel line is functioning properly and that the adhesive has successfully secured the fuel line. If any issues arise, carefully remove the adhesive and reapply it, following the same steps.
Remember, using a suitable adhesive or epoxy is crucial for a long-lasting repair. Always choose products specifically designed for fuel line applications to ensure the safety and reliability of your vehicle's fuel system.
Kawasaki Brute Force 750 Fuel Line Sizing Guide
You may want to see also
Test the fuel line for leaks and ensure proper functionality
Before you begin the process of removing JB Weld or any other epoxy-based adhesive from around the fuel line, it's crucial to ensure that the fuel line is in good condition and functioning properly. Testing for leaks and verifying the fuel line's functionality is an essential step to prevent any potential issues during the removal process. Here's a detailed guide on how to approach this task:
Step 1: Visual Inspection
Start by visually inspecting the fuel line for any visible signs of damage, cracks, or leaks. Look for any discolored or softened areas along the length of the fuel line, as these could indicate potential issues. Pay close attention to the connections and fittings, as these are common areas where leaks can occur. If you notice any damage, it's best to address it before proceeding with the removal process.
Step 2: Pressure Test
Perform a pressure test to check for leaks in the fuel line. This is a critical step to ensure the integrity of the fuel system. Here's how you can do it:
- Locate the fuel pump and the fuel tank.
- Disconnect the fuel line from the fuel pump and temporarily block the return line to prevent fuel from flowing back into the tank.
- Attach a pressure gauge to the fuel line and pump air into the line to create pressure.
- Observe the gauge for any drops in pressure, which could indicate a leak.
- If a leak is detected, identify the source and address it before continuing.
Step 3: Functionality Check
Ensure that the fuel line is functioning correctly by testing the fuel flow. Here's the process:
- Reconnect the fuel line to the fuel pump and ensure it is properly secured.
- Start the vehicle's engine and allow it to idle.
- Check for any unusual noises or vibrations coming from the fuel line or engine.
- Monitor the fuel gauge to ensure it is functioning correctly and accurately reflecting the fuel level.
- If the fuel line is not functioning properly, it may be necessary to replace it to prevent further issues.
Step 4: Use a Leak Detection Fluid
For a more comprehensive test, consider using a leak detection fluid specifically designed for fuel lines. This fluid will help identify even small leaks that might not be visible to the naked eye. Here's how to use it:
- Purchase a leak detection fluid from an automotive supply store.
- Disconnect the fuel line from the fuel pump and temporarily block the return line.
- Inject the leak detection fluid into the fuel line according to the manufacturer's instructions.
- Reattach the fuel line and start the engine.
- Observe the fluid for any changes in color or the appearance of bubbles, indicating a leak.
- If a leak is found, pinpoint the source and take the necessary steps to fix it.
By following these steps, you can ensure that the fuel line is in optimal condition before attempting to remove any adhesive. This thorough approach helps prevent potential fuel system issues and ensures a safe and effective removal process. Remember, proper testing and maintenance are key to keeping your vehicle's fuel system reliable and efficient.
Fixing Fuel Lines: A Guide to Replacing Aluminum Hose with Rubber
You may want to see also
Frequently asked questions
Removing JB Weld from a fuel line requires caution to avoid any fuel leaks. Start by applying heat to the JB Weld using a heat gun or hairdryer to soften the material. Once softened, carefully scrape away the JB Weld using a sharp tool, being mindful of the fuel line. Ensure you have a clean and dry work area to prevent any contamination.
While solvents can be effective, they may also damage the fuel line or leave residue. It's best to avoid solvents unless specifically recommended for the fuel line material. Instead, focus on heat-based methods or seek professional assistance for a safe and efficient removal process.
The tools required depend on the specific situation. For small areas, a sharp knife or razor blade can be used to carefully cut away the JB Weld. For larger or more stubborn deposits, a heat gun or hairdryer, along with a scraper, will be more effective. Always prioritize safety and consider wearing protective gear.
Reusing the fuel line depends on its condition after the removal process. If the fuel line is damaged or shows signs of deterioration during the removal, it might be best to replace it. Always inspect the fuel line for any cracks or damage before reuse to ensure it functions safely.
Yes, consider using temporary adhesives or sealants specifically designed for fuel lines. These alternatives are often easier to remove and may provide a more flexible solution. Always choose products that are compatible with the fuel line material and follow the manufacturer's instructions for safe application and removal.