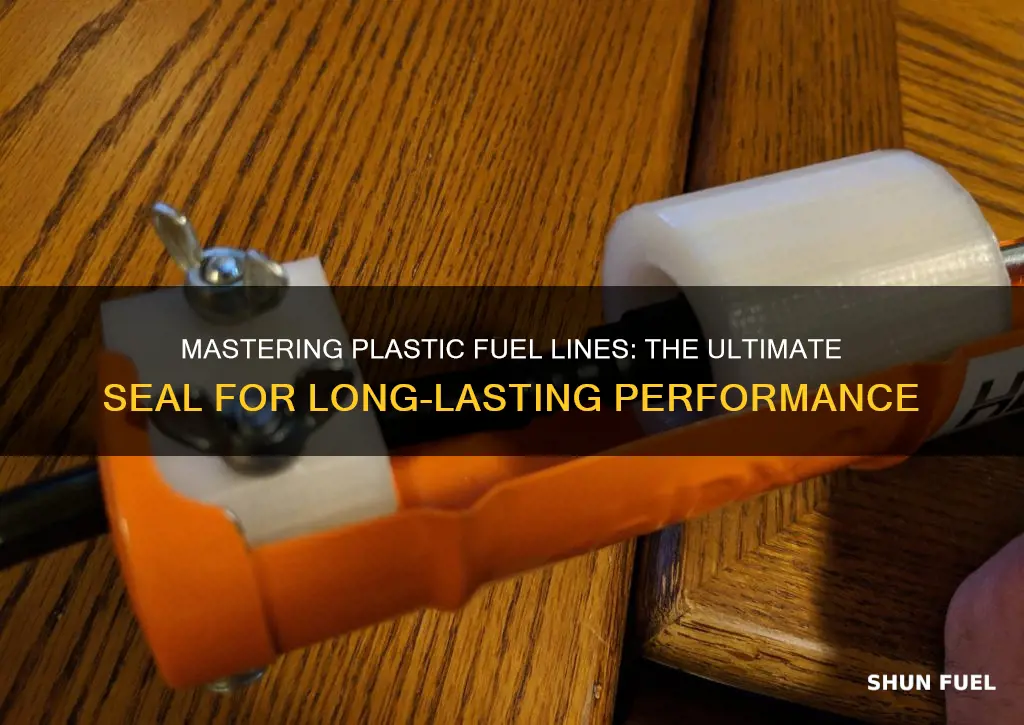
Will seal all work on plastic fuel lines is a crucial concept in the maintenance and repair of vehicles, especially those with fuel systems that utilize plastic lines. This process involves ensuring that any leaks or damage in the plastic fuel lines are effectively sealed to prevent fuel leaks, which can be dangerous and cause engine performance issues. The procedure typically includes identifying the source of the leak, cleaning the affected area, and applying an appropriate sealant or adhesive to create a secure and long-lasting repair. Properly sealing these lines is essential for vehicle safety and optimal engine operation.
Characteristics | Values |
---|---|
Brand | Various (e.g., Seal All, 3M, Loctite) |
Material | Plastic (fuel line) |
Application | Fuel lines, hoses, and connections |
Purpose | Sealing and repairing leaks |
Benefits | Waterproof, chemical-resistant, flexible |
Usage | Automotive, marine, and industrial |
Advantages | Easy to apply, quick-drying, long-lasting |
Compatibility | Most plastic fuel lines and hoses |
Color | Clear or translucent |
Package Size | Varies (e.g., 4 oz, 8 oz, 16 oz) |
Storage Life | Typically 2-5 years |
Application Temperature | Varies (e.g., -40°F to 250°F) |
Application Method | Brush, syringe, or spray |
Environmental Impact | Some products may be less environmentally friendly |
Regulatory Compliance | Meets industry standards |
What You'll Learn
- Material Compatibility: Ensure the sealant is compatible with plastic fuel lines to prevent damage
- Temperature Resistance: Choose a sealant that can withstand fuel line temperatures without degradation
- Flexibility: Select a flexible sealant to accommodate movement and prevent cracking
- Chemical Resistance: Opt for a sealant resistant to fuel chemicals to avoid corrosion
- Durability: Use a durable sealant for long-lasting protection against fuel line leaks
Material Compatibility: Ensure the sealant is compatible with plastic fuel lines to prevent damage
When it comes to sealing plastic fuel lines, material compatibility is a critical factor to ensure the longevity and reliability of your vehicle's fuel system. Plastic fuel lines are commonly used in modern vehicles due to their flexibility and lightweight nature, making them an ideal choice for fuel delivery. However, the choice of sealant is crucial to prevent any potential damage to these lines.
The primary concern with sealing plastic fuel lines is the risk of chemical degradation. Many sealants contain solvents or chemicals that can react with the plastic material, leading to softening, swelling, or even cracking of the fuel lines. This can result in fuel leaks, reduced performance, and potential safety hazards. Therefore, it is essential to select a sealant specifically designed for plastic fuel lines.
Look for sealants that are labeled as compatible with plastic materials, such as polyethene or polypropylene, which are commonly used in fuel lines. These sealants are formulated to adhere to the plastic surface without causing any adverse reactions. They create a strong bond that can withstand the internal fuel pressure and environmental conditions, ensuring a reliable seal.
Additionally, consider the temperature range and operating conditions of your vehicle. Some sealants are designed to withstand extreme temperatures, ensuring they remain effective in both hot and cold climates. This is particularly important for vehicles used in diverse weather conditions.
In summary, when sealing plastic fuel lines, always prioritize material compatibility. Choose a sealant specifically formulated for plastic fuel lines to avoid any potential damage. By selecting the right sealant, you can ensure a secure and long-lasting seal, contributing to the overall performance and safety of your vehicle's fuel system. Remember, proper preparation and the use of compatible materials are key to a successful and reliable fuel line repair or installation.
Finding the Perfect Fuel Line Size for Your Kubota
You may want to see also
Temperature Resistance: Choose a sealant that can withstand fuel line temperatures without degradation
When it comes to sealing plastic fuel lines, temperature resistance is a critical factor to consider. Fuel lines are exposed to a range of temperatures, from extreme cold during winter to high heat generated by the engine. Therefore, the chosen sealant must be able to withstand these varying conditions without compromising its effectiveness.
The primary goal is to ensure that the sealant maintains its integrity and continues to provide a secure seal, even when exposed to fuel's high temperatures. This is essential to prevent fuel leaks, which can lead to dangerous situations and potential engine damage.
One way to assess temperature resistance is by checking the sealant's service temperature range. Reputable manufacturers often provide this information, indicating the minimum and maximum temperatures at which the sealant remains effective. It is crucial to select a sealant that falls within the temperature range of your fuel lines' operating environment. For instance, if your fuel lines are subjected to temperatures below freezing, opt for a sealant designed for sub-zero conditions.
Additionally, consider the type of fuel your vehicle uses. Different fuels have varying boiling points and temperatures at which they can cause damage. For instance, ethanol-blended fuels may require a sealant with higher temperature resistance to prevent degradation. Always refer to the manufacturer's guidelines and choose a sealant that is specifically formulated for the type of fuel your vehicle uses.
In summary, when selecting a sealant for plastic fuel lines, temperature resistance is a key consideration. Ensure that the chosen sealant can withstand the specific temperature conditions your fuel lines encounter, whether it's extreme cold or high heat. By doing so, you guarantee a reliable and long-lasting seal, minimizing the risk of fuel leaks and potential engine issues.
Choosing the Right U.S. Coast Guard-Approved Fuel Line for Ocean Outboards
You may want to see also
Flexibility: Select a flexible sealant to accommodate movement and prevent cracking
When it comes to sealing plastic fuel lines, flexibility is a critical factor to ensure the longevity and reliability of the repair. Plastic fuel lines are inherently prone to movement due to engine vibrations, temperature changes, and the natural flexing of the vehicle's structure. Therefore, choosing a sealant that can accommodate this movement is essential to prevent cracking and potential fuel leaks.
The key to achieving flexibility in a sealant lies in the material composition. Look for sealants that contain elastic polymers or rubber-like compounds. These materials have the ability to stretch and return to their original shape, allowing them to move with the fuel lines without causing damage. Silicone-based sealants are an excellent choice for this application, as they offer superior flexibility and resistance to temperature variations.
During the selection process, consider the specific requirements of your project. If the fuel lines are subject to extreme temperatures or high-vibration environments, opt for a sealant with enhanced flexibility. Some manufacturers offer specialized sealants designed explicitly for fuel line applications, ensuring compatibility and optimal performance.
Application techniques also play a role in achieving flexibility. When applying the sealant, ensure that the surface is clean and free of debris. Follow the manufacturer's instructions for proper preparation and application methods. By doing so, you create a strong bond between the sealant and the fuel line, allowing for better flexibility and adhesion.
In summary, flexibility is a crucial aspect of sealing plastic fuel lines. By choosing a flexible sealant, you can accommodate the natural movement of the fuel lines, prevent cracking, and ensure a reliable seal. Remember to consider the material composition, specific project requirements, and application techniques to achieve the best results. With the right sealant, you can protect your fuel system and maintain the overall integrity of your vehicle.
Nissan Maxima Fuel Line: Location Guide for 2007 Models
You may want to see also
Chemical Resistance: Opt for a sealant resistant to fuel chemicals to avoid corrosion
When dealing with plastic fuel lines, ensuring the integrity and longevity of the system is paramount. One critical aspect often overlooked is the choice of sealant used to seal any repairs or connections. The primary concern here is chemical resistance, especially when it comes to the chemicals present in fuel.
Fuel, particularly gasoline and diesel, contains various additives and solvents that can be corrosive to certain materials. Over time, these chemicals can degrade the plastic fuel lines, leading to cracks, leaks, and ultimately, system failure. Therefore, selecting a sealant that is resistant to these fuel chemicals is essential to prevent corrosion and ensure the long-term reliability of the fuel system.
The key to achieving this is to choose a sealant specifically formulated to withstand the harsh environment of fuel. Look for sealants that are designed to be compatible with the type of fuel used in your vehicle. For example, gasoline-based sealants should be avoided for diesel applications, as the solvents in diesel can dissolve certain types of sealants, leading to reduced performance and potential damage.
Opting for a sealant with excellent chemical resistance ensures that it can form a robust and durable bond in the presence of fuel. This resistance is crucial, especially in high-temperature environments where fuel can accelerate the degradation of less resistant materials. A suitable sealant will not only prevent corrosion but also maintain the structural integrity of the sealed area, ensuring a leak-free and efficient fuel system.
In summary, when sealing any work on plastic fuel lines, prioritizing chemical resistance is vital. By selecting a sealant that can withstand the corrosive effects of fuel, you can significantly extend the lifespan of the fuel system and avoid costly repairs or replacements. This simple yet critical choice will contribute to the overall reliability and performance of your vehicle's fuel delivery system.
Unveiling the Car Fuel Line: Visual Guide
You may want to see also
Durability: Use a durable sealant for long-lasting protection against fuel line leaks
When it comes to sealing and protecting plastic fuel lines, durability is key. Plastic fuel lines are susceptible to leaks and damage over time due to their material properties and exposure to harsh environments. To ensure long-lasting protection, it is crucial to use a high-quality, durable sealant specifically designed for this purpose.
The primary goal of sealing a plastic fuel line is to create an airtight barrier that prevents fuel from leaking out and potential contaminants from entering the system. A durable sealant achieves this by forming a strong, flexible bond with the plastic material, providing a reliable seal that can withstand various stresses and conditions. Look for sealants that are specifically formulated for plastic applications, as they will have the necessary properties to adhere to and protect the fuel line effectively.
One important factor to consider is the flexibility of the sealant. Plastic fuel lines often experience movement and vibration, especially during vehicle operation. A durable sealant should be able to accommodate these movements without cracking or peeling, ensuring a long-lasting seal. Choose a sealant that offers excellent flexibility and has a wide operating temperature range to handle the varying conditions your vehicle may encounter.
Additionally, the sealant's resistance to fuel chemicals is vital. Fuel contains various additives and solvents that can degrade some sealants over time. Opt for a sealant that is specifically formulated to resist the chemicals present in fuel, ensuring its longevity and effectiveness. This will provide reliable protection against fuel leaks and potential engine damage.
In summary, when sealing plastic fuel lines, prioritize durability to ensure long-term protection. Select a sealant that is designed for plastic applications, offering flexibility, chemical resistance, and the ability to withstand the rigors of vehicle operation. By using a high-quality, durable sealant, you can effectively prevent fuel line leaks and maintain the integrity of your vehicle's fuel system. Remember, proper sealing is a critical aspect of vehicle maintenance, and investing in the right materials will pay off in the long run.
Unveiling the 1967 Ford LTD's Fuel Line Route
You may want to see also
Frequently asked questions
A seal is crucial for any fuel line, including those made of plastic, as it ensures a tight and secure connection. This prevents fuel leaks, which can be dangerous and cause environmental damage. The seal also helps to maintain the integrity of the fuel system, ensuring that fuel is delivered efficiently to the engine.
Over time, seals can wear out due to fuel exposure, temperature changes, or physical damage. Signs of a failing seal include fuel leaks, reduced engine performance, or strange noises from the fuel system. If you notice any of these issues, it's essential to inspect the fuel line and replace the seal if necessary to prevent further damage.
While some basic fuel line maintenance can be done by car owners, replacing a seal requires specific knowledge and tools. It's recommended to consult a professional mechanic or a fuel system specialist to ensure the job is done correctly. They have the expertise to identify the right seal for your vehicle and the necessary skills to install it without causing further issues.