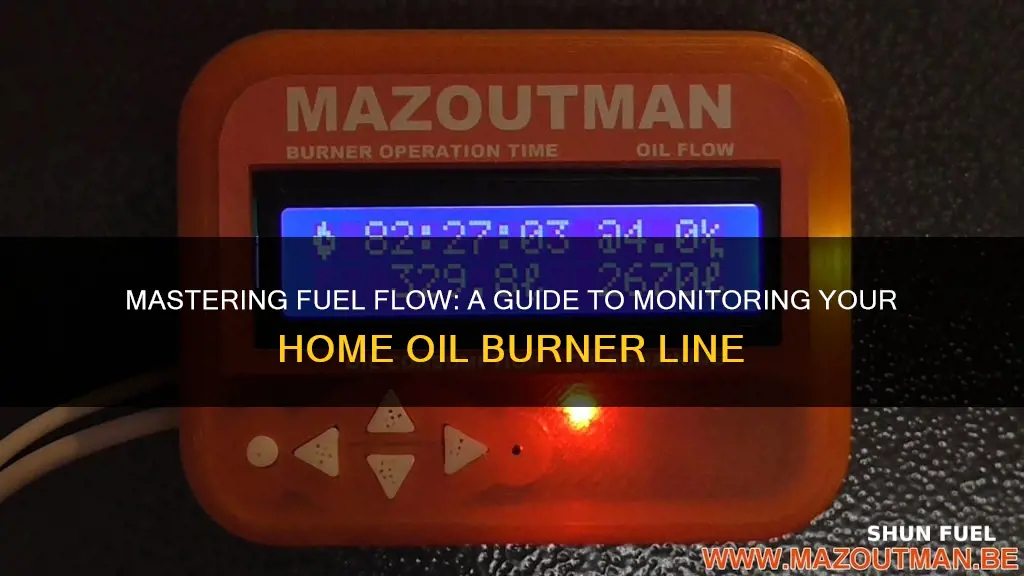
Monitoring fuel flow in a home oil burner line is a crucial aspect of maintaining a safe and efficient heating system. This process involves ensuring that the correct amount of oil is delivered to the burner, which is essential for optimal performance and energy efficiency. By implementing a monitoring system, homeowners can detect any issues with the fuel supply, such as blockages, leaks, or pressure fluctuations, allowing for prompt repairs and preventing potential breakdowns. This guide will provide an overview of the methods and tools available to effectively monitor fuel flow, ensuring the longevity and reliability of your home's heating system.
What You'll Learn
- Flow Meters: Use devices to measure fuel flow rate accurately
- Pressure Gauges: Monitor pressure to ensure optimal combustion
- Temperature Sensors: Detect temperature changes affecting fuel viscosity
- Flow Switches: Trigger alarms if flow rate drops or fluctuates
- Visual Inspection: Regularly check for blockages or leaks
Flow Meters: Use devices to measure fuel flow rate accurately
Flow meters are essential tools for monitoring and managing fuel flow in home oil burner systems. These devices provide accurate measurements of the fuel's flow rate, ensuring optimal performance and efficiency. By installing flow meters, homeowners can gain valuable insights into their oil burner's operation, leading to better energy management and cost savings.
When it comes to choosing the right flow meter, there are several options available. One common type is the positive displacement flow meter, which measures the volume of fuel passing through a pipe by using a rotating mechanism. This method is highly accurate and suitable for residential applications. Another popular choice is the turbine flow meter, which utilizes the rotation of a turbine blade proportional to the fluid's velocity, offering precise measurements.
Installation of flow meters is a relatively straightforward process. It typically involves connecting the meter to the fuel line between the oil tank and the burner. This placement allows for real-time monitoring of the fuel's flow rate. Homeowners should ensure that the flow meter is properly calibrated and aligned with the system's specifications to obtain accurate readings. Regular maintenance and cleaning of the flow meter are also crucial to prevent any blockages or inaccuracies.
The data provided by flow meters is invaluable for several reasons. Firstly, it helps identify any leaks or blockages in the fuel line, allowing for prompt repairs and preventing potential safety hazards. Secondly, monitoring fuel flow rate can optimize the burner's performance, ensuring efficient combustion and reducing energy waste. Additionally, homeowners can track their fuel consumption patterns, enabling better budgeting and cost control.
In summary, flow meters are powerful tools for monitoring fuel flow in home oil burner systems. With their ability to provide accurate measurements, they empower homeowners to make informed decisions regarding their energy usage. By investing in flow meters and regularly analyzing the data, individuals can enhance the efficiency of their oil burner, reduce energy costs, and contribute to a more sustainable and environmentally friendly home.
Choosing the Right Rubber for Your Fuel Line: A Guide
You may want to see also
Pressure Gauges: Monitor pressure to ensure optimal combustion
Monitoring the pressure in your home oil burner system is a critical aspect of ensuring efficient and safe operation. Pressure gauges play a vital role in this process, providing real-time data that helps you maintain optimal combustion conditions. Here's a detailed guide on how to utilize pressure gauges for effective monitoring:
Understanding Pressure in Oil Burner Systems: In an oil burner system, pressure is a key factor that influences the combustion process. The fuel oil must be delivered at the right pressure to ensure complete burning, which maximizes efficiency and minimizes emissions. Low pressure can lead to poor combustion, resulting in inefficient heating and potential safety hazards. Conversely, excessive pressure can cause issues like fuel spray nozzles becoming clogged or damaged.
Types of Pressure Gauges: When it comes to monitoring pressure, you have several options for pressure gauges: mechanical, electronic, and smart gauges. Mechanical pressure gauges, often analog devices, are simple and reliable. They provide a visual indication of pressure through a needle movement. Electronic pressure gauges offer digital readouts and can be connected to data logging systems for remote monitoring. Smart gauges, typically electronic, often feature advanced connectivity, allowing for real-time data transmission and remote control capabilities.
Installation and Placement: Proper installation and placement of pressure gauges are essential for accurate readings. The gauge should be installed in a location that is easily accessible for regular maintenance and reading. It should be mounted securely to prevent accidental dislodging. Position the gauge where it can capture the pressure of the fuel oil as it enters the burner system. This might involve installing the gauge in a pipe or line that connects the fuel tank to the burner.
Setting Optimal Pressure Ranges: To ensure optimal combustion, you need to establish the ideal pressure ranges for your specific oil burner system. These ranges can vary depending on the make and model of your burner, as well as local climate conditions. Consult your oil burner's manual or seek guidance from a professional technician to determine the recommended pressure settings. Typically, a pressure gauge will have a red line or a specific value indicating the upper limit of safe pressure.
Regular Monitoring and Maintenance: Regularly monitoring the pressure with your gauge is essential. It's recommended to check the pressure at least once a month and more frequently if you notice any unusual behavior or during seasonal changes. Keep a record of the pressure readings to identify any trends or anomalies. Additionally, ensure that the gauge is calibrated regularly to maintain accuracy. Calibration kits are available for most types of pressure gauges, allowing you to perform self-calibration or seek professional calibration services.
By implementing a pressure gauge monitoring system, you can proactively manage your home oil burner's performance, ensuring efficient combustion, cost savings, and a safer heating environment. Remember, proper maintenance and regular checks are key to extending the lifespan of your oil burner system.
Mastering Hose Barb Outboard Fuel Line Measurement: A Comprehensive Guide
You may want to see also
Temperature Sensors: Detect temperature changes affecting fuel viscosity
Temperature sensors play a crucial role in monitoring fuel flow in home oil burner systems, especially when it comes to detecting temperature changes that can impact fuel viscosity. These sensors are designed to measure temperature variations, which is essential for maintaining optimal performance and safety. Here's how they work and why they are important:
Understanding Fuel Viscosity: Fuel viscosity refers to the thickness or resistance of the oil to flow. It is influenced by temperature; as temperature increases, fuel tends to become less viscous, allowing for easier flow. Conversely, at lower temperatures, fuel thickens, making it harder to pass through the burner system. This viscosity change can significantly impact the burner's efficiency and performance.
Temperature Sensor Placement: To effectively monitor fuel flow, temperature sensors should be strategically placed in the oil burner system. One common location is near the fuel filter, as this area is close to the fuel source and can provide valuable insights into the fuel's temperature. Additionally, sensors can be installed in the return line, where the used oil is directed back to the tank, to measure temperature changes during the fuel's journey through the system.
Detecting Temperature Fluctuations: The primary function of these sensors is to detect even minor temperature fluctuations. When the temperature drops, the fuel becomes more viscous, potentially leading to poor combustion and reduced efficiency. Temperature sensors trigger alerts or warnings when they sense a significant temperature drop, indicating a potential issue. This early detection allows homeowners to take prompt action, such as adjusting the thermostat or addressing insulation issues.
Benefits of Temperature Monitoring: Regular monitoring of temperature changes using sensors offers several advantages. Firstly, it helps prevent fuel system failures by identifying potential issues early on. For instance, if the temperature drops too low, the fuel can become too thick, causing blockages or inefficient burning. Secondly, temperature monitoring ensures the burner operates within optimal parameters, maximizing energy efficiency and reducing fuel consumption.
Maintenance and Calibration: Proper maintenance and calibration of temperature sensors are essential. Over time, sensors may drift or require adjustment to maintain accuracy. Regular calibration ensures that the sensors provide reliable data, allowing homeowners to make informed decisions regarding their oil burner system's performance.
By implementing temperature sensors and monitoring temperature changes, homeowners can effectively manage their oil burner systems, ensuring efficient fuel flow and optimal performance while minimizing the risk of potential issues related to fuel viscosity.
Choosing the Right Fuel Line for Effective Brake Bleeding
You may want to see also
Flow Switches: Trigger alarms if flow rate drops or fluctuates
Flow switches are an essential component in monitoring and ensuring the efficient operation of home oil burner systems. These devices are specifically designed to detect changes in the flow rate of the fuel, such as oil, and can trigger alarms if the flow rate drops or fluctuates unexpectedly. By implementing flow switches, homeowners can take proactive measures to address potential issues with their heating systems, ensuring optimal performance and safety.
The primary function of a flow switch is to monitor the continuous flow of oil through the burner line. It is typically installed in series with the oil pump and before the main filter. When the oil flows through the switch, it completes an electrical circuit, which is then monitored by the switch. Under normal operating conditions, the flow switch remains in a closed state, allowing the heating system to function as intended. However, if the flow rate drops or fluctuates, the switch detects this change and triggers an alarm.
These alarms serve as an early warning system, alerting homeowners to potential problems. A drop in flow rate could indicate a clogged filter, a malfunctioning pump, or even a blocked pipe. Fluctuations in flow might suggest issues with the oil pressure or the presence of air in the system. By promptly identifying these issues, homeowners can take immediate action to resolve them before they lead to more significant and costly problems. For example, a clogged filter can be replaced, and a malfunctioning pump may require professional repair or replacement.
Flow switches are particularly useful for older homes or systems where regular maintenance might be overlooked. They provide an additional layer of protection and peace of mind, ensuring that any deviations from the normal flow rate are quickly detected. Modern flow switches often come with advanced features, such as remote monitoring capabilities, allowing homeowners to receive alerts on their smartphones or computers, even when they are away from home. This real-time monitoring capability enables swift responses to potential issues.
In summary, flow switches are a critical tool for monitoring fuel flow in home oil burner systems. They provide an early warning system, alerting homeowners to potential problems caused by changes in flow rate. By promptly addressing these issues, homeowners can ensure the longevity and efficiency of their heating systems while also maintaining a safe and comfortable living environment. Regular maintenance and the use of flow switches can significantly contribute to the overall reliability and performance of home oil burner systems.
Rubber Fuel Line: A Viable Substitute for Vacuum Hose?
You may want to see also
Visual Inspection: Regularly check for blockages or leaks
Visual inspection is a crucial step in monitoring the fuel flow in your home oil burner system. It allows you to identify potential issues early on, ensuring efficient operation and preventing costly repairs. Here's a detailed guide on how to perform regular visual inspections to check for blockages or leaks:
Start by examining the fuel line for any visible signs of damage or deterioration. Look for cracks, punctures, or kinks in the pipe, especially where it connects to the burner and the oil tank. Over time, fuel lines can develop issues due to age, freezing temperatures, or physical damage from rodents or other pests. Inspect the line for any signs of wear and tear, ensuring it is intact and secure.
Pay close attention to the connections and fittings. Check for any loose or damaged parts, including valves, pipes, and filters. Leaks can occur at these points, leading to fuel wastage and potential safety hazards. If you notice any corrosion, rust, or discolouration around the fittings, it may indicate a potential issue. Ensure all connections are tight and secure, and consider using thread seal tape or pipe compound to reinforce the joints.
Look for any signs of fuel accumulation or pooling around the burner or nearby areas. This could indicate a blockage or malfunction in the fuel system. Check for any unusual stains or wet patches on the floor or walls, as these might suggest a leak. Keep an eye out for any strange noises, such as hissing or gurgling sounds, which could be a sign of fuel escaping.
Regularly inspect the burner itself for any visible blockages. Remove the burner's access panel and check for any debris, dirt, or clogs that might obstruct the fuel flow. Use a soft brush or compressed air to gently clean the burner and remove any built-up residue. Ensure that the burner is free from any obstructions that could disrupt the efficient combustion process.
In addition to visual cues, trust your senses. If you notice a strong odour of fuel or smoke, it could indicate a leak or malfunction. Any unusual sounds or changes in the burner's performance should also be addressed promptly. By combining visual inspections with your senses, you can quickly identify potential problems and take the necessary steps to maintain a healthy fuel flow in your home oil burner system.
Fuel Line for Your 96 Civic: A Guide to Finding the Right Fit
You may want to see also
Frequently asked questions
Monitoring fuel flow is crucial for ensuring the efficient and safe operation of an oil-fired heating system. It helps detect any issues with the fuel supply, such as blockages, leaks, or improper pressure, which can lead to reduced heating performance, increased fuel consumption, and potential safety hazards.
You can use a fuel flow meter, also known as a line flow meter or oil flow meter, specifically designed for oil-burning applications. These meters are typically installed in-line between the oil tank and the burner. They measure the volume of oil passing through the line and provide accurate flow rate data, allowing you to identify any abnormalities.
Here are a few indicators of potential fuel flow issues:
- No heat or insufficient heat: If the burner is not producing enough heat, it could be due to a restricted fuel flow, often caused by a clogged filter, faulty pump, or low oil pressure.
- Excessive fuel consumption: A sudden increase in fuel usage without a corresponding rise in heat output may suggest a leak or malfunction in the fuel system.
- Oil leaks: Any visible oil leaks around the burner, pipes, or connections should be addressed immediately, as they can lead to reduced fuel flow and potential safety risks.
It is recommended to regularly monitor fuel flow, especially during the heating season. Aim to check the flow at least once a month or whenever you notice a change in the system's performance. Additionally, after any maintenance or repairs to the oil burner or fuel system, it's essential to verify the fuel flow to ensure everything is functioning correctly.