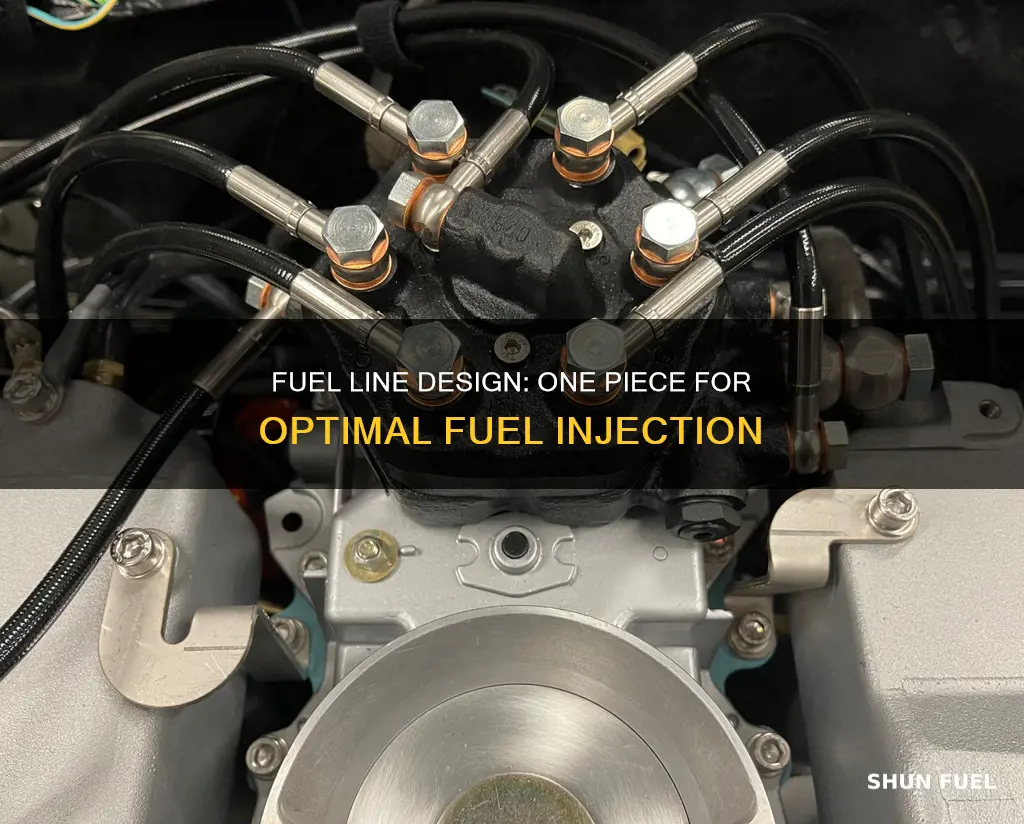
The design of fuel lines in fuel injection systems is a critical aspect of vehicle performance and reliability. One key consideration is whether a fuel line should be a single, continuous piece or consist of multiple segments. This decision impacts the system's efficiency, maintenance, and overall longevity. A one-piece fuel line offers several advantages, including improved fuel flow, reduced pressure drops, and enhanced system reliability due to the absence of connections that can leak or fail over time. However, it also presents challenges, such as increased complexity during installation and potential difficulties in replacing individual components if necessary. This paragraph introduces the debate on the merits and drawbacks of a single-piece fuel line in fuel injection systems, highlighting the importance of this design choice in optimizing vehicle performance and addressing potential maintenance concerns.
Characteristics | Values |
---|---|
Material | Plastic, metal (such as aluminum or stainless steel) |
Design | Single-piece or multi-piece |
Flexibility | Rigid or flexible |
Diameter | Varies depending on engine requirements |
Length | Customizable, typically 1-3 meters |
Compatibility | Specific to the vehicle's fuel injection system |
Durability | Resistant to heat, fuel degradation, and engine vibrations |
Installation | Easy to install, often requiring specialized tools |
Cost | Varies based on material, brand, and vehicle model |
Maintenance | Low maintenance, but regular checks for cracks or leaks are recommended |
What You'll Learn
- Design Considerations: One-piece fuel lines offer design simplicity, reducing potential leak points
- Performance Benefits: Single-piece lines can improve fuel flow, enhancing engine performance and efficiency
- Reliability: Fewer connections mean fewer potential failure points, increasing system reliability
- Maintenance: Easier to inspect and maintain, reducing downtime and repair costs
- Material Selection: Choosing appropriate materials is crucial for durability and compatibility with fuel
Design Considerations: One-piece fuel lines offer design simplicity, reducing potential leak points
When designing fuel injection systems, the choice of fuel line configuration is a critical aspect that can significantly impact the system's reliability and performance. One of the key considerations is whether to use a one-piece fuel line or multiple segments. This decision is not merely a matter of convenience but also a strategic design choice that can influence the overall efficiency and longevity of the system.
One-piece fuel lines, as the name suggests, are constructed as a single, continuous length of material. This design approach offers several advantages in terms of simplicity and reliability. Firstly, it eliminates the need for multiple connections or joints, which are common sources of potential leak points. By removing these interfaces, engineers can minimize the risk of fuel leakage, ensuring a more secure and efficient fuel supply to the engine. This is particularly crucial in high-performance applications where fuel efficiency and power output are maximized, and any leakage can lead to significant performance losses.
The design simplicity of one-piece fuel lines is a direct benefit of their construction. With fewer components, the assembly process becomes more straightforward, reducing the chances of human error during installation. This simplicity also translates to easier maintenance and troubleshooting, as there are fewer areas to inspect and potential failure points to consider. For instance, if a one-piece line develops a small puncture, it can be replaced as a whole, minimizing downtime and repair costs.
Furthermore, the use of one-piece fuel lines can enhance the overall aesthetics of the fuel injection system. With fewer components and a more streamlined design, the system appears more integrated and less cluttered. This is especially important in applications where space is at a premium, such as in high-performance racing cars or compact automotive designs.
In summary, one-piece fuel lines offer a compelling solution for fuel injection system design. Their ability to simplify the design, reduce potential leak points, and enhance overall system reliability makes them an attractive choice for engineers. While there may be considerations regarding material costs and initial setup complexity, the long-term benefits of improved performance and reduced maintenance make one-piece fuel lines a valuable asset in the world of fuel injection technology.
Unclogging Fuel Lines: Why a Flush is Necessary
You may want to see also
Performance Benefits: Single-piece lines can improve fuel flow, enhancing engine performance and efficiency
The concept of a single-piece fuel line for fuel injection systems has gained traction among automotive enthusiasts and engineers, and for good reason. One of the primary performance benefits of this design is the potential for improved fuel flow, which can have a significant impact on engine efficiency and overall power output.
In traditional fuel injection systems, the fuel line is often a separate component, consisting of multiple sections connected to deliver fuel from the tank to the engine. These connections can introduce various inefficiencies. For instance, the joints and bends in the line can restrict the smooth flow of fuel, leading to potential pressure drops and inconsistent fuel delivery. This is especially critical in high-performance engines where precise and rapid fuel injection is essential for optimal power generation.
A single-piece fuel line, on the other hand, offers a seamless path for fuel to travel from the tank to the engine. This design eliminates the potential bottlenecks and pressure losses associated with multiple connections. By providing a continuous and unobstructed flow path, the single-piece line ensures that fuel reaches the engine at the optimal pressure and temperature, allowing for more efficient combustion. This results in improved engine performance, as the engine can extract more power from the same volume of fuel.
Furthermore, the absence of joints and connections in a single-piece line reduces the risk of fuel leaks or contamination. Over time, multiple connections can degrade, leading to fuel leaks that may cause engine misfires or reduced performance. With a single-piece line, the risk of such issues is minimized, ensuring a more reliable and consistent fuel supply to the engine. This reliability can be particularly advantageous in racing or high-performance driving scenarios where every second counts.
In summary, the adoption of a single-piece fuel line for fuel injection systems offers a compelling performance advantage by optimizing fuel flow. This design choice can lead to enhanced engine efficiency, improved power output, and a more reliable fuel delivery system. As such, it is a valuable consideration for engineers and enthusiasts looking to maximize the potential of their fuel-injected engines.
W124 400E Fuel Line: An6 or Not? Unraveling the Mystery
You may want to see also
Reliability: Fewer connections mean fewer potential failure points, increasing system reliability
The concept of a single, continuous fuel line for fuel injection systems is an intriguing one, and it primarily revolves around enhancing reliability and performance. When a fuel line is designed as a single piece, it significantly reduces the number of connections and joints within the system. This design approach has several advantages that contribute to the overall reliability of the fuel injection setup.
One of the key benefits is the elimination of potential failure points. In a traditional fuel line system, multiple connections are required to join various components, such as the fuel pump, filter, and injectors. Each connection is a potential weak link that could fail over time due to factors like corrosion, vibration, or improper installation. With a one-piece fuel line, these connections are removed, reducing the chances of leaks, blockages, or system malfunctions. This simplicity in design makes it less prone to developing issues related to connections, ensuring a more reliable fuel supply to the engine.
Furthermore, a single fuel line can improve the overall efficiency of the fuel injection system. By removing the need for multiple connections, the system becomes less complex, and the risk of contamination or fuel degradation is minimized. Fuel lines, especially those with multiple joints, can sometimes act as pathways for air to enter the system, leading to issues like fuel vaporization and reduced performance. A continuous fuel line design mitigates this risk, ensuring that the fuel remains fresh and pressurized until it reaches the injectors.
In addition to reliability, a one-piece fuel line can also contribute to better fuel management and control. With fewer connections, the system becomes more responsive and efficient in delivering fuel to the engine. This is particularly important in high-performance applications where precise fuel injection timing is crucial. A continuous fuel line allows for more accurate fuel delivery, ensuring that the engine receives the exact amount of fuel required for optimal performance and combustion.
In summary, the idea of a single fuel line for fuel injection systems is a design philosophy that prioritizes reliability and performance. By minimizing connections, this approach reduces potential failure points, improves fuel efficiency, and enhances overall system responsiveness. While it may require careful consideration of material choices and installation techniques, the benefits of a one-piece fuel line can significantly contribute to a more dependable and efficient fuel injection setup.
Unkinking Fuel Lines: A Step-by-Step Guide to Smooth Operation
You may want to see also
Maintenance: Easier to inspect and maintain, reducing downtime and repair costs
The concept of a single-piece fuel line for fuel injection systems has gained traction in recent years, and for good reason. One of the most significant advantages of this design is the ease of maintenance it offers. With a one-piece fuel line, the inspection and maintenance process becomes significantly simpler, leading to reduced downtime and lower repair costs.
Traditional fuel lines often consist of multiple components, including various fittings, hoses, and clamps, which can make inspections and repairs time-consuming and complex. In contrast, a single-piece fuel line is just that—a continuous, seamless tube that runs from the fuel tank to the engine. This design simplifies the maintenance process by eliminating the need to disassemble multiple parts. Technicians can quickly inspect the entire line for any signs of damage, leaks, or wear without having to take the engine apart.
During routine maintenance checks, mechanics can easily identify potential issues such as cracks, punctures, or corrosion. The single-piece construction allows for a thorough visual inspection, ensuring that any problems are caught early. This simplicity in inspection translates to faster maintenance routines, reducing the time vehicles spend out of service. For example, a quick visual check can determine if the fuel line is intact, saving hours of diagnostic work that might be required with a multi-component system.
Furthermore, the ease of maintenance extends to the repair process. If a single-piece fuel line is damaged, it can often be replaced more efficiently. Technicians can quickly source and install a new line, minimizing the time required for repairs. This is particularly beneficial in high-volume repair shops or in situations where quick turnaround times are essential. The reduced complexity of the repair process can significantly lower labor costs and improve overall efficiency.
In summary, the one-piece fuel line design for fuel injection systems offers a practical solution to simplify maintenance and repair processes. By eliminating the need for multiple components, inspections and repairs become faster and more straightforward, leading to reduced downtime and lower maintenance costs. This approach not only benefits professional mechanics but also contributes to more efficient and cost-effective vehicle ownership for individual drivers.
Nylon Fuel Line Unions: Compatibility with Steel Lines
You may want to see also
Material Selection: Choosing appropriate materials is crucial for durability and compatibility with fuel
When it comes to fuel lines for fuel injection systems, material selection is a critical aspect that directly impacts the performance and longevity of the system. The primary goal is to ensure that the fuel lines are durable, compatible with the fuel, and capable of withstanding the high pressure and temperature variations associated with fuel injection. Here's a detailed look at the key considerations:
Durability and Flexibility: Fuel lines need to be robust and flexible to accommodate the dynamic nature of the fuel injection system. Materials like high-density polyethylene (HDPE) or reinforced rubber are often chosen for their ability to withstand repeated flexing and movement without cracking or deteriorating. These materials offer excellent resistance to fuel-related chemicals, ensuring the system's longevity.
Compatibility with Fuel: Different fuels have varying properties, and the chosen material must be compatible with the specific fuel type. For instance, ethanol-blended fuels require materials that can withstand the higher alcohol content without degradation. Materials like stainless steel or specialized polymers are often used for their inherent resistance to fuel-related corrosion and oxidation.
Pressure and Temperature Resistance: Fuel injection systems operate under high pressure and temperature conditions. Materials should be able to handle these extremes without compromising performance. For instance, silicone-based materials are popular for their ability to maintain flexibility and integrity under high temperatures and pressure. This ensures that the fuel lines remain effective even in demanding operating environments.
Chemical Resistance: Fuel lines must be resistant to the chemicals present in the fuel, especially in the case of ethanol-blended or synthetic fuels. Materials like HDPE or specialized fluoropolymers offer excellent chemical resistance, preventing fuel leakage and potential system failures.
Cost and Availability: Practical considerations also play a role in material selection. Some materials might offer superior performance but may be more expensive or less readily available. A balance between performance, cost, and availability is essential to ensure the system's overall feasibility and maintainability.
In summary, the choice of material for fuel lines in fuel injection systems is a complex decision that requires careful consideration of various factors. By selecting the right materials, engineers can ensure that the fuel lines are durable, compatible with the fuel, and capable of performing reliably in the demanding conditions of a fuel injection system. This attention to detail is vital for the overall efficiency and longevity of the vehicle's fuel delivery system.
Mastering Fuel Routing: A Guide to Walbro Carb Installations
You may want to see also
Frequently asked questions
While it is not mandatory, using a one-piece fuel line is often recommended for fuel injection systems. This design ensures a continuous and uninterrupted path for the fuel, reducing potential leakages and pressure drops.
A one-piece fuel line offers improved fuel delivery efficiency, as there are no joints or connections that could cause leaks. It also provides better flexibility, allowing for easier installation and minimizing the risk of damage during vehicle movement.
Yes, a one-piece fuel line can be utilized in various engine configurations. However, it is crucial to ensure that the line is compatible with the specific fuel pressure and flow requirements of the engine to maintain optimal performance.
One potential challenge is the cost, as one-piece fuel lines might be more expensive than traditional two-piece lines. Additionally, installation may require more skill and time, especially in tight spaces.
A well-designed one-piece fuel line can contribute to improved fuel efficiency by minimizing fuel loss and ensuring precise fuel delivery. This can lead to better engine performance and potentially lower fuel consumption.