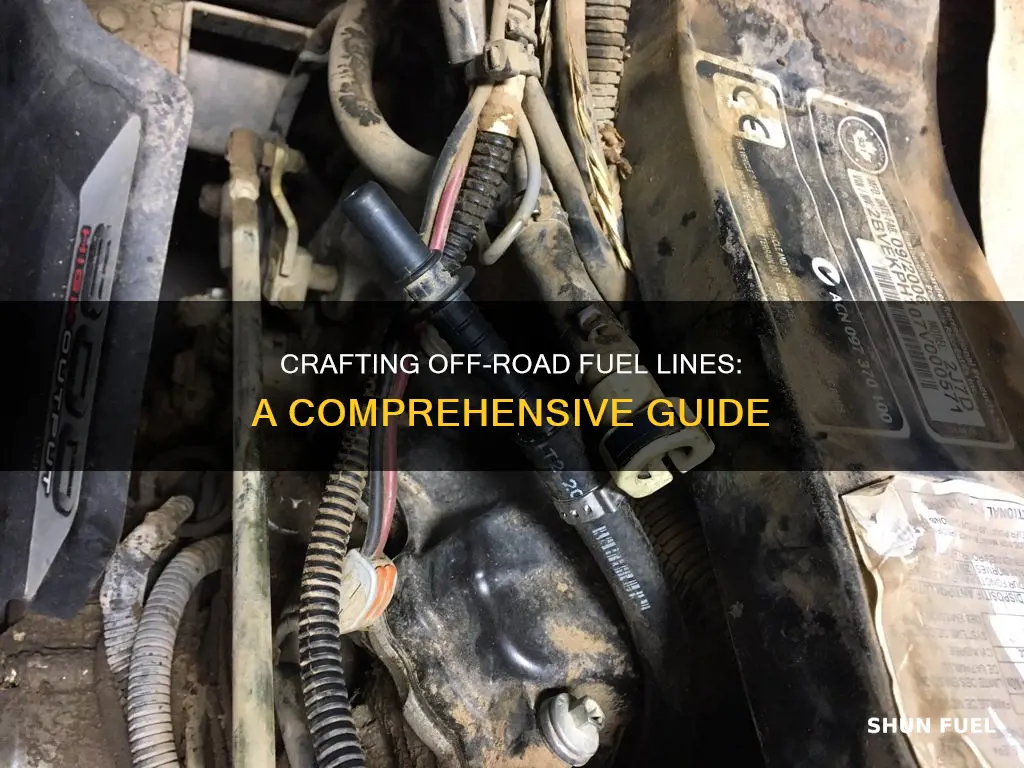
Creating fuel lines for off-road vehicles requires careful planning and specialized knowledge. This process involves selecting the right materials, such as durable rubber or synthetic hoses, and ensuring they can withstand the rigors of off-road environments, including extreme temperatures and vibrations. The design must also consider the vehicle's specific fuel system, including the fuel pump, tank, and injectors, to ensure optimal performance and safety. This guide will provide a step-by-step approach to constructing robust fuel lines tailored for off-road adventures, covering everything from material selection to installation techniques.
What You'll Learn
- Design and Material Selection: Choose durable materials like steel or high-density polyethylene for fuel lines
- Reinforcement and Protection: Reinforce lines with braids or sleeves to withstand off-road conditions and prevent damage
- Fitting and Connections: Use high-quality fittings and ensure tight connections to prevent leaks
- Routing and Placement: Route lines away from heat sources and sharp edges to avoid damage
- Testing and Inspection: Conduct pressure tests and inspections to ensure lines are leak-free and functional
Design and Material Selection: Choose durable materials like steel or high-density polyethylene for fuel lines
When designing fuel lines for off-road vehicles, material selection is a critical aspect to ensure durability and reliability in harsh environments. The primary goal is to create a fuel line that can withstand the rigors of off-road terrain, including extreme temperatures, vibrations, and potential impacts. One of the most commonly used materials for this purpose is steel. Steel offers exceptional strength and durability, making it ideal for withstanding the demanding conditions of off-road adventures. It is highly resistant to corrosion and can handle the pressure and heat associated with fuel systems. For instance, stainless steel is a popular choice due to its superior corrosion resistance, ensuring that the fuel lines remain intact even in the presence of moisture and chemicals.
Another excellent material for off-road fuel lines is high-density polyethylene (HDPE). HDPE is known for its lightweight nature, which reduces the overall weight of the fuel system, a crucial consideration for off-road vehicles where weight optimization is essential. This material is also highly flexible, allowing it to navigate through tight spaces and around various vehicle components without compromising its structural integrity. Additionally, HDPE is resistant to most chemicals found in fuels, ensuring that the material does not degrade over time, thus providing long-lasting performance.
The design of the fuel lines should incorporate features that enhance their durability. One approach is to use a braided construction, where multiple layers of material are braided together to create a strong and flexible fuel line. This design helps distribute stress evenly and prevents the line from kinking or bending excessively, which could lead to fuel leaks. Another important consideration is the use of protective sleeves or coatings to shield the fuel lines from potential impacts and abrasion. These protective measures can be made from materials like rubber or plastic, ensuring that the fuel lines remain intact even when subjected to rough terrain.
In summary, for off-road fuel lines, steel and high-density polyethylene are excellent choices due to their durability, flexibility, and resistance to environmental factors. The design should incorporate features like braided construction and protective sleeves to further enhance the fuel lines' resilience. By carefully selecting materials and implementing thoughtful design choices, you can create fuel lines that are reliable and capable of handling the challenges posed by off-road environments.
Mastering Fuel Line Removal: A Guide for 1997 Ford F150 Owners
You may want to see also
Reinforcement and Protection: Reinforce lines with braids or sleeves to withstand off-road conditions and prevent damage
When preparing fuel lines for off-road adventures, reinforcement and protection are crucial to ensure the lines can withstand the rigors of rough terrain. One effective method is to reinforce the fuel lines with braids or sleeves. These protective layers act as a shield, safeguarding the lines from potential damage caused by rocks, debris, and other obstacles encountered during off-road driving.
Braiding is a popular technique that involves intertwining multiple strands of material to create a sturdy and flexible reinforcement. By braiding the fuel lines, you add strength and durability, making them more resistant to wear and tear. This method is especially useful for areas where the fuel lines are more susceptible to impact, such as near the engine or under the vehicle's body. The braided pattern distributes the force evenly, preventing any single point from bearing the entire load, thus reducing the risk of breakage.
Sleeve protection, on the other hand, involves wrapping a protective covering around the fuel lines. These sleeves are typically made from durable materials like rubber or plastic, providing a smooth and protective barrier. The sleeves glide over the lines, absorbing shocks and impacts, and preventing any direct contact with harsh surfaces. This method is particularly useful for longer fuel lines, where the risk of damage is higher due to the increased distance between the source and the destination.
To implement this reinforcement technique, start by carefully measuring the length of the fuel lines that require protection. Then, procure the appropriate braiding material or sleeves based on the specific requirements of your vehicle. Ensure that the material is compatible with the fuel lines' diameter and the overall system design. Once you have the materials, carefully wrap or braid the lines, ensuring that the reinforcement is secure and taut. Pay close attention to any bends or turns in the line, as these areas may require additional support.
By employing braiding or sleeve reinforcement, you create a robust and reliable fuel line system tailored for off-road environments. This protective measure not only enhances the longevity of the fuel lines but also contributes to the overall safety and performance of your vehicle during challenging off-road journeys. Remember, proper reinforcement is a critical aspect of building a robust off-road fuel system, ensuring that your vehicle can handle the demands of rough terrain without compromising on fuel delivery.
Mastering EFI Fuel Line Installation: A Comprehensive Guide
You may want to see also
Fitting and Connections: Use high-quality fittings and ensure tight connections to prevent leaks
When constructing fuel lines for off-road vehicles, ensuring secure and leak-free connections is paramount. High-quality fittings are essential to withstand the rigors of off-road environments, including extreme temperatures, vibrations, and rough terrain. Start by selecting fittings that are specifically designed for fuel lines and compatible with the materials you've chosen. Look for fittings made from durable materials such as stainless steel or aluminum, which offer excellent resistance to corrosion and wear.
The process of fitting and connecting begins with preparing the fuel lines. Ensure that the lines are clean and free of any debris or contaminants. Use a suitable solvent cleaner to remove any old fuel or grease, allowing for a strong bond between the fittings and the line. Then, measure and cut the fuel lines to the desired length, ensuring a precise fit for the fittings.
Next, apply a thin layer of fuel line adhesive or tape to the interior of the fittings and the exterior of the fuel lines. This step creates a secure bond and prevents leaks. Carefully insert the fuel line into the fitting, ensuring it is centered and aligned properly. Use a crimping tool to create a tight, secure connection between the fitting and the line. The crimp should be firm but not overly tight to avoid damaging the fuel line. Repeat this process for each connection, ensuring an even and consistent crimp.
Tight connections are critical to prevent fuel leaks, which can be dangerous and cause engine performance issues. Use a torque wrench to ensure that each fitting is tightened to the specified torque value. Over-tightening can damage the fuel line, while under-tightening may result in leaks. Check for any signs of leakage around the fittings and make adjustments as necessary.
Finally, inspect all connections thoroughly. Look for any signs of damage, cracks, or leaks. Test the system by starting the engine and monitoring for any fuel-related issues. Properly fitted and connected fuel lines will ensure a reliable and safe fuel supply for your off-road adventures. Regular maintenance and inspections will also help identify and address any potential issues before they become major problems.
Step-by-Step Guide: Disconnecting Fuel Lines on Your Mazda 3
You may want to see also
Routing and Placement: Route lines away from heat sources and sharp edges to avoid damage
When designing fuel lines for off-road vehicles, proper routing and placement are crucial to ensure the system's longevity and performance. One critical aspect is to route the fuel lines away from heat sources and sharp edges to prevent damage. Here's a detailed guide on how to achieve this:
Identify Potential Hazards: Begin by thoroughly inspecting the vehicle's surroundings and identifying potential sources of heat and sharp objects. Common heat sources include exhaust systems, engine components, and even the vehicle's body panels, especially in areas with limited access. Sharp edges could be found in engine compartments, under the vehicle, or along the frame rails. Understanding these hazards is the first step in creating a safe routing plan.
Route Away from Heat: Fuel lines should be positioned to maintain a safe distance from heat sources. For example, if the engine block heater is located near the fuel tank, ensure the fuel lines are routed away from this area. Consider using heat shields or protective sleeves to shield the lines from direct contact with hot surfaces. This simple measure can prevent fuel line degradation and potential leaks.
Avoid Sharp Edges and Vibration: Off-road vehicles often encounter rough terrain, leading to potential damage from sharp edges and vibrations. Route the fuel lines away from frame rails, suspension components, and other sharp-edged parts. Use flexible hoses and protective covers to absorb vibrations and reduce the risk of chafing or puncturing the lines. Properly securing the lines with ties or clips can also prevent them from coming into contact with sharp surfaces.
Consider Flexibility and Accessibility: While routing away from hazards, ensure that the fuel lines maintain flexibility and accessibility. Avoid tight bends or kinks that could restrict fuel flow or make maintenance difficult. Allow for some slack in the routing to accommodate the vehicle's movement and potential expansion due to temperature changes. Additionally, ensure that the lines are easily accessible for inspection and potential repairs, especially in areas where the vehicle may be raised or modified.
Use Protective Materials: Enhance the protection of fuel lines by using appropriate materials. Consider fuel-resistant hoses and protective sleeves made from durable materials like rubber or PVC. These materials can withstand heat, abrasion, and chemical exposure, ensuring the lines' longevity. Properly sealing connections and using appropriate fasteners can further reinforce the system's integrity.
By following these guidelines, you can create a robust and reliable fuel system for off-road adventures, minimizing the risk of damage and ensuring a safe and efficient fuel supply. Proper routing and placement are essential steps in the overall process of building a customized fuel line system tailored to the challenges of off-road environments.
Quick Fix: Temporarily Stop Fuel Leaks in Metal Lines
You may want to see also
Testing and Inspection: Conduct pressure tests and inspections to ensure lines are leak-free and functional
When it comes to creating fuel lines for off-road vehicles, testing and inspection are crucial steps to ensure the lines are robust, reliable, and leak-free. This process involves a series of rigorous checks to verify the integrity of the fuel lines under various conditions. Here's a detailed guide on how to conduct these tests and inspections:
Pressure Testing:
- Start by filling the fuel lines with a suitable pressure gauge and a known amount of pressure, typically 50-100 psi above the operating pressure. This initial test helps identify any potential issues with the line's structure.
- Use a mechanical gauge or a digital pressure gauge to measure the pressure at different points along the line. Ensure that the pressure is evenly distributed and stable.
- Listen for any hissing or bubbling sounds, which could indicate leaks. If leaks are detected, carefully inspect the line for any visible damage, cracks, or weak spots.
- For more advanced testing, consider using a pressure-sensitive dye or a leak detection kit. These tools can help identify even the smallest leaks by releasing a colored dye or a chemical agent that reacts to pressure.
Leak Detection and Functional Inspection:
- After pressure testing, perform a visual inspection to check for any signs of damage or wear. Look for frayed lines, kinks, or any signs of corrosion.
- Apply a small amount of fuel to the line and observe for any leaks at connections, fittings, and joints. Ensure that all connections are tight and secure.
- Test the functionality of the fuel lines by simulating different driving conditions. This includes rapid acceleration, deceleration, and sudden changes in direction. Listen for any unusual noises and check for fuel flow consistency.
- Consider using a fuel pressure gauge to measure the pressure at the engine's fuel injectors or carburetor. This will help ensure that the fuel lines are delivering the required pressure for optimal engine performance.
Long-Term Testing:
- For off-road applications, it's essential to simulate the extreme conditions your vehicle might encounter. Conduct long-term testing by running the engine for extended periods, including high-load and low-load scenarios.
- Monitor the fuel lines for any signs of degradation, such as softening or hardening, which could affect their flexibility and durability.
- Regularly inspect the lines for any signs of fuel contamination, especially if using non-standard fuels. Contaminated fuel can lead to blockages and damage to the fuel system.
Documentation and Record-Keeping:
- Maintain detailed records of all testing procedures, including pressure values, test dates, and any issues encountered. This documentation will be valuable for future reference and can help identify patterns or recurring problems.
- Keep a log of any repairs or replacements made during the testing process, ensuring that all necessary actions are documented.
By following these testing and inspection procedures, you can ensure that your off-road fuel lines are of the highest quality, providing reliable performance and safety in demanding environments. Regular maintenance and testing are key to extending the lifespan of your fuel lines and maintaining the overall health of your vehicle's fuel system.
Clogged Fuel Line? Fix Your Lawn Mower's Performance with These Steps
You may want to see also
Frequently asked questions
For off-road applications, fuel lines are typically made from durable materials like stainless steel, high-density polyethylene (HDPE), or braided nylon. These materials offer excellent resistance to fuel contamination, extreme temperatures, and abrasion, ensuring reliable performance in rugged environments.
Selecting the appropriate fuel line diameter depends on various factors, including engine power, fuel flow rate, and desired pressure. Generally, a larger diameter fuel line is recommended for high-performance engines to handle increased fuel volume and pressure. Off-road enthusiasts often opt for lines with diameters ranging from 3/8" to 1/2" for optimal performance and reliability.
Yes, proper installation is crucial for the longevity of fuel lines. Here are some tips:
- Ensure a secure connection by using fuel line connectors that provide a tight seal.
- Route the fuel lines away from heat sources and sharp edges to prevent damage.
- Use fuel line protectors or sleeves to guard against punctures and abrasion during off-road adventures.
- Regularly inspect the fuel lines for any signs of wear or damage, especially after off-road trips, and replace them if necessary.