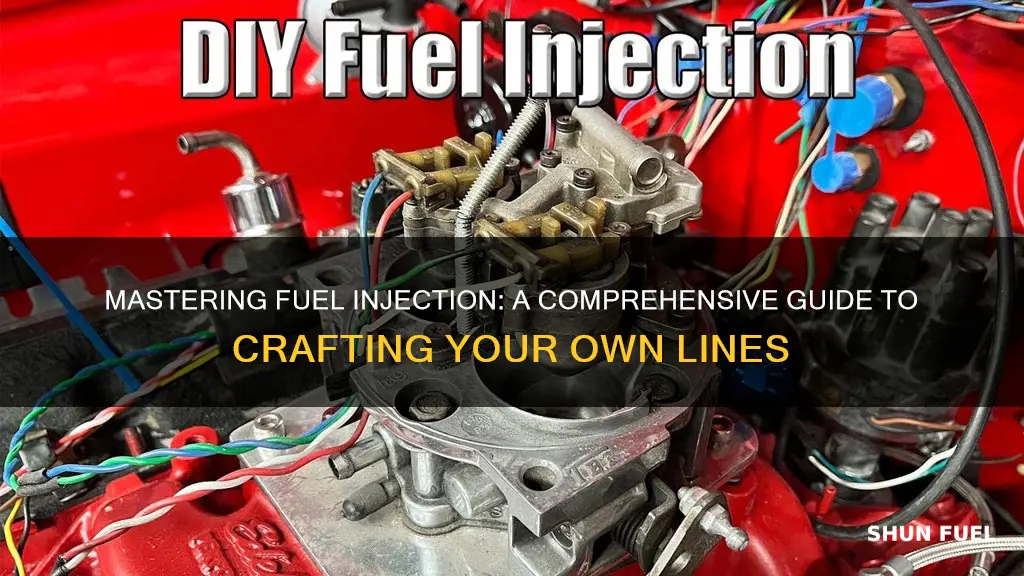
Fuel injection lines are a crucial component in modern vehicle engines, and understanding how to make them is essential for mechanics and DIY enthusiasts. This process involves creating a precise and efficient pathway for fuel to travel from the fuel tank to the engine's injectors. It requires careful consideration of materials, such as high-quality rubber or synthetic compounds, to ensure durability and resistance to fuel degradation. The lines must be designed with specific diameters and lengths to match the engine's requirements, and they should be assembled with precision to avoid leaks and ensure optimal performance. This guide will provide a step-by-step approach to constructing fuel injection lines, covering everything from material selection to assembly techniques.
What You'll Learn
- Fuel Injection Basics: Understand the principles of fuel injection systems and their role in engine performance
- Line Material Selection: Choose the right materials for fuel injection lines based on compatibility and durability
- Line Routing and Placement: Properly route and position fuel lines to avoid interference and ensure optimal flow
- Clamping and Support: Secure fuel lines with appropriate clamps and supports to prevent leaks and damage
- Testing and Maintenance: Regularly inspect and test fuel injection lines for leaks and performance issues
Fuel Injection Basics: Understand the principles of fuel injection systems and their role in engine performance
Fuel injection systems are a crucial component of modern engines, revolutionizing the way engines operate and perform. These systems play a vital role in optimizing fuel efficiency, power output, and overall engine health. Understanding the basics of fuel injection is essential for anyone looking to enhance their vehicle's performance or simply appreciate the inner workings of an engine.
At its core, a fuel injection system is responsible for delivering the precise amount of fuel required for combustion in an engine's cylinders. Unlike traditional carburetor systems, fuel injection offers a more controlled and efficient process. The system operates by precisely metering and injecting fuel into the engine's intake manifold or directly into the combustion chamber. This precision ensures that the fuel-air mixture is optimized for efficient combustion, resulting in improved power and performance.
The process begins with the fuel injection pump, which is typically driven by a gear or belt connected to the engine. This pump draws fuel from the fuel tank and pressurizes it, ensuring a consistent and controlled flow. The pressurized fuel is then directed through injectors, which are strategically positioned in the engine's intake manifold or cylinders. These injectors spray the fuel in a fine mist, ensuring complete atomization and efficient mixing with the incoming air.
One of the key advantages of fuel injection is its ability to provide a precise fuel-air mixture. Modern fuel injection systems use sophisticated electronic controls to monitor and adjust the fuel injection timing, quantity, and pressure. This ensures that the engine receives the exact amount of fuel required at any given operating condition. As a result, the engine can maintain optimal performance across a wide range of speeds and loads, delivering improved power, torque, and fuel efficiency.
Furthermore, fuel injection systems offer enhanced responsiveness and throttle control. The electronic controls allow for rapid adjustments to the fuel injection rate, enabling quick acceleration and improved low-end torque. This responsiveness is particularly beneficial for sports cars and high-performance vehicles, where quick bursts of power are often required. Additionally, fuel injection systems can adapt to varying driving conditions, such as changes in altitude or temperature, ensuring consistent performance regardless of the environment.
In summary, fuel injection systems are a sophisticated technology that has transformed engine performance and efficiency. By precisely controlling fuel delivery, these systems optimize combustion, improve power output, and enhance overall engine health. Understanding the principles of fuel injection is essential for anyone seeking to maximize their vehicle's potential or simply appreciate the intricate workings of modern engines. With their ability to provide a precise fuel-air mixture and responsive throttle control, fuel injection systems continue to play a pivotal role in the automotive industry.
Mastering Quick Connect Fuel Lines: A Step-by-Step Guide to Disconnection
You may want to see also
Line Material Selection: Choose the right materials for fuel injection lines based on compatibility and durability
When it comes to constructing fuel injection lines, material selection is a critical aspect that directly impacts the performance, reliability, and longevity of the system. The primary goal is to ensure compatibility and durability, as these lines carry high-pressure fuel, which can be highly corrosive and potentially damaging if not properly managed. Here's a detailed guide on how to choose the right materials for your fuel injection lines:
Understanding the Environment: Before selecting any material, it's essential to understand the operating environment of the fuel injection lines. This includes factors such as temperature extremes, exposure to sunlight or heat sources, the presence of chemicals or corrosive substances, and the overall mechanical stress the lines will endure. For instance, lines in high-temperature environments might require materials with excellent heat resistance, while those exposed to sunlight might need UV-resistant materials to prevent degradation.
Material Compatibility: Compatibility is a key consideration. The materials used for the lines should be compatible with the fuel being injected, as well as any other substances that might come into contact with them. For example, if the fuel contains ethanol, the materials should be able to withstand the corrosive effects of ethanol. Additionally, the lines should not react with any chemicals used in the fuel system, such as detergents or lubricants. Common materials used for fuel lines include rubber, silicone, and various types of plastics, each with its own set of advantages and limitations.
Durability and Flexibility: Fuel injection lines need to be durable enough to withstand the mechanical stresses of the engine, including vibrations, temperature changes, and pressure fluctuations. They should also be flexible to accommodate the movement of the engine components. Rubber and silicone are popular choices for their flexibility, but the specific type and grade of these materials should be chosen carefully to ensure they meet the required durability standards. For instance, high-temperature environments might call for a more heat-resistant grade of silicone.
Pressure Rating and Burst Strength: The chosen material should have a pressure rating that exceeds the maximum operating pressure of the fuel system. This ensures that the lines can handle the fuel pressure without failing. Additionally, the burst strength of the material should be considered, which is the maximum pressure at which the material is expected to rupture. Materials with higher burst strengths are more reliable and can handle more aggressive fuel systems.
Testing and Quality Control: To ensure the best results, it is crucial to test the chosen materials under simulated engine conditions. This includes subjecting the lines to various temperatures, pressures, and chemical environments to assess their performance and longevity. Quality control measures should be implemented to verify that the materials meet the specified requirements. This might involve laboratory testing, as well as on-vehicle testing to ensure the lines perform as expected in real-world conditions.
Mastering the Art of Fuel Line Disconnection: A Step-by-Step Guide
You may want to see also
Line Routing and Placement: Properly route and position fuel lines to avoid interference and ensure optimal flow
When designing fuel injection lines, proper routing and placement are critical to ensure efficient fuel delivery and prevent potential issues. Here's a detailed guide on how to achieve optimal line routing and placement:
- Understand the Layout: Begin by thoroughly understanding the engine bay layout and the available space. Identify the locations of various components such as the fuel pump, injectors, engine block, and any other obstacles. This knowledge will help you plan the route for the fuel lines, ensuring they don't interfere with moving parts or critical components.
- Route Planning: Design a route that minimizes the length of the fuel lines. Longer lines can lead to increased fuel pressure drop and potential flow restrictions. Aim for a direct path from the fuel pump to the injectors, ensuring the lines are as short as possible. Consider the engine's orientation; horizontal lines are generally preferred as they provide better flow characteristics compared to vertical lines.
- Avoid Interference: Proper routing is essential to prevent interference with other engine components. Fuel lines should be positioned away from moving parts like valves, camshafts, and timing chains. Ensure there is sufficient clearance to avoid damage or malfunction during engine operation. For example, route the lines away from the engine block and any heat-generating components to prevent overheating.
- Secure Mounting: Securely mount the fuel lines to the engine bay using appropriate ties or brackets. This prevents movement and ensures the lines maintain their optimal position. Avoid tight bends or kinks in the lines, as these can restrict fuel flow and potentially cause damage over time. Use flexible ties or clips that allow for slight adjustments to accommodate any minor variations in the engine bay's dimensions.
- Optimize Flow: Consider the flow characteristics of the fuel lines. Use smooth-bore lines with minimal internal surface roughness to ensure efficient fuel delivery. Avoid using lines with sharp bends or abrupt changes in diameter, as these can create flow restrictions and pressure drops. Properly sized lines with gradual transitions will help maintain optimal fuel pressure and flow rate.
- Regular Maintenance: Regularly inspect the fuel lines for any signs of damage, leaks, or wear. Over time, fuel lines can degrade due to heat, fuel contamination, or physical stress. Replace any damaged lines promptly to maintain proper fuel injection performance.
By following these guidelines, you can ensure that the fuel lines are properly routed and positioned, avoiding interference and optimizing fuel flow to the injectors. This results in efficient engine operation and improved overall performance. Remember, proper maintenance and regular checks are also essential to keep the fuel system in optimal condition.
Poulin Fuel Line 530069599: Unlocking the Right Size for Your Vehicle
You may want to see also
Clamping and Support: Secure fuel lines with appropriate clamps and supports to prevent leaks and damage
When it comes to fuel injection systems, proper clamping and support are crucial to ensure optimal performance and longevity. Fuel lines are susceptible to leaks and damage due to their position near heat sources and vibrations. Here's a detailed guide on how to secure fuel lines effectively:
Clamping Techniques:
- Use high-quality metal or plastic fuel line clamps specifically designed for fuel applications. These clamps should have a sturdy construction to withstand fuel pressure and environmental factors.
- When clamping, ensure a tight fit around the fuel line. Start by placing the clamp over the line, then tighten it securely. Avoid overtightening to prevent damage to the line or surrounding components.
- Consider the location of the clamp. It should be positioned away from heat sources like exhaust manifolds or engine components that could cause damage.
- For multiple fuel lines, use a 'clamping kit' or a custom-made bracket to secure them in a neat and organized manner. This prevents tangling and ensures easy access during maintenance.
Supporting the Fuel Lines:
- Fuel lines should be supported at regular intervals to reduce stress and prevent kinking. Use rubber or plastic supports that can absorb vibrations and protect the lines.
- Mount the supports at strategic points, such as near the fuel tank, along the length of the lines, and at any bends or turns. Ensure they are securely attached to the vehicle's body or frame.
- For longer fuel lines, consider using a 'fuel line bridge' or a custom-made support structure to distribute the weight evenly and prevent sagging.
- In areas with high vibration, such as near the engine, use vibration-damping supports to minimize the impact on the fuel lines.
By implementing these clamping and support techniques, you can ensure that your fuel injection lines are secure, protected from potential hazards, and less prone to leaks. Regular inspection and adjustment of these clamps and supports are essential, especially during routine engine maintenance, to maintain the overall health of your fuel system.
Cold Weather Fuel Line Freezing: A Risk for Airplanes?
You may want to see also
Testing and Maintenance: Regularly inspect and test fuel injection lines for leaks and performance issues
Fuel injection lines are critical components of a vehicle's engine, and ensuring their proper functioning is essential for optimal performance and fuel efficiency. Regular testing and maintenance of these lines are crucial to identify and rectify potential issues before they escalate into more significant problems. Here's a comprehensive guide on how to approach this task:
Visual Inspection: Begin by performing a thorough visual inspection of the fuel injection lines. Look for any visible signs of damage, such as cracks, punctures, or corrosion. Inspect the lines for any signs of leakage, especially around connections and fittings. Even a small leak can lead to engine misfires and reduced performance. Check for any signs of contamination, such as dirt or debris, which could indicate a compromised seal or fitting issue.
Leak Testing: To ensure the lines are leak-free, perform a leak test. This can be done by applying a small amount of diesel fuel or a suitable test fluid to the lines and observing for any seepage. Use a bright light or a flashlight to illuminate the lines and detect even the smallest leaks. If a leak is detected, immediately address the issue by tightening connections, replacing damaged fittings, or repairing the line.
Pressure Testing: Fuel injection lines should operate within specific pressure ranges to function correctly. Use a fuel pressure gauge to measure the pressure at the injectors. Compare the readings to the manufacturer's specifications to ensure they fall within the acceptable range. If the pressure is too low or too high, it may indicate a problem with the pump, regulator, or lines themselves. Adjustments or replacements might be necessary to restore optimal pressure.
Performance Evaluation: Regularly testing the fuel injection system's performance is vital. This involves monitoring the engine's idling quality, acceleration, and overall responsiveness. Listen for any unusual noises, such as hissing or roaring, which could indicate a problem with the lines or injectors. Check for engine misfires, which may be caused by clogged or damaged fuel lines. Addressing these issues promptly can prevent long-term engine damage.
Maintenance Schedule: Establish a regular maintenance schedule for fuel injection line testing and inspection. This is especially important for vehicles with high mileage or those operating in harsh environments. Consider the following maintenance routine: every 10,000 miles or annually, inspect and test the lines for any signs of wear and tear. Keep a record of any issues found and the corresponding repairs or replacements made. This documentation will help identify recurring problems and guide future maintenance decisions.
By following these testing and maintenance procedures, you can ensure that your fuel injection lines remain in excellent condition, providing efficient fuel delivery and optimal engine performance. Regular attention to these critical components will save you from potential breakdowns and costly repairs in the long run.
Does Fuel Line Size Affect Engine Performance?
You may want to see also
Frequently asked questions
Fuel injection is a process where fuel is injected directly into the engine's cylinders to optimize combustion. It is crucial as it enhances engine performance, improves fuel efficiency, and reduces emissions.
Before installing fuel injection lines, ensure the engine is cool and drain the fuel tank. Clean the engine bay and lines to remove any debris. Inspect the lines for any damage or leaks, and replace any faulty parts.
You will need fuel injection line kits, which typically include the lines, fittings, and necessary hardware. Common tools include a fuel pump, fuel pressure gauge, line cutting tools, and a fuel filter. It's essential to have the correct specifications and sizes for your engine.
Yes, customization is possible. You can adjust the line length, use different materials, or modify the fuel flow rate to suit your engine's needs. However, it requires careful consideration and testing to ensure optimal performance and safety.