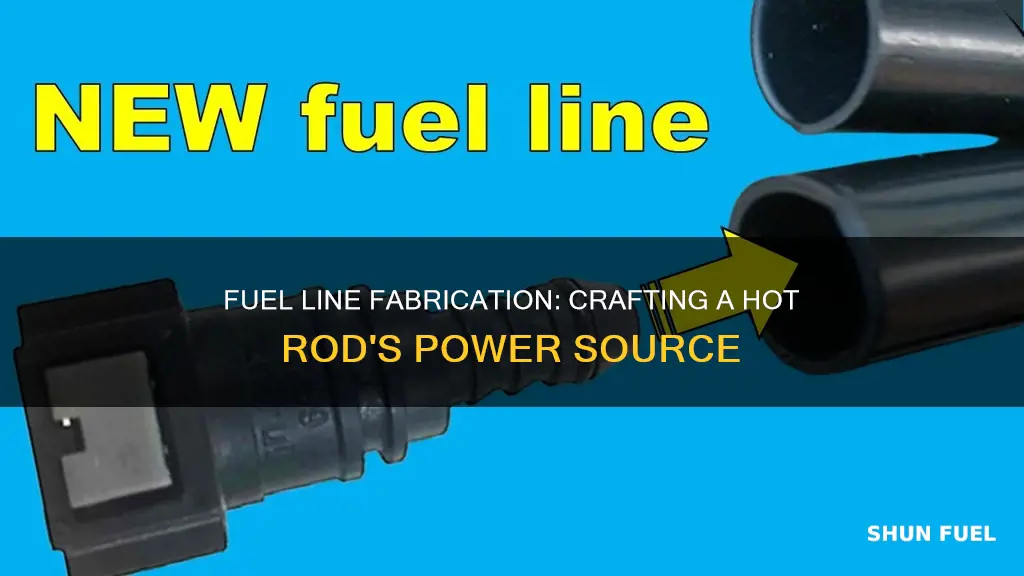
Creating a fuel line for a hot rod carburetor is an essential step in restoring or modifying a classic car's engine. This process involves careful selection of materials, precise measurements, and skilled craftsmanship to ensure optimal performance and reliability. The fuel line must be designed to handle high pressure and temperatures while maintaining a tight fit to prevent leaks and ensure efficient fuel delivery to the carburetor. This guide will provide a step-by-step overview of the process, including material preparation, cutting, bending, and installation techniques, to help enthusiasts achieve a professional-looking and functional fuel line for their hot rod.
What You'll Learn
- Fuel Pump Selection: Choose a pump with adequate flow rate for your engine's needs
- Line Material: Opt for durable materials like stainless steel or brass for longevity
- Line Routing: Route lines away from heat sources and sharp bends to prevent damage
- Fittings and Connections: Use high-quality fittings and ensure tight, leak-free connections
- Testing and Adjustments: Test the fuel system under load and make adjustments for optimal performance
Fuel Pump Selection: Choose a pump with adequate flow rate for your engine's needs
When it comes to building a fuel system for a hot rod with a carburetor, selecting the right fuel pump is a critical component of the process. The pump's primary role is to deliver the required amount of fuel to the carburetor at the right pressure, ensuring optimal engine performance. Here's a guide on how to choose the appropriate fuel pump for your hot rod's engine:
Flow Rate Considerations: The flow rate of a fuel pump is a crucial specification to match with your engine's requirements. It is measured in gallons per minute (GPM) and indicates the volume of fuel the pump can deliver in one minute. For a hot rod, you'll want to consider the engine's displacement and power output. Larger engines or those with high-performance modifications often demand more fuel, so a higher GPM pump is necessary. As a general rule, aim for a pump that provides at least 1.5 to 2 times the engine's estimated fuel consumption to ensure it can meet the needs of even the most demanding driving conditions.
Pressure Regulation: Fuel pumps also play a vital role in maintaining the correct fuel pressure. The pressure required depends on the carburetor type and engine configuration. For a typical hot rod setup, a pump capable of generating 4-6 psi (pounds per square inch) is often sufficient. However, for high-performance applications or engines with modified intake systems, you might need a pump that can deliver higher pressure to ensure proper atomization and efficient combustion.
Compatibility and Size: Ensure that the fuel pump you select is compatible with your hot rod's existing fuel lines and fittings. Consider the physical size and mounting options of the pump to ensure it fits within the available space in your engine bay. Some pumps offer adjustable flow rates, allowing you to fine-tune the performance according to your engine's needs.
Testing and Calibration: After installing the fuel pump, it's essential to test and calibrate the system. This process involves measuring the fuel pressure and flow rate at different engine speeds to ensure it meets the required specifications. Adjustments might be necessary to optimize the pump's performance and ensure a smooth and efficient fuel delivery system for your hot rod.
Remember, the goal is to provide your hot rod's engine with the right amount of fuel, at the right pressure, and at the right time. By carefully selecting a fuel pump with an adequate flow rate, you'll ensure that your hot rod's carburetor receives the necessary fuel for optimal performance and power delivery.
Unclamp Fuel Line: A Step-by-Step Guide to Easy Access
You may want to see also
Line Material: Opt for durable materials like stainless steel or brass for longevity
When it comes to constructing a fuel line for a hot rod carburetor, the choice of material is crucial for ensuring durability and long-term performance. Opting for high-quality, durable materials like stainless steel or brass is an excellent decision that will pay off in the long run. These materials offer several advantages that make them ideal for this application.
Stainless steel is renowned for its exceptional corrosion resistance, making it an excellent choice for fuel lines. It can withstand the harsh chemicals in gasoline and prevent any potential degradation or deterioration over time. This is especially important in the high-temperature and corrosive environment of a hot rod engine. By using stainless steel, you ensure that the fuel line remains strong and reliable, even when exposed to extreme conditions.
Similarly, brass is another excellent option for fuel line construction. It possesses inherent durability and flexibility, allowing it to withstand the rigors of a hot rod's mechanical environment. Brass is also resistant to corrosion, ensuring that the fuel line remains intact and functional even in the presence of moisture and varying temperatures. Its natural resistance to rust and oxidation makes it a reliable choice for fuel lines, providing long-lasting performance.
Both stainless steel and brass offer superior strength and flexibility, which are essential properties for fuel lines. These materials can accommodate the vibrations and movements experienced in a hot rod engine without compromising their structural integrity. The flexibility ensures that the fuel line can navigate around engine components effortlessly, while the strength prevents any potential leaks or damage.
In summary, when building a fuel line for a hot rod carburetor, it is imperative to choose materials that can withstand the demanding conditions of a high-performance engine. Stainless steel and brass are the go-to options due to their durability, corrosion resistance, and ability to maintain structural integrity. By selecting these materials, you ensure that your fuel line will provide reliable performance and contribute to the overall success of your hot rod's engine.
Twisted Fuel Line? Fix It with These Simple Steps (Pics)
You may want to see also
Line Routing: Route lines away from heat sources and sharp bends to prevent damage
When installing fuel lines for a hot rod carburetor, proper line routing is crucial to ensure the system's longevity and performance. One of the most critical aspects of this process is to route the lines away from heat sources and sharp bends. This practice is essential to prevent damage to the fuel lines, which can lead to fuel leaks, reduced performance, and even engine failure.
Heat sources, such as exhaust manifolds, headers, and engine components, can cause the fuel lines to expand and contract rapidly, leading to potential cracks and leaks. To mitigate this risk, it is recommended to route the fuel lines as far away from these heat sources as possible. This can be achieved by using flexible metal or rubber hoses that can be bent around the engine without coming into direct contact with hot surfaces. Additionally, consider using heat shields or insulation to further protect the fuel lines.
Sharp bends in the fuel lines can also be detrimental. These bends can cause stress on the line's material, leading to potential cracks or even complete rupture. To avoid this, aim for smooth, gradual curves when routing the lines. The general rule of thumb is to keep the radius of the bend as large as possible to minimize stress. For example, if you need to bend a line around a component, ensure the bend radius is at least twice the diameter of the line to reduce the risk of damage.
Another important consideration is the use of appropriate fasteners and ties. When securing the fuel lines, avoid tight bends or kinks by using ties or clips that allow for some flexibility. This is especially important when the lines need to accommodate the engine's movement during operation. Additionally, ensure that all fasteners are tight enough to secure the lines but not so tight that they cause unnecessary stress or damage.
In summary, proper line routing is a critical aspect of installing fuel lines for a hot rod carburetor. By routing the lines away from heat sources and sharp bends, you can significantly reduce the risk of damage and ensure a reliable fuel supply to the engine. This attention to detail will contribute to the overall performance and longevity of your hot rod's fuel system.
Stock Steel Fuel Line Pressure Limits: A Comprehensive Guide
You may want to see also
Fittings and Connections: Use high-quality fittings and ensure tight, leak-free connections
When building a fuel line for a hot rod carburetor, the quality of fittings and connections is paramount to ensure optimal performance and reliability. High-quality fittings are essential to maintain a tight and secure seal, preventing fuel leaks and potential engine issues. Here's a detailed guide on this crucial aspect:
Choose the Right Fittings: Opt for fittings specifically designed for fuel lines in automotive applications. These fittings are typically made from durable materials such as brass, stainless steel, or aluminum, ensuring longevity and resistance to fuel degradation. Common types include compression fittings, quick-connect fittings, and barbed fittings. Each type has its advantages, so select based on your specific needs and the layout of your fuel system. For instance, compression fittings offer a tight seal with a compression ring, while quick-connect fittings provide ease of installation and removal.
Prepare the Fuel Line and Fitting: Before connecting, ensure the fuel line is clean and free of any debris or contaminants. Use a fuel line cleaner or a mild solvent to remove any old fuel or varnish. Cut the fuel line to the desired length, allowing for a small overlap at the fitting end for a secure connection. Prepare the fitting by removing any existing seals or o-rings and inspecting the threads for damage or wear.
Assembly and Tightening: Follow the manufacturer's instructions for each fitting type. For compression fittings, insert the fuel line into the fitting, ensuring the line is centered. Then, tighten the fitting securely using a wrench, being careful not to overtighten, as this can damage the fuel line. For quick-connect fittings, simply snap the fitting onto the fuel line, ensuring a snug fit. Always double-check the tightness of the connections to guarantee a leak-free seal.
Leak-Proof Connections: Tight, leak-free connections are critical to the performance and safety of your hot rod's fuel system. Use thread seal tape or pipe compound on the threads of compression fittings to prevent leaks. For quick-connect fittings, ensure the locking mechanism is engaged and secure. Regularly inspect all connections for any signs of leakage, especially after initial assembly and during regular maintenance checks.
Testing and Final Touches: After completing the fittings and connections, test the fuel system under various conditions. Start the engine and monitor for any fuel-related issues, such as sputtering or excessive fuel consumption. If any leaks are detected, carefully identify the source and re-tighten or replace the affected fittings. Ensure all connections are secure and aligned to maintain the overall aesthetics of your hot rod's fuel line.
Fuel Line Installation: A Step-by-Step Guide for Your Tank
You may want to see also
Testing and Adjustments: Test the fuel system under load and make adjustments for optimal performance
When it comes to tuning a hot rod's carburetor, testing and adjustments are crucial to achieving optimal performance. Here's a detailed guide on how to test and fine-tune your fuel system under load conditions:
Load Testing:
The key to successful testing is simulating real-world driving conditions. You'll want to test your fuel system under load to ensure it delivers the right amount of fuel at various engine speeds and loads. Here's how:
- Use a Load Simulator: Invest in a load simulator, which can be a simple device that applies a controlled load to your engine. This simulates acceleration, deceleration, and varying engine speeds.
- Engine Speed Range: Test your fuel system across the entire engine speed range. Start with low idle and gradually increase the speed, simulating different driving conditions.
- Load Application: While testing, apply varying loads by using the load simulator. This will mimic situations like overtaking, climbing hills, or towing.
Testing Procedures:
- Fuel Pressure: Monitor fuel pressure during testing. Low pressure can indicate a restricted fuel line or pump issue.
- Idle Quality: Check idle quality (engine speed stability) and adjust the carburetor settings accordingly.
- Acceleration: Observe engine response during acceleration. A well-tuned fuel system should provide smooth power delivery without hesitation.
- Backfire and Popping: Listen for backfires or popping sounds, which can indicate improper fuel-air mixture or fuel system issues.
Adjustments:
Based on your test results, make adjustments to the carburetor settings:
- Fuel Mixture: Fine-tune the air-fuel mixture by adjusting the carburetor's idle and acceleration pumps. Richen the mixture slightly if you experience backfires, but be careful not to overdo it.
- Choke Settings: Adjust the choke to control the fuel-air mixture at different temperatures.
- Fuel Pump: If fuel pressure is low, consider adjusting the fuel pump settings or checking for restrictions in the fuel line.
- Jetting: Modify the jetting (fuel passages) to control the fuel flow rate. Smaller jets may be needed for high-performance applications.
Remember:
- Safety First: Always prioritize safety during testing. Ensure proper ventilation and wear protective gear when working with fuel.
- Data Logging: Consider using a data logging device to record engine parameters during testing for detailed analysis.
- Iterative Process: Tuning a carburetor is often an iterative process. Make small adjustments, test, and repeat until you achieve the desired performance.
Mastering the Art of Fuel Line Installation: A Step-by-Step Guide
You may want to see also
Frequently asked questions
A fuel line is a crucial component in any carburetor system, especially for hot rods, as it delivers the fuel from the fuel tank to the carburetor, ensuring a steady supply of gasoline for the engine to run efficiently.
When selecting fuel line material, consider factors like durability, flexibility, and resistance to fuel degradation. Common choices include nylon, stainless steel, or braided rubber, each offering varying levels of strength and flexibility. Nylon is lightweight and flexible, while stainless steel provides excellent corrosion resistance. Braided rubber offers a balance between flexibility and strength.
Using a standard fuel line may not be ideal for hot rods due to the high fuel flow rates and potential for heat buildup. Specialized fuel lines designed for high-performance applications are recommended. These lines often feature larger diameters, improved flexibility, and heat-resistant materials to handle the demands of high-speed driving and the engine's heat.