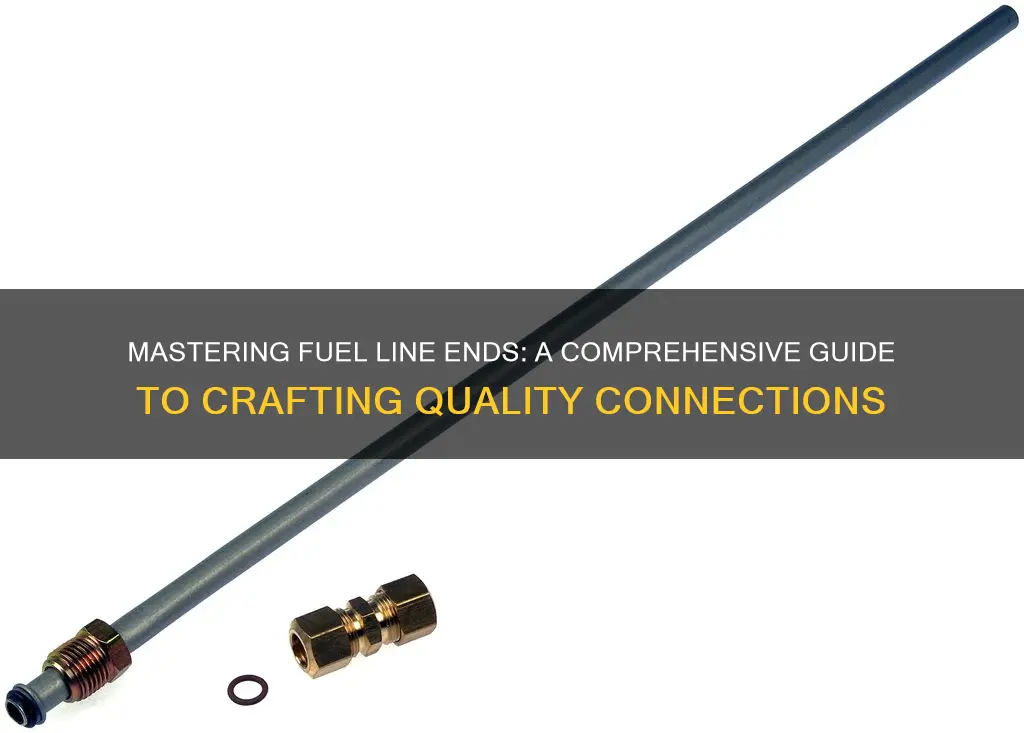
Making fuel line ends is a crucial process in the construction and maintenance of fuel systems in vehicles and machinery. It involves creating a secure and reliable connection between the fuel line and the fuel source or tank. This task requires precision and attention to detail to ensure the fuel line is properly sealed and protected from leaks and damage. The process typically involves soldering, crimping, or using specialized connectors, depending on the specific requirements and materials used in the fuel system. Understanding the different methods and techniques for making fuel line ends is essential for anyone working with fuel systems, ensuring efficient and safe operation.
What You'll Learn
- Fuel Line Materials: Choose appropriate materials for fuel lines, considering durability and compatibility
- End Connections: Explore various connection methods like crimping, soldering, or quick-connect fittings
- Fuel Line Routing: Plan optimal routes to avoid damage and ensure easy access
- Fuel Line Protection: Use protective measures like insulation or shielding to prevent damage
- Fuel Line Testing: Conduct pressure and leak tests to ensure the integrity of the fuel line ends
Fuel Line Materials: Choose appropriate materials for fuel lines, considering durability and compatibility
When it comes to fuel lines, selecting the right materials is crucial for ensuring optimal performance and longevity. The primary goal is to choose materials that can withstand the harsh conditions of fuel transport, including varying temperatures, pressure, and chemical exposure. Here's a detailed guide on the key considerations for fuel line materials:
Durability and Flexibility: Fuel lines need to be durable enough to handle the rigors of the automotive environment. Look for materials that offer excellent resistance to abrasion, fatigue, and corrosion. High-density polyethylene (HDPE) and polyvinyl chloride (PVC) are popular choices due to their flexibility and ability to withstand repeated bending without kinking. These materials can flex and move with the vehicle's components, ensuring a reliable fuel supply.
Compatibility with Fuel Type: Different types of fuel require specific materials to prevent contamination and ensure safety. For gasoline, materials like HDPE or PVC with a high-temperature rating are suitable. These materials can handle the volatility of gasoline and resist degradation over time. For diesel, consider materials like stainless steel or brass, which offer superior corrosion resistance and can withstand the higher pressure and temperature fluctuations associated with diesel fuel.
Temperature Resistance: Fuel lines must be able to operate reliably across a wide temperature range. Materials like HDPE and PVC have good temperature stability, allowing them to handle both hot and cold environments without becoming brittle or soft. In contrast, materials like stainless steel and brass are ideal for high-temperature applications, ensuring the fuel line remains flexible and functional even when exposed to engine heat.
Chemical Compatibility: Consider the chemicals present in the fuel and choose materials that are resistant to these substances. For example, ethanol-blended fuels may require materials that can withstand ethanol's corrosive properties. In such cases, HDPE or a specialized fuel line material designed for ethanol-resistant applications would be preferable.
Reinforcement and Protection: For fuel lines that are subject to more severe conditions, such as those in high-performance vehicles or off-road applications, consider adding reinforcement. Braided stainless steel or aramid fibers can provide additional strength and protection against abrasion. Additionally, protective sleeves or coatings can be applied to the fuel line to further enhance its durability.
By carefully selecting materials based on these factors, you can ensure that your fuel lines are robust, compatible, and capable of delivering fuel efficiently and safely. Remember, the right choice of materials is a critical aspect of building a reliable fuel system.
Fuel Line Coolers: Do They Really Work?
You may want to see also
End Connections: Explore various connection methods like crimping, soldering, or quick-connect fittings
When it comes to connecting fuel lines, there are several methods to ensure a secure and reliable end connection. Each method has its own advantages and is suitable for different scenarios. Here's an exploration of the various connection techniques:
Crimping: This method involves using a crimping tool to compress a fitting onto the fuel line. It is a popular choice due to its simplicity and effectiveness. Crimping provides a tight and secure connection, ensuring that the fuel line is firmly held in place. The process typically includes inserting the fuel line into the fitting, then using the crimping tool to apply pressure and create a mechanical bond. This technique is often used for high-pressure applications and is known for its durability. It is crucial to follow the manufacturer's guidelines for the specific crimping tool and fitting to ensure a proper connection.
Soldering: Soldering is an excellent option for creating a strong and permanent bond between fuel lines and fittings. This method involves melting a solder material onto the fitting and allowing it to cool, forming a solid connection. Soldering provides a leak-free seal and is particularly useful for high-temperature or corrosive environments. To begin, ensure the fuel line and fitting are clean and free of any oxidation. Apply a flux to the fitting to promote better solder adhesion. Then, heat the fitting and apply the solder, ensuring it flows onto the fuel line's surface. Practice and precision are key when soldering to achieve a professional finish.
Quick-Connect Fittings: These fittings offer a convenient and versatile solution for fuel line connections. Quick-connect fittings typically feature a barbed design with an O-ring or gasket for a secure seal. They are easy to install and provide a reliable connection without the need for specialized tools. Simply insert the fuel line into the fitting, ensuring proper alignment, and then tighten the coupling nut. Quick-connect fittings are ideal for applications where frequent disconnection and reconnection are required, such as in racing or recreational vehicles. However, they may not be suitable for high-pressure or extreme temperature conditions.
Each connection method has its own set of advantages and is chosen based on the specific requirements of the fuel line installation. Crimping offers simplicity and strength, soldering provides a permanent bond, and quick-connect fittings excel in convenience and versatility. Understanding these techniques and their applications will enable you to make informed decisions when connecting fuel lines, ensuring a safe and efficient fuel delivery system.
Symmetrical Staging: Achieving Perfect Asparagus Fuel Line Balance
You may want to see also
Fuel Line Routing: Plan optimal routes to avoid damage and ensure easy access
When designing the fuel line routing for your vehicle, it's crucial to prioritize safety and accessibility. The goal is to ensure that the fuel lines are protected from potential damage while also providing easy access for maintenance and repairs. Here's a step-by-step guide to help you plan optimal routes:
- Identify Potential Hazards: Begin by assessing the vehicle's surroundings and identifying areas that could pose a risk to the fuel lines. Common hazards include engine components, suspension parts, exhaust systems, and body panels. Consider the vehicle's operating conditions, such as the terrain it will encounter, to anticipate potential impacts. For example, if your vehicle is designed for off-road use, the fuel lines might need extra protection against rocks and debris.
- Route Planning: Design a path for the fuel lines that avoids these identified hazards. Here are some key considerations:
- Ground Clearance: Ensure the fuel lines have sufficient clearance from the ground, especially in areas prone to impacts or vibrations.
- Clearance from Moving Parts: Keep the fuel lines away from suspension components, exhaust pipes, and other moving parts that could cause damage during operation.
- Body Panels and Trim: Route the lines away from body panels, trim, and any sharp edges that might come into contact with the lines during vehicle movement.
- Optimal Length: Aim for a slightly longer route to reduce stress on the lines. Longer routes can help minimize the risk of damage and provide more flexibility.
Use Protective Materials: To further safeguard the fuel lines, consider using protective materials:
- Rubber or Plastic Sleeving: Encase the fuel lines with protective sleeves made of rubber or plastic to shield them from sharp edges and potential impacts.
- Braided Steel: For high-pressure fuel lines, braided steel can provide excellent protection against damage.
- Insulation: In colder climates, insulate the fuel lines to prevent freezing and potential damage.
- Access Points: Strategically place access points along the fuel line route to facilitate maintenance and inspections. These access points should be easily reachable and well-marked. Ensure that any connections or fittings are securely fastened to prevent leaks.
- Documentation: Create detailed documentation of the fuel line routing plan, including diagrams and descriptions. This documentation will be invaluable for future maintenance, repairs, and any modifications to the vehicle's fuel system.
By following these steps, you can create a robust fuel line routing system that minimizes the risk of damage and ensures easy access for maintenance, ultimately contributing to the overall reliability of your vehicle. Remember, proper planning and protection are key to avoiding costly repairs and ensuring the longevity of your fuel system.
Mastering Holden Fuel Line Removal: A Step-by-Step Guide
You may want to see also
Fuel Line Protection: Use protective measures like insulation or shielding to prevent damage
When it comes to protecting fuel lines, especially in the context of creating fuel line ends, insulation and shielding are crucial components to ensure the longevity and reliability of your fuel system. Fuel lines are susceptible to various forms of damage, including corrosion, heat, and physical impacts, which can lead to leaks, reduced performance, and even system failures. Here's a detailed guide on how to implement protective measures for your fuel lines:
Insulation for Temperature and Corrosion Resistance: One of the primary concerns for fuel lines is the potential for corrosion and temperature-related damage. To address this, consider using specialized insulation materials designed for fuel line protection. You can wrap the fuel lines with a high-temperature-resistant insulation material, such as a heat-resistant tape or a flexible insulation sleeve. This insulation acts as a barrier, preventing direct contact between the fuel lines and harsh environmental factors. For example, if your vehicle operates in extreme temperatures or is exposed to corrosive substances, ensure that the insulation is compatible with the fuel type and can withstand the operating conditions.
Shielding against Mechanical Stress: Fuel lines are also vulnerable to mechanical stress, especially in areas where they are routed through engine compartments or under the vehicle's body. To protect against this, consider using protective sleeves or shields made from durable materials like rubber or plastic. These sleeves can be slid over the fuel lines, providing a physical barrier that absorbs impact and reduces the risk of damage from sharp edges or vibrations. For instance, if your fuel lines pass through areas with potential impact hazards, such as near exhaust pipes or under the vehicle's frame, shielding them with protective covers will add an extra layer of defense.
Customized Insulation for Specific Applications: Different fuel line configurations and applications may require tailored insulation solutions. For instance, in high-performance vehicles or those with unique fuel system designs, you might need to consult manufacturer guidelines or seek expert advice to determine the best insulation materials and techniques. Customized insulation ensures that the fuel lines are protected in the most effective way possible, considering the specific challenges of your vehicle's fuel system.
Regular Inspection and Maintenance: While protective measures are essential, regular maintenance and inspections are equally vital. Periodically check the fuel lines for any signs of damage, wear, or insulation displacement. Look for cracks, brittleness, or any exposed fuel line that might be rubbing against other components. Early detection can prevent further damage and ensure that your fuel system remains reliable. Additionally, when working on fuel line repairs or modifications, always ensure that the protective insulation and shielding are properly re-installed to maintain the integrity of the fuel system.
By implementing these protective measures, you can significantly enhance the durability and reliability of your fuel lines, especially when creating fuel line ends. Insulation and shielding provide a robust defense against various environmental and mechanical threats, ensuring that your fuel system operates efficiently and safely. Remember, proper protection is a critical aspect of vehicle maintenance, contributing to overall performance and longevity.
Subaru Fuel Line Maintenance: Tips for Smooth Running
You may want to see also
Fuel Line Testing: Conduct pressure and leak tests to ensure the integrity of the fuel line ends
Fuel line testing is a critical step in ensuring the safety and reliability of any fuel-powered system. When it comes to fuel line ends, proper testing is essential to verify their integrity and prevent potential issues. Here's a comprehensive guide on how to conduct pressure and leak tests for fuel line ends:
Pressure Testing:
- Prepare the Test Setup: Gather the necessary equipment, including a pressure gauge, a calibrated test vessel, and a source of compressed air or gas. Ensure the test vessel is clean and dry to avoid any contamination.
- Connect the Fuel Line: Securely attach the fuel line ends to the test setup. Use appropriate fittings and ensure a tight connection to minimize the risk of leaks.
- Apply Pressure Gradually: Start by applying a low pressure to the fuel line and gradually increase it. Monitor the pressure gauge to observe any changes. The goal is to simulate real-world operating conditions and identify any weaknesses in the fuel line ends.
- Check for Leaks: During the pressure test, inspect the fuel line ends for any signs of leakage. Look for visual indicators like drips or bubbles, and also listen for hissing sounds. Ensure that the fuel line ends are tightly sealed to prevent any fuel loss.
- Record Results: Document the pressure levels and any observed leaks. Note the time taken to reach specific pressure milestones. This data will help in analyzing the performance of the fuel line ends.
Leak Testing:
- Visual Inspection: Begin with a thorough visual inspection of the fuel line ends. Look for any visible damage, cracks, or deformities that could potentially cause leaks. Pay attention to areas where connections are made.
- Bubble Test: Fill the test vessel with a suitable liquid, such as water or a non-reactive fluid. Submerge the fuel line ends and observe if any bubbles form. Bubbles indicate the presence of air or fuel leaks.
- Smoke Test: Use a non-flammable smoke or fog machine to introduce a fine mist into the fuel line. Inspect the fuel line ends for any smoke or fog escaping, which would signify a leak.
- Pressure Decay Test: After the initial pressure test, perform a pressure decay test. Release the pressure gradually and monitor it over time. Any significant drop in pressure indicates a potential leak.
- Data Analysis: Compare the test results with the manufacturer's specifications and industry standards. Ensure that the fuel line ends meet the required leak-free standards.
By following these testing procedures, you can effectively evaluate the quality and reliability of fuel line ends. Regular testing is crucial, especially when dealing with fuel systems, as it helps identify potential issues before they lead to costly repairs or safety hazards. Remember, proper testing ensures the longevity and performance of your fuel-powered equipment.
Understanding Fuel Line Sizes for Your Long 460 Engine
You may want to see also
Frequently asked questions
You will need a fuel line cutter or a pair of sharp scissors or knives, a fuel line crimping tool or a crimping die, and a variety of fuel line fittings such as quick-connects, barbed fittings, or flare fittings, depending on your specific application.
Measure the desired length of the fuel line, ensuring there is enough extra length to allow for crimping or connecting the fitting. Use the fuel line cutter to make a clean cut, being careful not to damage the inner diameter of the line.
It is generally not recommended to reuse a fitting if the end is damaged. Fuel line fittings are designed for one-time use, and reusing them may compromise the integrity of the connection, leading to potential fuel leaks or system failures. It's best to replace the fitting in such cases.
Crimping involves inserting the fuel line into the fitting and then using the crimping tool to apply pressure and create a secure connection. Ensure the line is clean and free of debris. Follow the manufacturer's instructions for the specific fitting you are using, as crimping techniques may vary.
Clean the fuel line and fitting ends thoroughly to remove any contaminants. Apply a thin layer of fuel line adhesive or tape to the fitting and line, if required. Crimp or connect the fitting securely, ensuring it is tight and free of any gaps. Test the connection by applying pressure and checking for leaks.