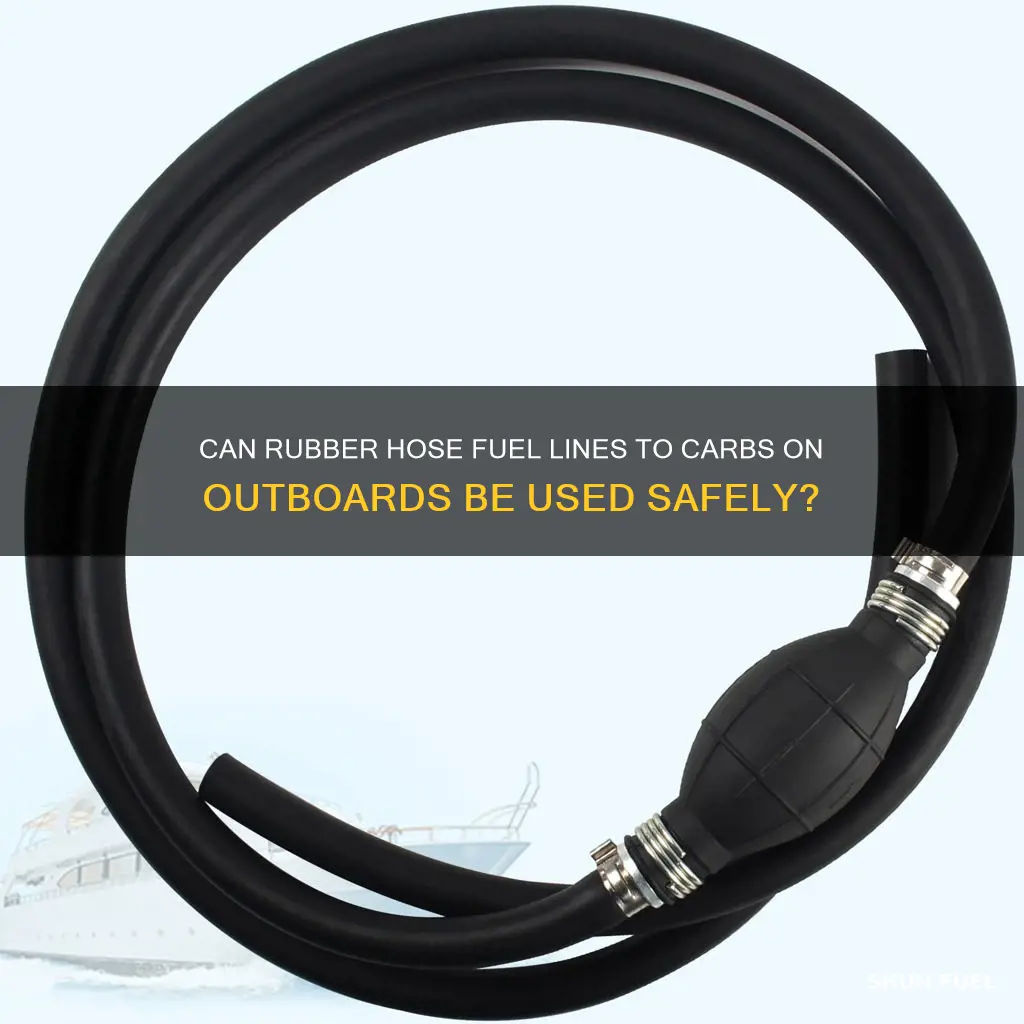
When it comes to outboard engines, the fuel lines connecting the fuel tank to the carburetor can be a critical component. Traditionally, these fuel lines were made of rigid metal or flexible metal-reinforced rubber. However, some enthusiasts and DIYers have wondered if rubber hoses can be used as an alternative. This question arises from the desire to simplify the fuel system, reduce weight, and potentially improve performance. The debate centers around the suitability of rubber hoses for fuel lines, considering factors such as flexibility, durability, and the potential for fuel leaks. This discussion aims to explore the pros and cons of using rubber hoses in this specific application.
Characteristics | Values |
---|---|
Material | Rubber |
Compatibility | Outboard Carburetor Systems |
Durability | Resistant to fuel, oil, and weather |
Flexibility | Allows for easy installation and movement |
Temperature Range | Suitable for various temperatures |
Pressure Rating | Designed to handle fuel pressure |
Color | Varies (black, blue, red) |
Length | Customizable or pre-cut lengths available |
Ease of Installation | Straightforward process |
Maintenance | Regular inspection and cleaning recommended |
Cost | Generally affordable |
What You'll Learn
- Material Compatibility: Rubber hoses can be used for fuel lines to carbs on outboards, but ensure compatibility with fuel type
- Pressure Resistance: Rubber hoses should withstand fuel pressure and temperature changes without cracking or leaking
- Flexibility: Flexibility is crucial for rubber hoses to accommodate engine movement and vibrations
- Durability: Choose durable rubber hoses that can withstand marine environments and UV exposure
- Installation: Proper installation techniques ensure a secure and leak-free connection between fuel lines and carbs
Material Compatibility: Rubber hoses can be used for fuel lines to carbs on outboards, but ensure compatibility with fuel type
When it comes to fuel lines for outboard engines, the choice of material is crucial for optimal performance and longevity. While rubber hoses are commonly used, it's essential to understand the nuances of material compatibility, especially when dealing with different fuel types.
Rubber hoses have been a popular choice for fuel lines due to their flexibility and ease of installation. They are generally durable and can withstand the rigors of marine environments. However, the compatibility of rubber with the fuel type is a critical factor. Different fuels, such as gasoline, ethanol blends, or marine diesel, can have varying effects on rubber. For instance, ethanol-blended fuels can be more corrosive to certain types of rubber, leading to potential degradation over time. Therefore, it is imperative to select the appropriate rubber compound that can withstand the specific fuel being used.
The key to ensuring material compatibility is to consider the fuel's properties and the hose's intended purpose. For outboard engines, the fuel lines need to handle the pressure and temperature variations associated with the engine's operation. Some rubber compounds are more resistant to fuel degradation and can maintain their structural integrity over a wider range of conditions. For example, natural rubber hoses are known for their flexibility and resistance to gasoline, making them suitable for standard fuel lines. On the other hand, synthetic rubber compounds, such as neoprene or butyl, offer enhanced resistance to fuel-related degradation, making them ideal for applications involving ethanol-blended fuels or marine diesel.
When selecting rubber hoses, it is advisable to consult the engine manufacturer's guidelines or specifications. These resources can provide valuable insights into the recommended materials and compatibility considerations for a particular outboard engine model. Additionally, understanding the fuel system's design and the specific requirements of the carburetor can help in choosing the right hose size and configuration to ensure a reliable fuel supply.
In summary, while rubber hoses are a viable option for fuel lines on outboards, the choice should be made with careful consideration of material compatibility. The type of fuel being used is a critical factor, as it can influence the hose's performance and durability. By selecting the appropriate rubber compound, outboard engine owners can ensure a reliable and efficient fuel supply while maintaining the overall health of their marine equipment.
Fuel Line Installation: A Step-by-Step Guide for Beginners
You may want to see also
Pressure Resistance: Rubber hoses should withstand fuel pressure and temperature changes without cracking or leaking
When it comes to fuel lines for outboard engines, the choice of material is crucial for ensuring optimal performance and longevity. Rubber hoses, while commonly used, require careful consideration regarding their ability to withstand the demanding conditions of fuel systems. One of the primary concerns is pressure resistance, as fuel lines must handle the force exerted by the engine's fuel pump without compromising their integrity.
Rubber hoses are generally flexible and lightweight, making them suitable for routing through tight spaces within an outboard engine. However, their performance under pressure is a critical factor. Over time, fuel pressure can cause rubber to degrade and become brittle, leading to potential cracking or failure. This is especially critical in high-performance engines where fuel pressure may be significantly higher. To ensure pressure resistance, it is essential to select rubber hoses with a reinforced construction, often featuring layers of fabric or steel wire to provide additional strength. These reinforcements help distribute the fuel pressure evenly, preventing localized stress and potential leaks.
Temperature changes also play a significant role in the performance of rubber hoses. Fuel systems experience temperature fluctuations, especially in marine environments where engines may operate in varying weather conditions. Rubber hoses should be able to withstand these temperature extremes without becoming brittle or losing their flexibility. A common solution is to use hoses with a synthetic rubber compound that offers improved temperature resistance compared to standard natural rubber. This ensures that the hoses remain pliable and resistant to cracking, even when exposed to hot or cold fuel temperatures.
In addition to material selection, proper installation and maintenance are vital to maintaining pressure resistance. Hoses should be securely fastened and supported to prevent excessive bending or stress. Regular inspections can help identify any signs of wear and tear, allowing for timely replacement before pressure-related issues arise. It is also recommended to use fuel system additives that provide lubrication and protection to the rubber hoses, further enhancing their durability.
By understanding the challenges posed by pressure and temperature variations, outboard engine owners can make informed decisions when choosing fuel lines. Selecting the right materials, such as reinforced rubber hoses, and implementing proper installation practices will contribute to a reliable and efficient fuel system, ensuring the engine's performance and longevity.
Visual Guide: Understanding the Appearance of a Fuel Line Clamp
You may want to see also
Flexibility: Flexibility is crucial for rubber hoses to accommodate engine movement and vibrations
Flexibility is an essential characteristic of rubber hoses used in fuel lines for outboard engines with carburetors. The primary role of these hoses is to facilitate the transfer of fuel from the tank to the carburetor while being able to withstand the dynamic nature of the engine's operation. Rubber hoses offer a unique advantage here due to their inherent flexibility, which is crucial for several reasons.
Firstly, outboard engines are designed to move, especially when navigating through water or experiencing wave action. This movement can cause the engine components to shift and vibrate. Rubber hoses, with their elastic properties, can absorb and distribute these vibrations, ensuring that the fuel supply remains stable and uninterrupted. This flexibility is vital to prevent fuel starvation, which could lead to engine misfires, stalling, or even damage.
Secondly, the design of outboard engines often incorporates various mounting points and brackets to secure components. These mounting systems can impose additional stress on the fuel lines, especially during acceleration or when the engine is under load. Rubber hoses, being flexible, can bend and adjust to these mounting constraints without compromising the fuel flow. This adaptability ensures that the fuel lines remain intact and functional, even in tight or unconventional engine mounting configurations.
Furthermore, the flexibility of rubber hoses allows for easier installation and maintenance. When connecting the fuel lines to the carburetor and other engine components, the hoses can conform to the available space, making the setup process more manageable. This ease of installation is particularly beneficial for boat owners or mechanics who may need to replace or repair the fuel lines regularly due to wear and tear or accidental damage.
In summary, the flexibility of rubber hoses is a critical factor in ensuring the reliable operation of outboard engines with carburetors. It accommodates engine movement, reduces the risk of fuel-related issues, and simplifies the installation process. When selecting or designing fuel lines for these applications, the use of flexible rubber hoses is highly recommended to maximize performance and longevity.
Understanding the Car's Fuel Line: A Comprehensive Guide
You may want to see also
Durability: Choose durable rubber hoses that can withstand marine environments and UV exposure
When it comes to marine applications, the choice of fuel lines is crucial for ensuring optimal performance and longevity. Rubber hoses are a popular option for connecting fuel lines to carbs on outboard motors, but it's essential to select the right type to withstand the harsh marine environment. Durability is a key factor to consider, as these hoses will be exposed to various elements, including UV radiation from the sun, saltwater, and potential impact from waves or boat movement.
Marine environments are particularly challenging for rubber hoses due to the corrosive nature of saltwater and the intense UV rays that can degrade materials over time. Therefore, it is imperative to choose a rubber hose specifically designed to resist these conditions. Look for hoses made from high-quality, UV-resistant rubber compounds that can maintain their flexibility and integrity even in direct sunlight. Some manufacturers offer hoses treated with additives to enhance their resistance to UV damage, ensuring they remain durable over extended periods.
The choice of rubber hose should also consider the flexibility required for the application. Marine environments can be unpredictable, with sudden changes in direction and movement. A durable rubber hose should offer a good balance between flexibility and rigidity to accommodate these movements without compromising its structural integrity. This is especially important in areas where the hose might be subjected to additional stress, such as near the engine or in areas prone to vibration.
In addition to UV resistance, the hose should be able to withstand the chemical properties of fuel and engine oils. Marine fuels often contain additives that can accelerate the degradation of certain rubber compounds. Therefore, it is advisable to choose hoses made from materials that are resistant to fuel degradation, ensuring a longer lifespan for the fuel lines. This might involve selecting hoses with specific chemical resistance ratings or those designed explicitly for marine fuel applications.
Lastly, proper installation and maintenance are essential to maximize the durability of rubber hoses. Ensure that the hoses are securely fastened and protected from physical damage during installation. Regularly inspect the hoses for any signs of wear and tear, especially in areas where they are most susceptible to damage, such as bends or connections. Timely replacement of worn-out hoses will help maintain the overall performance and reliability of the outboard motor's fuel system.
Fuel Line Removal: A Tool-Free Guide to Success
You may want to see also
Installation: Proper installation techniques ensure a secure and leak-free connection between fuel lines and carbs
When connecting fuel lines to carbs on an outboard engine, it is crucial to use the correct materials and follow proper installation techniques to ensure optimal performance and prevent leaks. While rubber hoses are commonly used for fuel lines, it is essential to understand the specific requirements and best practices for this application.
The first step in installation is to inspect the fuel lines and carbs for any signs of damage or wear. Look for cracks, punctures, or any other defects that could compromise the integrity of the system. If any issues are found, replace the affected parts immediately. Ensure that the fuel lines are free of any kinks or bends that could restrict flow or cause damage during installation.
Next, prepare the fuel lines and carbs by cleaning them thoroughly. Remove any old fuel, debris, or contaminants that may be present. This step is crucial to ensure a clean and secure connection. Use a suitable cleaner and follow the manufacturer's instructions for the best results. Rinse the lines and carbs thoroughly to remove any residue.
Now, it's time to connect the fuel lines to the carbs. Start by identifying the correct fuel line ports and carb fittings. Match the fuel line sizes to the corresponding carb fittings for a proper fit. Insert the fuel line into the port, ensuring it is aligned correctly. Use a fuel line clamp or fitting to secure the line in place. Tighten the clamp or fitting securely, but be careful not to overtighten, as this can damage the fuel line.
For a more permanent solution, consider using fuel line connectors or fittings specifically designed for outboard engines. These connectors often feature a quick-connect design, making installation faster and easier. Ensure that the connectors are compatible with the fuel line material and size. Follow the manufacturer's instructions for proper installation and tightening. Regularly inspect and maintain these connections to prevent leaks over time.
In summary, proper installation techniques are vital for a secure and leak-free connection between fuel lines and carbs on an outboard engine. By following these steps, you can ensure optimal fuel delivery and engine performance. Remember to use the correct materials, inspect for damage, clean the components, and secure the connections properly. Regular maintenance and inspections will also help identify and address any potential issues, ensuring the longevity of your outboard engine's fuel system.
E85 Fuel Line: Choosing the Right Option for Your Engine
You may want to see also
Frequently asked questions
Yes, rubber hoses can be used for fuel lines on outboard motors, but it's important to choose the right type of rubber hose for the application. Marine-grade rubber hoses are commonly used and are designed to withstand the harsh marine environment, including exposure to fuel, oil, and UV light. These hoses are typically reinforced with braided materials to provide strength and flexibility.
Rubber hoses offer several benefits. They are lightweight, flexible, and easy to install, making them a convenient choice for outboard motors. Rubber hoses can absorb vibrations and reduce engine noise, providing a smoother running experience. Additionally, they are cost-effective and widely available, making them a popular choice for boat owners.
When choosing rubber hoses, it's crucial to consider the fuel type and pressure. Different fuels have varying properties, and the hose should be compatible with the specific fuel being used. Check the pressure rating of the hose to ensure it can handle the fuel pressure in your outboard motor. It's also advisable to select a hose with a suitable inner diameter to ensure proper fuel flow.
The replacement interval for rubber fuel hoses depends on various factors, including the motor's usage, environmental conditions, and the quality of the hose. As a general guideline, it's recommended to inspect the hoses regularly for any signs of wear, cracking, or damage. If the hoses show signs of deterioration or if the motor is used frequently in harsh conditions, consider replacing them every 5-10 years or as advised by the motor manufacturer. Regular maintenance and timely replacements will ensure optimal performance and prevent potential fuel-related issues.