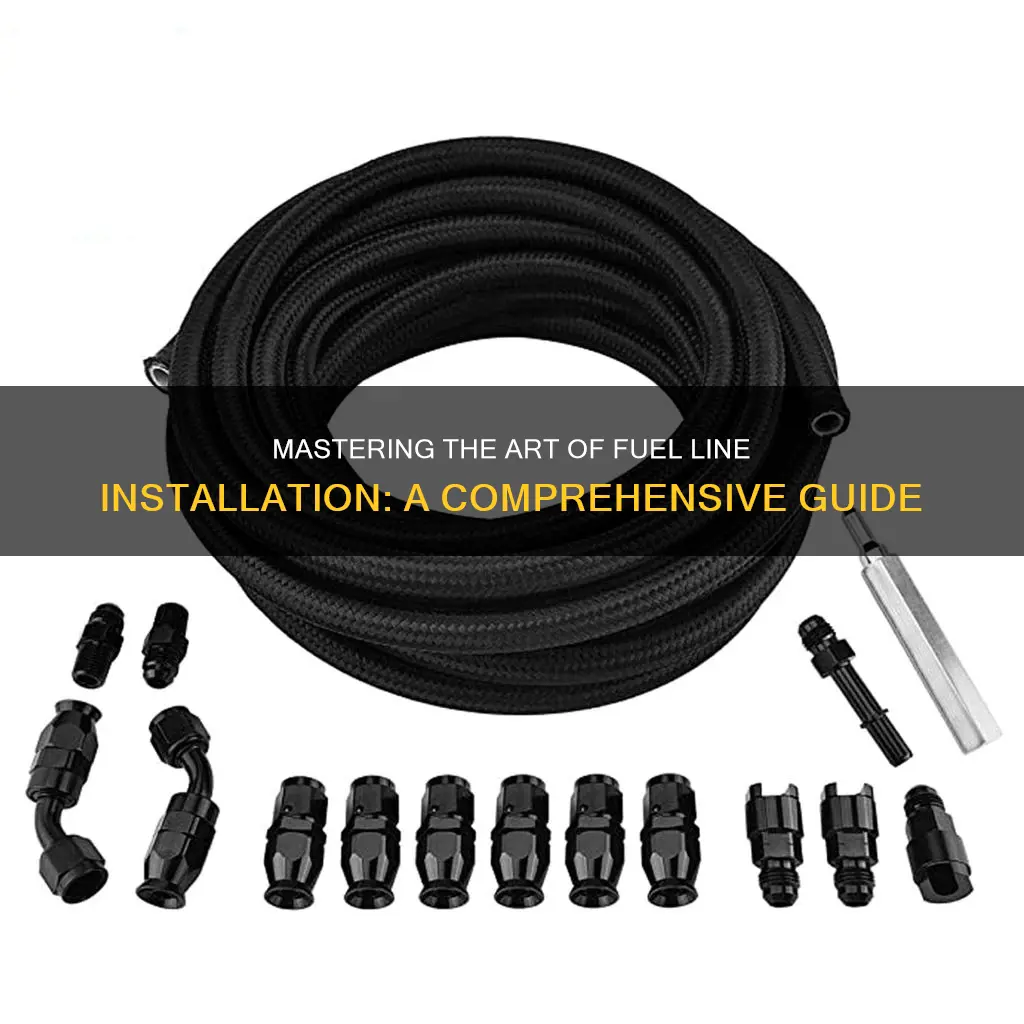
Making a fuel line for an LS engine can be a rewarding project for any car enthusiast. It involves careful preparation and attention to detail to ensure the fuel line is properly installed and functions efficiently. This guide will provide a step-by-step process, covering everything from choosing the right materials to soldering and testing the fuel line to ensure it's ready for your LS engine.
What You'll Learn
- Materials and Tools: Gather necessary supplies like fuel line, connectors, and crimping tools
- Preparation: Clean and inspect the fuel line and engine connections for damage
- Installation: Route the fuel line carefully, ensuring it's secure and free of kinks
- Testing: Check for leaks and proper fuel flow using a pressure gauge
- Maintenance: Regularly inspect and replace fuel lines to prevent issues
Materials and Tools: Gather necessary supplies like fuel line, connectors, and crimping tools
To begin the process of creating a fuel line for your LS engine, it's crucial to gather the right materials and tools. Here's a detailed breakdown of what you'll need:
Materials:
- Fuel Line: The primary component is the fuel line itself, which should be compatible with your LS engine's specifications. Ensure it's made from high-quality materials that can withstand fuel pressure and temperature variations.
- Connectors: You'll require fuel line connectors to join the fuel line to the engine's fuel rail, pump, or other components. Choose connectors that are compatible with your fuel line diameter and have a secure sealing mechanism.
- Hose Clamps: These are essential for securing the fuel line to the engine bay and preventing any potential leaks. Get a set of hose clamps that fit your fuel line size.
- Fuel Filter (Optional): If you plan to filter the fuel before it reaches the engine, consider adding a fuel filter to your setup.
Tools:
- Crimping Tool: A crimping tool is a must-have for this project. It allows you to securely connect the fuel line to the connectors. Ensure you have a tool that can handle the connector type you've chosen.
- Pliers: Standard pliers will be useful for adjusting and holding components while you work.
- Fuel Line Cutter: This tool will help you cut the fuel line to the desired length, ensuring a precise fit.
- Tape Measure: For accurate measurements of the fuel line length.
- Safety Gear: Don't forget to wear safety gloves and goggles to protect yourself during the process.
Having all these materials and tools ready will ensure a smooth and efficient fuel line installation process. It's essential to double-check compatibility and specifications for each component to guarantee a reliable and safe fuel system for your LS engine.
Mastering the Art of GM Plastic Fuel Line Removal: A Step-by-Step Guide
You may want to see also
Preparation: Clean and inspect the fuel line and engine connections for damage
Before you begin the process of modifying or replacing your fuel line, it is crucial to ensure that the existing setup is in optimal condition. Start by thoroughly cleaning the fuel line to remove any built-up contaminants, such as fuel residue, dirt, or debris. This step is essential as it helps prevent any potential issues that may arise from using a contaminated fuel line. You can use a fuel line cleaner, which is typically a solvent-based product designed to dissolve and remove these substances. Apply the cleaner according to the manufacturer's instructions, allowing sufficient time for it to work its way through the line. After cleaning, rinse the fuel line to eliminate any remaining cleaner and ensure a fresh start.
In addition to cleaning, a comprehensive inspection is necessary. Carefully examine the fuel line for any signs of damage, such as cracks, leaks, or corrosion. Inspect the connections between the fuel line and the engine as well. Look for any loose fittings, damaged O-rings, or signs of wear and tear. These connections are critical to the proper functioning of the fuel system, and any issues here can lead to fuel leaks or reduced performance. If you notice any damage, it is imperative to replace the affected parts to ensure the safety and efficiency of your engine.
When inspecting the engine connections, pay close attention to the fuel pump and its wiring. The fuel pump is responsible for delivering fuel to the engine, and any damage or malfunction can result in poor performance or even engine failure. Check for any signs of corrosion or damage to the wiring harness and ensure that all connections are secure and intact. It is also a good practice to test the fuel pump's functionality using a multimeter to ensure it is delivering the correct voltage and current.
By taking the time to clean and inspect the fuel line and engine connections, you are performing a vital step in the preparation process. This ensures that any potential issues are identified and addressed before proceeding with the modification or replacement, ultimately contributing to a smoother and more successful outcome. Remember, a well-prepared fuel system is the foundation for a reliable and efficient engine.
Dodge 1500 Fuel Line Removal: A Step-by-Step Guide
You may want to see also
Installation: Route the fuel line carefully, ensuring it's secure and free of kinks
When installing a fuel line for your LS engine, proper routing is crucial to ensure optimal performance and reliability. Here's a detailed guide on how to route the fuel line carefully and securely:
Planning the Route: Begin by studying your engine bay layout and identifying the optimal path for the fuel line. Consider the location of the fuel pump, the fuel tank, and the engine's various components. Aim for a route that minimizes sharp bends and potential stress points. Plan the path to ensure it doesn't interfere with other engine parts or components that could cause damage or restrict flow.
Materials and Tools: Gather the necessary tools and materials, including the fuel line itself, fittings, clamps, and any required adapters. Ensure you have the correct size and type of fuel line for your LS engine to match the specifications.
Routing Process: Start by attaching the fuel line to the fuel pump using the appropriate fitting. Securely fasten it with a clamp to prevent movement. Then, carefully guide the line through the engine bay, following your planned route. Take note of any potential obstacles or areas where the line might need to be bent around. Use the appropriate tools to carefully bend the fuel line without causing damage or kinks. Ensure that the line is not pinched or compressed, as this can restrict fuel flow.
Securing the Line: As you route the fuel line, secure it at regular intervals using clamps or ties. This prevents the line from becoming loose or causing interference with other components. Ensure that the line is taut and free-flowing, with no sharp bends that could lead to fuel restriction or potential leaks.
Final Checks: Once the fuel line is routed and secured, perform a thorough inspection. Check for any kinks, sharp bends, or areas of compression. Ensure that all connections are tight and secure. Verify that the fuel line is not touching any hot surfaces or engine components that could cause damage. Test the fuel system to ensure proper fuel flow and pressure.
Remember, proper routing and installation are critical to the performance and longevity of your LS engine's fuel system. Take the time to plan and execute the installation carefully to avoid potential issues.
Mastering the Art of Fuel Line Removal: A Step-by-Step Guide
You may want to see also
Testing: Check for leaks and proper fuel flow using a pressure gauge
When it comes to testing your fuel line setup, ensuring there are no leaks and proper fuel flow is crucial. This step is often overlooked, but it's essential to verify the integrity of your fuel system before taking your modified vehicle out for a spin. Here's a detailed guide on how to test your fuel line setup using a pressure gauge:
Gather the Tools and Materials:
You'll need a few essential tools for this test: a pressure gauge, a fuel pump tester (if applicable), and a container to collect fuel samples. Ensure you have the correct gauge for your fuel system's pressure range. It's also a good idea to wear protective gear, such as gloves and safety goggles, to avoid any potential fuel-related hazards.
Step 1: Check for Leaks:
Start by inspecting the fuel line connections and fittings. Look for any signs of damage, corrosion, or loose fittings. Use a soapy water solution and carefully inspect the entire length of the fuel line. Even a small crack or bubble can lead to significant issues. If you spot any leaks, tighten the fittings or consider replacing the affected section of the fuel line.
Step 2: Prime the Fuel System:
Turn on the fuel pump and allow it to prime the system. This process ensures that the fuel is distributed evenly throughout the line. Listen for any unusual noises, and check for proper fuel flow at various points along the line. If you have a fuel pump tester, use it to verify the pump's functionality and flow rate.
Step 3: Apply Pressure:
Connect the pressure gauge to the fuel line, ensuring a secure and tight connection. Turn on the fuel pump again and observe the gauge reading. The pressure should stabilize at a specific value, depending on your fuel system's design. If the pressure drops significantly or fluctuates, it indicates a potential issue with the fuel line or pump.
Step 4: Check for Proper Fuel Flow:
While monitoring the pressure, observe the fuel flow rate. A properly functioning fuel line should deliver fuel at a consistent rate. If the flow seems inconsistent or weak, it could be due to a restriction or blockage in the line. In such cases, you might need to clean or replace the affected section of the fuel line.
Step 5: Document and Verify:
Record the pressure and flow rates you've measured. Compare these values with the expected specifications for your vehicle's fuel system. If everything is within the acceptable range, you've successfully tested for leaks and proper fuel flow. However, if any issues are detected, further investigation and potential repairs are necessary before you can safely operate your modified vehicle.
Remember, thorough testing is vital to ensure the safety and performance of your modified engine. By following these steps and paying close attention to detail, you can identify and address any fuel line-related problems before they cause unexpected issues on the road.
Tygon Fuel Line: Top Sources for Purchase
You may want to see also
Maintenance: Regularly inspect and replace fuel lines to prevent issues
Regular maintenance of fuel lines is crucial to ensure optimal performance and longevity of your vehicle's fuel system. Over time, fuel lines can deteriorate due to various factors, including age, exposure to heat and chemicals, and general wear and tear. Neglecting this maintenance can lead to fuel leaks, reduced engine performance, and even potential safety hazards. Therefore, it is essential to establish a routine for inspecting and replacing fuel lines to keep your vehicle running smoothly and efficiently.
Start by familiarizing yourself with the location of the fuel lines in your vehicle. Fuel lines are typically made of rubber or synthetic materials and are responsible for transporting fuel from the tank to the engine. They are often located beneath the vehicle, along the frame, and near the engine compartment. Inspecting these lines regularly can help identify any signs of damage or deterioration. Look for cracks, brittleness, soft spots, or any visible signs of corrosion. Also, check for any signs of fuel leakage, which could indicate a damaged or worn-out fuel line.
During your inspections, pay close attention to the connections between the fuel lines and other components, such as the fuel pump, engine, and tank. These connections should be secure and free from any signs of corrosion or damage. Over time, these connections can loosen or corrode, leading to fuel leaks and potential engine issues. Tighten any loose connections and consider using thread seal tape or pipe dope to prevent further corrosion.
If you notice any issues during your inspections, it is best to replace the affected fuel lines promptly. Worn-out or damaged fuel lines can lead to fuel leaks, which may cause engine misfires, reduced power, and even potential fire hazards. When replacing fuel lines, ensure you use high-quality replacement parts that are compatible with your vehicle's make and model. Properly secure the new fuel lines and ensure all connections are tight and corrosion-free.
In addition to visual inspections, consider using a fuel pressure gauge to check the pressure in the fuel lines. Low fuel pressure can indicate a restricted or damaged fuel line, which may require replacement. Regularly replacing fuel lines as part of your vehicle's maintenance routine will help prevent unexpected breakdowns and ensure your engine receives the correct amount of fuel for optimal performance. Remember, proper maintenance can save you from costly repairs and keep your vehicle running reliably for years to come.
Backflushing Fuel Lines: A DIY Guide to Unclogging Tank Screens
You may want to see also
Frequently asked questions
Creating a fuel line for an LS engine, which is a popular upgrade for Chevrolet's small-block V8, is essential for optimizing fuel delivery and performance. It allows for a more efficient and reliable fuel system, ensuring that the engine receives the correct amount of fuel at the right pressure, resulting in improved power output and overall engine health.
The fuel line size depends on various factors, including the engine's displacement, compression ratio, and desired power level. Generally, larger displacement LS engines benefit from larger fuel lines to accommodate higher fuel flow rates. It's recommended to consult the engine manufacturer's guidelines or seek advice from experienced tuners to determine the appropriate fuel line diameter for your specific build.
While it is possible to use standard fuel lines, it is not ideal for optimal performance. LS engines often require high-flow fuel lines to handle the increased fuel demand, especially when coupled with modifications like larger injectors or performance upgrades. Using standard fuel lines may lead to fuel pressure issues and reduced power, so it's best to invest in a dedicated high-flow fuel line designed for LS engines.
Fuel lines for LS engines are typically made from high-quality materials such as stainless steel or aluminum. Stainless steel is popular due to its durability and resistance to corrosion, making it suitable for high-performance applications. Aluminum fuel lines are also used, offering a lightweight alternative, but they may require more frequent maintenance due to their susceptibility to oxidation.