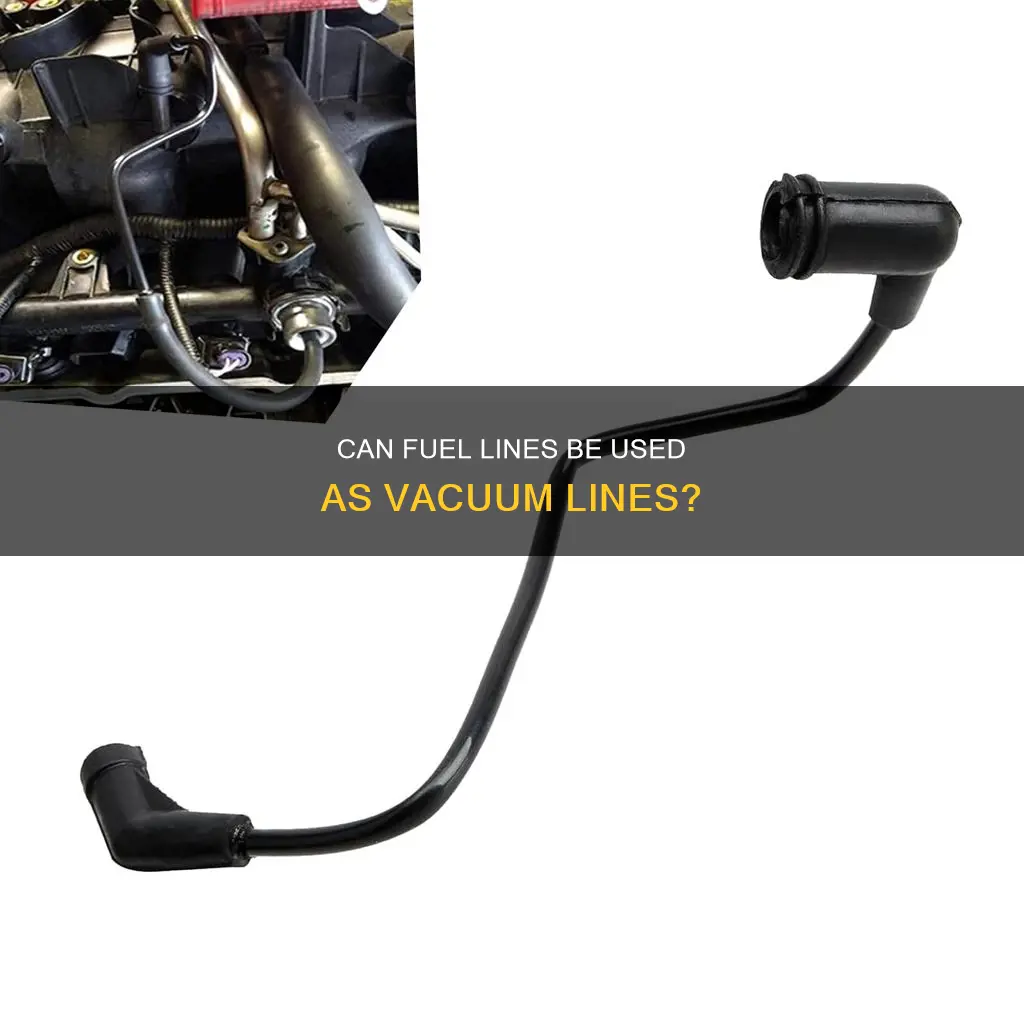
Can a fuel line be used as a vacuum line? This question often arises in discussions about vehicle maintenance and performance. While both fuel lines and vacuum lines serve critical functions in an engine's operation, they are designed for different purposes. Fuel lines are specifically engineered to transport gasoline or diesel from the tank to the engine, ensuring a steady and controlled supply of fuel. On the other hand, vacuum lines are responsible for creating a vacuum to control the engine's intake and exhaust systems, allowing for precise regulation of air-fuel mixtures. Understanding the differences between these two types of lines is essential for proper vehicle maintenance and troubleshooting.
Characteristics | Values |
---|---|
Material | Plastic, rubber, metal |
Diameter | Varies, typically 1/4" to 1" |
Pressure Rating | Depends on the specific fuel line, can range from low to high pressure |
Temperature Range | Varies, can handle hot or cold environments |
Flexibility | Can be flexible or rigid |
Compatibility | May require modifications for certain applications |
Cost | Generally more expensive than standard vacuum lines |
Availability | Widely available in automotive and industrial supply stores |
Installation | Requires careful fitting and sealing to prevent leaks |
Maintenance | Regular inspection and replacement may be necessary |
Safety | Fuel lines must meet safety standards and regulations |
What You'll Learn
- Material Compatibility: Check if fuel line material is suitable for vacuum applications
- Pressure Requirements: Ensure fuel line can withstand vacuum pressures without failure
- Flexibility: Evaluate if fuel line's flexibility meets vacuum line's bending needs
- Temperature Tolerance: Confirm fuel line can handle vacuum system temperatures
- Installation Techniques: Learn proper methods for connecting fuel line to vacuum ports
Material Compatibility: Check if fuel line material is suitable for vacuum applications
When considering the use of fuel lines in vacuum applications, material compatibility is a critical factor to ensure the system's reliability and performance. The primary concern is whether the material of the fuel line can withstand the unique challenges posed by the vacuum environment without compromising its structural integrity or functionality.
Vacuum systems operate under low-pressure conditions, which can lead to rapid material degradation if the fuel line is not compatible. Certain materials, such as rubber or plastic, may not be suitable for vacuum use due to their tendency to become brittle and crack under reduced pressure. These materials can also absorb moisture from the vacuum environment, leading to potential performance issues.
To ensure compatibility, it is essential to select a fuel line material that can maintain its flexibility, strength, and chemical resistance in a vacuum. Materials like silicone, fluoropolymers (such as PTFE or FEP), or specialized vacuum-grade hoses are often preferred. These materials offer excellent resistance to temperature changes, moisture absorption, and chemical corrosion, making them ideal for vacuum applications.
Additionally, the design and construction of the fuel line should consider factors like vacuum pressure, temperature range, and the presence of corrosive gases or vapors. Proper sealing and reinforcement of the fuel line connections are crucial to prevent leaks and ensure a secure fit within the vacuum system.
In summary, when using fuel lines in vacuum applications, it is imperative to carefully evaluate the material's compatibility and its ability to withstand the specific conditions of the vacuum environment. Selecting the right material and ensuring proper design considerations will contribute to a reliable and efficient vacuum system.
Understanding the Husqvarna YTH20B42T Fuel Pump Line Connections
You may want to see also
Pressure Requirements: Ensure fuel line can withstand vacuum pressures without failure
When considering the use of fuel lines for vacuum applications, it is crucial to understand the pressure requirements and potential challenges. Fuel lines are primarily designed to transport fuel under pressure, ensuring a reliable and efficient flow to the engine. However, when it comes to vacuum lines, the pressure dynamics change significantly. Vacuum lines operate at a lower pressure than atmospheric pressure, and this difference in pressure can impact the performance and integrity of the fuel line.
The key to ensuring the compatibility of a fuel line for vacuum applications lies in its ability to withstand vacuum pressures without failure. Vacuum pressures can vary depending on the specific system and its design, but they typically range from a few inches of mercury (inHg) to around 29.5 inHg, which is equivalent to standard atmospheric pressure. Fuel lines must be capable of withstanding these lower pressures without compromising their structural integrity or allowing fuel to leak or vaporize.
To meet these pressure requirements, fuel lines should be selected based on their material properties and design specifications. High-quality fuel lines are often made from materials like rubber, silicone, or specialized polymers that offer excellent resistance to vacuum-induced stresses. These materials can maintain their shape and flexibility even under reduced pressure conditions, ensuring a reliable connection and preventing fuel leaks. Additionally, the inner diameter and wall thickness of the fuel line should be appropriate for the expected vacuum pressure, allowing for efficient fluid flow without excessive pressure drop.
During the installation process, it is essential to pay attention to the connections and fittings. Vacuum applications may require specialized fittings that can withstand the lower pressure differentials. Proper sealing and secure connections are vital to prevent any vacuum-induced leaks or failures. Regular inspections and maintenance can also help identify potential issues, ensuring that the fuel line continues to perform reliably over time.
In summary, when using fuel lines for vacuum applications, it is imperative to prioritize pressure requirements. Selecting the right materials, considering the vacuum pressure range, and ensuring proper installation and maintenance will guarantee that the fuel line can withstand the unique challenges of vacuum systems without compromising performance or safety. Understanding these pressure considerations is essential for anyone working with fuel lines in vacuum-related applications.
Leaking Fuel Line: A Hidden Cause of Low Engine Idle
You may want to see also
Flexibility: Evaluate if fuel line's flexibility meets vacuum line's bending needs
When considering the potential use of fuel lines as vacuum lines, one crucial aspect to evaluate is the flexibility of the fuel lines. Flexibility is a key requirement for vacuum lines, as they often need to be bent and manipulated to fit various shapes and sizes of equipment. The ability to bend without kinking or breaking is essential to ensure a reliable and efficient vacuum system.
Fuel lines, designed for transporting fuel, are typically made of materials that offer a certain level of flexibility. This flexibility is often achieved through the use of rubber or synthetic compounds, which can withstand the pressure and temperature variations associated with fuel. However, the flexibility of fuel lines may not always meet the specific needs of vacuum applications. Vacuum lines require a higher degree of flexibility to navigate around obstacles and accommodate the unique demands of the vacuum environment.
To assess the suitability of fuel lines for vacuum applications, it is important to consider the bending radius and the overall flexibility of the material. Vacuum lines often need to be bent at sharp angles or wrapped around complex shapes, requiring a higher level of pliability. If the fuel line's flexibility is insufficient, it may result in kinking, which can restrict the flow of vacuum and potentially damage the system. Therefore, it is crucial to choose fuel lines with the appropriate flexibility to ensure they can withstand the bending requirements of the vacuum setup.
In some cases, fuel lines may need to be flexible enough to navigate through tight spaces or around sensitive components. This is particularly important in medical or industrial vacuum systems where precision and maneuverability are essential. By evaluating the flexibility of the fuel lines, engineers can ensure that the vacuum system can be designed with the necessary adaptability to meet the specific needs of the application.
Additionally, the material composition of the fuel lines should be considered. Some materials may offer superior flexibility while maintaining the required strength and durability for vacuum applications. It is essential to choose the right material and design to ensure the fuel lines can handle the vacuum's demands without compromising performance or safety.
Choosing the Right Fuel Line Tubing: A Comprehensive Guide
You may want to see also
Temperature Tolerance: Confirm fuel line can handle vacuum system temperatures
When considering the use of fuel lines as vacuum lines, it's crucial to evaluate their temperature tolerance. Fuel lines are designed to withstand the high temperatures generated by the engine and the fuel system, which can reach up to 250°F (121°C) or more. This is essential because the vacuum system operates at much lower temperatures, typically around room temperature or slightly above, depending on the ambient conditions. Therefore, the temperature tolerance of the fuel line is a critical factor in determining its suitability for use as a vacuum line.
The temperature tolerance of a fuel line is typically specified by the manufacturer and can vary depending on the material and construction of the line. Common materials used for fuel lines include rubber, silicone, and nylon, each with its own temperature range. For example, natural rubber fuel lines may have a temperature tolerance of -40°F to 250°F (-40°C to 121°C), while silicone fuel lines can handle temperatures ranging from -65°F to 450°F (-54°C to 232°C). These temperature ratings ensure that the fuel line can withstand the extreme conditions of the fuel system without degrading or failing.
To confirm the temperature tolerance of a fuel line for use as a vacuum line, it is essential to consult the manufacturer's specifications. Look for the maximum and minimum temperature limits that the fuel line can safely operate within. This information will help you understand whether the fuel line can handle the lower temperatures of the vacuum system without compromising its integrity. Additionally, consider the duration of exposure to these temperatures, as some materials may have different tolerances for short-term versus long-term exposure.
In practice, when using a fuel line as a vacuum line, it is advisable to select a line with a temperature tolerance that is well above the expected operating temperatures of the vacuum system. This ensures a safety margin and accounts for any potential temperature fluctuations. For instance, if the vacuum system operates at temperatures around 70°F (21°C), choosing a fuel line with a temperature tolerance of 0°F to 250°F (-18°C to 121°C) would provide a suitable margin of safety.
Furthermore, it is important to consider the environmental conditions in which the vacuum system will operate. If the system is exposed to extreme cold or heat, the temperature tolerance of the fuel line becomes even more critical. In such cases, selecting a fuel line with a higher temperature rating or considering alternative materials that offer better temperature resistance may be necessary to ensure the longevity and reliability of the vacuum system.
Signs of a Clogged Fuel Line: What to Look For
You may want to see also
Installation Techniques: Learn proper methods for connecting fuel line to vacuum ports
When it comes to connecting fuel lines to vacuum ports, it's essential to follow proper installation techniques to ensure optimal performance and safety. Here's a detailed guide on how to achieve this:
Preparation: Before beginning the installation, ensure you have the correct tools and materials. You'll need the appropriate fuel line, vacuum ports, and the necessary fittings or adapters. It's crucial to inspect the fuel line for any defects or damage. Check for cracks, leaks, or any signs of deterioration. If any issues are found, replace the fuel line to prevent potential problems during operation.
Connection Process: Start by locating the vacuum port on your engine or system. These ports are typically designed to accommodate fuel lines and are often color-coded for easy identification. Carefully insert the fuel line into the vacuum port, ensuring a snug fit. Use a suitable connector or adapter to secure the connection. Tighten the fittings securely, but be cautious not to overtighten, as this can damage the fuel line or port. It's important to maintain a tight seal to prevent air leaks and ensure efficient vacuum operation.
Testing and Inspection: After the initial connection, it's vital to test the setup. Start the engine and monitor for any unusual noises or vibrations. Check for leaks around the connections to ensure they are secure. If everything appears normal, run the engine at different speeds and loads to ensure the vacuum system functions correctly. Inspect the fuel line for any signs of strain or damage during this testing phase.
Additional Tips: Consider using a vacuum gauge to measure the system's performance. This tool will help you verify the vacuum level and ensure it meets the required specifications. Additionally, when working with fuel lines, always follow the manufacturer's guidelines for the specific fuel type and engine application. Different fuels may require unique handling and connection methods.
By adhering to these installation techniques, you can effectively connect fuel lines to vacuum ports, ensuring a reliable and safe vacuum system. Remember, proper preparation, secure connections, and thorough testing are key to achieving optimal performance.
Fixing the 2005 Chevy Blazer's Fuel Line: A Step-by-Step Guide
You may want to see also
Frequently asked questions
Yes, fuel lines can be utilized as vacuum lines in certain scenarios. While fuel lines are primarily designed to transport fuel, they can also serve as a temporary vacuum source due to their ability to create a partial vacuum. However, it's important to note that fuel lines are not specifically engineered for vacuum applications and may not provide the same level of performance and reliability as dedicated vacuum hoses.
One advantage is the availability and cost-effectiveness of fuel lines. They are readily available in various sizes and materials, making it convenient for quick repairs or temporary solutions. Additionally, fuel lines are often made of flexible materials, allowing for easier routing and installation.
Yes, there are some considerations. Fuel lines may not be as durable or heat-resistant as specialized vacuum hoses, which can affect their long-term performance. They might also have a higher pressure rating, which could lead to issues if the vacuum system requires a lower pressure. Furthermore, fuel lines may contain contaminants or have a different internal surface finish, potentially impacting vacuum efficiency.
To use fuel lines as vacuum lines, you can consider modifying them to better suit the vacuum requirements. This may involve cutting and reshaping the lines, adding vacuum fittings, and ensuring proper sealing to prevent air leaks. It's crucial to test the modified lines to ensure they meet the desired vacuum levels and maintain system integrity.
While fuel lines are generally made of materials like rubber or plastic, certain compounds might offer better vacuum performance. For instance, some fuel lines use a blend of rubber and plasticizers, providing flexibility and resistance to vacuum collapse. It's recommended to consult the manufacturer's specifications or seek expert advice to determine the most suitable fuel line material for your vacuum application.