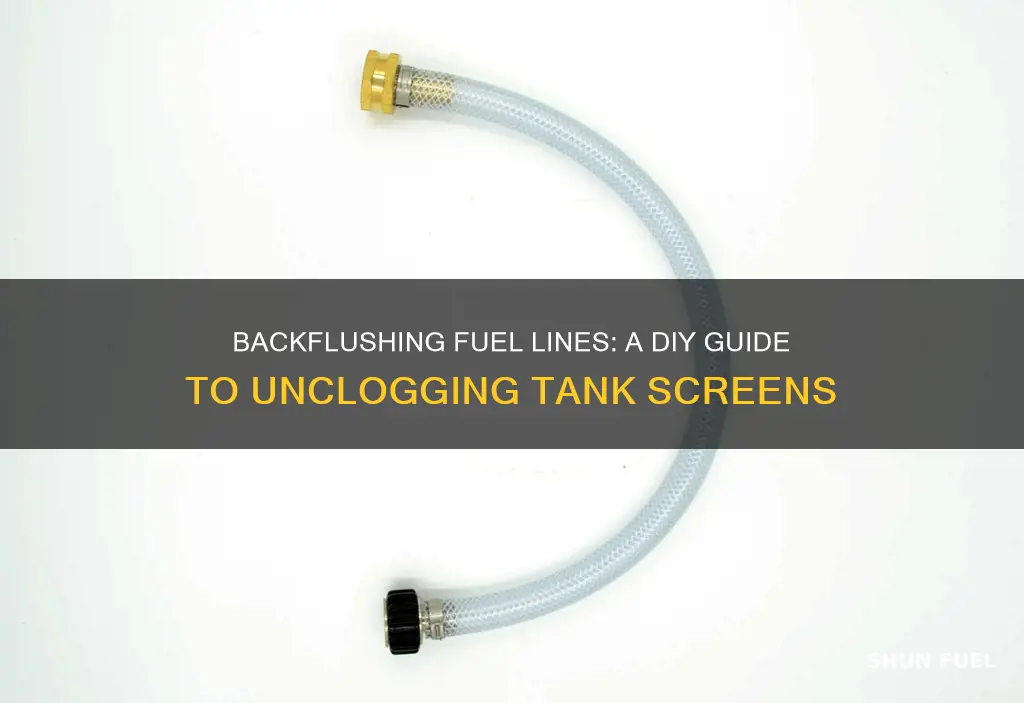
Backflushing fuel lines is a technique used to clear blockages in fuel tanks, but it's important to understand the process and its limitations. While backflushing can be effective in unclogging a tank screen, it requires careful execution and consideration of potential risks. This method involves reversing the flow of fuel through the lines to dislodge any debris or clogs. However, it's crucial to follow proper procedures and safety guidelines to avoid causing further damage or contamination. Understanding the mechanics of fuel systems and the specific requirements of your vehicle is essential before attempting any such maintenance.
Characteristics | Values |
---|---|
Method | Backflushing involves pushing fuel through the lines in reverse to dislodge blockages. |
Effectiveness | Can be effective for minor clogs but may not work for severe blockages. |
Risks | Potential for fuel to spill, damage fuel system components, or cause engine misfires. |
Tools Required | Pressure washer, fuel pump, and appropriate connectors. |
Expertise | Requires some mechanical knowledge and experience with fuel systems. |
Safety Precautions | Ensure engine is off, fuel is drained, and all safety protocols are followed. |
Alternative Solutions | Consider using a fuel filter cleaner or seeking professional assistance for complex issues. |
What You'll Learn
- Fuel Line Material Compatibility: Ensure the fuel lines are compatible with the fuel type to avoid contamination
- Backflushing Technique: Use a specific backflushing technique to clear the tank screen effectively
- Pressure and Flow Control: Control pressure and flow rate during backflushing to prevent damage
- Safety Precautions: Implement safety measures to prevent fuel spills and ensure a safe backflushing process
- Post-Backflush Inspection: Inspect the fuel lines and tank after backflushing to ensure proper clearance
Fuel Line Material Compatibility: Ensure the fuel lines are compatible with the fuel type to avoid contamination
When dealing with fuel systems, ensuring compatibility between the fuel lines and the fuel type is crucial to prevent contamination and maintain optimal performance. Different fuels have varying properties, and using the wrong type of fuel line can lead to several issues. For instance, gasoline fuel lines are typically made of materials that can withstand the volatility of gasoline, such as rubber or specific types of plastic. In contrast, diesel fuel lines require materials that can handle the higher pressure and lubricity of diesel, often using materials like steel or specific rubber compounds.
The compatibility of fuel lines is essential for several reasons. Firstly, it ensures that the fuel is not exposed to materials that could cause degradation or contamination. For example, some fuels contain additives that can react with certain plastics or rubbers, leading to fuel degradation and potential performance issues. Secondly, it helps prevent fuel leaks and potential safety hazards. Using the correct material for fuel lines ensures a tight seal, reducing the risk of fuel escaping and causing environmental damage or fire hazards.
To determine the compatibility of fuel lines, it is important to consider the fuel's properties and the line's material. Each fuel type has its own set of characteristics, including volatility, temperature sensitivity, and the presence of specific additives. For instance, ethanol-blended fuels require fuel lines made from materials that can withstand the higher ethanol content without compromising the line's integrity. Similarly, aviation fuels, which are often highly refined and contain additives, necessitate fuel lines made from materials that can resist corrosion and maintain flexibility over a wide temperature range.
When selecting fuel lines, it is advisable to consult the manufacturer's guidelines or seek expert advice. These sources can provide specific recommendations based on the fuel type and the application. Additionally, understanding the fuel system's design and the location of the fuel lines can help in choosing the most suitable materials. For instance, fuel lines in high-temperature environments may require materials with superior heat resistance, while those in areas prone to vibration might need flexible materials to withstand the movement.
In summary, ensuring the compatibility of fuel lines with the fuel type is a critical aspect of maintaining a fuel system's performance and safety. By considering the fuel's properties and selecting the appropriate materials, you can avoid contamination, prevent leaks, and ensure the overall reliability of the fuel system. This practice is especially important in applications where fuel quality and system integrity are essential, such as in aviation or high-performance automotive settings.
Mastering Harbor Freight Fuel Line Disconnect: A Comprehensive Guide
You may want to see also
Backflushing Technique: Use a specific backflushing technique to clear the tank screen effectively
Backflushing is a technique used to clear blockages in fuel lines and tanks, and it can be an effective method to unclog a tank screen. This process involves reversing the flow of fuel to dislodge any debris or contaminants that may be causing the blockage. Here's a detailed guide on how to perform this technique:
Preparation: Before you begin, ensure you have the necessary tools and safety equipment. You'll need a fuel pump, a container to collect the fuel, a length of flexible hose, and protective gear such as gloves and goggles. It is crucial to work in a well-ventilated area and to disconnect the fuel lines from the tank to prevent any accidental fuel release.
Step-by-Step Process: Start by placing the container under the fuel line to catch any fuel that flows out. Then, attach the flexible hose to the fuel pump and the other end to the fuel line, ensuring a secure connection. Turn on the fuel pump and slowly increase the pressure to create a reverse flow. The goal is to push the fuel through the line and into the tank, dislodging any blockages. Keep the process slow and controlled to avoid excessive pressure, which could damage the fuel system. As the fuel flows, you may notice a change in the sound of the pump, indicating the movement of debris.
Troubleshooting: If the backflushing process doesn't immediately clear the screen, you may need to repeat the process or adjust the technique. Consider using a higher-pressure pump or a longer hose to increase the force of the fuel flow. In some cases, you might need to remove the tank screen and clean it manually to ensure a thorough unclogging.
Safety and Maintenance: Backflushing should be done regularly to prevent the buildup of contaminants in the fuel system. It is also essential to inspect the fuel lines and tank regularly for any signs of damage or wear, especially after performing this technique. Proper maintenance will ensure the longevity of your fuel system and prevent potential issues.
Remember, when dealing with fuel systems, always prioritize safety and follow manufacturer guidelines. Backflushing can be an effective solution for clearing tank screens, but it should be done with caution and the right tools to avoid any potential hazards.
2005 Toyota Camry Fuel Line Location: A Quick Guide
You may want to see also
Pressure and Flow Control: Control pressure and flow rate during backflushing to prevent damage
Backflushing fuel lines to unclog a tank screen is a technique that can be effective, but it requires careful control of pressure and flow rate to avoid potential damage to the system. The process involves reversing the flow of fuel through the lines to dislodge any blockages, and this must be done with precision to ensure the system's integrity.
The key to successful backflushing is to maintain optimal pressure and flow conditions. If the pressure is too high, it can lead to excessive force, potentially causing damage to the fuel lines, pump, or even the tank itself. On the other hand, if the pressure is too low, the backflush may not be effective, and the blockages might remain. Therefore, it is crucial to monitor and adjust the pressure accordingly.
Flow rate also plays a critical role. A controlled and steady flow rate is essential to ensure that the fuel is moving through the lines at a consistent pace. Rapid or inconsistent flow can create turbulence, which may lead to air bubbles forming in the fuel, causing further issues. By maintaining a steady flow, you can ensure that the backflush process is thorough and effective without causing any unnecessary strain on the system.
To control pressure and flow, consider using a pressure gauge and a flow meter. These tools will allow you to measure and adjust the pressure and flow rate in real-time. Start with a low pressure and gradually increase it, monitoring the flow rate simultaneously. This gradual approach ensures that you can identify the optimal pressure and flow for your specific fuel line and tank configuration.
Additionally, consider the use of a filter or strainer in the backflush line to capture any debris or contaminants that may be dislodged during the process. This extra step can help prevent any foreign matter from re-blocking the lines or causing damage to the fuel system. By combining precise pressure and flow control with the use of filters, you can effectively backflush fuel lines while minimizing the risk of damage.
Unclipping the Ford Pink Fuel Line: A Step-by-Step Guide
You may want to see also
Safety Precautions: Implement safety measures to prevent fuel spills and ensure a safe backflushing process
Before attempting any backflushing procedure, it is crucial to prioritize safety to prevent potential hazards associated with fuel handling. Here are some essential safety precautions to follow:
- Prepare the Work Area: Ensure the work area is well-ventilated and clear of any obstacles or trip hazards. Set up containment booms or absorbent materials around the fuel tank to capture any potential spills. This step is vital to contain any fuel that might leak during the backflushing process.
- Personal Protective Equipment (PPE): Always wear appropriate PPE, including safety goggles, gloves, and a respirator mask. Fuel can be harmful if inhaled or comes into contact with the skin, so protective gear is essential. Consider wearing long sleeves and pants to minimize skin exposure.
- Ventilation and Gas Detection: Proper ventilation is critical to prevent the buildup of flammable gases. Open windows and doors to allow fresh air circulation. Additionally, use a gas detector to monitor the air for any fuel vapor accumulation. This step ensures early detection of potential hazards and allows for immediate action.
- Fuel Line Inspection: Before backflushing, inspect the fuel lines for any visible damage or blockages. Replace any damaged lines to prevent leaks during the process. Ensure all connections are secure and tight to avoid fuel escaping during the procedure.
- Slow and Controlled Process: When backflushing, use a slow and controlled approach. Apply pressure gradually to avoid sudden bursts of fuel. This technique helps prevent excessive fuel flow and reduces the risk of spills. Always maintain a steady and cautious pace throughout the process.
- Emergency Preparedness: Have a response plan ready in case of an accident. Keep a fire extinguisher nearby, and ensure you know how to use it. In the event of a fuel leak or fire, act quickly and calmly to minimize potential damage and injuries.
By implementing these safety measures, you can significantly reduce the risks associated with backflushing fuel lines. It is essential to stay vigilant and follow all safety guidelines to ensure a safe and successful procedure. Remember, safety should always be the top priority when working with fuel.
Fuel Lines: Unveiling the Differences and Their Impact
You may want to see also
Post-Backflush Inspection: Inspect the fuel lines and tank after backflushing to ensure proper clearance
After performing a backflush to clear a tank screen, a thorough inspection is crucial to ensure the system's integrity and prevent potential issues. This inspection process involves a systematic evaluation of the fuel lines and the tank to verify that the clearance is adequate and that no damage has occurred during the cleaning process. Here's a step-by-step guide to conducting this inspection:
Fuel Line Inspection: Start by examining the fuel lines for any signs of damage, blockages, or debris accumulation. Look for kinks, bends, or any visible wear and tear along the length of the lines. Ensure that the lines are properly secured and that there are no sharp bends or restrictions that could impede fuel flow. Check for any signs of corrosion or deterioration, especially in areas where the lines connect to the tank or other components. It is essential to verify that the fuel lines have been properly aligned and that there is sufficient clearance between the lines and other nearby parts to allow for smooth fuel movement.
Tank Inspection: Access the fuel tank and inspect its interior for any signs of clogging, corrosion, or damage. Look for any visible debris or residue that may have been dislodged during the backflush process. Ensure that the tank's walls and bottom are clean and free from any obstructions. Check the tank's ventilation system to make sure it is functioning correctly and that there are no blockages in the vents or breathing valves. Verify that the tank's fuel level is at the appropriate mark and that there are no leaks or spills around the tank's perimeter.
Clearance and Alignment: Measure and compare the clearance between the fuel lines and the tank walls, ensuring that it meets the manufacturer's specifications. Proper clearance is essential to prevent fuel line damage and ensure efficient fuel flow. Check for any misalignments in the fuel lines or connections, as this could lead to fuel leaks or reduced performance. Make any necessary adjustments to the lines to ensure they are straight and properly positioned.
Documentation and Reporting: Document the inspection findings, including any issues or areas of concern. Create a detailed report outlining the condition of the fuel lines, tank, and overall system. This report should include recommendations for any necessary repairs or maintenance to ensure the system's optimal performance. It is crucial to address any identified problems promptly to prevent further complications and ensure the safety and efficiency of the fuel system.
By following these inspection procedures, you can effectively verify the success of the backflush process and maintain the integrity of the fuel system. Regular maintenance and inspections are essential to identify and rectify potential issues, ensuring the reliable operation of the fuel lines and tank.
Fuel Pump Upgrade: Big Line Solutions for Your Chevy Yukon
You may want to see also
Frequently asked questions
Backflushing fuel lines can be an effective technique to address a clogged tank screen, but it should be done with caution and proper precautions. It is important to ensure that the fuel system is properly bled and that all safety measures are in place before attempting this process. Always refer to the vehicle's manual for specific instructions and recommendations.
Backflushing fuel lines can carry certain risks. It may lead to fuel contamination if not done correctly, as air bubbles and debris can be introduced into the fuel system. Additionally, there is a risk of fuel leakage if the lines are not properly sealed during the process. It is crucial to have a thorough understanding of the fuel system and to follow all safety guidelines to minimize these risks.
The frequency of backflushing depends on various factors, including the age of the vehicle, driving conditions, and fuel quality. As a general guideline, it is recommended to backflush the fuel lines every 50,000 to 100,000 miles or as advised by the vehicle manufacturer. Regular maintenance and monitoring of fuel system performance can help determine if backflushing is necessary.