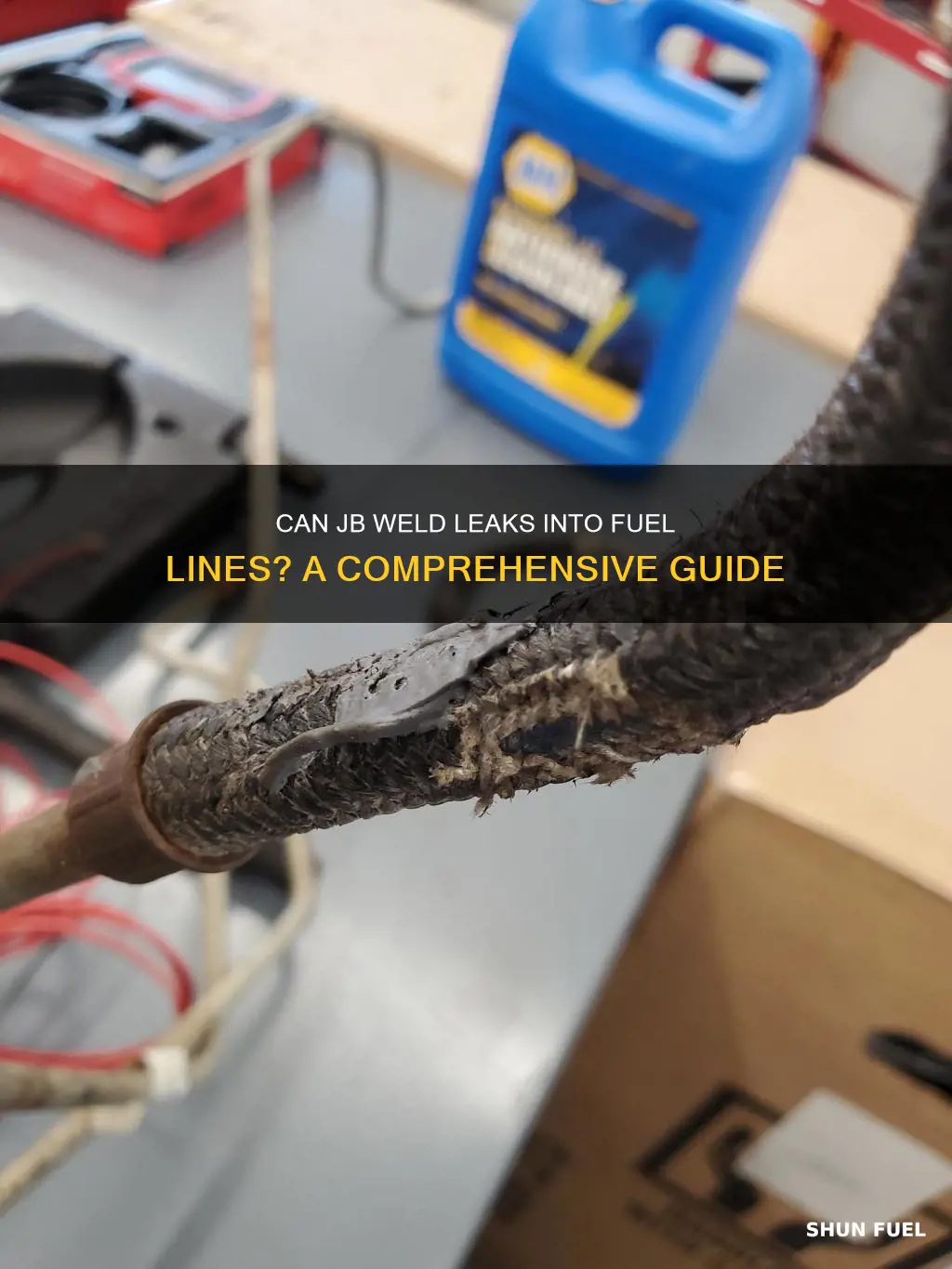
Can JB Weld leak into a fuel line? This question delves into the potential risks and implications of using JB Weld, a popular epoxy-based adhesive, in fuel line repairs. While JB Weld is known for its strong bonding properties, its compatibility with fuel lines is a concern. This paragraph will explore the potential for JB Weld to leak into fuel lines, the consequences of such leaks, and the importance of using appropriate materials for fuel system repairs to ensure safety and reliability.
Characteristics | Values |
---|---|
Chemical Composition | Epoxy-based adhesive |
Temperature Resistance | Can withstand temperatures up to 300°F (149°C) |
Flexibility | Provides some flexibility when cured |
Bond Strength | Strong bond to metal surfaces |
Application | Not suitable for bonding fuel lines directly |
Compatibility | May not be compatible with all fuel line materials |
Leaking Risk | Potential for leakage if not applied correctly |
Environmental Impact | May contain hazardous substances |
Regulatory Compliance | Not a replacement for proper fuel line installation |
What You'll Learn
- Weld Material Compatibility: Ensure JB Weld is compatible with fuel line material to prevent leaks
- Welding Technique: Proper technique is crucial to avoid cracks and leaks in the weld
- Fuel Line Material: Different fuel line materials may react differently with JB Weld
- Temperature Sensitivity: Welded joints can fail at extreme temperatures, leading to fuel leaks
- Long-Term Reliability: Regular inspections are needed to ensure the weld remains leak-free over time
Weld Material Compatibility: Ensure JB Weld is compatible with fuel line material to prevent leaks
When it comes to repairing fuel lines, the choice of welding material is critical to ensure the integrity and safety of the system. JB Weld, a popular two-part epoxy-based adhesive and sealant, is often used for its versatility and ease of application. However, it's essential to consider the compatibility of JB Weld with the material of the fuel line to prevent potential leaks and ensure a reliable repair.
The compatibility of JB Weld with fuel line materials is a crucial factor in determining its effectiveness. Fuel lines are typically made from various materials such as rubber, vinyl, or plastic, each with unique properties. Rubber fuel lines, for example, are known for their flexibility and resistance to heat and chemicals. When using JB Weld on rubber fuel lines, it's essential to choose a compatible adhesive that won't degrade the rubber over time, as this could lead to cracks and eventual leaks.
For rubber fuel lines, a suitable alternative to JB Weld might be a rubber-based adhesive or a specialized epoxy designed for rubber bonding. These materials are formulated to adhere to rubber without causing damage or compromising its structural integrity. Similarly, if the fuel line is made of vinyl or plastic, selecting an adhesive that is compatible with these materials is vital. Some epoxy systems are specifically engineered to bond with vinyl and plastic, ensuring a strong and durable repair.
Incompatibility between JB Weld and the fuel line material can result in several issues. If the adhesive is not compatible, it may not adhere properly to the fuel line, leading to gaps or weak bonds. Over time, these gaps can cause fuel to leak, potentially causing engine misfires, reduced performance, and even fire hazards. Additionally, incompatible adhesives might react with the fuel line material, causing it to deteriorate or become brittle, further exacerbating the problem.
To ensure a successful repair, it is recommended to consult the manufacturer's guidelines or seek professional advice when selecting the appropriate welding or bonding material for the specific fuel line material. By choosing the right adhesive, you can create a robust and leak-free connection, restoring the fuel system's functionality and safety. Remember, proper material compatibility is key to achieving long-lasting and reliable repairs.
2008 Cobalt Fuel Line: Size and Compatibility Guide
You may want to see also
Welding Technique: Proper technique is crucial to avoid cracks and leaks in the weld
When it comes to welding, especially in applications involving fuel lines, the importance of proper technique cannot be overstated. The goal is to ensure a strong, reliable bond without compromising the integrity of the material, particularly in critical systems like fuel lines. One of the most common welding methods used in such scenarios is the use of JB Weld, a popular epoxy-based adhesive and sealant. However, despite its versatility, JB Weld must be applied with precision to avoid potential issues.
The primary concern when welding or using JB Weld on fuel lines is the risk of cracks and leaks. These can occur if the welding process is not executed correctly, leading to potential fuel system failures. Cracks in the weld can be caused by a variety of factors, including improper surface preparation, excessive heat, and incorrect application of the adhesive. For instance, if the surface of the fuel line is not cleaned and prepared adequately, the JB Weld may not adhere properly, leading to a weak bond that could eventually fail.
To prevent these issues, it is essential to follow a structured welding technique. Firstly, ensure that the fuel line and any adjacent components are thoroughly cleaned to remove dirt, grease, and other contaminants. This can be achieved using a degreaser and a wire brush to ensure a clean, smooth surface. Next, apply a primer designed for the specific materials being used to provide an additional layer of protection and improve adhesion.
The welding process itself should be carried out with care. Use a heat source that is appropriate for the material, ensuring that the temperature is controlled to avoid overheating the surrounding areas. Apply the JB Weld in a thin, even layer, allowing it to set slightly before applying additional layers to build up the required thickness. Each layer should be applied at right angles to the previous one to ensure a strong, cohesive bond. Finally, allow sufficient time for the weld to cure according to the manufacturer's instructions.
In summary, achieving a successful weld when using JB Weld on fuel lines requires attention to detail and adherence to specific techniques. By properly preparing the surface, using the right materials, and applying the adhesive with precision, you can minimize the risk of cracks and leaks, ensuring the long-term reliability of the fuel system. This approach is crucial in maintaining the safety and functionality of any system that relies on the integrity of the weld.
Fuel Line Leaks: Spotting the Signs and What to Do
You may want to see also
Fuel Line Material: Different fuel line materials may react differently with JB Weld
When it comes to repairing fuel lines, JB Weld is a popular choice due to its ease of use and strong bonding properties. However, it's crucial to understand that the effectiveness and safety of this repair depend heavily on the material of the fuel line itself. Different fuel line materials can react variably with JB Weld, leading to potential issues down the line.
For instance, JB Weld is generally not recommended for use with rubber fuel lines. Rubber is a soft, flexible material that can be easily damaged by the heat and pressure generated during the curing process of JB Weld. This can lead to cracks, leaks, and even the deterioration of the rubber over time. In contrast, JB Weld can be an effective repair for fuel lines made of harder materials like nylon or PVC. These materials are more resistant to the heat and pressure involved in the curing process, making them less prone to damage.
Another important consideration is the compatibility of JB Weld with the specific fuel line material. Some materials may require a primer or specific application techniques to ensure a strong bond. For example, if you're working with a fuel line made of a composite material, you might need to use a primer designed for such materials to ensure the best possible bond. Always refer to the manufacturer's guidelines for the specific fuel line material you're working with.
In addition, the temperature and environmental conditions can also influence the performance of JB Weld in a fuel line. Extreme temperatures, whether hot or cold, can affect the curing process and the long-term performance of the repair. Similarly, exposure to sunlight, UV radiation, and other environmental factors can impact the durability of the repair. Always consider the typical operating conditions of your vehicle and choose a repair method that can withstand those conditions.
Lastly, it's essential to follow the manufacturer's instructions for JB Weld and the specific fuel line material you're working with. These instructions often include important details about preparation, application, and curing times. By adhering to these guidelines, you can ensure a safe and effective repair that minimizes the risk of leaks or other issues.
Chevy Silverado Fuel Line: 2008 Model Size Guide
You may want to see also
Temperature Sensitivity: Welded joints can fail at extreme temperatures, leading to fuel leaks
Welding, especially when using products like JB Weld, can be a useful method for repairing fuel lines and other automotive components. However, it is crucial to understand the limitations and potential risks associated with this process, particularly concerning temperature sensitivity. Extreme temperatures can cause welded joints to fail, resulting in fuel leaks, which can be a serious safety hazard.
The primary concern with temperature sensitivity is the potential for expansion and contraction of the materials involved. When a fuel line is subjected to high temperatures, such as those experienced during engine operation, the metal and the JB Weld material can expand. This expansion can cause stress on the welded joint, potentially leading to cracks or even complete separation. Similarly, during cold weather, the materials can contract, and the joint may become tight, leading to increased pressure and potential failure.
In the context of fuel lines, temperature sensitivity is a critical issue. Fuel lines are designed to withstand the temperature fluctuations that occur during normal operation. However, if a welded joint fails due to temperature extremes, it can result in fuel leakage. This leakage can lead to engine misfires, reduced performance, and even potential fires or explosions in extreme cases.
To mitigate these risks, it is essential to follow proper welding procedures and use appropriate materials. JB Weld, for instance, offers a range of products designed for specific applications and temperature ranges. It is crucial to select the right product for the specific temperature conditions the vehicle will encounter. Additionally, ensuring that the welding process is carried out with precision and following manufacturer guidelines can help minimize the chances of joint failure.
In summary, temperature sensitivity is a critical factor to consider when using JB Weld or any welding method for fuel line repairs. Understanding the potential for expansion and contraction, and taking steps to minimize temperature-related stress on the welded joint, can help ensure the safety and reliability of the vehicle's fuel system. Always consult the manufacturer's instructions and seek professional advice when dealing with critical automotive repairs.
Motorcycle Fuel Line: Top Stores for Quality Parts
You may want to see also
Long-Term Reliability: Regular inspections are needed to ensure the weld remains leak-free over time
When it comes to ensuring the long-term reliability of any repair or modification, especially in critical systems like fuel lines, regular inspections are an absolute necessity. This is particularly true for JB Weld, a popular epoxy-based adhesive and sealant, which is often used to repair damaged fuel lines. While JB Weld is known for its strong bonding capabilities and ability to withstand high temperatures, it is not immune to potential issues over time.
The primary concern with any weld or repair in a fuel line is the possibility of leaks. Fuel lines are designed to withstand the pressure and temperature fluctuations of gasoline or diesel, and any compromise in the integrity of the weld could lead to dangerous consequences. Over time, the weld might degrade due to factors such as heat, vibration, or chemical exposure from the fuel itself. This degradation can result in the formation of cracks or gaps in the weld, allowing fuel to leak out.
Regular inspections are a proactive measure to prevent such issues. By visually examining the weld and the surrounding area, you can identify any signs of wear, damage, or separation. Look for any visible cracks, pitting, or discoloration, as these could indicate that the weld is failing. Additionally, inspect the fuel line for any signs of fuel leakage, such as stains or a sweet odor, which could be a clear indication of a compromised weld.
During these inspections, it's also important to check the overall condition of the fuel line. Over time, fuel lines can develop issues such as corrosion, cracking, or softening, which can affect the weld's integrity. Ensuring that the fuel line is in good condition and free from any pre-existing damage will contribute to the long-term success of the repair.
In summary, regular inspections are a critical aspect of maintaining the reliability of a JB Weld repair in a fuel line. By staying vigilant and addressing any issues promptly, you can ensure that the weld remains leak-free and that the fuel line continues to function safely and efficiently over an extended period. This proactive approach is essential for both the performance and safety of the vehicle's fuel system.
Mastering the Art of GM Plastic Fuel Line Removal: A Step-by-Step Guide
You may want to see also
Frequently asked questions
JB Weld is not recommended for fuel line repairs. It is a temporary fix and can cause more harm than good. The adhesive can leak into the fuel system, leading to engine issues and potential safety hazards.
Using JB Weld on fuel lines can result in several problems. The adhesive may not withstand the high temperatures and pressure inside the fuel system, leading to potential leaks and engine misfires. Additionally, the chemicals in JB Weld can contaminate the fuel, causing performance issues and potential damage to the engine over time.
Yes, there are specialized products designed for fuel line repairs. These products are typically made from materials that can withstand the harsh conditions of the fuel system. It is best to consult a professional mechanic or use products specifically formulated for fuel line repairs to ensure a safe and effective solution.
Regular maintenance and inspections can help prevent fuel line damage. Keep an eye out for any signs of wear and tear, such as cracks or corrosion. Using high-quality fuel and ensuring proper fuel system maintenance can also reduce the risk of fuel line issues. If any problems are detected, it is crucial to address them promptly to avoid further complications.