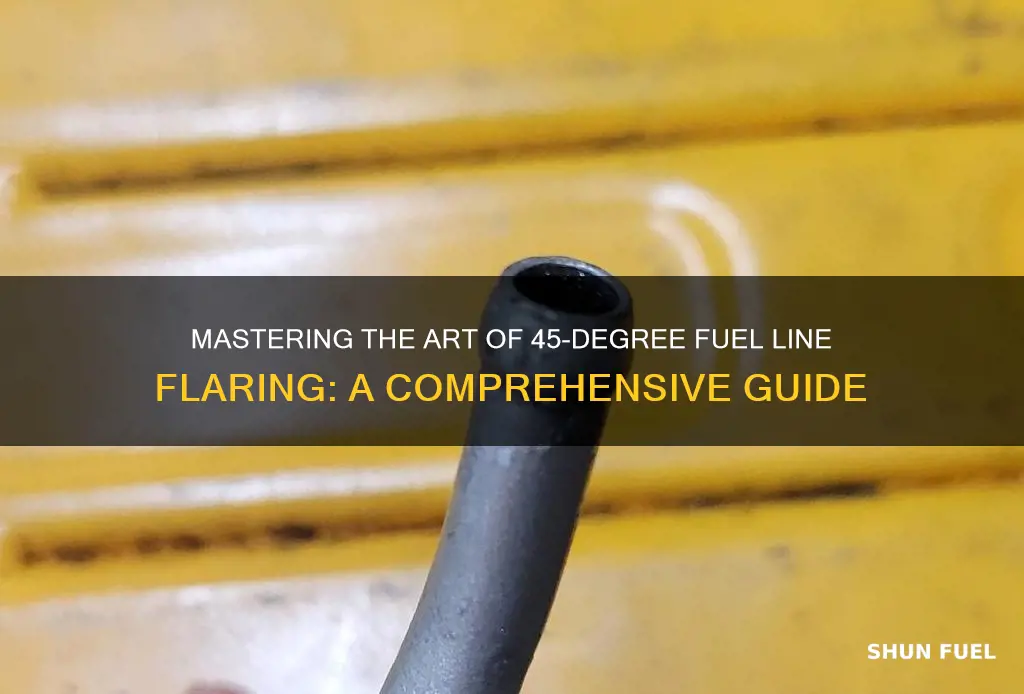
A 45-degree fuel line flare is a crucial step in ensuring a secure and leak-free connection for fuel lines in automotive or industrial applications. This process involves creating a precise angle and shape to fit the fuel line into a fitting, typically a flare nut. It requires careful measurement and technique to achieve a tight seal without damaging the fuel line. The following guide will provide a step-by-step approach to mastering this technique, ensuring a professional and reliable finish.
What You'll Learn
Preparation: Gather tools: flare gun, fuel line, primer, and flux
Before you begin the process of creating a 45-degree fuel line flare, it's crucial to ensure you have all the necessary tools and materials ready. This preparation step is essential to guarantee a smooth and successful flare job. Firstly, you'll need a flare gun, which is a specialized tool designed for creating flares. It's important to choose a flare gun that is appropriate for the size and material of your fuel line. Next, you'll require a length of fuel line that matches the desired flare size and shape. This fuel line should be made of a material that is compatible with the fuel it will carry. Additionally, you'll need a primer and flux. The primer is used to prepare the fuel line for the flare, ensuring a strong bond between the fuel line and the flare. Flux, on the other hand, helps to remove any oxidation or debris from the fuel line, ensuring a clean and smooth surface for the flare.
Having all these materials gathered and organized will make the flare process more efficient and less prone to errors. It's a good practice to double-check the compatibility of the fuel line material with the primer and flux to avoid any potential issues during the flare creation. Once you have all the tools and materials ready, you can proceed to the next step, which is the actual flare creation process. Remember, proper preparation is key to achieving a successful and durable 45-degree fuel line flare.
Jeep Cherokee Fuel Filter: In-Line or Not? 1997 Model
You may want to see also
Clamping: Secure fuel line with a clamp at 45-degree angle
When working on a 45-degree fuel line flare, clamping is a crucial step to ensure a secure and reliable connection. Here's a detailed guide on how to achieve this:
Start by ensuring you have the right tools and materials. You'll need a high-quality fuel line clamp specifically designed for the diameter of your fuel line. These clamps are typically made of durable materials like stainless steel or aluminum to withstand the pressure and temperature variations in a fuel system. Choose a clamp with a 45-degree angle to match the flare angle. This angle is essential for a proper fit and to avoid any potential leaks.
Now, locate the section of the fuel line where you want to install the flare and clamp. Clean the area to remove any dirt or debris that might interfere with the installation. Ensure the fuel line is straight and free of any kinks or bends that could affect the flare's alignment.
Place the fuel line clamp onto the fuel line, positioning it at the desired 45-degree angle. The clamp should fit snugly around the fuel line, providing a secure hold. Use your hands or a pair of pliers to tighten the clamp firmly, but be careful not to overtighten, as this can damage the fuel line. The goal is to create a tight seal without causing any strain or damage.
Once the clamp is securely in place, check for any signs of leakage. You can do this by applying a small amount of diesel fuel or a suitable sealant to the flare and observing if any fuel escapes. If there are no leaks, your 45-degree fuel line flare is now securely clamped and ready for use.
Remember, proper clamping is vital for the longevity and safety of your fuel system. It ensures that the fuel line remains in place even under various driving conditions, preventing potential fuel leaks and engine performance issues. Always follow manufacturer guidelines and use the appropriate tools and materials for the best results.
John Deere L110 Fuel Line Disconnect: A Step-by-Step Guide
You may want to see also
Flaring: Use flare gun to create a 45-degree bend
Flaring is a crucial technique in plumbing and automotive work, allowing you to create custom bends in pipes or hoses, which is especially useful for fuel lines. Achieving a 45-degree angle is a common requirement in these applications, and using a flare gun is an efficient method to accomplish this. Here's a step-by-step guide to mastering the art of flaring for a 45-degree bend:
Gather the Tools and Materials: Before you begin, ensure you have the necessary tools. A flare gun is the primary tool for this task, and it comes in various sizes depending on the diameter of the pipe or hose you're working with. You'll also need the appropriate flare inserts or dies that match the size of your fuel line. Additionally, have a supply of the material you're flaring, such as fuel line itself, pipe, or hose.
Prepare the Work Area: Set up your workspace to ensure safety and efficiency. Clear a flat surface and ensure you have adequate lighting. Place a sturdy workbench or a flat surface where you can securely position the flare gun and the material you're working on. It's essential to have a stable foundation to guide the flare process.
Position the Flare Gun: Hold the flare gun firmly in one hand, ensuring it is aligned with the end of the fuel line or hose. The flare gun should be positioned at a 45-degree angle to the material you're flaring. This angle is crucial to achieving the desired 45-degree bend. Apply firm pressure to the trigger of the flare gun to initiate the bending process.
Apply Force and Bend: As you pull the trigger, the flare gun will create a bending force, forcing the material to take the shape of the flare gun's barrel. Guide the material with your other hand to ensure it follows the desired 45-degree path. Apply steady pressure and maintain the angle to create a smooth, consistent bend. Take your time with this step to ensure precision.
Secure the Flare: Once you've achieved the desired angle, release the trigger and carefully remove the flare gun. The material should now have a 45-degree bend. To secure the flare, you can use a flare tool to crimp the bent section, creating a tight, sealed connection. This step ensures the longevity and functionality of the fuel line.
Practice and Precision: Flaring requires practice and precision. Take the time to experiment with different angles and pressures to understand how the flare gun and material respond. Each project may have unique requirements, so adapting your technique accordingly is essential. With practice, you'll develop the skill to create perfect 45-degree flares consistently.
Fuel Line Size: Is Bigger Always Better?
You may want to see also
Priming: Apply primer to flare joint for bonding
When preparing to create a 45-degree fuel line flare, priming the flare joint is a crucial step to ensure a strong and durable bond. This process involves applying a specialized primer to the flare joint, which acts as a base layer to promote adhesion and create a solid foundation for the flare.
Start by ensuring the flare joint is clean and free of any debris or contaminants. Use a wire brush or a small scraper to gently remove any old primer or residue from the joint. This step is essential to guarantee a proper bond. Once the joint is clean, apply a thin and even layer of primer using a small brush or a spray gun, depending on your preference and the accessibility of the joint. The primer should be specifically designed for fuel line applications and compatible with the materials used in the flare.
Take your time to ensure the primer is applied uniformly across the entire flare joint. It's important to follow the manufacturer's instructions regarding the drying time of the primer. Typically, a light touch or a finger test can be used to determine if the primer is dry to the touch. Avoid any excessive force or pressure on the joint during this stage to prevent any damage.
After the primer has dried, inspect the flare joint to ensure there are no visible imperfections or gaps. If any areas require additional primer, apply a second thin layer, allowing sufficient time for it to cure before proceeding with the next steps of the flare creation process. Proper priming is essential for the overall success of the 45-degree fuel line flare, as it ensures a strong bond between the flare and the fuel line, leading to a reliable and leak-free connection.
Nylon Fuel Line Repair: Quick Tips for a Successful Fix
You may want to see also
Assembly: Connect flare to fuel line, ensuring a tight seal
When connecting a flare to a fuel line, it's crucial to ensure a tight and secure seal to prevent any leaks or potential hazards. Here's a step-by-step guide to achieving this:
Start by preparing the flare and fuel line. Ensure both components are clean and free of any debris or contaminants. Use a suitable solvent or cleaner to remove any old adhesives or residues from previous connections. This step is essential to guarantee a proper bond and seal.
Next, apply a thin layer of fuel-resistant adhesive or sealant to the flare and the corresponding section of the fuel line. The type of adhesive used should be compatible with the materials of both the flare and the fuel line to ensure a durable bond. Allow the adhesive to sit for a few moments to become tacky, providing enough time for the flare and fuel line to adhere properly.
Now, carefully align the flare with the fuel line, ensuring that the 45-degree angle is maintained. Apply firm pressure to the flare, holding it in place for the recommended time specified by the adhesive manufacturer. This pressure will help create a tight seal and ensure the flare is securely attached.
To further enhance the seal, consider using a clamp or a specialized flare fitting tool to apply additional pressure. This extra force will help create a robust bond and prevent any potential leaks. Make sure the clamp is secure and tightened evenly to avoid damaging the flare or fuel line.
Finally, inspect the connection thoroughly. Check for any visible gaps or imperfections in the seal. If everything looks good, test the system by applying pressure and observing for any leaks. A successful connection will result in a tight, leak-free seal, ensuring the fuel line is securely connected to the flare.
Fuel Line Routing: A Guide to Running Return Lines on Your 69 Mustang
You may want to see also