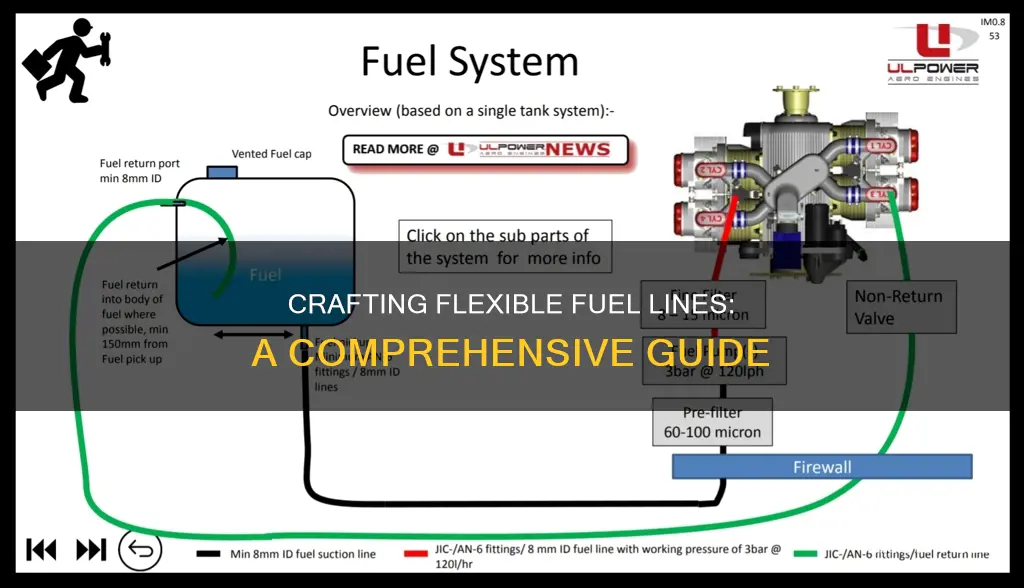
Flexible fuel lines are essential components in various applications, from automotive to industrial, where the ability to transmit fuel efficiently and reliably is crucial. Making these lines involves a careful process that requires specific materials and techniques to ensure flexibility, durability, and compatibility with different fuels. This guide will explore the key steps and considerations involved in manufacturing flexible fuel lines, including material selection, design principles, and assembly methods, to help readers understand the process and achieve high-quality results.
What You'll Learn
- Material Selection: Choose flexible fuel-resistant materials like rubber or silicone
- Line Design: Ensure lines have enough flexibility and diameter for fuel flow
- Routing: Route lines away from heat sources and sharp bends
- Clamps: Use secure, vibration-resistant clamps to attach lines
- Testing: Inspect lines for leaks and ensure proper fuel flow
Material Selection: Choose flexible fuel-resistant materials like rubber or silicone
When it comes to creating flexible fuel lines, material selection is a critical aspect that ensures the durability and reliability of the fuel system. One of the most commonly used materials for this purpose is rubber. Rubber is an excellent choice due to its inherent flexibility and resistance to various fuels. It can withstand the corrosive nature of gasoline, diesel, and even ethanol blends without compromising its structural integrity. The elasticity of rubber allows it to bend and move with the fuel lines, making it ideal for applications where flexibility is essential.
Another popular material for fuel lines is silicone. Silicone rubber is known for its exceptional heat resistance and stability under varying temperatures. It can handle the extreme conditions that fuel systems often encounter, such as hot engine compartments and fluctuating temperatures. Silicone's flexibility is comparable to rubber, ensuring that the fuel lines remain pliable and adaptable. Additionally, silicone is resistant to fuel degradation, making it a long-lasting option for fuel line construction.
Both rubber and silicone offer excellent resistance to fuel-related chemicals, ensuring that the fuel lines remain intact and free from leaks. These materials are designed to mimic the natural elasticity of the human body, allowing them to absorb vibrations and movements without cracking or breaking. This flexibility is crucial for fuel lines as they need to accommodate the natural expansion and contraction of the vehicle's engine and fuel system components.
In the manufacturing process, it is essential to consider the specific fuel types and operating conditions. For instance, if the fuel line will be exposed to high temperatures, silicone might be the preferred choice. Conversely, for applications where flexibility is the primary concern, rubber could be the more suitable option. The material selection should also consider the overall design and installation process to ensure a seamless and efficient fuel line system.
By choosing the right flexible fuel-resistant materials, you can ensure the longevity and performance of your fuel system. Rubber and silicone are proven choices, offering the necessary flexibility, resistance to fuel-related chemicals, and adaptability to various environmental conditions. Proper material selection is a key step in the process of creating functional and reliable flexible fuel lines.
Fuel Return Line Repair: A Guide for Jaguar XJ6 Sovereign Owners
You may want to see also
Line Design: Ensure lines have enough flexibility and diameter for fuel flow
When designing flexible fuel lines, ensuring optimal flexibility and appropriate diameter is crucial for efficient fuel flow and system longevity. Here's a detailed guide on how to achieve this:
Material Selection: The foundation of a flexible fuel line lies in its material composition. Opt for high-quality, flexible materials specifically designed for fuel applications. Common choices include rubber compounds, such as natural or synthetic rubber, or specialized fuel-resistant hoses. These materials should be able to withstand the corrosive nature of fuel while maintaining flexibility over a wide temperature range.
Line Construction: The construction of the fuel line itself plays a vital role in flexibility. Consider a multi-layer construction with an inner layer made of a compatible material that directly contacts the fuel. This inner layer should be followed by a flexible intermediate layer, typically a braided or spiral-wound reinforcement, which provides the necessary flexibility. Finally, an outer layer can be added for protection against abrasion and environmental factors.
Diameter Considerations: The diameter of the fuel line is a critical factor in fuel flow rate and pressure drop. A larger diameter allows for higher fuel flow capacity, which is essential for high-performance applications or engines with increased fuel demands. However, it's important to strike a balance. If the diameter is too large, it may lead to unnecessary pressure drop and increased system complexity. Aim for a diameter that meets the engine's requirements while maintaining efficient fuel delivery.
Flexibility Testing: To ensure the fuel lines are flexible enough, rigorous testing is recommended. This can be done by bending the lines to various angles and radii, simulating real-world conditions. The lines should be able to conform to these shapes without permanent deformation or excessive stress on the material. Flexibility testing also helps identify potential weak points or areas of reduced flexibility, allowing for design improvements.
Reinforcement and Protection: Depending on the application, consider adding additional reinforcement to critical areas. This could involve braiding or spiraling the fuel line with a sturdy material to enhance flexibility while maintaining structural integrity. Additionally, protect the fuel lines from potential hazards like sharp edges, heat sources, or vibration by incorporating protective covers or sleeves.
Duramax Fuel Line Removal: A Step-by-Step Guide for DIY Mechanics
You may want to see also
Routing: Route lines away from heat sources and sharp bends
When designing the routing of flexible fuel lines, it's crucial to prioritize safety and performance. One critical aspect is to route the lines away from heat sources and sharp bends. This practice ensures the longevity and reliability of the fuel system.
Heat sources, such as exhaust manifolds, engine blocks, or even hot surfaces in the engine bay, can cause the fuel lines to degrade over time. High temperatures can lead to fuel line hardening, cracking, or even melting, resulting in fuel leaks or system failures. To mitigate this, it's essential to route the fuel lines as far as possible from these heat sources. This might involve running the lines through insulated sleeves or using heat shields to protect the fuel lines.
Additionally, sharp bends or kinks in the fuel lines can restrict fuel flow, create pressure drops, and potentially damage the lines. These issues can lead to fuel starvation, especially during high-performance driving or when the engine is under load. To avoid this, the fuel lines should be routed with gentle curves and smooth transitions. The use of flexible, high-pressure fuel lines with a suitable diameter can also help accommodate the necessary bends without compromising flow.
A strategic approach to routing involves considering the overall layout of the engine bay and the vehicle's architecture. The fuel lines should be positioned to avoid any potential interference with moving parts, such as suspension components or the transmission. Proper clearance and a well-planned route will ensure that the fuel lines remain intact and functional throughout the vehicle's lifetime.
In summary, routing flexible fuel lines away from heat sources and sharp bends is a critical step in ensuring the performance and longevity of the fuel system. By implementing these routing practices, you can minimize the risk of fuel line damage, maintain optimal fuel flow, and ultimately enhance the overall reliability of the vehicle's fuel delivery system.
Troubleshooting Clogged Fuel Lines: A Guide for 91 F150 Owners
You may want to see also
Clamps: Use secure, vibration-resistant clamps to attach lines
When it comes to creating flexible fuel lines, ensuring a secure and reliable connection is crucial. One of the key components to achieving this is the use of vibration-resistant clamps. These specialized clamps are designed to withstand the rigors of the automotive environment, providing a tight and durable hold on the fuel lines.
The process of attaching the fuel lines with clamps involves several steps. Firstly, you'll need to ensure that the fuel lines are clean and free of any debris or contaminants. This is essential to prevent any potential leaks or damage. Once the lines are prepared, locate the desired attachment points, typically where the lines connect to various components such as the fuel tank, engine, or fuel pump.
Securely fasten the clamps around the fuel lines, ensuring they are tight enough to provide a firm grip but not so tight that they cause any damage to the line. Vibration-resistant clamps often feature a unique design with a series of teeth or serrations that grip the line tightly. This design allows the clamp to hold the line firmly even during sudden movements or vibrations, such as those experienced during acceleration or when driving over rough terrain.
It is important to use the appropriate size and type of clamp for the specific fuel line. Different sizes and materials of fuel lines may require specialized clamps to ensure a proper fit and secure attachment. Always refer to the manufacturer's guidelines or consult a professional to determine the correct clamp specifications for your particular fuel line setup.
By using vibration-resistant clamps, you can ensure that your flexible fuel lines remain securely attached, even under challenging conditions. This not only enhances the overall reliability of your fuel system but also helps prevent potential issues such as fuel leaks or line damage caused by excessive movement or vibration.
Unveiling the Material Mystery: What Fuels Clear Fuel Lines?
You may want to see also
Testing: Inspect lines for leaks and ensure proper fuel flow
When it comes to testing the newly installed or modified flexible fuel lines, a thorough inspection is crucial to ensure optimal performance and safety. Here's a step-by-step guide on how to test and verify the integrity of these lines:
Leak Detection: Begin by applying a soapy water solution to the fuel lines. This simple yet effective method helps identify any potential leaks. Take a small brush or a cloth and gently wipe the lines, ensuring you cover all connections and bends. If there are any cracks, punctures, or faulty fittings, you'll notice bubbles forming on the surface as the soap creates a temporary seal. It's essential to act promptly if you spot any leaks, as they can lead to fuel contamination, reduced engine performance, and potential safety hazards.
Pressure Testing: Another critical aspect of testing is to check the fuel lines' ability to withstand pressure. You can use a fuel line pressure tester for this purpose. Connect the tester to the fuel line and gradually increase the pressure. Observe the gauge to ensure it remains stable and does not drop. If the pressure drops, it indicates a potential issue, such as a weakened line or a faulty connection. This test is particularly important for lines that will be subjected to varying fuel pressures during engine operation.
Flow Rate Assessment: Proper fuel flow is essential for efficient engine operation. To test the flow rate, you can use a flow meter or a calibrated container. Attach the flow meter to the fuel line and measure the volume of fuel passing through it over a specific time interval. Compare the results with the expected flow rate based on the engine's requirements. If the flow rate is inconsistent or lower than expected, it may indicate blockages, clogs, or issues with the fuel pump.
Visual Inspection: While testing, don't forget the power of visual inspection. Carefully examine the fuel lines for any visible signs of damage, such as cuts, tears, or kinks. Check for any signs of corrosion or deterioration, especially if the lines are made of metal. Ensure that all connections are secure and free from any debris or contaminants. A thorough visual inspection can often reveal issues that might not be apparent during other tests.
Engine Performance Check: Finally, the most practical way to test the fuel lines is by putting the system through its paces on the engine. Start the engine and monitor its performance. Listen for any unusual noises, such as hissing or roaring, which could indicate a leak. Observe the engine's behavior, ensuring it starts efficiently, runs smoothly, and maintains optimal performance. Any deviations from the expected behavior may require further investigation and adjustments.
The Ultimate Guide to Choosing the Best Marine Fuel Line
You may want to see also
Frequently asked questions
Flexible fuel lines are typically made from materials like rubber, silicone, or a blend of both. These materials offer flexibility, durability, and resistance to fuel chemicals, ensuring a reliable connection between fuel tanks and engines.
Selecting the appropriate fuel line involves considering factors such as fuel type, pressure requirements, and vehicle specifications. Consult your vehicle's manual or seek advice from automotive experts to determine the specific size and type of fuel line needed for your engine.
While some DIY enthusiasts may attempt fuel line installation, it is generally recommended to seek professional assistance. Fuel line installation requires precision and knowledge of vehicle systems to ensure proper connections and avoid potential leaks.
Regular inspection for cracks, brittleness, or signs of fuel contamination is essential. Keep fuel lines clean and free from debris. Avoid using sharp objects that could damage the lines. Properly secure connections to prevent chafing and ensure optimal performance.