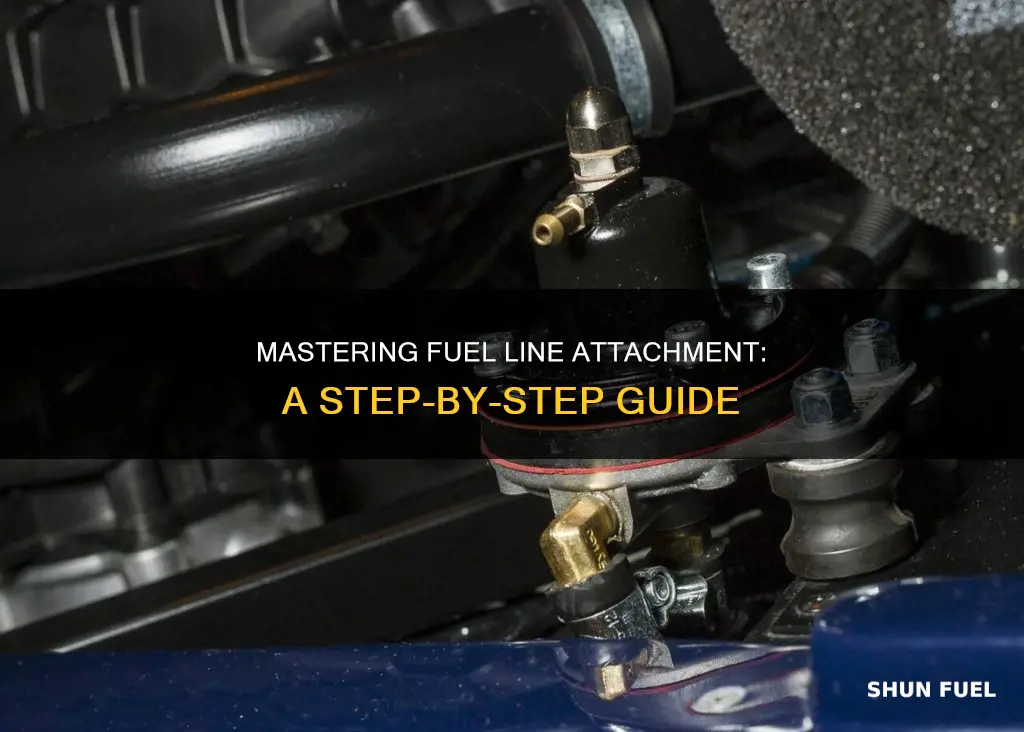
Attaching fuel lines is a crucial step in any vehicle's maintenance and repair process. It requires precision and attention to detail to ensure the system operates safely and efficiently. This guide will provide a step-by-step process for attaching fuel lines, covering the necessary tools, safety precautions, and techniques to ensure a secure and reliable connection.
What You'll Learn
- Fuel Line Materials: Choose the right materials for fuel lines, considering durability and compatibility
- Fuel Line Routing: Plan and route fuel lines to avoid damage and ensure proper flow
- Fuel Line Clamps: Use appropriate clamps to secure fuel lines and prevent leaks
- Fuel Line Testing: Test fuel lines for leaks and ensure proper pressure and flow
- Fuel Line Maintenance: Regularly inspect and maintain fuel lines to prevent issues and ensure safety
Fuel Line Materials: Choose the right materials for fuel lines, considering durability and compatibility
When it comes to choosing the right materials for fuel lines, durability and compatibility are key considerations to ensure the safety and efficiency of your fuel system. The primary goal is to select materials that can withstand the harsh conditions of fuel transport, including temperature fluctuations, pressure variations, and chemical exposure.
One of the most common materials used for fuel lines is rubber, which offers excellent flexibility and resistance to abrasion. Natural rubber, in particular, is known for its durability and ability to withstand high temperatures, making it a popular choice for fuel lines. It can handle the corrosive nature of fuels and is less likely to crack or degrade over time. However, it's important to note that rubber fuel lines may require regular inspection and replacement, especially in high-temperature environments, as they can become brittle over time.
Another popular option is synthetic rubber, such as neoprene or EPDM (ethylene propylene diene monomer). These materials provide enhanced durability and resistance to fuel degradation compared to natural rubber. Synthetic rubbers are often used in high-temperature and high-pressure applications due to their superior flexibility and resistance to aging. They can handle a wider range of fuel types and are less prone to cracking, making them a reliable choice for long-term fuel line installations.
For applications requiring even higher performance, stainless steel fuel lines are an excellent choice. Stainless steel offers exceptional durability, resistance to corrosion, and the ability to withstand extreme temperatures. It is an ideal material for high-performance vehicles or in environments where fuel lines are exposed to harsh chemicals or aggressive fuel types. While stainless steel fuel lines are more expensive, their longevity and compatibility with various fuels make them a worthwhile investment.
In addition to the material selection, it's crucial to consider the compatibility of the fuel lines with the specific fuel being transported. Different fuels have varying chemical compositions and properties, which can affect the choice of material. For example, ethanol-blended fuels may require fuel lines with enhanced resistance to ethanol's corrosive effects. Always refer to the manufacturer's guidelines and consult industry resources to ensure the chosen materials are compatible with the intended fuel.
Hose Clamps on Fuel Lines: A Practical Guide
You may want to see also
Fuel Line Routing: Plan and route fuel lines to avoid damage and ensure proper flow
Fuel line routing is a critical aspect of vehicle maintenance and performance, ensuring that fuel is efficiently delivered to the engine while minimizing the risk of damage. Proper routing involves careful planning and execution to avoid potential hazards and maintain optimal fuel flow. Here's a comprehensive guide to help you master the art of fuel line routing:
Understanding the Basics: Before you begin, familiarize yourself with the vehicle's fuel system layout. Locate the fuel tank, fuel pump, and the various fuel lines that connect these components. Each vehicle model may have unique configurations, so consult the manufacturer's manual for specific details. Understanding the system's layout is crucial for identifying potential routing challenges and ensuring a smooth installation process.
Planning the Route: Start by mapping out the path the fuel lines will take. Aim for a route that is as straight and direct as possible, minimizing sharp bends and kinks. Fuel lines should be routed away from high-temperature areas, such as exhaust manifolds and engine components, to prevent overheating and potential damage. Keep the lines as short as practical to reduce the risk of leaks and ensure efficient fuel delivery. Consider the vehicle's underbody and engine bay layout to identify suitable paths for the fuel lines.
Avoiding Obstacles: Fuel lines must be carefully routed to avoid contact with moving parts, sharp edges, or potential impact zones. For example, in a vehicle with a manual transmission, the fuel lines should be positioned to clear the gear shift mechanism. In off-road vehicles, ensure the lines are not susceptible to damage from rocks or debris. Proper insulation and protective sleeves can be used to safeguard the lines where necessary.
Securing the Lines: Once the routing is planned, secure the fuel lines using appropriate clamps or ties. Ensure that the lines are tightly fastened to prevent movement, which could lead to leaks or damage. Avoid tight bends or sharp turns that might restrict fuel flow. Use the manufacturer's recommended hardware and follow the installation instructions for a secure and reliable setup.
Regular Maintenance: Proper fuel line routing is not a one-time task; it requires regular maintenance. Inspect the lines periodically for any signs of damage, cracks, or leaks. Check for proper tension and ensure that the lines remain in their intended positions. Regular maintenance will help identify potential issues early on and ensure the long-term reliability of your vehicle's fuel system.
Braided Fuel Line Installation: A Step-by-Step Guide
You may want to see also
Fuel Line Clamps: Use appropriate clamps to secure fuel lines and prevent leaks
When it comes to securing fuel lines, using the right clamps is essential to ensure a safe and efficient fuel system. Fuel lines are critical components in any vehicle's engine, and proper attachment and maintenance can prevent costly and dangerous leaks. Here's a guide on how to use fuel line clamps effectively:
Choose the Right Clamp: The first step is to select the appropriate clamp for your fuel line. Different types of fuel lines and applications may require specific clamp designs. Common types include stainless steel clamps, which offer excellent corrosion resistance and durability, making them ideal for high-temperature and high-pressure environments. Another option is the fuel line clamp with a quick-release feature, allowing for easy installation and removal. Ensure you measure the fuel line's diameter to choose a clamp with the correct inside diameter to fit snugly.
Prepare the Fuel Line: Before attaching the clamp, ensure the fuel line is clean and free of any debris or contaminants. Use a fuel line cleaner or a mild detergent to wash the line, ensuring no residue remains. This step is crucial to prevent any interference with the clamp's grip and to maintain a secure connection.
Install the Clamp: Start by positioning the clamp around the fuel line, ensuring it is centered and aligned with the line's path. Use your fingers or a pair of pliers to tighten the clamp securely. The goal is to create a firm grip without causing any damage to the fuel line. Over-tightening can lead to line distortion or damage, so be cautious. A good rule of thumb is to tighten the clamp until it is snug, and then slightly loosen it to allow for some flexibility.
Test for Leaks: After installing the clamp, it's essential to test for any potential leaks. This can be done by applying a small amount of fuel line sealer or a similar product around the clamp's edges. Wait for the recommended time (usually a few minutes) and then check for any signs of leakage. If no leaks are detected, your fuel line is secure.
Regular Maintenance: Fuel line clamps should be checked regularly for any signs of wear and tear. Inspect the clamps for any cracks, corrosion, or signs of looseness. Over time, clamps can degrade due to fuel exposure and temperature changes. Replacing worn-out clamps is crucial to maintaining a safe fuel system. Consider using a corrosion-resistant material for the clamp's inner surface to further protect against fuel-related degradation.
By following these steps and using the appropriate fuel line clamps, you can effectively secure your fuel lines, ensuring a reliable and safe vehicle operation. Remember, proper maintenance and attention to detail are key to preventing fuel-related issues.
Fuel Line Swap: EFI to Carb Conversion Guide
You may want to see also
Fuel Line Testing: Test fuel lines for leaks and ensure proper pressure and flow
Fuel line testing is a crucial step in ensuring the safety and efficiency of your vehicle's fuel system. It helps identify potential issues before they cause major problems, saving you from costly repairs and potential hazards. Here's a comprehensive guide on how to test fuel lines for leaks and maintain optimal pressure and flow:
- Gather the Necessary Tools and Materials: Before you begin, ensure you have the required tools and materials. You'll need a fuel pressure gauge, a leak detection kit or soapy water, a wrench, and a supply of compressed air. These tools will assist in measuring pressure, identifying leaks, and ensuring a proper connection.
- Locate the Fuel Lines: Familiarize yourself with the location of the fuel lines in your vehicle. These lines typically run from the fuel tank to the engine, and you should be able to access them under the hood and along the vehicle's frame. Mark their positions to ensure you can easily locate them during the testing process.
- Test for Leaks: Start by inspecting the fuel lines for any visible signs of damage, cracks, or corrosion. Use the leak detection kit or soapy water to perform a more thorough inspection. Spray the soapy water or use the leak detection kit along the length of the fuel lines. Leaks will create bubbles, indicating the presence of a problem. Pay attention to connections, as these areas are prone to developing leaks. If you find any leaks, repair or replace the affected fuel line immediately.
- Measure Fuel Pressure: Use the fuel pressure gauge to check the pressure in the fuel lines. The pressure should be within the manufacturer's specified range. If the pressure is too low, it may indicate a restricted fuel flow or a problem with the fuel pump. If the pressure is too high, it could suggest an issue with the fuel injectors or a malfunctioning pressure regulator. Adjustments or repairs may be necessary to bring the pressure within the optimal range.
- Check Fuel Flow: Ensure that the fuel is flowing correctly through the system. Start the engine and monitor the fuel gauge or fuel warning light. If the fuel level drops rapidly, it could indicate a blockage or leak in the fuel lines. Listen for any unusual noises, such as hissing or roaring, which may suggest a fuel line issue. Proper fuel flow ensures that the engine receives the required amount of fuel for efficient operation.
- Inspect Connections: Pay close attention to all connections, including the fuel lines to the fuel pump, filter, and injectors. Tighten any loose connections and ensure they are secure. Over time, connections can loosen due to vibration, leading to potential fuel leaks. Regularly checking and tightening these connections is essential for maintaining a safe and efficient fuel system.
By following these steps, you can effectively test and maintain your fuel lines, ensuring they operate optimally and safely. Regular testing is vital to prevent fuel-related issues and maintain the overall performance of your vehicle.
Unleash the Power: NICOPP Lines for Fuel Efficiency
You may want to see also
Fuel Line Maintenance: Regularly inspect and maintain fuel lines to prevent issues and ensure safety
Fuel lines are an essential component of any vehicle's fuel system, and proper maintenance is crucial to ensure optimal performance and safety. Regular inspection and care can help prevent costly repairs and potential hazards associated with fuel line failures. Here's a comprehensive guide on how to maintain your fuel lines effectively:
Visual Inspection: Start by performing routine visual inspections of the fuel lines. Look for any signs of damage, such as cracks, leaks, or corrosion. Check for any visible wear and tear, especially in areas where the lines are more susceptible to stress, like bends, fittings, and attachments. Over time, fuel lines can degrade due to exposure to fuel vapors, heat, and vibration, so regular checks are vital. Inspect the lines for any bulging or softening, as this could indicate internal damage or a compromised structure.
Pressure Testing: Conducting pressure tests is an effective way to assess the integrity of your fuel lines. This test involves using a specialized tool to apply pressure to the lines and checking for any leaks. Start by ensuring the fuel system is depressurized and then connect the testing equipment to the fuel lines. Gradually increase the pressure and observe for any signs of leakage. If a leak is detected, it's essential to address the issue promptly, as it could lead to fuel contamination or even fire hazards.
Clamping and Securing: Proper clamping and securing of fuel lines are critical to maintaining their functionality. Ensure that all connections are tight and secure, using the appropriate tools and fasteners. Check for any loose fittings or clamps that might cause the lines to vibrate or move, leading to potential damage. Regularly inspect the clamps for wear and replace them if they become brittle or damaged. Properly routing the fuel lines away from moving parts and heat sources is also essential to prevent damage and ensure longevity.
Fuel Line Protection: Consider using protective measures to safeguard your fuel lines. This can include applying fuel line insulation to vulnerable areas, especially where the lines pass through tight spaces or come into contact with hot surfaces. Insulation helps prevent damage from heat, cold, and mechanical stress. Additionally, using protective sleeves or covers can shield the lines from sharp objects and potential impacts, further extending their lifespan.
Regular Maintenance Schedule: Implement a regular maintenance schedule to stay on top of fuel line care. This might include annual inspections and pressure tests, especially for older vehicles or those with high mileage. Keep a record of your inspections and any issues found, allowing you to track the health of your fuel system over time. By being proactive, you can identify and address potential problems before they escalate, ensuring a reliable and safe fuel system.
The Ultimate Guide to Choosing Lubricant for Fuel Line Installation
You may want to see also
Frequently asked questions
Attaching fuel lines requires precision and the right tools to ensure a tight seal. Start by cleaning the fuel line ends and the fitting surfaces to remove any dirt or debris. Then, use a fuel line adapter or a fuel line coupling that matches the diameter of your fuel line. Apply a thin layer of fuel line tape or fuel line compound around the fitting, ensuring it is centered. Tighten the fitting securely by hand, then use a fuel line crimping tool to apply the final crimp. This process creates a reliable bond.
Reusing old fuel lines is possible, but it should be done with caution. Inspect the old fuel lines for any signs of damage, cracks, or corrosion. If the lines are in good condition, you can attach them to new fittings. Ensure the fittings are compatible with the fuel line size and material. Consider using a fuel line adapter to facilitate the connection. However, always prioritize safety and consider replacing the lines if they are old or have been exposed to harsh conditions.
Attaching fuel lines typically requires a few essential tools. You will need a fuel line crimping tool, which comes in various sizes depending on the fuel line diameter. A pair of pliers or a fuel line cutter is also useful for preparing the lines. Additionally, have a fuel line tape or compound ready for sealing. It's important to have the right tools to ensure a professional and secure attachment.
Preventing fuel leaks is crucial for safety. Before attaching the fuel lines to the engine, ensure the engine is cool to avoid any heat-related issues. Inspect the engine fittings and fuel line connections for any damage or corrosion. Use a fuel-resistant tape or compound to seal the connections, ensuring a tight fit. Always follow the manufacturer's guidelines for the specific engine model. Regularly check for any signs of leaks and address them promptly.