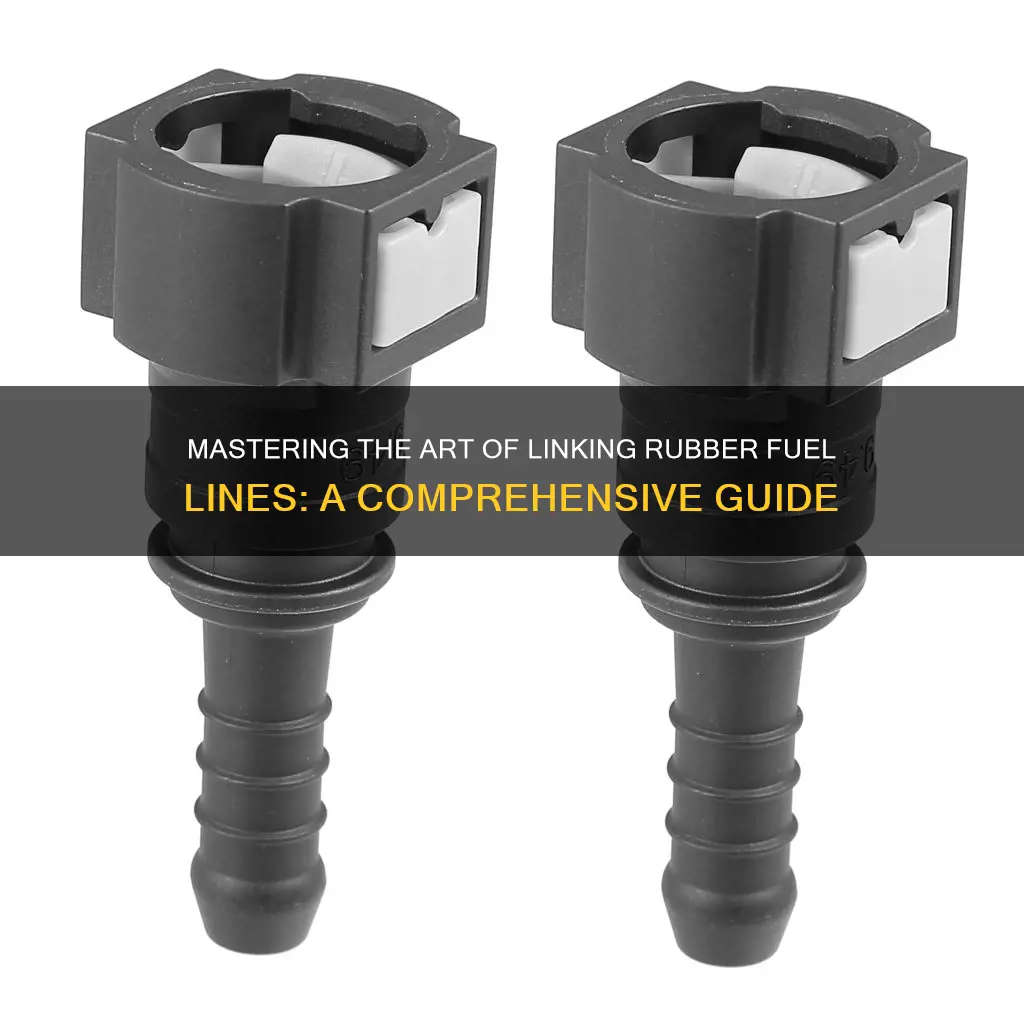
Connecting two rubber fuel lines requires careful attention to ensure a secure and leak-free join. This process involves preparing the lines by cleaning and deburring the ends, then using a suitable adhesive or heat-shrink coupling to bond the lines together. It's important to follow manufacturer guidelines and best practices to ensure a reliable connection that can withstand the pressures and temperatures encountered in a fuel system.
What You'll Learn
- Preparation: Ensure both lines are clean, dry, and free of debris
- Clamps: Use appropriate fuel line clamps for a secure connection
- Alignment: Align lines properly to avoid kinks and ensure smooth flow
- Fitting Types: Choose the right fitting type for your application
- Testing: Check for leaks and ensure proper pressure before use
Preparation: Ensure both lines are clean, dry, and free of debris
When preparing to connect two rubber fuel lines, it's crucial to ensure that the process is done correctly and safely. The first step in this process is to thoroughly prepare the fuel lines by making sure they are clean, dry, and free of any debris or contaminants. This initial preparation is essential to guarantee a secure and reliable connection.
Start by cleaning each fuel line separately. Use a mild detergent or soap and warm water to remove any dirt, grime, or old fuel residue. Scrub the lines gently with a soft-bristled brush or a clean cloth to ensure no residue remains. Rinse the lines thoroughly with water to eliminate any soap or detergent, and allow them to air dry completely. This cleaning process ensures that there are no foreign particles that could interfere with the connection.
After cleaning, inspect the fuel lines for any signs of damage or wear. Check for cracks, tears, or any other defects that might compromise the integrity of the lines. If you notice any issues, it's best to replace the affected lines to ensure a safe and functional connection.
Once the lines are clean and dry, verify that they are free of debris. Use a fine-tooth comb or a small brush to carefully remove any small particles or lint that may have accumulated during the cleaning process. Pay close attention to the threads or connectors where the lines will be joined, as these areas should be free of any obstructions.
By taking the time to properly prepare the fuel lines, you create a solid foundation for a successful connection. This step ensures that the lines are in optimal condition, allowing for a tight and secure fit when joined together. Proper preparation is a critical aspect of working with fuel lines, as it contributes to the overall safety and efficiency of the fuel system.
Sealing Fuel Lines: A Comprehensive Guide to Effective Repairs
You may want to see also
Clamps: Use appropriate fuel line clamps for a secure connection
When connecting two rubber fuel lines, using the right clamps is crucial for a secure and reliable connection. Clamps play a vital role in ensuring that the fuel lines remain tightly sealed and do not leak, which is essential for the safe operation of your vehicle's fuel system. Here's a step-by-step guide on how to use clamps effectively:
Choose the Right Clamp: Select a fuel line clamp that is specifically designed for rubber fuel lines. These clamps are typically made of durable materials like stainless steel or brass, ensuring they can withstand the corrosive nature of fuel. The clamp should have a smooth, flexible jaw that can conform to the shape of the fuel line without causing damage. Avoid using metal clamps on rubber lines, as they can scratch or cut the material over time.
Prepare the Fuel Lines: Before clamping, ensure that the fuel lines are clean and free of any debris or contaminants. Use a cloth or brush to wipe down the surfaces where the lines will be connected. This step is important to create a tight seal and prevent any foreign matter from interfering with the clamp's effectiveness.
Apply the Clamp: Start by positioning the clamp around the fuel line, ensuring it is centered and aligned with the connection point. Use your hands or a pair of pliers to apply firm pressure to the clamp, tightening it securely. The goal is to create a snug fit without distorting the fuel line's shape. You should feel resistance as you tighten the clamp, indicating a proper connection. Avoid over-tightening, as it can lead to damage to the fuel line.
Secure Multiple Clamps: If you need to connect two fuel lines together, use multiple clamps for added security. Space the clamps evenly along the length of the connection to distribute the pressure evenly. This approach ensures that the connection is robust and less likely to fail. Remember to tighten each clamp firmly, following the same technique as before.
Test for Leaks: After clamping the fuel lines, it's essential to test for any leaks. Turn on the fuel supply and inspect the connections for any signs of fuel escaping. If you notice any leaks, carefully adjust the clamp's position or tighten it further to resolve the issue. Properly secured clamps should provide a tight seal, preventing any fuel loss.
By following these steps and using the appropriate fuel line clamps, you can ensure a secure and leak-free connection between rubber fuel lines. This method is a simple yet effective way to maintain the integrity of your vehicle's fuel system, promoting safety and optimal performance.
QFT SL600 Fuel Line Compatibility: HR600 to SL600 Upgrade
You may want to see also
Alignment: Align lines properly to avoid kinks and ensure smooth flow
When connecting two rubber fuel lines, proper alignment is crucial to ensure a smooth and uninterrupted flow of fuel. Here's a detailed guide on how to achieve this:
- Preparation: Before you begin, ensure you have the necessary tools and materials, including the two fuel lines, connectors or fittings, and any required tools for tightening. Clean the ends of the fuel lines to remove any dirt or debris that might interfere with the connection.
- Alignment Technique: The key to successful alignment is to create a straight and continuous path for the fuel. Start by positioning the two fuel lines side by side, ensuring they are of equal length. Carefully align the ends of the lines, making sure they are parallel to each other. You can use a straight edge or a ruler to guide the alignment, ensuring a precise and straight connection.
- Avoiding Kinks: Kinks in the fuel lines can lead to reduced flow and potential damage. To prevent this, maintain a consistent and straight connection. Avoid bending the lines excessively or forcing them into tight spaces. The goal is to create a smooth transition between the two lines, allowing fuel to flow freely without any obstructions.
- Secure Connection: Once aligned, securely fasten the fuel lines using the appropriate connectors or fittings. Tighten them according to the manufacturer's instructions to ensure a reliable seal. Double-check the connection to make sure it is tight and there are no gaps or leaks. Proper alignment and a secure connection will guarantee a seamless flow of fuel, reducing the risk of engine issues caused by kinks or blockages.
Remember, taking the time to align the fuel lines correctly is essential for optimal engine performance and longevity. This simple step can prevent potential issues and ensure a reliable fuel supply.
Fuel Line Mystery: FL20C's Dual Fuel Lines Explained
You may want to see also
Fitting Types: Choose the right fitting type for your application
When connecting two rubber fuel lines, it's crucial to select the appropriate fitting type to ensure a secure and reliable connection. The right fitting will depend on various factors, including the application, the size of the fuel lines, and the desired level of flexibility and durability. Here's a guide to help you choose the suitable fitting type:
- Compression Fittings: These are commonly used for fuel lines and offer a reliable sealing mechanism. Compression fittings consist of a ferrule (usually made of metal) that is crimped or compressed onto the fuel line. The ferrule compresses the line's outer layer, creating a tight seal. This type of fitting is ideal for applications where a strong, leak-free connection is required. When using compression fittings, ensure that the fuel lines are clean and free of debris. Measure the fuel lines carefully to determine the correct ferrule size, as different sizes are available to accommodate various diameters.
- Quick-Connect Fittings: For applications that require frequent disconnection and reconnection, quick-connect fittings are a convenient choice. These fittings typically feature a male and female end, with a locking mechanism to secure the connection. They are often used in racing or recreational vehicles where easy and rapid fuel line changes are necessary. Quick-connect fittings provide a secure seal and are easy to install, making them a popular option for those seeking convenience without compromising performance.
- Clamp-Style Fittings: Clamp fittings use a clamp to secure the fuel lines together. This type of fitting is versatile and can be used for various applications. The clamp applies pressure to the fuel lines, creating a tight seal. Clamp-style fittings are often used in situations where a more permanent connection is desired, as they can be less prone to leakage compared to other types. When installing, ensure that the clamp is properly tightened to achieve a secure hold.
- Swivel Fittings: Swivel fittings are ideal for applications where flexibility is essential. These fittings allow the fuel lines to rotate, providing a range of movement. Swivel fittings are commonly used in situations where the fuel lines need to accommodate angles or bends. They are particularly useful in engine compartments with limited space or when connecting fuel lines to various components that require different orientations.
When selecting a fitting type, consider the specific requirements of your project. For high-performance applications, compression fittings might be the best choice due to their strength and reliability. In contrast, quick-connect fittings offer convenience for frequent disconnections. Clamp-style fittings provide versatility, while swivel fittings excel in situations demanding flexibility. Always ensure that the chosen fitting type is compatible with the fuel line material and size to guarantee a secure and leak-free connection.
Fuel Line Fixes: A Guide to Common Issues and Solutions
You may want to see also
Testing: Check for leaks and ensure proper pressure before use
Before you even consider connecting the two rubber fuel lines, it's crucial to ensure that the system is leak-free and pressurized correctly. This step is essential for safety and the efficient operation of your fuel system. Here's a detailed guide on how to test for leaks and check the pressure:
Leak Testing:
- Prepare the Setup: Ensure you have a clean and dry environment. Gather the necessary tools, including a soapy water solution, a spray bottle, and a clean cloth. You might also want to use a small, portable pump to assist with the testing process.
- Connect the Lines: Carefully connect the two rubber fuel lines, ensuring a tight and secure fit. Use the appropriate connectors or clamps if available. Make sure the lines are properly aligned and there are no kinks or twists that could cause issues.
- Apply Soapy Water: Spray the soapy water solution onto the connections and along the length of both fuel lines. Pay close attention to the joints and any potential leak points. The soap will create a visible lather if there is a leak, making it easier to identify.
- Inspect for Leaks: Carefully examine the entire system. Look for any bubbles forming on the surface of the soapy water. If you see bubbles, it indicates a potential leak. Even a small amount of air or liquid escaping can lead to significant issues over time. Ensure you inspect all connection points, including where the lines attach to the fuel tank and any additional fittings.
- Fix and Re-test: If you find any leaks, carefully disconnect the lines and identify the source of the issue. Repair or replace the damaged parts as necessary. Re-test the system after making the necessary fixes to ensure the problem is resolved.
Pressure Testing:
- Use a Pressure Gauge: Connect a pressure gauge to one end of the fuel line. You can use a small hand pump or a more powerful industrial pump, depending on the system's requirements.
- Apply Pressure Gradually: Start by applying a low level of pressure and gradually increase it. Check the gauge regularly to monitor the pressure rise. The goal is to reach a specific pressure level that is safe and suitable for your fuel system.
- Maintain Pressure: Keep the pressure steady for a few minutes to ensure it holds. If the pressure drops, it may indicate a leak or an issue with the connection.
- Record and Adjust: Record the pressure reading and make any necessary adjustments to reach the desired pressure. This step is crucial for ensuring the fuel lines can handle the required fuel flow and pressure for your application.
Remember, proper testing is an essential safety measure to prevent fuel leaks and potential engine damage. Always follow manufacturer guidelines and best practices for your specific fuel system.
Fuel Line Sizing for the Jeep TJ: A Guide
You may want to see also
Frequently asked questions
Connecting rubber fuel lines requires a careful process to ensure a tight and leak-free seal. Start by cleaning the ends of both lines to remove any dirt or debris. Then, use a fuel line connector kit, which typically includes a ferrule and a crimping tool. Slide the ferrule onto one line, then carefully insert the other line into the ferrule, ensuring it's aligned properly. Use the crimping tool to apply pressure and create a secure connection. Repeat this process for the second line.
You'll need a few essential tools for connecting rubber fuel lines. A fuel line connector kit is the most important, which includes the ferrules and the crimping tool. Additionally, have a pair of pliers or a line cutter for any necessary adjustments or trimming. It's also a good idea to have a rag or cloth to wipe your hands and the lines, ensuring a clean connection.
Rubber fuel lines are generally compatible with most fuel systems. However, it's important to check the specifications of your vehicle or equipment to ensure the lines are the correct size and type. Some fuel lines may have specific requirements, such as being designed for high-pressure applications or certain fuel types. Always refer to the manufacturer's guidelines for the best results.
While rubber is a common and effective material for fuel lines, you can also use other materials like vinyl or nylon, depending on your specific needs. Different materials offer various advantages, such as increased flexibility or resistance to certain chemicals. However, rubber is often preferred due to its durability and compatibility with most fuel systems. Ensure that the chosen material is suitable for the fuel type and operating conditions.