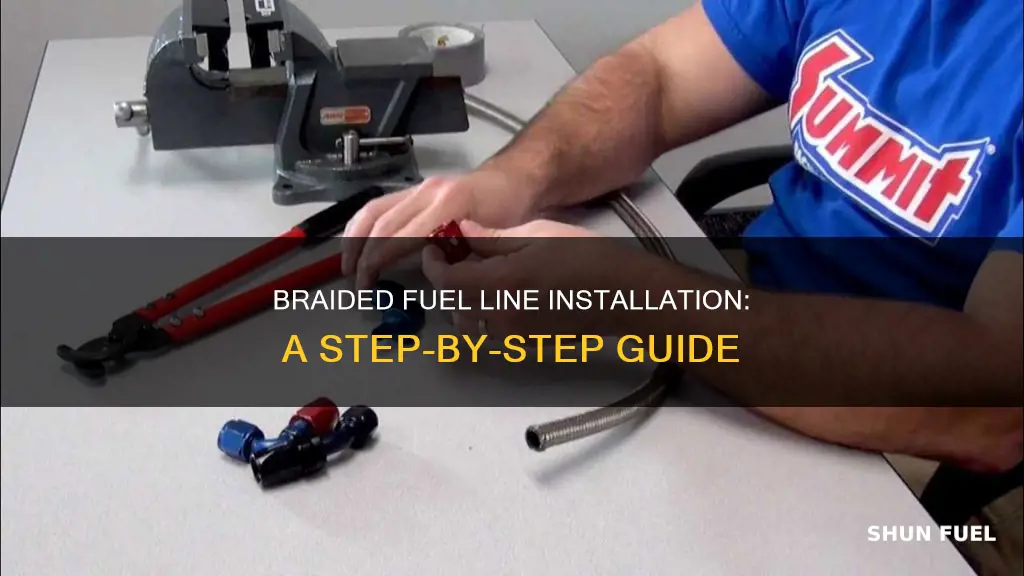
Running braided fuel lines is a crucial step in ensuring the efficient and safe delivery of fuel to your engine. This process involves carefully routing the fuel lines through the engine bay, often in a braided or woven design to protect against damage from heat, vibration, and other potential hazards. By following a few key steps, you can ensure that your fuel lines are properly installed and functioning optimally, contributing to the overall performance and longevity of your vehicle.
What You'll Learn
- Preparation: Clean and inspect the fuel line for damage before installation
- Routing: Route the line away from heat sources and sharp edges
- Clamping: Use appropriate clamps to secure the line in place
- Testing: Check for leaks and ensure proper fuel flow
- Maintenance: Regularly inspect and replace worn-out fuel lines
Preparation: Clean and inspect the fuel line for damage before installation
Before you begin the installation process of a braided fuel line, it is crucial to ensure that the line is in optimal condition to prevent any potential issues. Start by thoroughly cleaning the fuel line to remove any dirt, debris, or old fuel residue. This step is essential as it ensures a clean and smooth surface for the new braided fuel line to be installed. Use a suitable cleaning agent, such as a fuel line cleaner, and apply it to the entire length of the line. Allow the cleaner to work for the recommended time, which typically ranges from a few minutes to an hour, depending on the product. Then, rinse the line with clean water to eliminate any remaining cleaner and ensure a spotless interior.
Once the cleaning process is complete, it's time to inspect the fuel line for any signs of damage or wear. Carefully examine the line for any cuts, punctures, kinks, or cracks. Pay close attention to the areas where the line will be most susceptible to damage, such as bends, fittings, and connections. If you notice any damage, it is crucial to replace the affected section of the fuel line to maintain the integrity of the entire system. Ensure that you have the necessary replacement parts readily available before proceeding.
When inspecting the fuel line, also check for any signs of deterioration, such as brittleness or softening of the material. This could indicate that the line has been exposed to extreme temperatures or harsh chemicals, compromising its strength and flexibility. If you identify any areas of concern, it is best to replace the entire fuel line to avoid potential fuel leaks or system failures.
Additionally, consider the condition of the fittings and connectors. Over time, these components can become corroded or damaged, leading to potential fuel leaks. Inspect the fittings for any signs of corrosion, pitting, or damage. If necessary, clean or replace the fittings to ensure a secure and reliable connection.
By taking the time to clean and inspect the fuel line, you are taking a proactive approach to maintaining your vehicle's fuel system. This preparation step is vital to ensure a successful installation and to prevent any potential issues that may arise from using damaged or contaminated fuel lines. Remember, a well-maintained fuel system contributes to optimal engine performance and longevity.
Rusted Fuel Line: When Check Engine Light Ticks
You may want to see also
Routing: Route the line away from heat sources and sharp edges
When installing a braided fuel line, proper routing is crucial to ensure the system's longevity and performance. One essential aspect of this process is routing the line away from potential heat sources and sharp edges to prevent damage and ensure optimal functionality. Here's a detailed guide on how to achieve this:
Start by identifying potential heat sources in your vehicle's engine bay. These could include exhaust manifolds, catalytic converters, or even the engine block itself, especially in older vehicles. Braided fuel lines are designed to be flexible, but excessive heat can still cause degradation over time. By routing the line away from these heat sources, you create a protective barrier, ensuring the fuel line remains in good condition. Use heat shields or insulation materials if necessary to further safeguard the line.
Additionally, be mindful of sharp edges and protruding components within the engine bay. These could include engine mounts, transmission mounts, or even the frame rails. Sharp edges can cut or damage the braided fuel line, leading to fuel leaks and potential safety hazards. When routing the line, ensure it is positioned at a safe distance from these sharp objects. Consider using protective sleeves or tubing to guide the line around these areas, providing an extra layer of protection.
The routing process should also consider the overall layout of the engine bay. Aim to keep the fuel line as straight as possible to minimize stress on the braided material. Avoid sharp bends or kinks, as these can lead to reduced flexibility and potential failure points. Allow the line to follow the natural contours of the engine bay, ensuring it is not cramped or forced into awkward positions.
When routing around obstacles, use the natural curves and contours of the vehicle's components. For example, if you need to route the line around a large component, follow its shape rather than forcing the line into an unnatural path. This approach ensures the line remains flexible and reduces the risk of damage.
Remember, the goal is to create a safe and efficient path for the braided fuel line, minimizing its exposure to potential hazards. By following these routing guidelines, you can ensure a reliable and long-lasting fuel system for your vehicle. Proper routing is a critical step in the installation process, contributing to the overall performance and safety of your vehicle's fuel system.
Optimizing Fuel Return Line Size: A Comprehensive Guide
You may want to see also
Clamping: Use appropriate clamps to secure the line in place
When working with braided fuel lines, proper clamping is essential to ensure a secure and reliable connection. The first step is to identify the correct type of clamp for your specific application. Braided fuel lines often require specialized clamps that can withstand the high pressure and temperature fluctuations associated with fuel systems. These clamps are typically made from durable materials such as stainless steel or aluminum to ensure longevity and resistance to corrosion.
Start by cleaning the fuel line and the area where the clamp will be applied. Remove any dirt, debris, or old clamps to ensure a clean and smooth surface for the new clamp. Measure the length of the fuel line section you intend to secure and cut the clamp to the appropriate size. Ensure that the clamp is slightly longer than the fuel line section to allow for a snug fit.
Position the clamp over the fuel line, aligning the clamp's mounting holes with the fuel line's fittings or mounting points. Use the appropriate tools, such as a wrench or pliers, to tighten the clamp securely. The goal is to create a firm grip without causing damage to the fuel line. Over-tightening can lead to line distortion or damage, so be cautious and use controlled force.
Check the clamp's orientation to ensure it is positioned correctly and securely fastened. The clamp should be tight enough to prevent any movement or leakage but not so tight that it causes damage. Adjust the clamp as needed to achieve the desired level of security. It is crucial to maintain a consistent and firm grip throughout the clamping process.
Remember that the specific clamping techniques may vary depending on the fuel line's diameter, the type of fittings used, and the overall system design. Always refer to the manufacturer's guidelines or consult a professional for detailed instructions tailored to your particular fuel line setup. Proper clamping ensures the safety and efficiency of your fuel system, preventing potential leaks and maintaining optimal performance.
Diesel Fuel Line Bio Removal: Tips and Tricks
You may want to see also
Testing: Check for leaks and ensure proper fuel flow
When it comes to testing the braided fuel line, ensuring that it is leak-free and functioning correctly is crucial for the safe and efficient operation of your vehicle. Here's a step-by-step guide to help you with this process:
Leak Detection: Begin by inspecting the fuel line for any visible signs of damage or deterioration. Look for cracks, punctures, or any areas where the line might be rubbing against sharp edges or components. Use a bright flashlight to illuminate the line and inspect it thoroughly. If you notice any issues, it's essential to address them before proceeding. You can use a soapy water solution to perform a visual inspection. Apply the solution to the fuel line and look for bubbles, as they indicate potential leaks. This method is particularly useful for hard-to-reach areas.
Pressure Testing: Set up a pressure testing system to check for leaks and ensure the integrity of the fuel line. This can be done using a fuel pressure gauge and a hand pump or a dedicated fuel pressure tester. Start by ensuring the engine is off and the vehicle is in a stable position. Connect the gauge to the fuel line and pump up the pressure gradually. Observe the gauge for any drops in pressure, which could indicate a leak. It's important to follow the manufacturer's guidelines for the correct pressure range. If the pressure drops significantly, you may need to tighten connections or replace the fuel line.
Flow Rate Measurement: Proper fuel flow is essential for optimal engine performance. To check the flow rate, you can use a fuel flow meter or a calibrated container. Start by disconnecting the fuel line from the fuel tank and securely attaching the flow meter. Turn on the engine and allow it to idle. Measure the fuel flow over a set period, typically 5-10 minutes, and compare it to the expected values for your vehicle. If the flow rate is significantly lower than the specified range, it may indicate a restriction or leak in the fuel line.
Visual Inspection After Testing: After completing the pressure and flow tests, perform a thorough visual inspection of the entire fuel line system. Look for any signs of damage, corrosion, or debris buildup. Check all connections and fittings for tightness and secure them if necessary. Ensure that the fuel line is routed away from heat sources and sharp objects to prevent further damage.
Remember, regular maintenance and testing of the braided fuel line are vital to prevent fuel-related issues and ensure your vehicle's reliability. Always refer to the manufacturer's instructions for specific guidelines and safety precautions during the testing process.
Toyota Fuel Line Removal: A Step-by-Step Guide for Beginners
You may want to see also
Maintenance: Regularly inspect and replace worn-out fuel lines
Regular maintenance of your braided fuel lines is crucial to ensure optimal performance and longevity. Over time, fuel lines can deteriorate due to various factors, including fuel contamination, age, and environmental conditions. Here's a comprehensive guide on how to inspect and replace worn-out fuel lines:
Visual Inspection: Start by visually examining the braided fuel lines. Look for any signs of damage, such as cracks, brittleness, or visible wear. Check for any leaks or moisture accumulation around the connections. Pay close attention to areas where the fuel lines are exposed to extreme temperatures or vibrations, as these factors can accelerate degradation. Inspect the entire length of the fuel lines, including the fittings and clamps, to identify any potential issues.
Pressure Testing: Conducting a pressure test is an effective way to assess the integrity of the fuel lines. Use a fuel line pressure tester to apply pressure to the system. Start with a low pressure and gradually increase it while monitoring for any leaks or abnormalities. If you notice any signs of leakage or pressure drop, it indicates potential damage to the fuel lines, and replacement is necessary.
Replacement Process: When you identify worn-out fuel lines, it's essential to replace them promptly. Start by disconnecting the fuel lines from the fuel tank and the engine. Carefully remove the old lines, ensuring you don't damage the surrounding components. Clean the fittings and ensure they are free from debris. Measure the new fuel lines to ensure they fit perfectly, and use the appropriate tools to secure the connections. Tighten the fittings securely but avoid over-tightening to prevent damage.
Safety Precautions: Working with fuel lines requires caution to avoid accidents. Always wear protective gear, such as gloves and safety goggles, to prevent fuel contact with your skin and eyes. Ensure proper ventilation in the work area to minimize the inhalation of fuel vapors. Dispose of the old fuel lines and fuel safely, following local regulations.
Remember, regular maintenance and timely replacement of worn-out fuel lines are essential to maintain the efficiency and safety of your vehicle's fuel system. By following these steps, you can ensure that your braided fuel lines remain in optimal condition, providing reliable performance for years to come.
T100 Fuel Line Guide: Choosing the Right Option
You may want to see also
Frequently asked questions
Braided fuel lines are an essential component in fuel delivery systems, especially for high-performance vehicles or those with modified engines. They are designed to replace traditional rubber hoses, offering several advantages. Braided lines provide a more flexible and durable solution, ensuring a reliable fuel supply while reducing the risk of fuel leaks and improving overall performance.
Installing braided fuel lines is a straightforward process, but it requires some patience and the right tools. First, ensure you have the appropriate size and length of braided line for your specific application. Start by cutting the line to the desired length, then slide the fuel connector onto the line, making sure it fits snugly. Next, slip the line through the fuel rail or filter, routing it carefully to avoid any sharp bends. Secure the line with clamps or ties, ensuring a tight and neat fit. Finally, connect the fuel pump and injectors, double-checking all connections for tightness.
Braided fuel lines are generally compatible with most fuel types, including gasoline, diesel, and ethanol blends. However, it's crucial to check the manufacturer's specifications for your specific fuel line model. Some braided lines may have limitations with certain fuel additives or extreme temperatures, so always refer to the product guidelines for compatibility and recommended usage.
To ensure the longevity of your braided fuel line, it's essential to handle and install it with care. Avoid sharp bends or kinks, as these can lead to reduced flexibility and potential fuel leaks. Always route the line away from sharp edges, heat sources, or areas prone to vibration. Regularly inspect the line for any signs of wear or damage, and replace it if necessary. Proper maintenance and careful installation will help maintain the integrity of the braided fuel line.