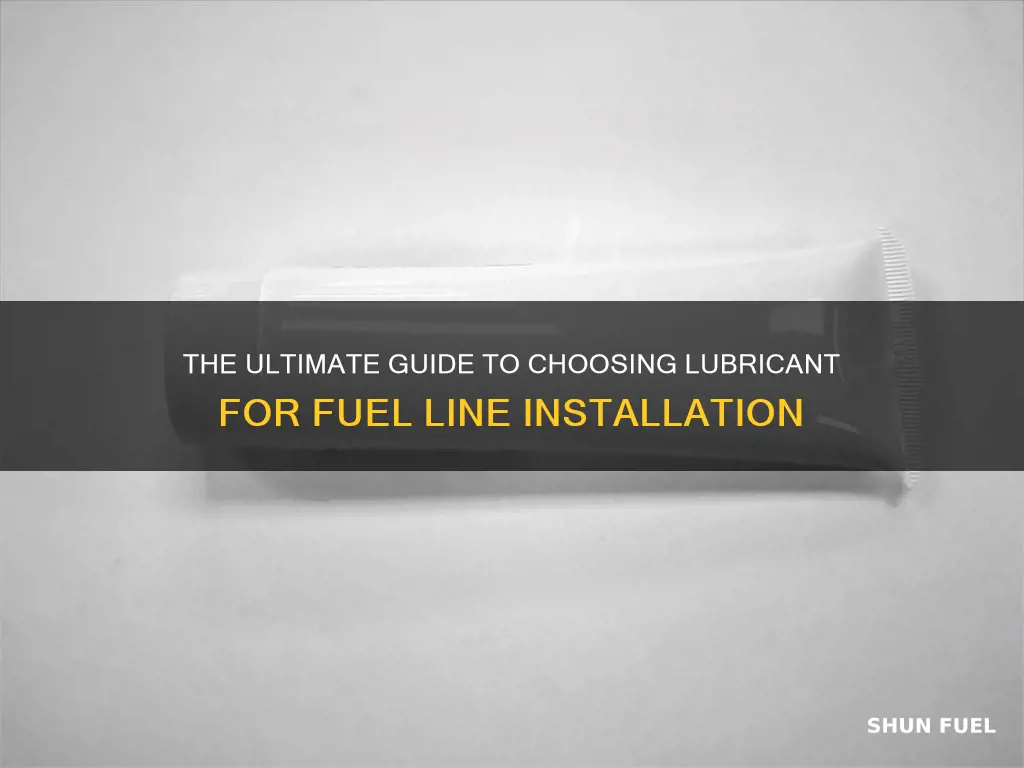
When installing a new fuel line, it's important to choose the right lubricant to ensure a secure and leak-free connection. The type of lube you select can impact the overall performance and longevity of your fuel system. This guide will provide insights into the best lubricants for connecting new fuel lines, ensuring a smooth and reliable installation process.
What You'll Learn
- Fuel Line Material Compatibility: Ensure the lube is compatible with the fuel line material to prevent degradation
- Viscosity Considerations: Choose a lube with appropriate viscosity for the fuel line's diameter and flow rate
- Temperature Range: Select a lube that can withstand the temperature extremes of the fuel line's environment
- Corrosion Prevention: Use a lube that prevents corrosion in the fuel line, especially if it contains metal components
- Ease of Application: Opt for a lube that is easy to apply and dries quickly to avoid mess and residue
Fuel Line Material Compatibility: Ensure the lube is compatible with the fuel line material to prevent degradation
When working on a fuel system, it's crucial to consider the compatibility of lubricants with the materials used in the fuel lines. The primary goal is to prevent any degradation or damage to the fuel line, which could lead to fuel leaks, reduced performance, or even system failure. Here's a detailed guide on ensuring compatibility:
Understanding Fuel Line Materials: Different types of fuel lines are made from various materials, such as rubber, vinyl, or synthetic compounds. Rubber is a common choice due to its flexibility and durability. Vinyl is also used, especially in older systems. Synthetic materials, like polyurethane, offer enhanced resistance to fuel degradation. Identifying the specific material of your fuel line is essential before selecting a lubricant.
Lubricant Compatibility: The key to a successful fuel line installation or repair is using a lubricant that is compatible with the chosen material. For rubber fuel lines, a suitable lubricant might be a synthetic-based grease or a silicone-based compound. These lubricants provide a protective barrier, ensuring the fuel line remains intact and flexible. For vinyl lines, a different approach is required, as some lubricants can cause degradation. In such cases, a mild detergent or a specialized vinyl lubricant is recommended.
Preventing Degradation: Incompatible lubricants can lead to fuel line degradation, which is a serious issue. For instance, using a petroleum-based lubricant on a rubber fuel line can cause swelling and cracking over time. Similarly, certain lubricants can attack the protective coating on synthetic fuel lines, leading to material breakdown. Always refer to the manufacturer's guidelines or seek expert advice to ensure you select the right lubricant for the specific fuel line material.
Application Techniques: Proper application of the lubricant is as important as its compatibility. When lubricating fuel lines, ensure an even coating without excess product. Over-lubrication can attract dirt and debris, potentially causing blockages. For connections, a small amount of lubricant on the threads and a light coating on the fuel line can be sufficient. Always wipe away any excess to avoid contamination.
Testing and Inspection: After applying the lubricant, it's beneficial to test the system's performance. This includes checking for leaks, ensuring proper fuel flow, and monitoring the vehicle's overall behavior. Regular inspections can help identify any issues related to lubricant compatibility, allowing for prompt action to prevent further damage.
Air in Diesel Fuel Lines: Causes and Solutions
You may want to see also
Viscosity Considerations: Choose a lube with appropriate viscosity for the fuel line's diameter and flow rate
When connecting a new fuel line, it's crucial to consider the viscosity of the lubricant you use. Viscosity is a measure of a fluid's resistance to flow and is directly related to the fuel line's diameter and flow rate. The right viscosity ensures optimal performance and longevity of the fuel line connection.
For smaller fuel lines with a diameter of 1/4 inch or less, a low-viscosity lubricant is recommended. These lubricants, typically in the range of 100-200 cSt (centistokes), are easy to apply and provide sufficient lubrication without hindering the flow of fuel. This is especially important in high-performance applications where fuel needs to move quickly and efficiently.
As the fuel line diameter increases, the viscosity of the lubricant should also increase. For lines with a diameter of 3/8 inch or more, a medium-viscosity lubricant, ranging from 200-400 cSt, is ideal. This viscosity ensures that the lubricant provides adequate protection and sealing without restricting the flow of fuel. It's a balance that ensures the fuel line functions optimally while maintaining a secure connection.
In some cases, where the fuel line has a high flow rate or is subjected to extreme temperatures, a higher-viscosity lubricant might be necessary. These lubricants, typically above 400 cSt, offer excellent protection against wear and tear and can withstand the demands of high-performance engines. However, it's essential to choose a lubricant that is compatible with the fuel type to avoid any potential issues.
In summary, when selecting a lubricant for connecting a new fuel line, it's vital to match the viscosity to the fuel line's diameter and flow rate. This ensures a secure, efficient, and long-lasting connection, contributing to the overall performance and reliability of the fuel system. Always refer to the manufacturer's guidelines and consult experts if needed to make the best choice.
Understanding the Role of Fuel Line Pumps in Vehicles
You may want to see also
Temperature Range: Select a lube that can withstand the temperature extremes of the fuel line's environment
When it comes to choosing the right lubricant for connecting a new fuel line, one of the most critical factors to consider is the temperature range it can withstand. Fuel lines are exposed to a wide range of temperatures, from extreme cold during winter to high heat generated by the engine's operation. Therefore, selecting a lubricant that can perform optimally across this temperature spectrum is essential to ensure the longevity and reliability of your fuel system.
The temperature extremes in a fuel line environment can vary significantly. During winter, temperatures can drop well below freezing, causing the fuel to thicken and potentially leading to clogs or reduced performance. In contrast, summer heat can cause fuel to expand, potentially leading to leaks or damage to the fuel line itself. Therefore, the chosen lubricant must remain stable and effective under these varying conditions.
A suitable lubricant should have a high flash point and a low pour point. The flash point is the temperature at which the lubricant can withstand an open flame without igniting, ensuring it can handle the heat generated by the engine. A low pour point means the lubricant remains in a usable liquid state even at very low temperatures, preventing it from becoming too thick and hard to work with.
Synthetic lubricants, such as those based on polyalphaolefins (PAOs) or polyol esters, are often recommended for fuel lines. These synthetic lubricants offer excellent thermal stability, meaning they can withstand the wide temperature variations without breaking down or losing their lubricating properties. They also have a high resistance to oxidation, which helps prevent the formation of harmful deposits within the fuel system.
Additionally, some lubricants are specifically designed for fuel systems and are formulated to meet the unique challenges of this application. These products often include additives that provide additional protection against wear and corrosion, ensuring that the fuel line remains in optimal condition even in the harshest environments. Always refer to the manufacturer's guidelines and consult with experts to select the most appropriate lubricant for your specific fuel line and engine requirements.
Understanding Fuel Line Hose Clamp Sizes: A Comprehensive Guide
You may want to see also
Corrosion Prevention: Use a lube that prevents corrosion in the fuel line, especially if it contains metal components
When installing a new fuel line, it's crucial to consider the type of lubricant used to ensure optimal performance and longevity. One of the primary concerns is corrosion prevention, especially in fuel lines that contain metal components. Corrosion can lead to fuel leaks, reduced engine performance, and even potential safety hazards. Therefore, selecting the right lubricant is essential.
The fuel line is a critical component of the fuel system, responsible for transporting fuel from the tank to the engine. It often contains metal components such as fittings, clamps, and fuel injectors, which are susceptible to corrosion. Corrosion can occur due to the presence of moisture, fuel contaminants, or exposure to harsh environmental conditions. Over time, this corrosion can lead to the degradation of the fuel line's integrity, causing leaks and potential engine damage.
To prevent corrosion, it is recommended to use a lubricant specifically designed for fuel lines. These lubricants are typically made from corrosion-resistant materials and are formulated to provide a protective barrier between the metal components and the surrounding fuel. One popular option is a synthetic-based lubricant, which offers excellent anti-corrosion properties. Synthetic lubricants are known for their stability and resistance to breakdown, ensuring that the fuel line remains protected even in harsh conditions.
When choosing a lubricant, look for products that are specifically labeled for fuel line applications. These lubricants are often designed to withstand the high-pressure and temperature fluctuations experienced in the fuel system. Additionally, they may contain additives that further enhance corrosion prevention. Some lubricants are even compatible with ethanol-blended fuels, which are commonly used in modern vehicles, ensuring that the lubricant can adapt to various fuel types.
In summary, when connecting a new fuel line, prioritize corrosion prevention by using a specialized lubricant. This will help maintain the integrity of the fuel line, especially in metal components, and ensure the overall reliability of the fuel system. Always refer to the manufacturer's guidelines and consult with automotive experts for the most suitable lubricant options for your specific vehicle and fuel line requirements.
E85 Fuel Line Maintenance: What to Flush and Why
You may want to see also
Ease of Application: Opt for a lube that is easy to apply and dries quickly to avoid mess and residue
When it comes to choosing the right lubricant for connecting a new fuel line, ease of application is a crucial factor to consider. You want a product that is straightforward to use and doesn't require complex procedures or multiple steps, especially in a situation where time is of the essence. Opt for a lube that is designed for quick and easy application, ensuring that the process is as simple and efficient as possible. This will help you avoid any unnecessary mess and residue, which can be a real headache when working with fuel lines.
Look for lubricants that come in convenient packaging, such as spray cans or squeeze bottles, as these allow for precise control and an even distribution of the product. This type of packaging is ideal for hard-to-reach areas and ensures that you can apply the lube without creating a mess. Additionally, a quick-drying formula is essential to prevent any unwanted residue or stickiness, which could interfere with the proper functioning of the fuel line.
Some lubricants are specifically formulated for fuel line installations, making them an excellent choice for this particular task. These products are designed to be user-friendly, often with a low viscosity that allows for easy application and rapid drying. They are typically non-greasy, ensuring that there is no excess product left behind, which could attract dirt and debris. This type of lube is a preferred option as it provides the necessary protection without the hassle of dealing with messy residue.
Another advantage of using a lube that dries quickly is the reduced risk of contamination. When working with fuel lines, you want to minimize any potential interference with the fuel's purity. A fast-drying lubricant ensures that the fuel line is ready for use immediately after installation, without any lingering traces of the lube that could affect performance. This is especially important in high-performance engines where every component must function optimally.
In summary, when selecting a lubricant for connecting a new fuel line, prioritize products that are easy to apply and have a rapid drying time. This approach will help you maintain a clean and efficient installation process, ensuring that your fuel line is ready for use without any unwanted mess or residue. Remember, the goal is to find a lube that simplifies the task and provides the necessary protection for your fuel system.
Fuel Line Protests: Dakota's Burning Questions
You may want to see also
Frequently asked questions
When connecting a new fuel line, it is recommended to use a high-temperature silicone grease or a fuel-resistant tape. These materials ensure a secure and leak-free connection, as they provide a protective barrier against fuel leakage and can withstand the high temperatures typically encountered in fuel systems.
No, regular grease is not suitable for this application. Regular grease can become soft and lose its lubricating properties when exposed to fuel, leading to potential leaks. It's important to choose a lubricant specifically designed for fuel lines to ensure long-term reliability.
Start by cleaning the connectors to remove any dirt or debris. Then, apply a small amount of lubricant to the threads and O-rings of the connectors. Ensure you cover the entire surface to create a secure seal. Over-lubrication can lead to excess material entering the fuel system, so use a light, even coating.
Yes, it's best to avoid using petroleum-based lubricants like white lithium grease, as they can attract dirt and moisture, leading to corrosion. Also, stay away from silicone-based lubricants that are not fuel-resistant, as they may dissolve over time, causing potential issues.
Using no lubricant at all is not recommended. Proper lubrication is essential to ensure a tight connection and prevent fuel leaks. Without lubricant, the fuel line may not seal properly, leading to potential engine performance issues and safety hazards.