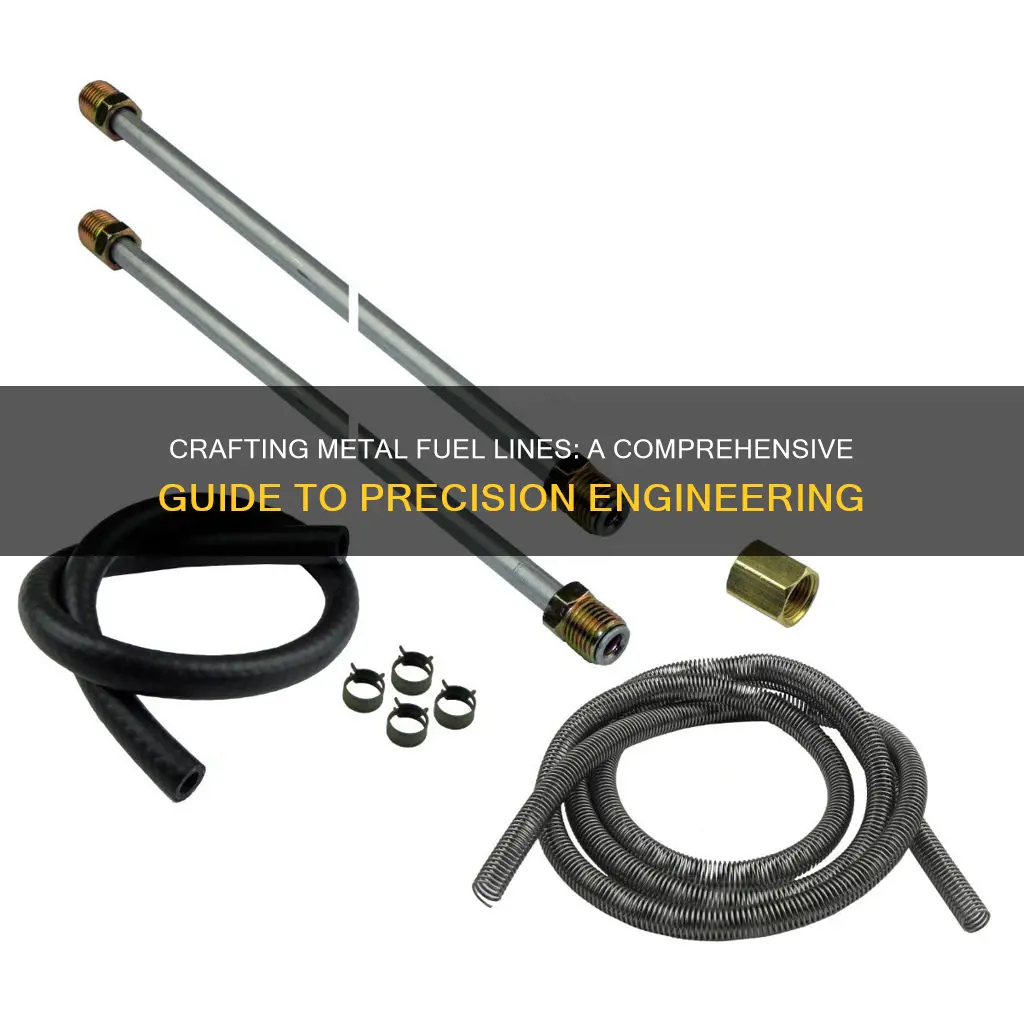
Metal fuel lines are an essential component in many automotive and industrial applications, providing a robust and reliable way to transport fuel. Manufacturing these lines involves several key steps, including selecting the appropriate metal material, such as aluminum or stainless steel, for its strength and corrosion resistance. The process begins with precise cutting and bending of the metal to fit the specific dimensions required for the fuel line. Next, the metal is often welded or brazed to ensure a strong and leak-proof connection. Finally, the fuel lines may be coated or treated to enhance their durability and resistance to fuel degradation. This process ensures that the fuel lines can withstand high pressure and temperature, making them a vital part of any fuel system.
What You'll Learn
- Material Selection: Choose appropriate metal, considering factors like durability and corrosion resistance
- Design Considerations: Ensure lines are designed to withstand pressure, temperature, and vibration
- Fabrication Techniques: Employ methods like bending, welding, and soldering for precise construction
- Coating and Protection: Apply protective coatings to prevent corrosion and ensure long-term reliability
- Testing and Inspection: Conduct thorough testing to ensure fuel lines meet safety standards and performance requirements
Material Selection: Choose appropriate metal, considering factors like durability and corrosion resistance
When it comes to creating metal fuel lines, the choice of material is critical to ensure the system's longevity and safety. The primary consideration here is durability, as fuel lines need to withstand high pressure and temperature variations, as well as potential impacts during vehicle operation. One of the most commonly used metals for this application is stainless steel, specifically grades like 304 or 316. These grades offer excellent corrosion resistance, which is crucial in preventing fuel degradation and ensuring the purity of the fuel supply. Stainless steel's ability to resist oxidation and chloride-induced corrosion makes it ideal for fuel lines, especially in environments with varying humidity and temperature.
Another option is aluminum, which is known for its lightweight properties and excellent corrosion resistance. Aluminum fuel lines are often used in racing applications or where weight reduction is a priority. However, it's important to note that aluminum may not be as durable as stainless steel in certain environments, especially when exposed to saltwater or highly corrosive substances. For these reasons, it's essential to consider the specific conditions of the fuel system's operation.
For applications requiring even higher durability, consider using alloys like Inconel or Monel. These materials are known for their exceptional resistance to heat, corrosion, and mechanical stress. While they are more expensive, they provide an added layer of protection against extreme conditions, making them suitable for high-performance vehicles or specialized industrial applications. The choice of metal should also consider the compatibility with the fuel type. For instance, some metals may react with certain fuels, leading to degradation or contamination.
In addition to the metal's inherent properties, the surface treatment and coating can significantly impact durability. Applying a protective coating or plating can enhance corrosion resistance and provide a barrier against fuel-related chemical reactions. This is particularly important for the internal surface of the fuel lines to prevent any potential contamination. The manufacturing process should also be optimized to ensure consistent quality and minimize the risk of defects that could compromise the fuel line's integrity.
In summary, the material selection for metal fuel lines is a critical aspect of the design process. It requires a careful consideration of factors such as environmental conditions, fuel type, and the desired performance characteristics. By choosing the right metal and implementing appropriate surface treatments, engineers can create fuel lines that are not only durable but also reliable and safe for their intended use.
Saab 01 Fuel Line: Return Line Mystery Solved
You may want to see also
Design Considerations: Ensure lines are designed to withstand pressure, temperature, and vibration
When designing metal fuel lines, it is crucial to consider the environmental factors that the lines will be exposed to during operation. The primary goal is to ensure the lines can withstand the pressures, temperatures, and vibrations encountered in the engine bay. Here are some key design considerations to achieve this:
Material Selection: Choose a suitable metal alloy that can handle the expected pressure and temperature ranges. Common choices include stainless steel, aluminum, or brass, each offering different advantages. For instance, stainless steel provides excellent corrosion resistance and strength, making it ideal for high-pressure applications. Aluminum is lightweight and offers good thermal conductivity, which can be beneficial in managing heat dissipation. Consider the specific requirements of your fuel system and select a material that meets or exceeds those standards.
Line Diameter and Wall Thickness: The dimensions of the fuel lines should be carefully calculated to handle the anticipated pressure. Thicker walls and larger diameters can accommodate higher pressure differentials without compromising structural integrity. However, it's important to balance this with the need for flexibility to avoid excessive rigidity, which could lead to installation and operational issues. A compromise between strength and flexibility is essential to ensure the lines can withstand pressure while remaining manageable.
Reinforcement and Protection: To enhance the lines' ability to withstand vibrations, consider incorporating reinforcement techniques. This could involve braiding or spiraling the metal wire around the fuel line or using a protective covering, especially in areas prone to mechanical stress. Additionally, routing the lines away from sharp edges, heat sources, or high-vibration components can help prevent damage and ensure longevity.
Bending Radius and Flexibility: Fuel lines must be flexible to accommodate engine movement and various operating conditions. Design the lines with an appropriate bending radius to avoid kinking or bending beyond their structural limits. A well-designed fuel line should have a smooth, gradual bend to ensure it can flex without compromising its integrity. This is particularly important in high-vibration environments where sudden bends or sharp turns could lead to premature failure.
Testing and Simulation: Before finalizing the design, conduct thorough testing and simulations to validate the fuel lines' performance. Subject the lines to pressure, temperature, and vibration tests to ensure they meet the required specifications. Computer-aided simulations can also help predict the behavior of the lines under various conditions, allowing for adjustments to the design before physical prototyping.
Fuel Line Routing: Connecting Cylinder Heads for Optimal Performance
You may want to see also
Fabrication Techniques: Employ methods like bending, welding, and soldering for precise construction
When it comes to fabricating metal fuel lines, employing various techniques is essential to ensure a precise and reliable construction. One fundamental method is bending, which allows you to create custom curves and angles to fit the specific requirements of your fuel line design. Start by selecting a metal sheet or tube that matches the desired dimensions. Use a bench or pipe bender to carefully bend the material, ensuring the bend radius is appropriate for the application. Practice and precision are key here; you want to avoid any sharp bends that could compromise the structural integrity of the fuel line.
Welding is another critical fabrication technique. This process joins two or more metal pieces together, creating a strong and durable connection. For fuel lines, you'll typically use a gas welding process, such as oxy-fuel welding or TIG (Tungsten Inert Gas) welding. Prepare the metal surfaces by cleaning and removing any oxidation, then apply a suitable welding rod and a protective shielding gas. Practice good welding techniques, including proper arc control and consistent travel speed, to ensure a clean and strong weld bead.
Soldering is an excellent method for creating joints in metal fuel lines, especially when dealing with thinner materials. This process involves melting a solder alloy between two metal surfaces, creating a strong bond. Prepare the metal surfaces by cleaning them and ensuring they are free of any contaminants. Apply a flux to the joint area to promote adhesion, then heat the joint until the solder melts and flows, forming a secure connection. Soldering requires precision and a steady hand to avoid any voids or weak spots in the joint.
Additionally, consider using metal braze welding for joining dissimilar metals or materials with different melting points. This technique involves using a braze alloy that melts at a temperature lower than the base metals, allowing for a strong bond without the risk of damaging the materials. Braze welding can be particularly useful in fuel line applications where different metals or alloys are used in the construction.
In summary, the fabrication of metal fuel lines involves a combination of bending, welding, and soldering techniques. Bending provides the necessary flexibility and customizability, while welding ensures strong and durable connections. Soldering and braze welding techniques offer precise methods for joining various metal components. Each of these processes requires skill, precision, and attention to detail to create high-quality fuel lines that can withstand the demands of their intended use.
Subaru Fuel Line Disconnect: A Step-by-Step Guide
You may want to see also
Coating and Protection: Apply protective coatings to prevent corrosion and ensure long-term reliability
When it comes to creating metal fuel lines, one crucial aspect often overlooked is the application of protective coatings. These coatings play a vital role in preventing corrosion and ensuring the long-term reliability of the fuel lines. Here's a detailed guide on how to approach this process:
Understanding the Importance of Coating:
Metal fuel lines, despite their strength, are susceptible to corrosion, especially when exposed to harsh environments and fuel chemicals. Corrosion can lead to leaks, reduced efficiency, and even system failures. By applying protective coatings, you create a barrier that safeguards the metal, preventing direct contact with corrosive elements. This simple yet effective measure significantly extends the lifespan of the fuel lines.
Choosing the Right Coating Material:
The first step is selecting an appropriate coating material. Common choices include epoxy, polyurethane, or specialized fuel-resistant coatings. Consider the specific requirements of your fuel system. For instance, if the fuel contains ethanol, you might need a coating that can withstand its corrosive properties. Research and choose a coating that offers excellent adhesion, flexibility, and resistance to the fuel's chemical composition.
Preparation and Application:
Coating application requires careful preparation. Start by thoroughly cleaning the metal fuel lines to remove any dirt, grease, or old coatings. Ensure the surface is dry and free from contaminants. Then, apply the chosen coating material using a spray gun or brush, following the manufacturer's instructions. Multiple coats may be necessary for optimal protection. Allow sufficient time for each coat to dry and cure before handling or operating the fuel system.
Consider Environmental Factors:
Different environments demand specific coating considerations. For outdoor installations or areas with high humidity, choose coatings with excellent UV resistance and moisture barrier properties. In industrial settings, coatings should withstand abrasive conditions and chemical exposure. Always select a coating that aligns with the unique challenges of your operating environment.
Regular Maintenance and Inspection:
Even after applying protective coatings, regular maintenance is essential. Inspect the fuel lines periodically for any signs of damage, wear, or peeling coating. Address issues promptly to prevent further corrosion. Additionally, keep an eye on the fuel quality and system performance, as changes in fuel composition may require re-coating or adjustments to the protective measures.
By following these guidelines, you can effectively protect metal fuel lines, ensuring they remain reliable and efficient over an extended period. Remember, proper coating is a critical step in the process of making metal fuel lines, contributing to the overall safety and performance of your fuel system.
Small Engine Fuel Line: Choosing the Right Option for Your Needs
You may want to see also
Testing and Inspection: Conduct thorough testing to ensure fuel lines meet safety standards and performance requirements
When it comes to creating metal fuel lines, thorough testing and inspection are crucial to ensure the safety and performance of the final product. Here's a detailed guide on how to conduct these essential checks:
Pressure Testing: One of the primary methods to assess the integrity of metal fuel lines is through pressure testing. This process involves subjecting the fuel lines to various pressure levels, simulating real-world conditions. Start by filling the fuel lines with a suitable test fluid, such as water or a specialized fuel line testing liquid. Gradually increase the pressure to a level that exceeds the expected operating pressure. Observe for any leaks, bulging, or signs of damage. Leaks can indicate poor soldering or welding techniques, while bulging may suggest structural weaknesses. Ensure that the fuel lines can withstand the specified pressure without failure, as this directly impacts their ability to contain fuel safely.
Flexibility and Bend Testing: Metal fuel lines need to be flexible to accommodate engine movements and potential vibrations. Conduct bend testing by carefully bending the fuel lines at various angles and radii. Observe if the lines kink, crack, or show signs of permanent deformation. The goal is to ensure that the fuel lines can bend without compromising their structural integrity. This test is particularly important for fuel lines that will be routed through tight spaces or experience frequent movement.
Leak Detection: After pressure and bend testing, leak detection is a critical step. Use a soap solution or a specialized leak detection kit to coat the fuel lines. Allow the lines to dry, then observe for any bubbles forming on the surface. Bubbles indicate the presence of leaks, which could be due to soldering or welding defects. Repair or replace the affected sections to ensure there are no weak points that could lead to fuel leaks during operation.
Performance Evaluation: Testing should also focus on the performance aspects of the fuel lines. This includes checking for proper fuel flow rates, ensuring that the lines can handle the required fuel volume and pressure. Use flow meters and pressure gauges to measure and compare the performance against specifications. Any deviations from the expected values should be addressed and corrected.
Visual Inspection: Throughout the testing process, visual inspection is essential. Look for any visible defects, such as sharp bends, cracks, corrosion, or signs of material degradation. These issues may not be apparent during pressure testing but can become evident over time. Regular visual inspections can help identify potential problems early on and ensure the overall quality of the fuel lines.
By following these testing and inspection procedures, you can guarantee that the metal fuel lines meet the necessary safety standards and perform optimally in various automotive applications. It is a critical aspect of the manufacturing process that should not be overlooked.
Polaris Ranger Fuel Line: Location and Access Guide
You may want to see also
Frequently asked questions
Metal fuel lines are typically made from materials such as steel, aluminum, or copper alloys. These materials are chosen for their durability, strength, and resistance to corrosion, ensuring the fuel lines can withstand high-pressure environments and harsh conditions.
Achieving a precise fit is crucial for a secure installation. Measure the fuel line's diameter and the inside diameter of the fitting to ensure a snug match. Use the appropriate size of fittings and consider using a fuel line cutter and a deburring tool to ensure clean, straight cuts.
Yes, specialized tools are necessary for bending metal fuel lines. A mandrel bending machine or a hydraulic press brake is commonly used to create precise bends. These tools allow for controlled bending, ensuring the line maintains its structural integrity and fits the desired shape.
Soldering metal fuel lines involves a few steps. First, clean the surfaces to be soldered to remove any oxide layer. Then, apply a flux to facilitate the soldering process and ensure a strong bond. Heat the fuel line and fitting, then apply the solder, allowing it to melt and create a permanent connection.
To minimize corrosion, it's essential to use appropriate coatings and materials. Consider applying a protective coating or lining to the fuel lines, especially if they will be exposed to fuel with high acidic content. Regular inspection and maintenance can also help identify and address any signs of corrosion promptly.