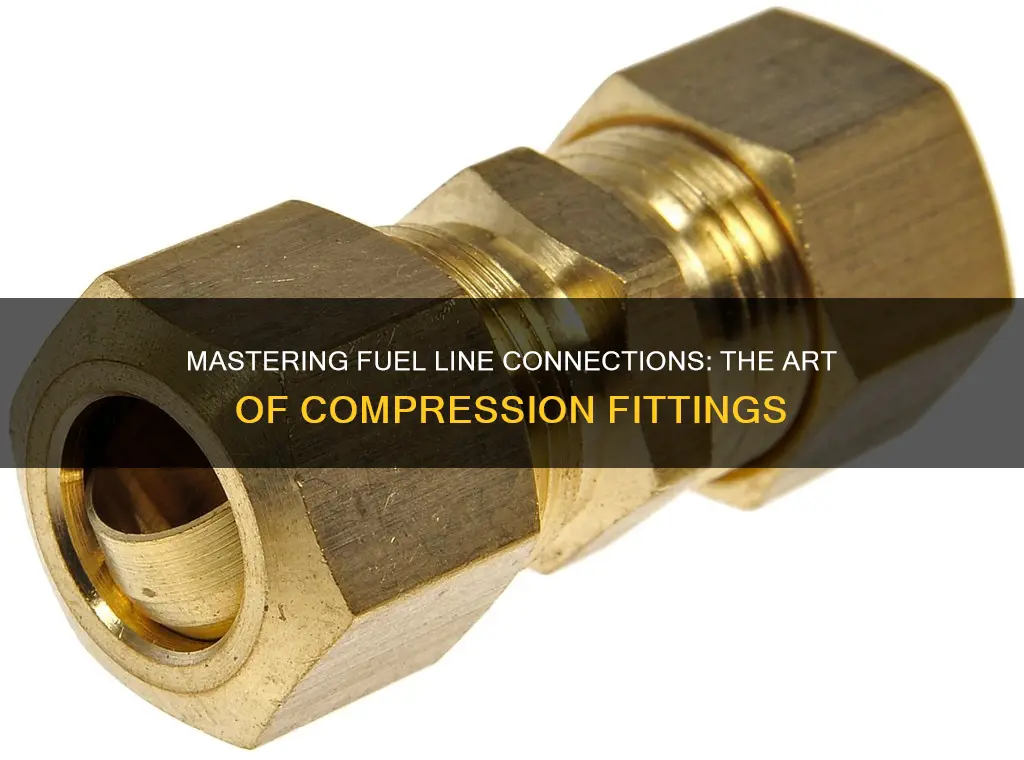
Compression fittings are an essential component for securing fuel lines in automotive applications. This guide will provide a step-by-step process for effectively using compression fittings to ensure a secure and reliable fuel line connection. By following these instructions, you can create a tight seal that prevents fuel leaks and ensures optimal performance. The process involves preparing the fuel line and fittings, inserting the line into the fitting, and then tightening the compression nut to create a secure bond. This method is a reliable and cost-effective way to maintain the integrity of your fuel system.
Characteristics | Values |
---|---|
Application | Fuel lines, often in automotive or marine settings |
Advantages | Secure connection, leak-proof, easy to install |
Materials | Brass, bronze, or stainless steel |
Size Compatibility | Varies by manufacturer, typically 1/4" to 3/8" ID |
Pressure Rating | Typically 150-300 psi, depending on material |
Installation | Tighten fittings by hand or with a tool, ensuring proper torque |
Leakage Prevention | Compression fittings create a mechanical seal by compressing the fuel line material |
Maintenance | Regularly check for tightness and signs of damage |
Safety | Properly installed compression fittings can prevent fuel leaks and potential fire hazards |
Cost | Generally affordable, with prices varying by material and size |
What You'll Learn
- Preparation: Clean and inspect fuel line, ensure it's dry and free of debris
- Fitting Selection: Choose compression fittings suited for fuel line material and size
- Assembly: Tighten fittings securely, ensuring no gaps or leaks
- Testing: Check for leaks using a soapy water solution or a pressure gauge
- Maintenance: Regularly inspect fittings for wear and replace if necessary
Preparation: Clean and inspect fuel line, ensure it's dry and free of debris
Before you begin the process of installing compression fittings on a fuel line, it is crucial to ensure that the fuel line is in optimal condition. Start by thoroughly cleaning the fuel line to remove any dirt, grime, or debris that may be present. This step is essential to guarantee a secure and reliable connection. Use a suitable cleaning agent, such as a fuel line cleaner, and apply it to the entire length of the fuel line. Allow the cleaner to work for the recommended time, which is typically around 10-15 minutes, to ensure effective removal of contaminants.
After cleaning, rinse the fuel line with a clean water supply to remove any remaining cleaning agent and debris. Make sure to flush the entire length of the line to ensure no residue is left behind. Once the fuel line is clean, it is important to inspect it for any signs of damage or deterioration. Check for cracks, holes, or any other visible defects that could compromise the integrity of the fuel line. If any issues are found, it is best to replace the fuel line to ensure a safe and efficient installation.
Drying the fuel line is another critical step in the preparation process. Moisture can lead to corrosion and potential issues with the compression fittings. Use a clean cloth or towel to wipe down the fuel line, removing any excess water. Alternatively, you can use a hairdryer on a low setting to speed up the drying process. Ensure that the fuel line is completely dry before proceeding with the installation of the compression fittings.
Additionally, pay attention to the surrounding area and ensure that the fuel line is free from any obstructions or interference. Remove any debris or foreign objects that might come in contact with the fuel line during the installation process. This step ensures that the compression fittings can be applied without any hindrance, providing a secure and tight connection. By following these preparation steps, you are setting the foundation for a successful and reliable fuel line installation.
Choosing the Right Tubing for Your Fuel Line: A Comprehensive Guide
You may want to see also
Fitting Selection: Choose compression fittings suited for fuel line material and size
When working with fuel lines, selecting the right compression fittings is crucial to ensure a secure and reliable connection. The first step is to identify the material and size of your fuel line. Different materials, such as rubber, plastic, or metal, require specific types of fittings to ensure a tight seal. For example, rubber fuel lines often use compression fittings made of brass or stainless steel, which provide excellent gripping power and durability. Plastic fuel lines might call for fittings made of nylon or polypropylene, offering chemical resistance and flexibility.
Once you've determined the material, the next consideration is the size of the fuel line. Compression fittings come in various sizes, typically measured in inches or millimeters. It's essential to choose a fitting that matches the inside diameter of your fuel line. A common rule of thumb is to select a fitting that is slightly larger than the fuel line's diameter to ensure a snug fit. This extra space allows for a secure connection without causing excessive pressure or damage to the fuel line.
For instance, if your fuel line has an inside diameter of 3/8 inches, you should opt for a compression fitting with a corresponding size. It's important to note that some fittings have adjustable sleeves or collars, allowing you to customize the fit for different sizes. These adjustable fittings can be a versatile choice, especially when working with a variety of fuel line sizes.
Additionally, consider the type of fuel being transported. High-octane fuels or those with additives might require specific fittings to prevent contamination. Always refer to the manufacturer's guidelines or consult an expert if you're unsure about the compatibility of fittings with the fuel type.
In summary, selecting the right compression fittings involves matching the material and size of the fuel line. By choosing fittings made from compatible materials and ensuring a proper size match, you can create a secure and leak-free connection for your fuel line system. Remember, proper fitting selection is a critical aspect of maintaining a safe and efficient fuel delivery system.
Chevy Fuel Line Clip Removal: A Step-by-Step Guide
You may want to see also
Assembly: Tighten fittings securely, ensuring no gaps or leaks
When working with compression fittings for fuel lines, ensuring a secure and leak-free assembly is crucial to maintain the integrity of your fuel system. Here's a step-by-step guide to achieving this:
Prepare the Components: Before you begin, ensure you have the correct compression fittings, fuel line, and any necessary tools like wrenches or pliers. Inspect the fittings for any signs of damage or wear, and confirm that the fuel line is free of any debris or contaminants.
Assembly Process: Start by inserting the fuel line into the compression fitting, ensuring it is aligned properly. The key to a successful connection lies in the compression process. Apply firm and even pressure to the fitting, moving it along the fuel line as you tighten. This action compresses the fitting onto the fuel line, creating a secure seal. Take note of the recommended torque specifications for the fittings you are using, as over-tightening can damage the fittings or fuel line.
Tightening Technique: Use a wrench or pliers to tighten the fitting securely. Apply a steady and controlled force, ensuring that the fitting is tightened evenly without any uneven pressure points. The goal is to achieve a tight, snug fit. Check for any gaps or leaks by gently pressing around the fitting and observing for any fuel line movement or seepage. If you notice any leaks, carefully tighten the fitting further, being mindful not to overtighten.
Final Checks: After tightening the fitting, inspect it for any visible signs of damage or distortion. Ensure that the fuel line is securely held in place and that there are no protruding parts that could cause damage. Test the assembly by running the fuel line under pressure or simulating real-world conditions to ensure the connection remains leak-free.
Remember, the compression fitting's primary purpose is to create a reliable seal, so taking the time to tighten and secure it properly is essential. This process ensures that your fuel system remains efficient and safe, preventing any potential fuel leaks or system failures. Always refer to manufacturer guidelines for specific instructions tailored to your fittings and fuel line materials.
Thawing Fuel Lines: Quick Fixes for Frozen Pipes
You may want to see also
Testing: Check for leaks using a soapy water solution or a pressure gauge
When working with compression fittings for fuel lines, it's crucial to ensure a secure and leak-free connection. After installing the fittings, the next step is to thoroughly test them to guarantee the safety and efficiency of your fuel system. One of the most common and effective methods for leak testing is using a soapy water solution. This simple yet reliable technique involves applying a thin layer of soapy water around the compression fitting and its surrounding areas. The soap acts as a visual indicator, creating bubbles wherever there is a leak. By observing the presence or absence of bubbles, you can quickly identify any potential issues. If bubbles appear, it indicates a leak, and you should recheck the installation or consider using a different fitting. This method is straightforward and accessible, making it a go-to choice for many professionals.
Alternatively, for a more precise and quantitative approach, a pressure gauge can be employed. This method involves applying pressure to the compression fitting and monitoring the gauge reading. Start by ensuring the fuel line is securely connected and the fitting is tightened according to the manufacturer's specifications. Then, slowly increase the pressure in the fuel line using a hand pump or a compressed air source. As you do this, keep an eye on the pressure gauge. A well-installed compression fitting should maintain a steady pressure reading without any drops or fluctuations. If the pressure drops, it signifies a leak, and you should investigate further. This method provides a more accurate assessment, especially when combined with the soapy water test, as it can help pinpoint the exact location of the leak.
When using the pressure gauge method, it's essential to follow safety precautions. Always wear protective gear, such as gloves and safety goggles, to prevent any potential injuries from fuel spills or pressure release. Additionally, ensure you are working in a well-ventilated area to avoid inhaling fuel vapors. Remember to release the pressure gradually and carefully to avoid sudden bursts or explosions. By combining these testing methods, you can effectively verify the quality of your compression fitting installation and ensure the integrity of your fuel system. Regularly checking for leaks is a critical aspect of maintenance, especially in high-pressure fuel systems, as it helps prevent costly repairs and potential safety hazards.
Waukasau Diesel's Fuel Return Line: Essential or Optional?
You may want to see also
Maintenance: Regularly inspect fittings for wear and replace if necessary
Regular maintenance of fuel lines is crucial to ensure the safe and efficient operation of any vehicle. One critical aspect of this maintenance is the inspection and care of compression fittings, which are used to connect fuel lines to various components in the fuel system. These fittings are essential for maintaining a secure and leak-free connection, and their condition should be regularly assessed.
Over time, compression fittings can experience wear and tear due to factors such as fuel contamination, temperature fluctuations, and mechanical stress. This wear may lead to reduced sealing performance, potentially causing fuel leaks, which can be dangerous and environmentally harmful. Therefore, it is imperative to inspect these fittings regularly to identify any signs of deterioration or damage.
To inspect the compression fittings, start by visually examining the connections for any visible signs of damage, such as cracks, corrosion, or deformation. Check for any signs of fuel leakage around the fittings, which could indicate a compromised seal. Additionally, look for any signs of wear on the fitting itself, such as frayed or damaged rubber components. If any issues are detected, it is essential to take immediate action.
If you notice any wear or damage, the appropriate course of action is to replace the affected compression fittings. This process involves carefully removing the old fitting and installing a new one, ensuring a proper seal. It is recommended to use high-quality replacement fittings that are compatible with your fuel system to guarantee optimal performance. When replacing fittings, ensure that you follow the manufacturer's guidelines and use the correct tools to avoid any damage to the fuel lines or other components.
In summary, regular inspection of compression fittings is a vital part of fuel line maintenance. By staying vigilant and promptly addressing any issues, you can ensure the reliability and safety of your vehicle's fuel system. Remember, proper maintenance can help prevent costly repairs and potential hazards associated with fuel leaks.
Mastering the Art of Fuel Line Removal: A Step-by-Step Guide for Your 2006 Nissan Altima
You may want to see also
Frequently asked questions
Compression fittings are essential for securely connecting fuel lines to fuel tanks, pumps, or other components in a fuel system. They provide a tight seal, preventing fuel leaks and ensuring the system's integrity.
Before installing a compression fitting, ensure the fuel line is clean and free of any debris or contaminants. Use a fuel line cleaner or a suitable solvent to remove any old fittings or residues. Then, apply a thin layer of fuel line tape or a suitable sealant around the fitting's compression ring to ensure a reliable seal.
One common mistake is overtightening the fitting, which can damage the fuel line or the fitting itself. Always follow the manufacturer's guidelines for torque specifications. Additionally, avoid using excessive force when inserting the fitting, as this can lead to misalignment or damage. It's crucial to ensure the fitting is properly seated and aligned with the fuel line to guarantee a secure and leak-free connection.