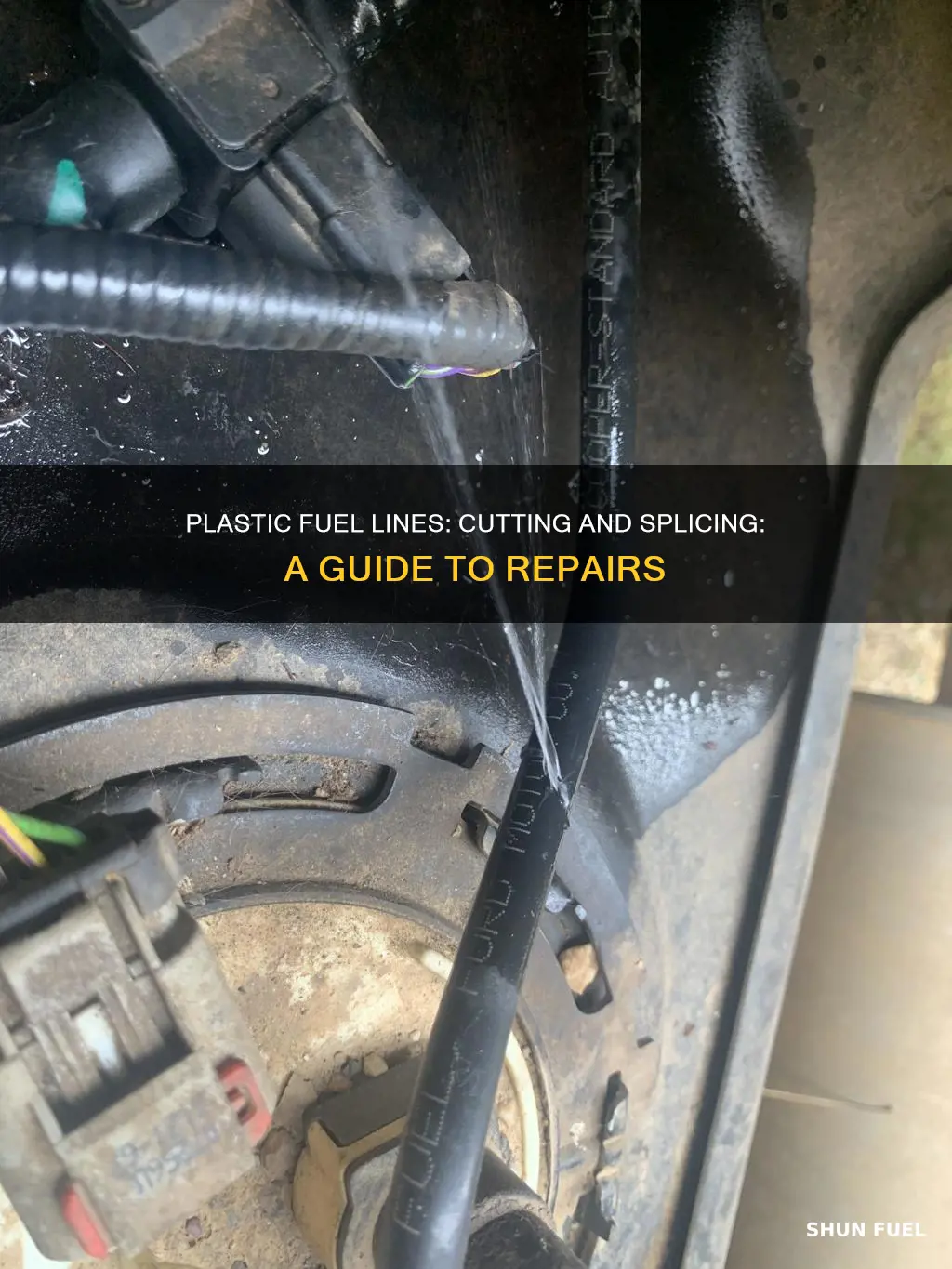
When it comes to repairing or modifying fuel lines in vehicles, a common question arises: Can plastic fuel lines be cut and spliced? The answer is yes, but it requires careful consideration and adherence to safety standards. Plastic fuel lines, often made from materials like polyethene or polypropylene, are commonly used in modern vehicles due to their flexibility and durability. While they can be cut and spliced, it's crucial to follow specific techniques to ensure a secure and reliable connection. This includes using the right tools, such as heat shrink sleeves or adhesive-lined connectors, to prevent leaks and ensure the integrity of the fuel system. Proper splicing techniques are essential to maintain the safety and performance of the vehicle's fuel supply.
Characteristics | Values |
---|---|
Material | Plastic (often polyethene or nylon) |
Durability | Resistant to fuel degradation and UV light |
Flexibility | Good flexibility, allowing for some movement without breaking |
Temperature Tolerance | Typically suitable for a wide range of temperatures, but specific limits vary by type |
Chemical Resistance | Resistant to most fuels and chemicals, but not all |
Cut and Splicing | Possible under certain conditions, but requires careful preparation and technique |
Advantages | Lightweight, cost-effective, and easy to install |
Disadvantages | May not be as strong as metal fuel lines, and splicing can be challenging |
Common Applications | Fuel delivery systems in vehicles, boats, and small engines |
Maintenance | Regular inspection for cracks or damage is recommended |
What You'll Learn
- Safety Precautions: Always wear protective gear and ensure proper ventilation when working with plastic fuel lines
- Material Compatibility: Verify that the splicing material is compatible with the fuel type and system pressure
- Cutting Techniques: Use sharp, clean tools and make precise cuts to avoid damage to the fuel line
- Splicing Methods: Explore various splicing techniques like heat shrink, adhesive, or crimping for a secure connection
- Testing and Inspection: Thoroughly test the spliced line for leaks and ensure it meets safety standards
Safety Precautions: Always wear protective gear and ensure proper ventilation when working with plastic fuel lines
When working with plastic fuel lines, it is crucial to prioritize safety to prevent any potential hazards. One of the primary safety precautions is to always wear appropriate protective gear. This includes gloves, safety goggles, and a respirator mask to safeguard against potential splashes, fumes, or airborne particles that may occur during the cutting and splicing process. Plastic fuel lines can release harmful chemicals if damaged, so protecting your skin, eyes, and respiratory system is essential.
Additionally, ensuring proper ventilation in the work area is vital. Plastic fuel lines, especially when heated or cut, can release volatile organic compounds (VOCs) and other hazardous gases. Working in a well-ventilated environment helps to disperse these fumes, reducing the risk of inhalation and potential health issues. Consider using a fume extractor or working outdoors if possible, to maintain a safe and healthy working condition.
Before beginning the cutting and splicing process, inspect the plastic fuel lines for any signs of damage or deterioration. Look for cracks, brittleness, or any visible wear and tear. If the lines are old or compromised, it is best to replace them entirely to avoid potential leaks and safety hazards. Proper preparation and identification of the material's condition can prevent accidents and ensure a safer working environment.
When cutting the plastic fuel lines, use sharp, clean tools designed for this purpose. Avoid using rusty or dull blades that could compromise the integrity of the cut. Properly align the cut to ensure a clean and precise edge, minimizing the risk of damage to the surrounding components. Always work in a controlled manner, taking breaks when needed, to maintain focus and reduce the chances of errors.
Remember, safety should be the top priority when working with any fuel-related components. By wearing the appropriate protective gear and ensuring good ventilation, you can significantly reduce the risks associated with handling plastic fuel lines. Following these precautions will not only protect you but also contribute to a safer and more efficient working process.
Is the Milwaukee Fuel Line Worth the Investment?
You may want to see also
Material Compatibility: Verify that the splicing material is compatible with the fuel type and system pressure
When splicing or repairing plastic fuel lines, it is crucial to consider material compatibility to ensure the integrity and safety of the fuel system. The primary concern is to choose a splicing material that can withstand the specific fuel type and system pressure to prevent potential issues such as fuel leaks, system failures, or even fire hazards.
The compatibility of the splicing material with the fuel type is essential. Different fuels have varying chemical compositions and properties. For example, gasoline and diesel have distinct characteristics that require specific materials to ensure a secure and reliable connection. Some plastics may be suitable for one fuel type but may not be compatible with another, leading to degradation or failure over time. It is imperative to consult the manufacturer's guidelines or technical data sheets to identify the appropriate materials for the specific fuel being used.
System pressure is another critical factor. Plastic fuel lines typically operate under varying pressure levels, and the chosen splicing material must be able to handle these conditions without compromising its structural integrity. High-pressure fuel systems, such as those in racing applications or heavy-duty vehicles, require materials that can withstand significant stress and potential heat generation. Materials like high-performance plastics or specialized adhesives designed for high-pressure environments should be considered to ensure the long-term reliability of the fuel system.
To verify material compatibility, it is recommended to follow these steps:
- Refer to the fuel system's technical documentation or manufacturer's specifications to identify the approved materials for splicing.
- Test the proposed splicing material against the fuel type to ensure it does not react negatively or cause any degradation. This can be done through laboratory testing or by consulting experts in the field.
- Evaluate the material's ability to handle the system pressure by considering factors such as temperature resistance, flexibility, and strength.
- Consider the environmental conditions the fuel system will be exposed to and select materials that can withstand those specific challenges.
By carefully assessing material compatibility, you can ensure that the splicing or repair work on plastic fuel lines is performed correctly, minimizing the risk of fuel-related issues and maintaining the overall safety and efficiency of the vehicle's fuel system.
Kawasaki Bayou 185 Fuel Line Sizing Guide
You may want to see also
Cutting Techniques: Use sharp, clean tools and make precise cuts to avoid damage to the fuel line
When working with plastic fuel lines, it is crucial to employ the right techniques to ensure a clean and secure cut. The process of splicing or repairing a fuel line requires precision and attention to detail to avoid any potential issues. Here's a guide on the cutting techniques to achieve this:
Using sharp tools is essential for a successful cut. Dull blades or scissors can lead to ragged edges, which may cause leaks or damage to the fuel line. Invest in a good pair of sharp scissors or a specialized fuel line cutter. These tools are designed to provide clean, precise cuts, ensuring that the fuel line remains intact and functional. It is worth the investment to ensure a professional finish.
Before making any cuts, ensure that the tool is clean and free of debris. Any dirt or contaminants on the cutting edge can compromise the quality of the cut. A simple way to prepare your tool is to wipe it down with a cloth or use a small brush to remove any visible dirt. This step is often overlooked but is crucial for achieving a neat and secure splice.
Precision is key when cutting plastic fuel lines. Take your time and measure twice to ensure accuracy. Mark the exact spot where you need to make the cut using a permanent marker or a small piece of tape. This step helps to guide your cut and ensures that you are making the incision in the right place. A precise cut will result in a seamless splice, reducing the risk of fuel leakage.
As you begin the cutting process, apply steady pressure and guide the tool along the marked line. Keep the cut as straight as possible to maintain consistency. Avoid applying excessive force, as it may lead to cracking or damage to the fuel line. A smooth and controlled cut will result in a professional-looking splice.
After the cut is made, inspect the edges to ensure they are clean and smooth. If there are any rough spots or small cracks, carefully trim them using the sharp tool. This step is vital to prevent any potential issues and ensure the fuel line's integrity. Taking the time to refine the cut will contribute to a successful repair or modification.
Clear Vinyl Tubing: A Fuel Line Alternative?
You may want to see also
Splicing Methods: Explore various splicing techniques like heat shrink, adhesive, or crimping for a secure connection
When it comes to splicing plastic fuel lines, there are several methods to ensure a secure and reliable connection. Here's an overview of some common techniques:
Heat Shrink Splicing: This method is widely used and offers a strong, durable bond. It involves heating a specialized heat shrink tube to a precise temperature, allowing it to shrink tightly around the cut ends of the fuel lines. The heat shrink material is typically made of a flexible, flame-resistant polymer. Before applying heat, ensure the lines are clean and free of any debris. Slide the heated tube over the cut ends, ensuring good contact, and then apply heat according to the manufacturer's instructions. As the tube shrinks, it creates a secure bond, providing excellent resistance to fuel leakage. This technique is favored for its simplicity and the ability to create a water-tight seal.
Adhesive splicing is another reliable method, especially for smaller fuel lines. It utilizes a specialized adhesive designed for plastic materials. The process begins by thoroughly cleaning the cut ends to remove any contaminants. Then, apply a thin layer of adhesive to each end, ensuring complete coverage. Allow the adhesive to set according to the product's guidelines, which may involve waiting for a specific time or applying heat. This method creates a strong bond between the fuel lines, making it ideal for temporary or permanent repairs. However, it's important to choose an adhesive suitable for the specific plastic type used in the fuel lines.
Crimping is a mechanical splicing technique that provides a secure connection without the need for heat or adhesives. It involves using a crimping tool to create a series of indentations or crimps around the fuel line. The crimps lock the two lines together, creating a strong, reliable bond. This method is particularly useful when working with fuel lines that are already installed, as it doesn't require removing or modifying the existing setup. Crimping tools are available in various sizes to accommodate different fuel line diameters.
Each splicing method has its advantages and is chosen based on factors such as the fuel line's condition, the desired strength of the connection, and the availability of tools. It's crucial to follow manufacturer guidelines and best practices to ensure a successful splice, maintaining the integrity of the fuel system.
Mastering Fuel Line Quick Connects: A Step-by-Step Guide
You may want to see also
Testing and Inspection: Thoroughly test the spliced line for leaks and ensure it meets safety standards
When splicing plastic fuel lines, it is crucial to perform thorough testing and inspection to ensure the integrity and safety of the system. After splicing the lines, the first step is to visually inspect the joint for any signs of damage, cracks, or imperfections. Look for any visible signs of stress or deformation around the splice area, as these could indicate potential weaknesses. It is essential to check for any debris or foreign objects that might have entered the splice during the process, as these can compromise the joint's strength.
The next step is to perform a leak test to verify the quality of the splice. This can be done using a simple pressure test or a more advanced method like a vacuum test. Apply pressure to the spliced line and observe for any leaks or bubbles forming around the joint. Even the smallest leak can lead to significant issues over time, so it is critical to identify and address any problems at this stage. Ensure that the pressure is gradually increased and maintained for a sufficient duration to cover all potential leak sites.
For a more comprehensive assessment, consider using a dye-penetration test, especially if you suspect any potential issues with the splice. This method involves introducing a non-toxic, water-soluble dye into the fuel system and observing if it seeps through the splice. If the dye is present, it indicates a potential leak path, and further investigation is required. This test is particularly useful for identifying hidden leaks that might not be visible during a visual inspection.
In addition to leak testing, it is essential to check the splice's structural integrity. This can be done by applying a load test, where the spliced line is subjected to varying pressures and temperatures to simulate real-world conditions. The goal is to ensure that the splice can withstand the expected stresses without failing. If any weaknesses are identified, the splice may need to be reinforced or replaced to meet safety standards.
Finally, always refer to the manufacturer's guidelines and industry standards for plastic fuel lines. These guidelines often provide specific requirements for splicing, including the types of materials and methods that are acceptable. Adhering to these standards ensures that the spliced line meets the necessary safety and performance criteria. Thorough testing and inspection are vital to guarantee the reliability and safety of the fuel system, especially when dealing with critical components like fuel lines.
Can Fuel Hose Be Used for Vacuum Lines?
You may want to see also
Frequently asked questions
Yes, plastic fuel lines can be cut and spliced, but it should be done with caution and proper techniques to ensure the modified lines can withstand the pressure and temperature changes in the fuel system. Using a heat source to slightly soften the plastic before splicing can help create a secure joint.
Cutting and splicing plastic fuel lines can introduce risks such as fuel leaks, reduced fuel pressure, and potential engine performance issues. It is crucial to ensure a tight and secure connection to prevent any fuel from escaping, which could lead to hazardous situations.
When splicing plastic fuel lines, it is recommended to use a fuel line cutter and a fuel line splicer. These tools help create clean and precise cuts, and the splicer ensures a secure connection. Applying a suitable fuel line adhesive or sealant can also enhance the joint's strength and durability.
While a standard hose cutter can be used, it may not provide the best results for fuel lines. Plastic fuel lines often require a more precise cut, and a dedicated fuel line cutter will offer better control and a cleaner edge. It is essential to follow the manufacturer's guidelines for the specific fuel line material.
To ensure compatibility, it is crucial to check the specifications and dimensions of the existing fuel lines and the spliced section. Using a fuel line with similar thickness, durometer, and inner diameter will help maintain the integrity of the fuel system. Consulting the vehicle's manual or seeking professional advice can provide valuable insights for the right choice.