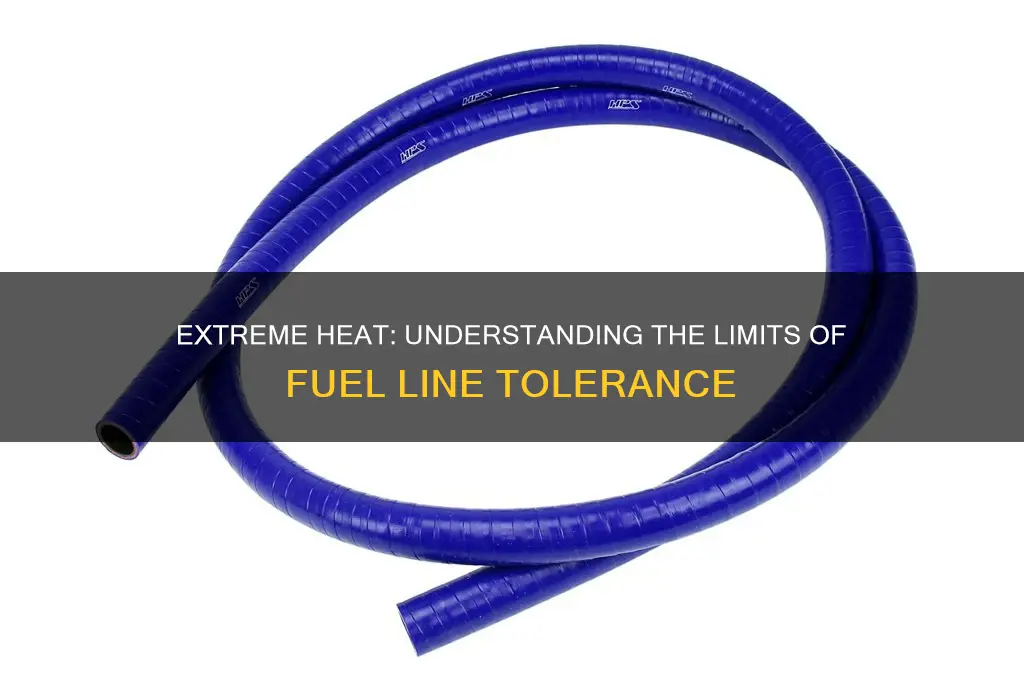
Fuel lines play a critical role in the performance and safety of any vehicle, and understanding the temperature limits of these lines is essential. The heat a fuel line can withstand depends on various factors, including the type of fuel, the line's material, and the vehicle's operating conditions. This discussion will explore the factors influencing fuel line temperature, the potential risks of overheating, and the measures taken to ensure optimal performance and safety.
What You'll Learn
- Fuel Line Material: Different materials have varying heat tolerances, affecting temperature limits
- Fuel Type: Some fuels reach higher temperatures than others due to their chemical properties
- Flow Rate: Higher flow rates can lead to increased heat in the fuel line
- Environmental Factors: External conditions like temperature and humidity impact fuel line temperature
- Engine Load: Increased engine load can cause fuel lines to get hotter
Fuel Line Material: Different materials have varying heat tolerances, affecting temperature limits
The material of a fuel line is a critical factor in determining its maximum operating temperature. Different materials have distinct heat tolerances, which can significantly impact the performance and longevity of the fuel line. Understanding these variations is essential for ensuring the safe and efficient operation of fuel systems in various applications.
Metallic materials, such as steel and aluminum, are commonly used for fuel lines due to their strength and durability. Steel fuel lines, for instance, offer excellent resistance to heat and can withstand temperatures up to 300°F (149°C). This makes them suitable for high-performance engines and applications where fuel temperatures may reach elevated levels. However, it's important to note that prolonged exposure to temperatures above the material's limit can lead to degradation and potential failure.
On the other hand, plastic fuel lines, often made from materials like nylon or polyetheretherketone (PEEK), have lower heat tolerances. Nylon fuel lines, for example, can typically handle temperatures up to 200°F (93°C). While plastic lines are lighter and more flexible, they may not be suitable for high-temperature environments or applications requiring extended exposure to heat. Proper selection of the material based on the expected fuel temperatures is crucial to avoid damage or performance issues.
In addition to metallic and plastic options, some fuel lines are constructed with composite materials, combining the benefits of both. These composites often provide improved heat resistance compared to pure plastics. For instance, a fuel line made with a composite material might offer a temperature range of 250°F to 300°F (121°C to 149°C), making it suitable for a wide range of applications.
When choosing the material for a fuel line, it is essential to consider the specific operating conditions, including fuel temperature, environmental factors, and the overall system design. Proper material selection ensures that the fuel line can withstand the anticipated heat levels without compromising safety or performance. Regular inspection and maintenance of fuel lines, especially in high-temperature environments, are recommended to identify and address any potential issues promptly.
Understanding the Linear Fuel Mass Model: A Comprehensive Guide
You may want to see also
Fuel Type: Some fuels reach higher temperatures than others due to their chemical properties
The temperature a fuel line can withstand is largely dependent on the type of fuel being used. Different fuels have distinct chemical compositions, which directly influence their boiling points and the temperatures they can reach when burned. For instance, gasoline, a common automotive fuel, has a relatively low flash point, typically around 40-60°C (104-140°F). This means that gasoline can ignite at a relatively low temperature, but it also means that the fuel line and other components in the fuel system must be designed to handle the temperatures that gasoline can reach during combustion.
In contrast, diesel fuel has a higher flash point, often exceeding 100°C (212°F). This higher flash point indicates that diesel fuel requires a much higher temperature to ignite, which can result in a more stable combustion process. Consequently, diesel fuel lines and related components are often designed to withstand higher temperatures compared to those used for gasoline.
The chemical properties of a fuel also play a significant role in its temperature characteristics. Fuels with a higher molecular weight and more complex molecular structure tend to have higher boiling points and can reach higher temperatures when burned. This is because these fuels require more energy to break down into their constituent components, which results in a more complete combustion process and higher temperatures.
On the other hand, fuels with simpler molecular structures, such as some biofuels, may have lower boiling points and can reach lower temperatures during combustion. These fuels are often designed to be more environmentally friendly and may require specific components in the fuel system to handle their unique temperature characteristics.
Understanding the temperature capabilities of different fuels is crucial for designing and maintaining fuel systems that are both efficient and safe. Engineers and designers must consider the chemical properties of the fuel being used to ensure that the fuel lines, pumps, and other components can withstand the temperatures generated during the combustion process. This is particularly important in high-performance applications where the fuel system must operate under extreme conditions.
Optimizing Performance: Choosing the Right Fuel Line for Your 2005 Johnson 90 HP
You may want to see also
Flow Rate: Higher flow rates can lead to increased heat in the fuel line
The flow rate of fuel through a line is a critical factor in determining the temperature of the fuel line. When the flow rate is high, the fuel moves rapidly through the line, leading to several potential consequences. Firstly, the increased velocity of the fuel can cause friction and turbulence within the line, especially if the line is not optimally designed for high-flow rates. This friction generates heat, which can be significant in thinner fuel lines. The heat generated by the friction can lead to a rise in the overall temperature of the fuel line, potentially reaching levels that may be considered too high for safe operation.
Secondly, higher flow rates can result in a more rapid transfer of heat from the fuel to the fuel line itself. As the fuel flows, it can transfer its thermal energy to the walls of the line, especially if the line is made of materials with lower thermal conductivity. This process is more pronounced when the fuel is under pressure, as higher pressure can accelerate the heat transfer. Over time, this can cause the fuel line to become excessively hot, potentially leading to degradation of the line's material properties and even the risk of fuel line failure.
To mitigate these issues, it is essential to consider the design and material of the fuel line when dealing with high-flow rates. Using fuel lines with thicker walls and materials that offer better thermal insulation can help reduce the heat generated by the flow. Additionally, ensuring that the fuel line is properly insulated and that there are no obstructions or bends that could cause turbulence can also help manage the temperature of the fuel line.
In summary, higher flow rates in fuel lines can lead to increased heat generation due to friction and rapid heat transfer. This can have implications for the performance and longevity of the fuel line. Therefore, careful consideration of flow rate management and line design is necessary to ensure safe and efficient operation, especially in high-performance applications where fuel flow rates are optimized for maximum power output.
Understanding Gas Tank Fuel Lines: A Comprehensive Guide
You may want to see also
Environmental Factors: External conditions like temperature and humidity impact fuel line temperature
The temperature of a fuel line can vary significantly depending on the environmental conditions it is exposed to. External factors such as temperature and humidity play a crucial role in determining how hot a fuel line can get. In regions with extremely hot climates, the fuel line may experience higher temperatures due to the intense heat from the sun and the surrounding environment. This can lead to potential issues with the fuel's stability and performance, especially if the fuel contains volatile components.
Temperature is a critical factor in fuel line performance. When the ambient temperature rises, the fuel line's temperature also increases. This is because the fuel line acts as a conduit for the fuel, and the heat from the surroundings is transferred to the fuel. In hot weather, the fuel line may become significantly warmer, potentially reaching temperatures that can affect the fuel's properties. For example, in high-temperature environments, the fuel's volatility may increase, leading to potential evaporation and reduced fuel efficiency.
Humidity, another environmental factor, also influences fuel line temperature. In humid conditions, the air contains a higher amount of water vapor. When the fuel line is exposed to humid environments, the fuel can absorb moisture from the air, leading to a phenomenon known as 'fuel line sweating'. This occurs when the fuel line's temperature is lower than the surrounding air, causing condensation and potential fuel degradation. Over time, this can result in fuel contamination and performance issues.
To mitigate these effects, it is essential to consider the specific environmental conditions of the fuel line's location. In hot and humid regions, fuel lines may require additional insulation or protective measures to prevent overheating and fuel degradation. Proper ventilation and the use of fuel additives can also help maintain fuel stability and performance in such environments. Understanding these environmental factors is crucial for ensuring the optimal operation and longevity of fuel lines in various settings.
Carbureted Engine Fuel Return Line: Essential or Optional?
You may want to see also
Engine Load: Increased engine load can cause fuel lines to get hotter
Increased engine load is a common scenario in automotive engineering, and it directly impacts the temperature of fuel lines. When an engine operates under higher load conditions, it demands more power, which translates to increased fuel consumption. This heightened fuel usage results in a higher flow rate through the fuel lines, leading to several consequences. Firstly, the increased flow rate can cause a phenomenon known as "fuel line surge." This surge occurs when the fuel pressure in the system rises rapidly, creating a temporary pressure spike. The surge can lead to a temporary increase in temperature as the fuel lines experience a rapid change in pressure and flow.
Secondly, the higher engine load often means the engine is operating at a higher RPM (revolutions per minute). This increased rotation rate causes the engine to work harder, generating more heat. As the engine's temperature rises, so does the temperature of the fuel lines. The fuel lines are typically made of materials like steel or aluminum, which have specific temperature limits. Prolonged exposure to high temperatures can cause these materials to degrade, leading to potential fuel leaks or even fuel line failure. This is especially critical in high-performance vehicles or those operating in extreme conditions.
To manage this issue, engineers often employ various strategies. One approach is to use fuel lines with higher temperature resistance, ensuring they can withstand the increased heat generated during high-load conditions. Additionally, implementing a cooling system for the fuel lines can help regulate their temperature. This could involve using a fuel cooler, which is a device designed to reduce the temperature of the fuel before it enters the engine, thus preventing the fuel lines from overheating.
Another method to mitigate the effects of increased engine load is to optimize the engine's fuel injection system. By adjusting the fuel injection timing and spray patterns, engineers can ensure that the engine receives the required amount of fuel without overloading the system. This precision in fuel delivery helps maintain a stable engine temperature, reducing the strain on the fuel lines.
In summary, increased engine load has a direct impact on fuel line temperature. The higher fuel consumption and engine RPMs lead to potential issues like fuel line surges and overheating. To address these challenges, automotive designers focus on using appropriate materials, implementing cooling systems, and optimizing fuel injection processes to ensure the engine operates efficiently and safely, even under demanding conditions. Understanding these factors is crucial for maintaining the performance and longevity of fuel lines in various vehicle applications.
Mastering the Art of Securing Fuel Lines: A Guide to Tightening Small Zip Ties
You may want to see also
Frequently asked questions
The temperature of a fuel line can vary depending on the engine and fuel type, but typically, it should not exceed 150°F (65°C) under normal operating conditions. Exceeding this temperature can cause fuel degradation and potential performance issues.
Overheating of the fuel line can be caused by several factors, including high engine load, prolonged idling, faulty fuel pumps, or a restricted fuel flow. It's essential to identify and address the root cause to prevent further damage.
Yes, overheating fuel lines can lead to engine misfires, reduced power, and even permanent engine damage. It can also result in fuel evaporation, leading to increased emissions and potential engine misfires. Regular maintenance and monitoring of fuel line temperatures are crucial to prevent such issues.