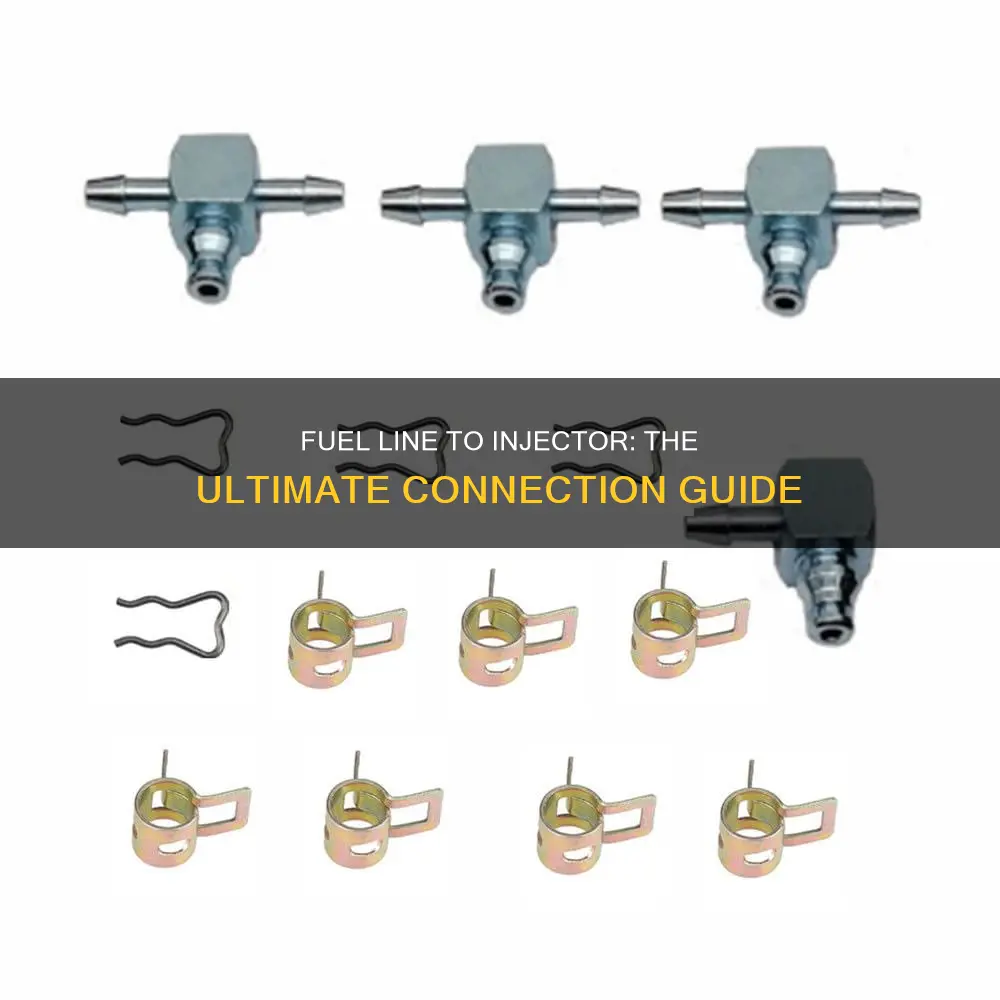
The fuel line plays a crucial role in delivering fuel from the tank to the engine's fuel injectors. This process involves a precise connection between the fuel line and the fuel injector to ensure optimal engine performance. Understanding the mechanics of this connection is essential for maintaining a reliable fuel supply and efficient combustion in modern vehicles.
Characteristics | Values |
---|---|
Connection Type | Fuel lines are typically connected to fuel injectors using a quick-connect fitting or a high-pressure hose. |
Material | The fuel line is made of materials like rubber, silicone, or steel, depending on the application and pressure requirements. |
Pressure Rating | Fuel lines are designed to withstand high-pressure fuel, often rated for pressures up to 100-150 psi or more. |
Flexibility | They are flexible to accommodate engine movement and vibrations. |
Diameter | The diameter varies depending on the fuel flow rate and pressure, typically ranging from 3/8" to 1/2" in diameter. |
Length | The length can vary based on engine layout and positioning, often ranging from a few inches to several feet. |
Compatibility | Fuel lines must be compatible with the fuel type (gasoline, diesel, etc.) and the engine's fuel system. |
Seals and Gaskets | Proper seals and gaskets are used to ensure a tight connection and prevent fuel leaks. |
Routing | Fuel lines are routed carefully to avoid damage and maintain a clear path to the fuel injectors. |
Maintenance | Regular inspection and replacement are recommended to ensure optimal performance and prevent fuel-related issues. |
What You'll Learn
- Fuel Line Material: Different materials like rubber or plastic are used for fuel lines, each with unique properties
- Fuel Line Routing: Proper routing ensures fuel reaches the injector without contamination or damage
- Fuel Filter Placement: Filters are crucial to prevent contaminants from reaching the injector, enhancing engine performance
- Fuel Pressure Regulation: The fuel line must maintain optimal pressure to ensure efficient injector operation
- Fuel Injector Mounting: Proper mounting ensures the injector is securely connected to the fuel line for reliable fuel delivery
Fuel Line Material: Different materials like rubber or plastic are used for fuel lines, each with unique properties
The choice of material for fuel lines is crucial in the automotive industry, as it directly impacts the performance and longevity of the fuel delivery system. Fuel lines are responsible for transporting fuel from the tank to the engine, and the material used determines the line's flexibility, durability, and resistance to fuel degradation.
One of the most common materials for fuel lines is rubber. Rubber fuel lines offer excellent flexibility, allowing them to accommodate the engine's movement and vibrations without cracking or breaking. This flexibility is essential to ensure a reliable fuel supply, especially in high-performance vehicles where engine movement can be more pronounced. Additionally, rubber is naturally resistant to fuel degradation, meaning it can withstand the chemicals present in gasoline or diesel without deteriorating over time. This property ensures that the fuel line remains intact and functional, even when exposed to the corrosive effects of fuel.
In contrast, plastic fuel lines have gained popularity due to their lightweight and cost-effective nature. Plastic lines are typically made from materials like polyvinyl chloride (PVC) or high-density polyethylene (HDPE). These materials offer good flexibility and resistance to fuel degradation, making them suitable for fuel delivery systems. Plastic lines are often preferred in modern vehicles due to their ease of installation and the reduced weight they bring to the engine bay. However, it's important to note that plastic lines may not be as flexible as rubber, which could be a consideration for certain engine designs.
The decision between rubber and plastic fuel lines often depends on the specific requirements of the vehicle. Rubber lines are ideal for high-performance engines or older vehicles where flexibility and long-term durability are essential. Plastic lines, on the other hand, provide a lightweight and cost-effective solution, making them a popular choice for newer, more fuel-efficient vehicles.
In summary, the material of a fuel line is a critical aspect of engine design, with rubber and plastic being the primary choices. Each material offers unique advantages, ensuring that fuel is delivered efficiently and safely to the engine, regardless of the vehicle's age or performance capabilities. Understanding these material properties is essential for engineers and mechanics to make informed decisions when working with fuel delivery systems.
Fuel Line Removal: A Step-by-Step Guide for Mazda Fuel Pumps
You may want to see also
Fuel Line Routing: Proper routing ensures fuel reaches the injector without contamination or damage
Fuel line routing is a critical aspect of vehicle maintenance that ensures the efficient and safe operation of the fuel injection system. Proper routing is essential to prevent contamination, damage, and potential engine performance issues. When connecting a fuel line to a fuel injector, it is crucial to follow these guidelines to maintain optimal engine performance.
The fuel line should be routed in a way that avoids any sharp bends or kinks, as these can restrict fuel flow and potentially cause damage to the line. It is recommended to use a flexible fuel line that can accommodate slight bends without compromising its integrity. The line should be secured using appropriate clamps or ties to prevent it from moving or coming loose during vehicle operation. Proper support and insulation are also vital to protect the fuel line from heat, vibrations, and potential damage from other vehicle components.
One important consideration is the placement of the fuel line relative to the fuel tank and other engine components. It should be positioned away from hot surfaces, such as exhaust manifolds or engine blocks, to prevent fuel contamination and potential fires. Additionally, the line should be kept away from sharp edges or protruding parts that could puncture or damage the fuel line.
In some cases, fuel lines may need to be routed through the engine bay, and it is crucial to ensure they are not in contact with any moving parts or components that could cause damage. Using protective sleeves or shields can help safeguard the fuel line from potential hazards. Regular inspection of the fuel line is also recommended to identify any signs of wear, damage, or contamination, allowing for prompt repairs or replacements.
By following these routing practices, you can ensure that the fuel line connects to the fuel injector efficiently, delivering clean and uncontaminated fuel for optimal engine performance. Proper maintenance and attention to fuel line routing will contribute to the longevity and reliability of your vehicle's fuel injection system.
Can Fuel Lines Rust? Uncovering the Truth
You may want to see also
Fuel Filter Placement: Filters are crucial to prevent contaminants from reaching the injector, enhancing engine performance
The placement of a fuel filter is a critical aspect of maintaining a vehicle's engine performance and longevity. Filters play a vital role in ensuring that contaminants do not reach the fuel injectors, which can cause significant issues. Here's an overview of why and how fuel filter placement is essential:
In a vehicle's fuel system, the fuel line is responsible for delivering fuel from the tank to the engine. This line is connected to the fuel injector, a crucial component that precisely sprays fuel into the engine's cylinders for combustion. Over time, fuel lines can accumulate contaminants such as dirt, rust, and debris, which may originate from the fuel tank, storage, or even the fuel pump. These contaminants can lead to a range of problems, including reduced engine performance, increased fuel consumption, and even engine damage.
Fuel filters are designed to trap these unwanted particles and ensure that only clean, contaminant-free fuel reaches the injector. They are typically located in the fuel line, often near the engine or the fuel pump, depending on the vehicle's design. The filter's placement is strategic, allowing it to capture contaminants before they can cause harm. When a fuel filter is positioned correctly, it acts as a barrier, ensuring that the fuel injector receives only the highest quality fuel.
Proper filter placement is essential for several reasons. Firstly, it prevents the injector from becoming clogged or damaged by contaminants. Clogged injectors can result in uneven fuel distribution, leading to poor engine performance, reduced power, and even misfires. Secondly, well-placed filters help maintain fuel pressure, ensuring that the engine receives the correct amount of fuel at the right time. This is critical for optimal combustion and engine efficiency.
Additionally, the placement of the fuel filter allows for easy access during maintenance and inspections. Regularly checking and replacing the filter ensures that the fuel system remains healthy. Over time, filters can become saturated with contaminants and may require replacement to maintain the engine's performance. By keeping the filter clean and functional, you contribute to the overall reliability and longevity of the vehicle's fuel system.
In summary, the placement of a fuel filter is a critical step in the fuel delivery process, ensuring that the fuel injector receives clean fuel. This placement is designed to protect the engine from contaminants, maintain optimal performance, and contribute to the overall health of the vehicle's fuel system. Regular maintenance and attention to the fuel filter's position and condition are essential for a well-functioning engine.
Chevy Fuel Pump Lines: A Step-by-Step Removal Guide
You may want to see also
Fuel Pressure Regulation: The fuel line must maintain optimal pressure to ensure efficient injector operation
The fuel line plays a critical role in the fuel injection system of an engine, as it is responsible for delivering the correct amount of fuel at the right pressure to each injector. This process is crucial for efficient engine operation and performance. When the fuel line connects to the fuel injector, it must maintain optimal pressure to ensure that the fuel is atomized and injected into the engine's cylinders at the precise moment required.
Fuel pressure regulation is essential because it directly impacts the engine's power output, fuel efficiency, and overall performance. If the pressure is too low, the fuel may not be atomized properly, leading to poor fuel-air mixture quality and reduced power. Conversely, if the pressure is too high, it can cause excessive fuel spray, leading to potential engine damage and inefficient combustion. Therefore, the fuel line must be designed and maintained to provide the ideal pressure range for the specific engine requirements.
The fuel line's role in pressure regulation is achieved through various mechanisms. One common method is the use of a fuel pressure regulator, which is typically located between the fuel pump and the injectors. This regulator monitors and adjusts the fuel pressure to maintain a consistent level. It ensures that the pressure remains within the engine's optimal range, compensating for any variations in fuel flow or engine load. Properly functioning fuel pressure regulators are vital, as they prevent over-pressurization and ensure the fuel injectors receive the correct amount of fuel.
In addition to the regulator, the fuel line itself can contribute to pressure regulation. The line's diameter and length are carefully chosen to minimize pressure drops as fuel travels from the pump to the injectors. Engineers design these lines to optimize flow characteristics, ensuring that the fuel pressure remains stable throughout the system. This attention to detail is crucial, especially in high-performance engines where precise fuel delivery is essential for achieving optimal power and responsiveness.
Maintaining the correct fuel pressure is a delicate balance, and it requires regular inspection and adjustment. Over time, fuel lines can develop leaks or clogs, leading to pressure drops and potential performance issues. Therefore, it is essential for vehicle owners and mechanics to monitor the fuel system regularly, checking for any signs of damage or malfunction. By ensuring the fuel line and associated components are in good condition, the engine's fuel pressure can be kept within the ideal range, resulting in improved performance and longevity.
Boost Engine Performance: Inline Fuel Pump Upgrade for Optimal Power
You may want to see also
Fuel Injector Mounting: Proper mounting ensures the injector is securely connected to the fuel line for reliable fuel delivery
The fuel injector is a critical component in modern vehicle engines, responsible for precise fuel injection to optimize combustion and performance. Proper mounting of the fuel injector is essential to ensure reliable fuel delivery and prevent potential issues. When connecting the fuel line to the injector, it is crucial to follow a structured approach to guarantee a secure and efficient setup.
To begin, locate the fuel injector and identify the fuel line connection port. This port is typically designed to accommodate the fuel line, often in the form of a quick-connect fitting or a threaded connection. Ensure that the fuel line is compatible with the injector's specifications to avoid any potential leaks or performance issues. The fuel line should be securely attached to the injector, providing a tight seal to prevent any fuel from escaping.
Mounting the fuel injector involves positioning it in a way that allows for easy access during maintenance and ensures it is protected from physical damage. It is recommended to use mounting brackets or clips provided by the manufacturer to secure the injector in place. These brackets should be tightened firmly to hold the injector in a stable position, preventing any movement that could lead to disconnection or damage. Proper mounting also includes ensuring that the fuel line is routed correctly, avoiding any sharp bends or kinks that might restrict fuel flow.
When connecting the fuel line, ensure that the fittings are clean and free of any debris. Use fuel line connectors that are compatible with the fuel type being used to ensure a reliable connection. Tighten the connectors securely, but be careful not to over-tighten, as this can damage the fuel line or injector. A proper connection should feel snug and secure, with no visible signs of leakage.
In summary, proper mounting of the fuel injector is a critical aspect of maintaining a vehicle's fuel delivery system. By following the manufacturer's guidelines and ensuring a secure connection between the fuel line and injector, you can guarantee reliable fuel supply, optimal engine performance, and longevity of the fuel injection system. Regular inspection and maintenance of the mounting and connection points will further contribute to the overall reliability of the vehicle's fuel system.
Cummins Fuel Injection Lines: Unraveling the Mystery of Uniform Lengths
You may want to see also
Frequently asked questions
The fuel line is typically connected to the fuel injector via a precision fuel line fitting, which ensures a secure and tight seal. This fitting is designed to withstand the pressure and temperature changes that occur within the fuel system. The connection is made by inserting the fuel line into the fitting and using a clamp or retaining ring to secure it in place. This method ensures a reliable and leak-free connection, allowing for efficient fuel delivery to the injector.
The fuel line fitting serves as a critical component in the fuel injection system, acting as a connector and seal between the fuel line and the fuel injector. Its primary function is to provide a secure and reliable connection, preventing fuel leaks and ensuring that the correct amount of fuel is delivered to the injector at the right pressure. The fitting is often made of durable materials like brass or stainless steel to withstand the corrosive nature of fuel and the internal pressures within the system.
Yes, the fuel line connection to the fuel injector can be replaced, but it requires careful disassembly and reassembly of the fuel system. If a leak or malfunction is detected, it is recommended to consult a professional mechanic or refer to the vehicle's repair manual for specific instructions. The process involves removing the old fitting, cleaning the surfaces, and then reinstalling a new fitting with the fuel line. Proper torque and sealing techniques must be followed to ensure a successful repair.