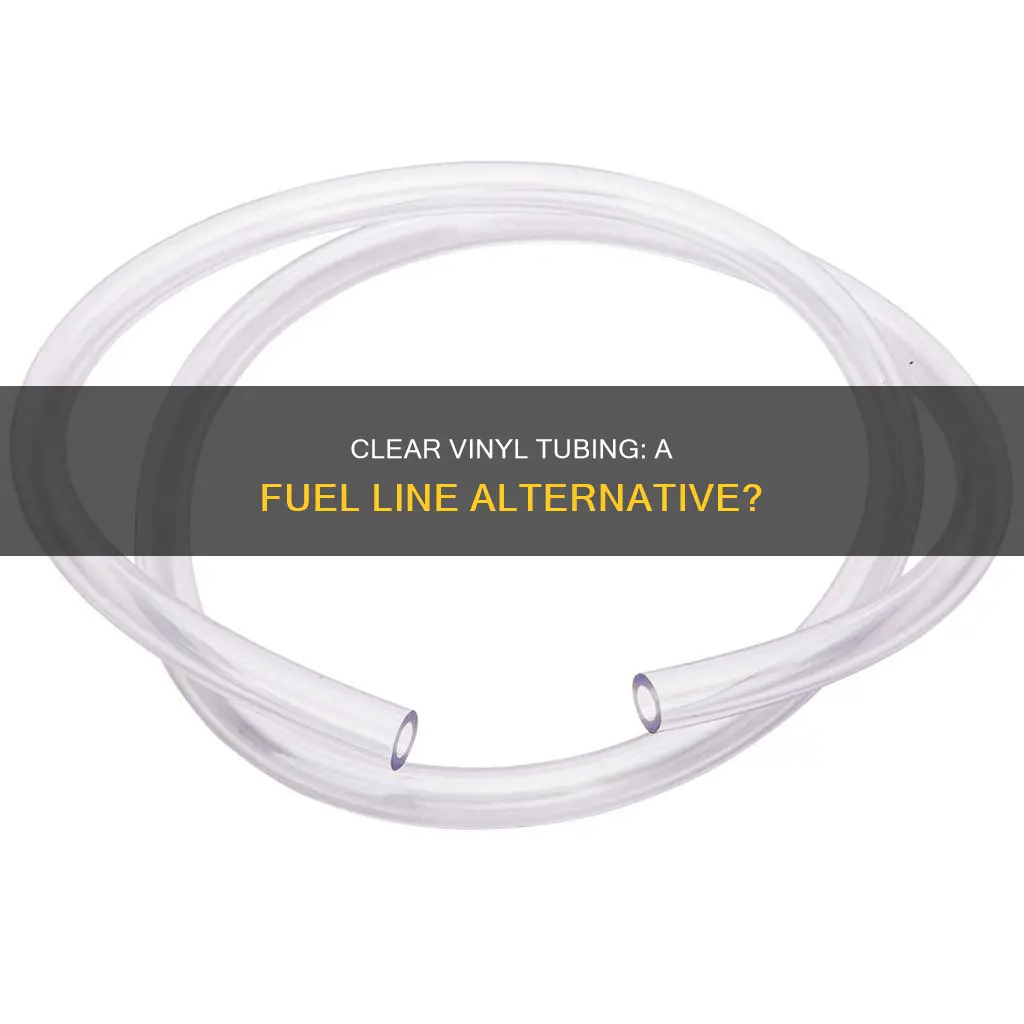
Clear vinyl tubing is a versatile material commonly used in various applications, but its suitability for fuel lines is a topic of debate. While some argue that clear vinyl tubing can be used for fuel lines, others caution against its use due to potential risks. This paragraph aims to explore the feasibility of using clear vinyl tubing for fuel lines, considering factors such as material compatibility, durability, and safety. By examining the advantages and disadvantages, we can determine whether clear vinyl tubing is a viable option for fuel line applications.
Characteristics | Values |
---|---|
Material | Vinyl |
Color | Clear |
Temperature Range | -40°F to 140°F (-40°C to 60°C) |
Flexibility | Good |
Chemical Resistance | Limited; suitable for non-aggressive fuels |
Pressure Rating | Typically 150 psi (10.3 bar) |
Applications | Fuel lines, ventilation, and non-critical plumbing |
Advantages | Lightweight, flexible, and cost-effective |
Disadvantages | Not suitable for high-temperature environments, can degrade over time with fuel exposure |
Regulatory Compliance | May require additional testing and approval for fuel use |
Standards | Meets or exceeds industry standards for fuel lines |
What You'll Learn
- Material Compatibility: Ensure the vinyl tubing is compatible with the fuel's properties
- Temperature Resistance: Check if the tubing can withstand fuel temperature variations
- Flexibility: Assess the tubing's flexibility for easy installation and movement
- Pressure Rating: Verify the tubing's pressure rating to handle fuel flow
- Durability: Evaluate the tubing's durability against fuel-related wear and tear
Material Compatibility: Ensure the vinyl tubing is compatible with the fuel's properties
When considering the use of clear vinyl tubing for fuel lines, it is crucial to prioritize material compatibility to ensure the safety and efficiency of the fuel delivery system. The compatibility of the tubing with the fuel's properties is a critical factor that can directly impact the performance and longevity of the fuel system. Here's a detailed guide on how to ensure compatibility:
Understand Fuel Properties: Different fuels have unique characteristics that can affect the choice of tubing material. For instance, gasoline, diesel, and aviation fuels have varying compositions and properties. Gasoline, being less dense and more volatile, requires tubing that can withstand its corrosive nature and prevent leaks. Diesel, on the other hand, is more viscous and can exert higher pressure on the tubing. Aviation fuels are often highly corrosive and require specialized materials. Understanding these fuel properties is essential to select the appropriate vinyl tubing.
Vinyl Tubing Considerations: Clear vinyl tubing, while flexible and lightweight, has specific limitations when used for fuel lines. The tubing's chemical composition and additives should be compatible with the fuel to avoid degradation over time. Some vinyl types may not withstand the corrosive effects of certain fuels, leading to potential leaks or fuel contamination. It is important to choose a vinyl formulation that is resistant to the specific fuel's chemicals and additives.
Testing and Certification: Reputable manufacturers often provide data sheets or technical specifications that outline the compatibility of their vinyl tubing with various fuels. Look for certifications and standards that ensure the tubing's suitability for fuel applications. Industry-recognized certifications, such as those from the Society of Automotive Engineers (SAE) or the American Petroleum Institute (API), can provide assurance of the tubing's performance and compatibility.
Customized Solutions: In some cases, customized vinyl tubing solutions may be required for specific fuel applications. This involves working with manufacturers to tailor the tubing's composition and additives to meet the unique demands of the fuel. Customization ensures that the tubing is optimized for the particular fuel's properties, providing enhanced compatibility and performance.
Regular Maintenance and Inspection: Even with compatible vinyl tubing, regular maintenance and inspections are essential. Over time, fuel lines can experience wear and tear, especially in high-pressure or high-temperature environments. Regular checks for cracks, brittleness, or signs of fuel degradation are necessary to ensure the system's safety and reliability.
Nylon Fuel Line: Top Sources for Purchase
You may want to see also
Temperature Resistance: Check if the tubing can withstand fuel temperature variations
When considering the use of clear vinyl tubing for fuel lines, it's crucial to evaluate its temperature resistance to ensure it can handle the varying fuel temperatures it will encounter. Fuel temperatures can fluctuate significantly, especially in different climates and operating conditions. Therefore, understanding the tubing's temperature range is essential to prevent damage and ensure safe operation.
Vinyl tubing, while known for its flexibility and cost-effectiveness, has limitations when it comes to temperature. Clear vinyl, in particular, is generally not suitable for fuel lines due to its relatively low temperature resistance. It can become brittle and crack when exposed to cold temperatures, which could lead to fuel leaks and potential safety hazards. On the other hand, when subjected to high temperatures, clear vinyl may soften and lose its structural integrity, potentially causing the fuel line to collapse or become dislodged.
To assess the temperature resistance of the tubing, it's important to consider the operating conditions of your specific application. Look for the tubing's temperature rating, which is often provided by the manufacturer. This rating will typically specify the maximum and minimum temperatures the tubing can withstand without permanent deformation or loss of function. For fuel lines, it's advisable to choose a tubing material with a temperature range that comfortably exceeds the expected minimum and maximum fuel temperatures.
In addition to the temperature rating, consider the duration of exposure to these temperatures. If the tubing will be subjected to extreme temperatures for extended periods, it may require a more robust material to ensure long-term reliability. For instance, some fuel lines might benefit from the use of specialized tubing designed to handle the wide temperature variations associated with fuel systems.
Lastly, it's worth noting that temperature resistance is not the only factor to consider. The flexibility, durability, and chemical resistance of the tubing are also important characteristics to ensure a reliable fuel line system. By carefully evaluating these factors, you can make an informed decision about the suitability of clear vinyl tubing for your specific fuel line application.
Finding the Perfect Fuel Line Size for Your Big Red 200ES
You may want to see also
Flexibility: Assess the tubing's flexibility for easy installation and movement
When considering the use of clear vinyl tubing for fuel lines, one crucial aspect to evaluate is its flexibility. Flexibility is a key factor in ensuring easy installation and accommodating the dynamic nature of fuel lines, especially in vehicles or machinery with moving parts. The ability of the tubing to bend and adjust to various positions without kinking or cracking is essential for a reliable and safe fuel system.
Vinyl tubing, known for its lightweight and durable properties, offers a good balance of flexibility and strength. Its design allows it to navigate through tight spaces and around obstacles with ease. When assessing flexibility, it's important to consider the tubing's ability to conform to the vehicle's contours without excessive bending or twisting. This ensures that the fuel line remains secure and doesn't interfere with other components during operation.
During installation, the tubing should be able to follow the natural curves and angles of the vehicle's frame and engine compartment. A flexible material will enable a neat and tidy route for the fuel line, reducing the risk of damage and improving overall aesthetics. Additionally, flexibility is vital when connecting multiple components, as it allows for smooth transitions and reduces stress on the tubing.
The flexibility of clear vinyl tubing also plays a role in its ability to withstand temperature changes. Fuel lines can experience temperature fluctuations, especially in outdoor environments. A flexible tubing material can better adapt to these changes, preventing cracks or leaks that may occur with less flexible alternatives. This is particularly important in ensuring the long-term reliability of the fuel system.
In summary, when using clear vinyl tubing for fuel lines, flexibility is a critical characteristic to assess. It enables easy installation, accommodates the vehicle's design, and provides durability in varying temperatures. By choosing tubing with adequate flexibility, you can ensure a secure and efficient fuel system, contributing to the overall performance and safety of the vehicle or machinery.
Fuel Line Straightening: A Step-by-Step Guide to a Smooth Ride
You may want to see also
Pressure Rating: Verify the tubing's pressure rating to handle fuel flow
When considering the use of clear vinyl tubing for fuel lines, it is crucial to prioritize safety and performance. One critical aspect to evaluate is the pressure rating of the tubing. Fuel systems operate under varying pressure conditions, and the chosen material must be able to withstand these pressures to ensure reliable and safe operation.
The pressure rating of a tubing material indicates the maximum pressure it can handle without compromising its structural integrity. For fuel lines, it is essential to select a tubing with a pressure rating that exceeds the system's operating pressure. This ensures that the tubing can accommodate the fuel flow rate and any potential pressure fluctuations without risk of failure or leakage.
To verify the pressure rating, consult the manufacturer's specifications for the chosen vinyl tubing. These specifications should provide detailed information about the tubing's construction, including the type of vinyl used and any reinforcing materials. Look for data sheets or technical documents that outline the pressure-temperature ratings for the specific tubing model. These ratings will typically be expressed in units of pressure, such as pounds per square inch (psi) or bar, and may vary depending on the tubing's thickness and dimensions.
Additionally, consider the potential operating conditions of the fuel system. Different fuel types and engine applications may require specific pressure ratings. For instance, high-performance engines or systems operating at elevated temperatures might demand higher pressure-rated tubing to handle the increased stress. It is essential to match the tubing's pressure rating to the system's requirements to ensure optimal performance and prevent potential hazards.
In summary, when using clear vinyl tubing for fuel lines, always verify the pressure rating to ensure it meets or exceeds the system's operating conditions. This critical step in the selection process helps guarantee the safety and efficiency of the fuel system, preventing potential failures and ensuring reliable fuel delivery.
Silverado Fuel Line: Understanding the Routing and Connections
You may want to see also
Durability: Evaluate the tubing's durability against fuel-related wear and tear
When considering the use of clear vinyl tubing for fuel lines, durability is a critical factor to evaluate, especially when it comes to the harsh conditions fuel can impose. Vinyl tubing, known for its flexibility and transparency, has been a popular choice for various applications, but its suitability for fuel lines requires careful examination.
The primary concern with vinyl tubing in fuel-related applications is its resistance to fuel-borne chemicals and the overall wear and tear it may experience. Fuel, especially when it contains additives, can be aggressive and potentially damage certain materials over time. Clear vinyl, while durable for many purposes, might not withstand the corrosive effects of fuel, leading to potential degradation and failure. This is particularly important in high-pressure systems or when the fuel contains ethanol, which can be more corrosive.
To assess durability, one should consider the tubing's ability to resist cracking, softening, or becoming brittle when exposed to fuel. A comprehensive test should involve subjecting the vinyl tubing to controlled fuel exposure and monitoring its performance over time. This could include using accelerated aging tests, where the tubing is exposed to simulated fuel conditions at elevated temperatures and pressures to mimic real-world usage. The results of these tests will provide valuable insights into the tubing's long-term viability.
Additionally, the flexibility of vinyl tubing is an advantage in many applications, but it can also be a concern in fuel lines. While flexibility is beneficial for accommodating vibrations and minor movements, it might not provide the necessary rigidity to withstand the constant pressure and potential shocks in a fuel system. This could lead to potential leaks or damage over time. Therefore, a balance must be struck between flexibility and the structural integrity required for a fuel line.
In summary, while clear vinyl tubing has its merits, its durability in fuel-related applications needs to be thoroughly evaluated. The tubing should be tested rigorously to ensure it can withstand the chemical and physical demands of fuel, providing a reliable and safe solution for fuel lines. This evaluation is crucial to ensure the longevity and performance of the fuel system, especially in critical applications where reliability is paramount.
Nylon Fuel Line: Choosing the Right Material for Optimal Performance
You may want to see also
Frequently asked questions
While clear vinyl tubing is not typically recommended for fuel lines, it can be used in certain applications. Clear vinyl is a flexible and lightweight material, making it suitable for non-critical fuel transfer lines or for use in non-fuel-intensive environments. However, it's important to note that vinyl is not as durable or resistant to fuel chemicals as some other materials like rubber or plastic.
The main limitations include its lower temperature resistance, as vinyl can become brittle and crack at lower temperatures. It also has limited resistance to fuel chemicals, which can cause degradation over time. Additionally, vinyl is not as strong as other materials, so it may not be suitable for high-pressure applications or in environments with frequent vibrations.
Clear vinyl tubing can be used for non-aggressive fuels like gasoline or ethanol blends. It is not ideal for fuels with high alcohol content or those containing water, as vinyl can absorb moisture and become less flexible. For more aggressive fuels like diesel or certain industrial chemicals, it's recommended to use materials with better chemical resistance, such as rubber or specialized fuel-grade plastics.