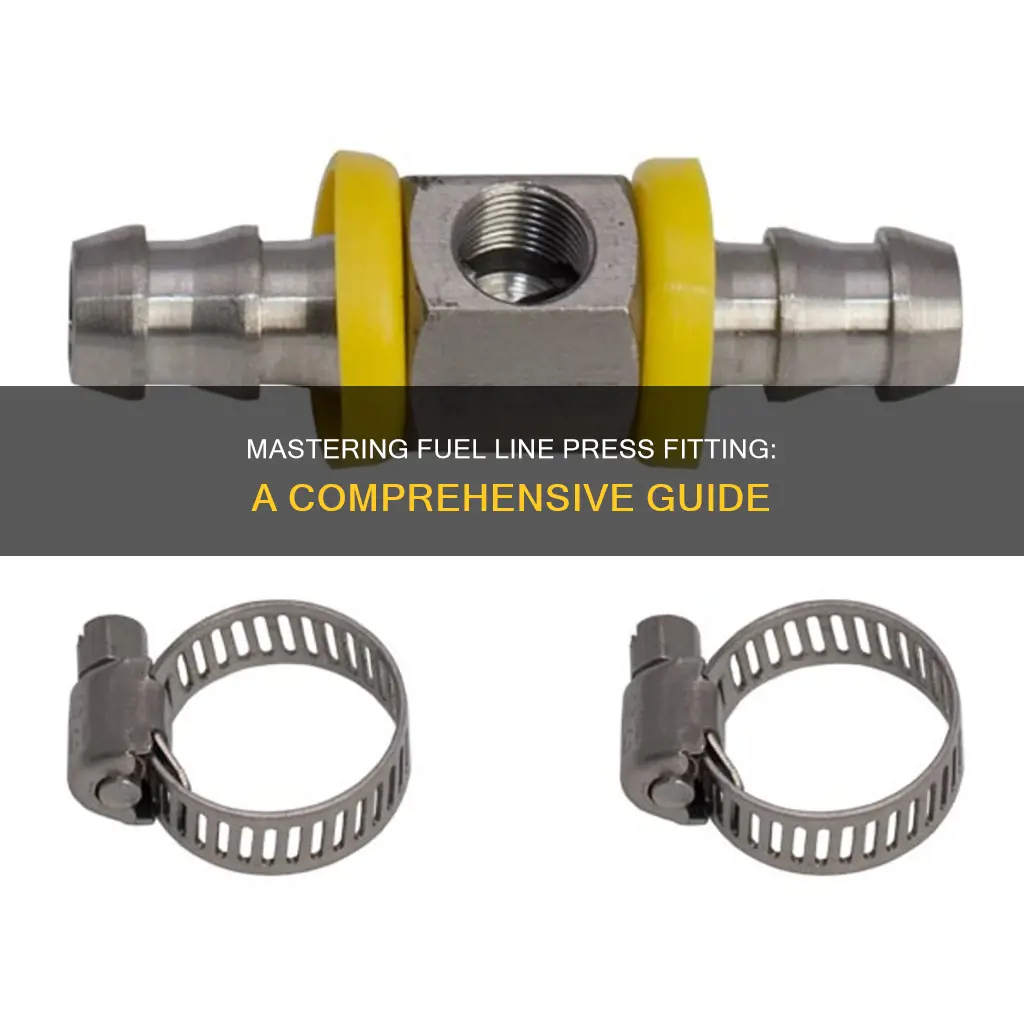
Press fittings onto fuel lines is a crucial process in ensuring a secure and leak-free connection for fuel delivery systems. This method involves using specialized tools to apply pressure to the fitting, which then creates a tight seal around the fuel line. The process requires precision and care to avoid damage to the fuel lines and ensure a reliable connection. Understanding the proper techniques and tools for press fitting is essential for anyone working on fuel systems, as it can significantly impact the performance and safety of the vehicle.
What You'll Learn
- Tools and Materials: Gather necessary tools like crimping pliers and fuel line
- Preparation: Clean and inspect fuel lines for damage before fitting
- Alignment: Ensure fuel lines are straight and aligned with fittings
- Crimping Technique: Apply pressure to crimp fittings onto fuel lines
- Testing: Verify proper connection by checking for leaks and functionality
Tools and Materials: Gather necessary tools like crimping pliers and fuel line
To ensure a secure and reliable connection for your fuel lines, it's essential to gather the right tools and materials. One of the most critical tools for this task is a set of crimping pliers. These specialized pliers are designed to create a tight and secure connection between the fuel line and the fitting. Look for a pair with adjustable jaws to accommodate different sizes of fittings. Additionally, ensure that the crimping pliers have a sturdy build and a comfortable grip to exert the necessary force without slipping.
Another crucial component is the fuel line itself. When selecting the fuel line, consider the specific requirements of your vehicle, including the diameter and material compatibility. Common materials for fuel lines include rubber, vinyl, or braided steel, each offering different levels of flexibility and durability. Choose a length that allows for a few extra inches of material on either side of the fitting to ensure a proper fit.
In addition to the crimping pliers and fuel line, you'll need a few other basic tools. A pair of adjustable wrenches or spanners will be useful for tightening the fittings securely. It's also a good idea to have a fuel line cutter or a sharp knife to trim the fuel line to the desired length. Furthermore, consider using a fuel line cleaner or a solvent to ensure a clean and dry connection, as contaminants can affect the performance of the fitting.
Remember, having the right tools and materials is just the first step. Proper technique and attention to detail are equally important when pressing fittings onto fuel lines. Always follow the manufacturer's guidelines and safety instructions for your specific vehicle and fittings.
Fixing Rust: A Guide to Repairing Fuel Lines with Compression Fittings
You may want to see also
Preparation: Clean and inspect fuel lines for damage before fitting
Before attempting to press-fit fuel lines, it is crucial to ensure a thorough preparation process to guarantee a successful and safe installation. The first step is to clean the fuel lines meticulously. Over time, fuel lines can accumulate dirt, debris, and contaminants from the fuel itself, which can lead to blockages and reduced performance. Start by removing any visible dirt or corrosion using a wire brush or a specialized fuel line cleaner. Pay close attention to bends and fittings, as these areas are prone to accumulation. Rinse the lines thoroughly with clean water to remove any residue, ensuring no traces of cleaning agents remain.
Once cleaned, inspect the fuel lines for any signs of damage. Look for cracks, punctures, or any other form of deterioration. This is essential as damaged lines can lead to fuel leaks, which pose a significant safety hazard. Check for any kinks or bends that might have occurred during storage or transportation. Ensure that the lines are flexible and free from any obstructions. If any damage is found, it is imperative to replace the affected sections before proceeding with the fitting process.
In addition to visual inspection, consider using a fuel line inspection camera to get a comprehensive view of the interior. This tool can help identify internal damage, blockages, or any other issues that might not be visible to the naked eye. By thoroughly cleaning and inspecting the fuel lines, you ensure that the fitting process is carried out on a solid foundation, minimizing the risk of future problems.
Remember, proper preparation is key to a successful installation, and taking the time to clean and inspect the fuel lines will pay off in the long run, ensuring optimal performance and safety. Always follow manufacturer guidelines and best practices to ensure you are using the correct tools and techniques for your specific fuel line fitting requirements.
Honda's Green Revolution: Plant-Based Fuel Lines?
You may want to see also
Alignment: Ensure fuel lines are straight and aligned with fittings
When working with fuel lines, ensuring proper alignment is crucial for a secure and leak-free connection. Here's a detailed guide on how to achieve this:
Understanding the Importance of Alignment: Before beginning the installation, it's essential to grasp why alignment matters. Fuel lines carry a highly volatile substance, and any misalignment can lead to potential leaks, which can be dangerous and cause engine performance issues. Proper alignment ensures a tight seal, preventing fuel from escaping and maintaining the integrity of the fuel system.
Preparation and Inspection: Start by laying out all the necessary components, including the fuel lines, fittings, and any necessary tools. Inspect the fittings for any signs of damage or wear. Ensure that the fittings are the correct size and type for your fuel lines. Measure and mark the desired length of the fuel lines, allowing for a slight overlap at the fittings to ensure a secure connection.
Alignment Technique: Begin by positioning the fuel line over the fitting, ensuring that it is centered and aligned with the fitting's port. Use a straightedge or a ruler to verify the line's straightness. The key is to maintain a consistent angle and position throughout the installation process. Avoid kinking or bending the fuel line excessively, as this can compromise its integrity.
Securing the Connection: Once the line is aligned, proceed with the installation process according to the manufacturer's instructions. This typically involves inserting the fitting into the fuel line and using a press tool or crimping method to create a secure connection. Apply firm pressure to the fitting, ensuring it is fully seated and locked into place. Repeat this process for each fitting, maintaining consistent alignment at every step.
Final Checks: After completing the installation, inspect the connections thoroughly. Look for any signs of fuel leakage around the fittings. Test the system by starting the engine and monitoring for any unusual noises or vibrations. Ensure that all connections are tight and secure. Proper alignment during the installation process will contribute to a reliable and long-lasting fuel system.
Mastering Fuel Line Measurement: A Comprehensive Guide
You may want to see also
Crimping Technique: Apply pressure to crimp fittings onto fuel lines
The crimping technique is a crucial method for securing fuel lines to fittings, ensuring a reliable and leak-free connection. This process involves applying precise pressure to the crimp fitting, which then compresses the fitting onto the fuel line, creating a secure bond. Here's a step-by-step guide to mastering this technique:
Preparation: Before beginning, ensure you have the necessary tools, including the crimping tool, the appropriate-sized crimp ring or sleeve, and the fuel line fitting. Inspect the fitting and fuel line for any damage or debris, ensuring they are clean and free of contaminants.
Positioning: Place the fuel line into the fitting, ensuring it is centered and aligned correctly. The fitting should have a designated port or groove to guide the fuel line, making it easier to position accurately.
Crimping Process: Now, the key step: apply pressure to the crimping tool. The tool will typically have a handle or lever that you need to squeeze or pull to generate the required force. The amount of pressure required can vary depending on the type of fitting and fuel line, so it's essential to consult the manufacturer's guidelines or refer to a resource like the one you searched for. As you apply pressure, the crimp ring or sleeve will compress around the fuel line, creating a secure grip. Ensure that the entire length of the fitting is crimped, not just a portion, to guarantee a robust connection.
Release and Inspection: After applying the pressure, slowly release the tool and check the crimp. It should appear as a smooth, continuous curve without any gaps or sharp edges. If the crimp is not uniform, it may indicate insufficient pressure or a misaligned fitting. In such cases, carefully remove the fitting and try again, ensuring you follow the manufacturer's recommendations for pressure and technique.
Safety and Practice: Crimping fuel lines requires precision and care. Always work in a well-ventilated area, and wear protective gear, especially when dealing with fuel. Practice this technique on scrap materials or old fittings to become proficient before working on critical fuel system components. Remember, a well-crimped fitting can make the difference between a reliable fuel system and potential leaks or system failures.
Gas Line Antifreeze: Unraveling the Fuel Stabilizer Mystery
You may want to see also
Testing: Verify proper connection by checking for leaks and functionality
When working with fuel lines, ensuring a secure and leak-free connection is crucial to prevent potential hazards and maintain the integrity of your vehicle's fuel system. Here's a detailed guide on how to test and verify the proper connection of press-fit fittings on fuel lines:
Leak Testing:
- After installing the press-fit fitting, it is essential to perform a leak test to ensure the connection is tight and secure. Start by applying a small amount of fuel or a suitable sealant around the fitting's threads. This step helps to identify any potential leaks.
- Use a leak detection method such as a soapy water solution or a specialized fuel line leak detector. Apply this solution to the fitting and its surrounding area, ensuring it covers the entire connection.
- Observe the fitting closely for any bubbles or foam forming on the surface. If you notice any bubbles, it indicates a potential leak. In such cases, re-tighten the fitting and retest until the leak is eliminated.
- For a more thorough test, you can use a pressure gauge to apply a slight vacuum or pressure to the fitting. This method helps identify internal leaks that might not be visible to the naked eye.
Functionality Check:
- Once the leak test is successful, it's time to verify the functionality of the press-fit fitting. Start the vehicle's engine and allow it to run for a few minutes to ensure it reaches operating temperature.
- Check for any unusual noises or vibrations coming from the fuel lines. Any rattling or unusual sounds could indicate a loose connection or potential damage.
- Monitor the fuel gauge and ensure it reads correctly. If the gauge shows an incorrect fuel level, it might suggest a leak or an issue with the fitting's functionality.
- Perform a visual inspection of the fuel lines and fittings. Look for any signs of damage, corrosion, or debris that might affect the flow of fuel. Ensure that the fitting is securely attached and there are no visible signs of wear.
Additional Tips:
- Always refer to the manufacturer's guidelines or instructions specific to the press-fit fitting you are using. Different fittings may have unique testing procedures.
- If you are using a fuel line with multiple fittings, repeat the leak and functionality tests at each connection point to ensure the entire system is secure.
- Regularly inspect and test fuel lines, especially in older vehicles or those with a history of fuel system issues, to prevent potential problems and ensure optimal performance.
Honda Motorcycle Fuel Line: Size Guide for Optimal Performance
You may want to see also
Frequently asked questions
A press fitting is a type of connector used to join fuel lines to fuel tanks or other components. It involves applying pressure to the fitting to create a secure and leak-tight connection. This method ensures a tight seal, preventing fuel leaks and potential hazards.
Selecting the appropriate press fitting depends on factors such as fuel line diameter, material, and the specific application. Refer to the manufacturer's guidelines or consult a fuel system expert to determine the correct fitting size and type for your fuel line.
You will need a few essential tools for this process, including a press tool (often a hydraulic or mechanical press), a die or mandrel specific to the fitting type, and a set of pliers or wrenches for any additional adjustments. Ensure you have the right tools for the job to achieve a proper connection.
It is generally not recommended to reuse press fittings, especially if they have been used previously. Over time, the fitting's sealing properties may degrade, and repeated use can lead to reduced performance and potential fuel leaks. It's best to replace them when needed.
During the installation process, you might encounter issues like improper alignment, insufficient pressure application, or incorrect fitting size. These problems can result in an ineffective connection. Always follow the manufacturer's instructions and double-check your work to avoid such complications.