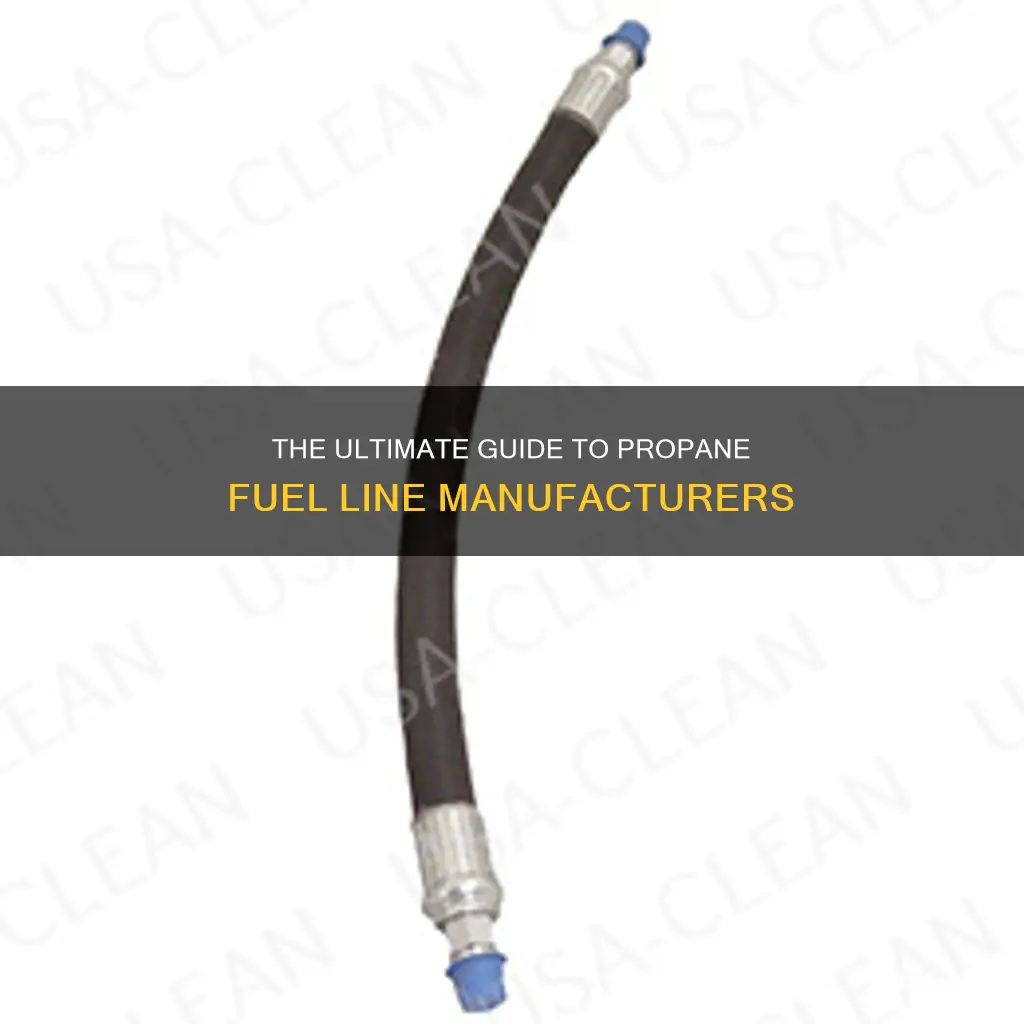
Propane fuel lines are an essential component for vehicles and appliances that run on propane gas. The production of these fuel lines involves specialized manufacturing processes to ensure durability and safety. Various companies and manufacturers worldwide produce propane fuel lines, each adhering to industry standards and regulations. These manufacturers utilize high-quality materials, such as stainless steel or brass, to create fuel lines that can withstand the corrosive nature of propane gas. The production process includes precise welding, coating, and testing to guarantee the integrity of the fuel lines. Understanding the different manufacturers and their production processes is crucial for selecting the right propane fuel lines for specific applications.
What You'll Learn
- Propane Fuel Line Manufacturing Process: The production of propane fuel lines involves extrusion, bending, and welding
- Materials Used in Propane Fuel Lines: Common materials include steel, aluminum, and plastic, each with unique properties
- Safety Standards and Regulations: Propane fuel lines must meet strict safety standards to prevent leaks and explosions
- Design and Engineering Considerations: Engineers consider factors like pressure, temperature, and compatibility when designing fuel lines
- Installation and Maintenance: Proper installation and regular maintenance are crucial to ensure the safe operation of propane fuel lines
Propane Fuel Line Manufacturing Process: The production of propane fuel lines involves extrusion, bending, and welding
The manufacturing process of propane fuel lines is a precise and intricate procedure, ensuring the production of high-quality components for the safe and efficient delivery of propane gas. This process primarily involves three key steps: extrusion, bending, and welding, each contributing to the final product's durability and reliability.
Extrusion: The journey begins with the selection of a suitable material, typically a flexible and durable polymer such as polypropylene or polyethylene. This material is then heated and softened through a process called extrusion, where it is pushed through a die to create a continuous, hollow tube. The die's design is crucial, as it determines the diameter and wall thickness of the fuel line. The extruded tube is then cooled and hardened, ensuring it maintains its shape and structural integrity. This step is critical as it sets the foundation for the fuel line's performance and safety.
Bending: After extrusion, the fuel line tube is ready for the bending process. This step requires precision and care to avoid damaging the material. The tube is carefully bent to the required curvature, ensuring it can withstand the pressure and flow of propane gas. Bending machines are often used to achieve consistent and accurate bends, especially for fuel lines destined for automotive or industrial applications. The bend radius and angle are carefully calculated to prevent stress concentrations that could lead to leaks or failures.
Welding: Welding is the final critical step in the manufacturing process. This process involves joining two or more fuel line segments together to form a continuous, seamless tube. The welding technique used depends on the specific application and material. For example, in-line welding is common for creating long, continuous fuel lines, while spot welding might be used for smaller, more intricate connections. The welds must be strong and leak-tight to ensure the safety and efficiency of the propane fuel system. Advanced welding techniques, such as laser or ultrasonic welding, are often employed to achieve high-quality, consistent joints.
The entire manufacturing process is a delicate balance of precision and quality control. Each step is carefully monitored to ensure the fuel lines meet industry standards and customer expectations. The final product should be flexible yet robust, capable of withstanding the harsh conditions of fuel transport and delivery. Properly manufactured propane fuel lines are essential for the safe operation of various applications, from residential BBQs to commercial vehicles and industrial equipment.
Duromax Fuel Line Diameter: 2003 Model Specs Revealed
You may want to see also
Materials Used in Propane Fuel Lines: Common materials include steel, aluminum, and plastic, each with unique properties
Propane fuel lines are an essential component of any propane-powered vehicle or appliance, and the choice of material is crucial for safety, durability, and performance. The primary materials used in the construction of these fuel lines are steel, aluminum, and various types of plastic, each offering distinct advantages and disadvantages.
Steel: One of the most common materials for propane fuel lines is steel, known for its exceptional strength and durability. Steel fuel lines are highly resistant to corrosion and can withstand high-pressure environments, making them ideal for propane systems. This material is often preferred for its longevity and ability to handle the rigors of everyday use. The thickness of steel lines varies, with thicker walls providing increased pressure resistance, which is crucial for propane systems that operate at elevated pressures. However, steel fuel lines can be heavier and more rigid compared to other materials, which might be a consideration for certain applications.
Aluminum: Aluminum is another popular choice for propane fuel lines, particularly in applications where weight reduction is essential. This material is lightweight, offering excellent corrosion resistance, and is often used in high-performance vehicles or appliances where fuel efficiency and reduced weight are critical. Aluminum lines are flexible and easy to install, making them a convenient option. However, they may not be as durable as steel and can be more susceptible to damage from sharp objects or impacts. Despite this, aluminum's advantages in terms of weight savings and corrosion resistance make it a preferred choice for certain propane systems.
Plastic (Polyethylene and Polypropylene): Plastic fuel lines, typically made from polyethylene or polypropylene, have gained significant popularity due to their flexibility, lightweight nature, and cost-effectiveness. These materials are highly resistant to corrosion and offer excellent flexibility, making them easy to route and install. Plastic lines are often used in residential propane appliances, such as grills and water heaters, where they provide a safe and reliable solution. The flexibility of plastic also reduces the risk of damage during installation and everyday use. However, it's important to note that plastic fuel lines may not be suitable for high-pressure applications and can be more susceptible to cracking or degradation over time, especially when exposed to sunlight.
Each material has its own set of advantages and is chosen based on the specific requirements of the propane system. Steel provides strength and durability, aluminum offers lightweight performance, and plastic delivers flexibility and cost-effectiveness. The choice of material ultimately depends on the intended use, environmental factors, and the specific needs of the propane fuel system in question.
Evinrude Outboard Fuel Line Sizing: 1999 200 HP Guide
You may want to see also
Safety Standards and Regulations: Propane fuel lines must meet strict safety standards to prevent leaks and explosions
Propane fuel lines are a critical component of any propane-powered system, and their safety is of utmost importance to prevent potential hazards. The manufacturing and installation of these fuel lines are subject to strict safety standards and regulations to ensure they meet the necessary requirements. These standards are in place to mitigate the risks associated with propane, a highly flammable and explosive gas.
One of the key regulations is the use of approved materials for the construction of fuel lines. Manufacturers must select materials that are compatible with propane and resistant to corrosion and degradation over time. Common materials include high-density polyethylene (HDPE) and stainless steel, which are known for their durability and ability to withstand the corrosive effects of propane. These materials are carefully chosen to ensure the long-term integrity of the fuel lines and prevent any potential leaks.
Safety standards also dictate the design and construction of the fuel lines. The lines must be designed to withstand pressure and temperature variations, ensuring they can handle the demands of the propane system. Manufacturers are required to follow specific guidelines for bending, joining, and terminating the fuel lines to ensure a secure and leak-free connection. Proper crimping, soldering, or welding techniques are employed to create a robust and reliable joint.
Furthermore, safety regulations mandate that propane fuel lines be installed by trained professionals who adhere to established protocols. This includes proper routing to avoid potential hazards like heat sources, sharp edges, or areas with high foot traffic. The lines should be securely fastened and protected from physical damage, ensuring they remain intact and functional over the system's lifespan.
Regular inspections and maintenance are also essential to meet safety standards. Propane fuel lines should be checked for any signs of damage, corrosion, or wear, especially in areas where they are exposed to the environment. Timely replacement or repair of faulty lines is crucial to prevent leaks and ensure the overall safety of the propane system. By adhering to these safety standards and regulations, manufacturers and users can minimize the risks associated with propane fuel lines and create a safer environment.
Unveiling the Mystery: Where Are Your Fuel Injector Lines?
You may want to see also
Design and Engineering Considerations: Engineers consider factors like pressure, temperature, and compatibility when designing fuel lines
When it comes to designing fuel lines for propane, engineers must consider several critical factors to ensure safety, efficiency, and reliability. Propane fuel lines are designed to transport this volatile and flammable gas from the tank to the appliance, and any failure in the system could lead to dangerous consequences.
One of the primary considerations is pressure. Propane is a compressed gas, and the fuel lines must be able to withstand the pressure exerted by the gas at various temperatures and conditions. Engineers calculate the required pressure rating for the fuel line based on the expected operating conditions, including the maximum and minimum temperatures the line will encounter and the pressure at which the propane is supplied. This ensures that the fuel line can handle the stress and prevent potential failures or leaks.
Temperature is another crucial factor. Propane's behavior can change significantly with temperature variations. Engineers need to select materials that can withstand the expected temperature range, from the cold temperatures at which propane can condense to the higher temperatures it may reach during operation. Materials with appropriate thermal expansion and contraction properties are chosen to ensure the fuel line maintains its integrity and seals over the entire temperature range.
Compatibility is also essential in the design process. The materials used for the fuel line, fittings, and connectors must be compatible with propane to prevent corrosion, degradation, or chemical reactions that could compromise the system's safety. Engineers select materials that are resistant to propane's corrosive nature and can withstand the gas's chemical properties without leaching or releasing harmful substances. This includes considering the compatibility of the materials with the surrounding environment and any potential contaminants.
Additionally, engineers must consider the design and layout of the fuel line system. This includes the routing of the line to avoid potential hazards, such as sharp bends or kinks that could restrict flow or cause damage. The system should also be designed to minimize the risk of vibration-induced failures, especially in mobile applications. Proper support and protection for the fuel line are essential to ensure its longevity and safety.
In summary, designing fuel lines for propane requires a meticulous approach, taking into account pressure, temperature, and compatibility. Engineers must carefully select materials and design the system to ensure it can handle the unique challenges posed by propane transportation and usage. This attention to detail is vital to prevent accidents and ensure the efficient and safe operation of propane-powered appliances.
Scooter Fuel Lines: Powering the Engine's Heart
You may want to see also
Installation and Maintenance: Proper installation and regular maintenance are crucial to ensure the safe operation of propane fuel lines
The installation and maintenance of propane fuel lines are critical aspects of ensuring the safe and efficient operation of any propane-powered system. Proper installation is the foundation for a reliable and safe system, and it requires careful attention to detail. When installing propane fuel lines, it is essential to use high-quality materials that are designed for propane use. This includes selecting the right type of fuel line, such as flexible or rigid lines, depending on the specific application and environment. Flexible lines are commonly used for their ease of installation and ability to conform to various shapes, while rigid lines offer more structural support and are ideal for outdoor applications.
During the installation process, it is crucial to follow manufacturer guidelines and local building codes. The fuel lines should be securely attached to the propane tank and the appliance using appropriate fittings and clamps. Proper alignment and support are essential to prevent damage and ensure a tight seal. All connections must be tight and free from any leaks, as even a small leak can lead to potential hazards. It is recommended to use a propane leak detector or soapy water test to verify the integrity of the connections.
Regular maintenance is equally important to keep the propane fuel lines in optimal condition. Over time, fuel lines can degrade due to various factors such as temperature fluctuations, UV exposure, and chemical corrosion. Inspecting the fuel lines periodically for any signs of damage, cracks, or brittleness is essential. Look for any visible wear and tear, especially at connection points and bends, as these areas are more susceptible to deterioration. If any issues are detected, immediate action should be taken to repair or replace the affected sections.
In addition to visual inspections, it is beneficial to perform pressure tests on the fuel lines to ensure they can withstand the required operating pressures. These tests can identify potential weaknesses or leaks that may not be visible to the naked eye. Regular maintenance also includes keeping the propane tank and associated equipment clean and free from debris. This helps prevent blockages and ensures the efficient flow of propane.
By adhering to proper installation practices and implementing regular maintenance routines, you can significantly reduce the risk of accidents and ensure the longevity of your propane fuel lines. It is always advisable to consult the manufacturer's guidelines and, if necessary, seek professional assistance to guarantee the safety and performance of your propane system.
Optimizing Fuel Delivery: Choosing the Right Line for Your 500HP EFI Engine
You may want to see also
Frequently asked questions
Propane fuel lines are typically manufactured by specialized companies that produce components for the fuel industry. These manufacturers ensure the lines meet industry standards and regulations for safe propane transportation and usage.
It's important to purchase propane fuel lines from reputable and authorized suppliers. These suppliers often have partnerships with manufacturers to ensure the lines are of high quality and compatible with various propane systems. Always check for certifications and reviews to make an informed choice.
The lifespan of a propane fuel line depends on various factors, including the material, quality, installation, and maintenance. With proper care and regular inspections, a well-maintained fuel line can last for many years. It is recommended to replace lines every 10-15 years or as advised by the manufacturer.
Yes, propane fuel lines can be made from various materials such as steel, aluminum, or plastic (polyethylene). Each material has its advantages and is chosen based on factors like cost, durability, and resistance to corrosion. Common types include stainless steel, aluminum-clad steel, and high-density polyethylene (HDPE).
Safety is paramount when selecting a manufacturer. Look for companies that adhere to industry standards and regulations, such as those set by the American Society of Mechanical Engineers (ASME) and the National Fire Protection Association (NFPA). Ensure they provide detailed specifications, testing reports, and warranties to guarantee the safety and reliability of their products.