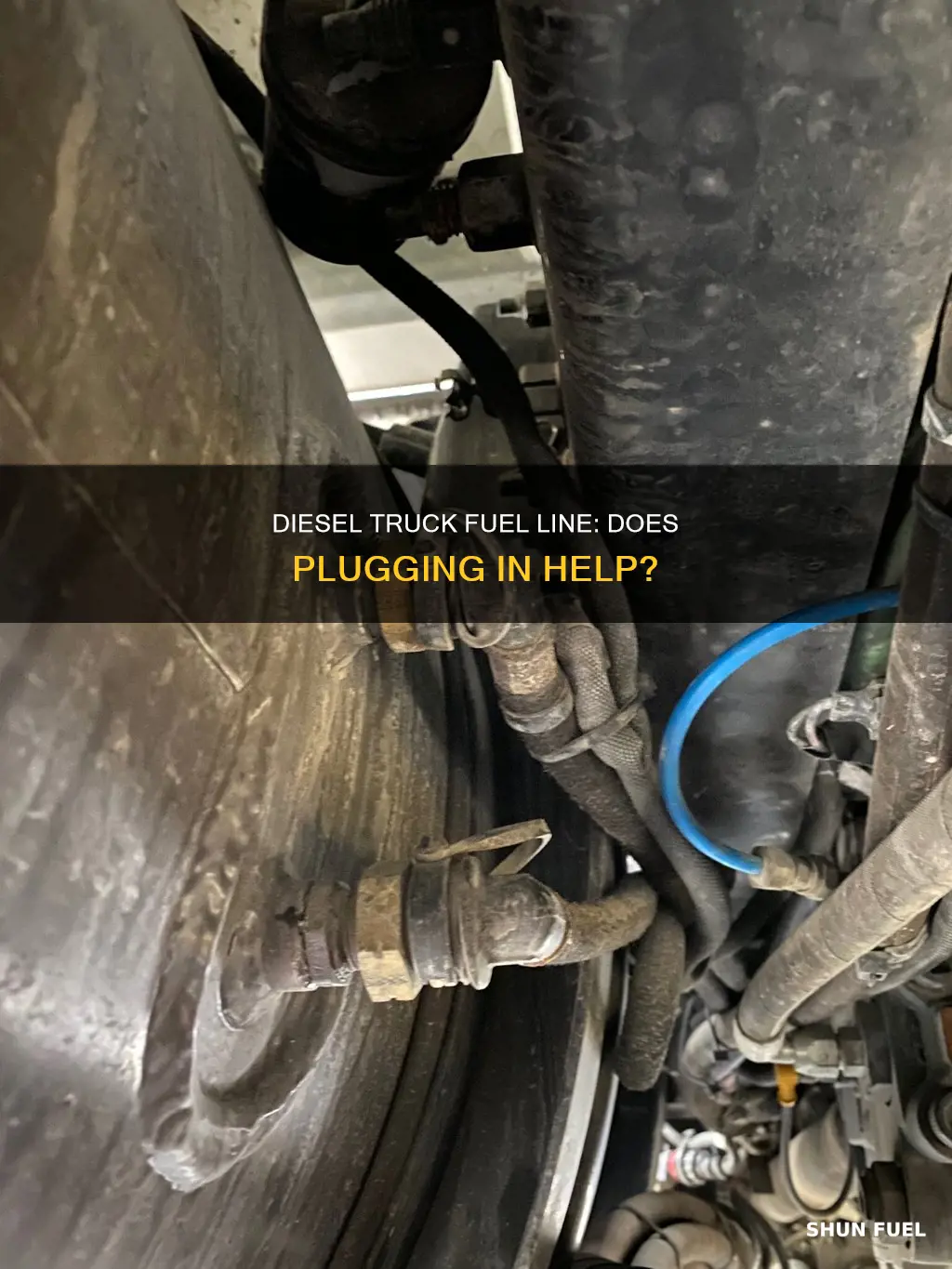
When it comes to diesel trucks, proper maintenance is crucial to ensure optimal performance and longevity. One common question among truck owners is whether plugging in the truck helps fuel lines. In this paragraph, we will explore the benefits and potential drawbacks of this practice, examining how it can impact fuel line health and overall engine performance. By understanding the pros and cons, truck owners can make informed decisions about their vehicle's maintenance routine.
Characteristics | Values |
---|---|
Fuel Line Maintenance | Plugging in a diesel truck can help maintain the fuel lines by preventing fuel degradation. The electrical power can run fuel line pumps, ensuring a consistent flow of fuel to the engine. |
Fuel Efficiency | Improved fuel efficiency is a potential benefit. The electric power can assist in optimizing fuel usage, especially during idling, which can save fuel and reduce emissions. |
Engine Performance | Enhanced engine performance is possible. The additional power can improve acceleration and overall engine response, making the truck more responsive. |
Emission Reduction | Reduced emissions are a key advantage. The electric system can help lower the release of pollutants, contributing to a cleaner environment. |
Long-Term Reliability | Over time, plugging in can increase the truck's reliability. It may extend the lifespan of the fuel system, reducing the need for frequent repairs. |
Fuel Line Health | The practice can promote healthier fuel lines by preventing fuel contamination and ensuring proper fuel circulation. |
Cost Savings | While there may be initial costs, long-term savings can be achieved through reduced fuel consumption and maintenance expenses. |
Environmental Impact | A more eco-friendly approach, as it can minimize the environmental footprint of diesel trucks. |
Technology Integration | Modern diesel trucks often feature advanced technology, and plugging in can enhance the integration of various systems, including fuel management. |
Safety | Improved safety is a potential outcome, as a well-maintained fuel system can reduce the risk of fuel-related accidents. |
What You'll Learn
- Fuel Line Material: Different materials react differently to electricity, so choose wisely
- Fuel Line Length: Longer lines may require more power to maintain pressure
- Fuel Pump Efficiency: Plugging in can improve pump performance and fuel flow
- Fuel Filter Maintenance: Regular cleaning prevents clogging and ensures clean fuel delivery
- Fuel Tank Venting: Proper venting prevents pressure buildup and fuel line damage
Fuel Line Material: Different materials react differently to electricity, so choose wisely
When it comes to fuel lines in diesel trucks, the choice of material is crucial, as different materials can react differently to electricity, potentially causing issues over time. This is especially important when considering the use of electricity to help maintain or repair these lines, as some materials may be more susceptible to damage or corrosion when exposed to electrical currents.
One common material used for fuel lines is rubber. Rubber is a good insulator, meaning it can effectively block the flow of electricity. This property makes it a suitable choice for fuel lines, as it helps prevent electrical interference that could potentially damage the fuel system. However, it's important to note that rubber fuel lines may require more frequent replacements due to their susceptibility to wear and tear from fuel contaminants.
On the other hand, some materials, like certain types of plastic, can be more reactive to electricity. For instance, polyvinyl chloride (PVC) is a common plastic used in various applications, including fuel lines. While PVC is generally a good insulator, some types of PVC can be more prone to electrical discharge, which may lead to arcing or sparking. This can be a concern, especially in high-voltage environments, as it could potentially damage the fuel system or even pose a safety risk.
Another factor to consider is the material's resistance to corrosion. Fuel lines are constantly exposed to fuel, which can contain moisture and acids that can accelerate corrosion. Materials like stainless steel and brass are often preferred for their excellent corrosion resistance, ensuring that the fuel lines remain in good condition over time. These materials are also less likely to react with electricity, making them a safer choice for electrical applications.
In summary, when dealing with fuel lines in diesel trucks, it's essential to choose materials that are compatible with electrical systems and can withstand the corrosive nature of fuel. By selecting the right material, you can ensure the longevity and reliability of the fuel system, potentially saving time and money on maintenance and repairs.
Choosing the Right Fuel Line for Your 04 RMZ 250
You may want to see also
Fuel Line Length: Longer lines may require more power to maintain pressure
The length of the fuel line in a diesel truck plays a significant role in its performance and efficiency, especially when it comes to maintaining adequate fuel pressure. Longer fuel lines, while providing more flexibility and potentially reducing the risk of damage from minor impacts, present unique challenges. One of the primary concerns is the increased resistance that longer lines offer to the flow of fuel. As the fuel travels through the line, it must overcome this resistance, which can lead to a decrease in pressure at the engine's fuel injectors. This reduction in pressure can result in less efficient combustion, reduced power output, and even potential engine misfires.
To address this issue, it is essential to consider the power requirements of the fuel system. Longer fuel lines demand more power to maintain the necessary pressure to ensure optimal engine performance. The fuel pump, which is responsible for creating the required pressure, must work harder to overcome the increased resistance. This can lead to higher fuel consumption and, in some cases, even strain on the pump itself, potentially reducing its lifespan.
One effective solution to mitigate the impact of longer fuel lines is to use a fuel pressure regulator. This device monitors and adjusts the fuel pressure to maintain a consistent level, compensating for the increased resistance. By ensuring that the fuel pressure remains within the optimal range, the engine can operate efficiently, and the risk of performance issues due to low pressure is minimized. Additionally, regular maintenance, such as checking and replacing the fuel filter, can help maintain the overall health of the fuel system.
For diesel truck owners, it is crucial to be aware of the potential challenges posed by longer fuel lines. Proper maintenance and the use of appropriate accessories, such as fuel pressure regulators, can help ensure that the engine continues to perform at its best. Understanding the relationship between fuel line length and power requirements is essential for optimizing the performance and longevity of a diesel truck's fuel system.
In summary, longer fuel lines in diesel trucks require more power to maintain the necessary pressure for efficient operation. This increased resistance can lead to reduced engine performance and potential issues. Implementing solutions like fuel pressure regulators and regular maintenance can help mitigate these challenges, ensuring that the truck's fuel system operates optimally.
Unleash Your Engine's Potential: Understanding the 8AM Fuel Line
You may want to see also
Fuel Pump Efficiency: Plugging in can improve pump performance and fuel flow
Plugging in a diesel truck can have a significant impact on fuel pump efficiency and overall fuel flow, which is a crucial aspect of vehicle performance and longevity. When you connect a truck to a power source, such as a battery charger or a portable generator, it provides an additional electrical load that can help optimize the fuel pump's operation. This is particularly beneficial for diesel engines, which often rely on robust fuel systems to ensure efficient combustion.
The primary benefit of plugging in is the potential to enhance the fuel pump's performance. Fuel pumps are responsible for delivering fuel from the tank to the engine at the required pressure. Over time, these pumps can experience wear and tear, leading to reduced efficiency. By applying an external power source, you can create a controlled environment that allows the pump to operate at its peak capacity. This additional power can help maintain or even increase the pump's pressure output, ensuring a steady and consistent fuel supply to the engine.
In the context of diesel trucks, where fuel lines are typically longer and more complex compared to gasoline vehicles, plugging in can be a game-changer. Longer fuel lines can lead to pressure drops, especially during acceleration or when the engine is under load. By improving the pump's performance, you can mitigate these pressure losses, ensuring that the engine receives the necessary fuel volume and pressure for optimal operation. This is especially important for heavy-duty diesel trucks, where efficient fuel management is critical for performance and fuel economy.
Furthermore, plugging in can contribute to better fuel flow management. When a diesel truck is idling or stationary, the fuel pump may not be operating at its most efficient level, leading to potential fuel wastage. By connecting the truck to a power source, you can ensure that the pump remains active and operational, even when the engine is not running. This proactive approach helps maintain the health of the fuel system, reducing the risk of fuel line blockages, sediment buildup, and other issues that can arise from stagnant fuel.
In summary, plugging in a diesel truck can be a valuable practice to enhance fuel pump efficiency and overall fuel flow. It provides an opportunity to optimize the pump's performance, manage pressure drops in longer fuel lines, and ensure a consistent fuel supply. By incorporating this simple maintenance step, diesel truck owners can improve their vehicle's performance, fuel economy, and the longevity of their fuel system components.
Flare for Aluminum Fuel Lines: Unlocking the Secrets of a Perfect Fit
You may want to see also
Fuel Filter Maintenance: Regular cleaning prevents clogging and ensures clean fuel delivery
Maintaining the fuel filter on your diesel truck is an essential part of regular vehicle care. Over time, fuel filters can become clogged with contaminants, leading to reduced engine performance and potential long-term damage. Regular cleaning and maintenance of the fuel filter can help prevent these issues and ensure your truck runs efficiently.
The primary function of a fuel filter is to remove impurities from the fuel before it reaches the engine. Diesel fuel can contain various contaminants, including water, sediment, and even small particles of metal or debris. When these impurities accumulate in the filter, they can restrict fuel flow, leading to engine misfires, reduced power, and even temporary loss of power. Regular cleaning of the fuel filter helps to remove these contaminants, ensuring that only clean, high-quality fuel reaches the engine.
One effective method for maintaining the fuel filter is to use a fuel filter cleaner. These products are designed to dissolve and remove built-up contaminants, restoring the filter's performance. They are typically added to the fuel tank and circulate through the system, cleaning the filter and the fuel lines. It's important to follow the manufacturer's instructions for the correct dosage and usage of these cleaners.
In addition to using fuel filter cleaners, it's also recommended to regularly inspect and replace the fuel filter. Over time, even with cleaning, the filter can become worn out or damaged. A visual inspection can help identify signs of wear, such as cracks or leaks. If the filter is in poor condition, it should be replaced to ensure optimal fuel delivery. Regular replacement intervals can vary, but it's generally advised to check the manufacturer's guidelines for your specific truck model.
By implementing a regular fuel filter maintenance routine, you can significantly improve the performance and longevity of your diesel truck's engine. This simple yet crucial task can help prevent costly repairs and ensure your vehicle operates at its best. Remember, proper maintenance is key to keeping your truck reliable and efficient on the road.
Camaro Fuel Line Placement: Above or Below Battery Cables?
You may want to see also
Fuel Tank Venting: Proper venting prevents pressure buildup and fuel line damage
Proper venting of the fuel tank is a critical aspect of maintaining a diesel truck's fuel system, ensuring optimal performance and longevity. When a diesel engine operates, it generates pressure within the fuel tank due to the combustion process and the expansion of gases. Without adequate ventilation, this pressure can build up, leading to several issues that may damage the fuel lines and overall system.
The primary purpose of venting is to release this excess pressure and allow the fuel to breathe, preventing a vacuum that could restrict the flow of fuel to the engine. Over time, a vacuum condition can cause fuel to become stale and less efficient, impacting the truck's performance. Moreover, the pressure buildup can lead to the formation of air bubbles in the fuel lines, which can be extremely detrimental. These bubbles may cause erratic engine behavior, reduced power, and even engine stall.
Venting the fuel tank is a relatively simple process. It involves the installation of a vent line, typically a small diameter tube, that connects the fuel tank to the atmosphere or a breather system. This line allows air to enter the tank, equalizing the pressure and preventing the formation of a vacuum. The vent should be positioned in a way that it is not susceptible to water intrusion, especially in vehicles used in wet environments. Water in the fuel can cause corrosion and further damage the fuel system.
In addition to the physical venting, it is essential to consider the role of the fuel tank's breather cap or breather system. These components are designed to allow air to enter the tank while keeping contaminants out. Regular inspection and cleaning of these parts are necessary to ensure their effectiveness. Over time, they can become clogged with dirt and debris, hindering the proper venting process.
By implementing proper venting techniques, diesel truck owners can significantly reduce the risk of fuel line damage and ensure a consistent and efficient fuel supply to the engine. This simple maintenance practice is often overlooked but plays a vital role in the overall health and performance of the vehicle's fuel system.
Thawing Diesel Fuel Lines: Optimal Temperature for Winter
You may want to see also
Frequently asked questions
Plugging in a diesel truck, especially when referring to the act of connecting a vehicle to a power source, is not a common or recommended practice for fuel line maintenance. However, if you're asking about the use of a fuel plug, it can be a useful tool for temporary fuel line protection. A fuel plug is a device that can be inserted into the fuel line to prevent fuel from flowing while the truck is being worked on, ensuring that the fuel system remains dry and clean.
A fuel plug is designed to fit into the fuel line, creating a sealed connection. When installed, it blocks the flow of fuel, allowing for safe and controlled access to the fuel system without the risk of spills or contamination. This is particularly useful when replacing fuel filters, repairing fuel lines, or performing other maintenance tasks that require temporary fuel isolation.
While fuel plugs are a convenient solution, they should be used with caution. Prolonged use may lead to fuel line degradation over time, especially if the plug is not removed promptly after the work is completed. It's essential to follow manufacturer guidelines and remove the plug once the task is finished to ensure the fuel system's integrity.
No, plugging in a diesel truck is not a permanent solution for fuel line problems. It is a temporary measure to ensure safety during maintenance. For long-term fuel line issues, it's recommended to inspect and repair the fuel system, which may involve replacing damaged lines, filters, or other components. Regular maintenance and addressing fuel system problems promptly can help prevent further complications.