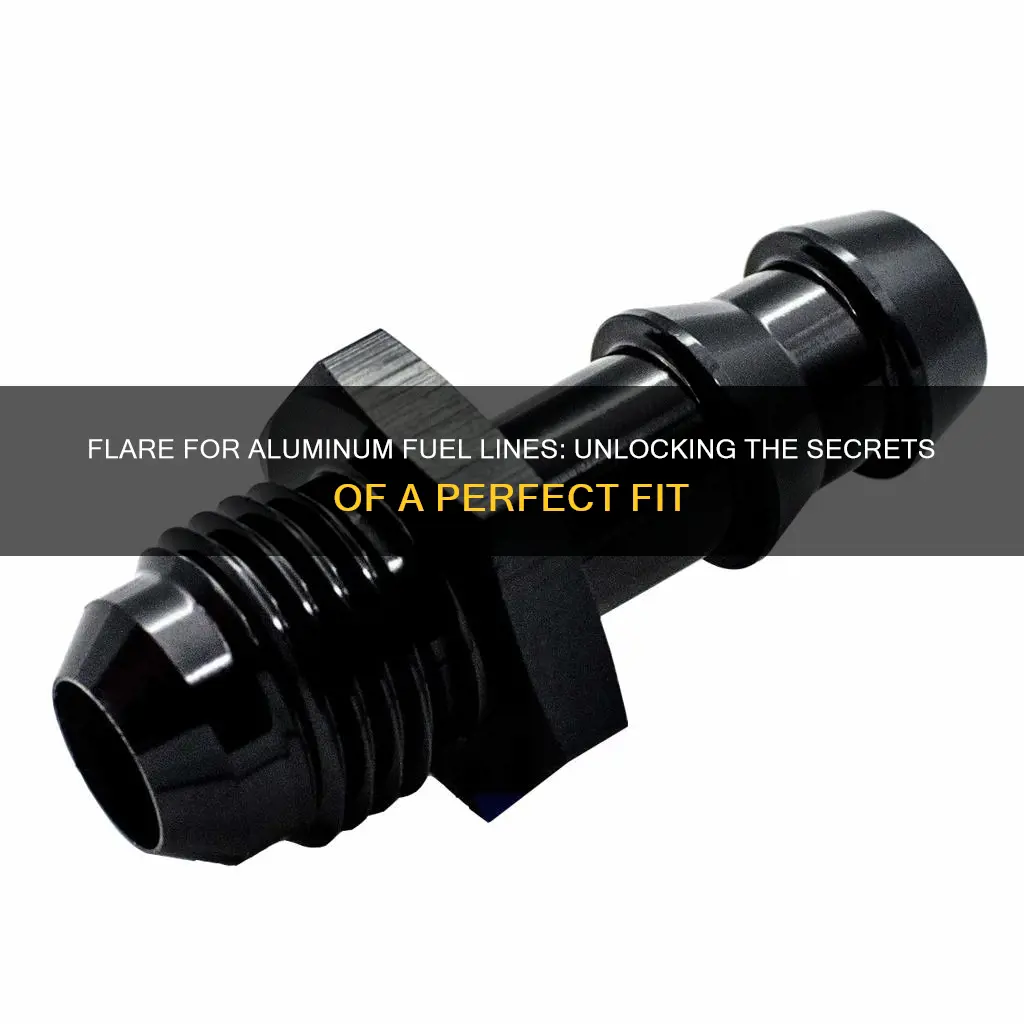
Aluminum fuel lines are a popular choice for many vehicle owners due to their lightweight and corrosion-resistant properties. However, one common issue that arises with these lines is the tendency to develop a flare or kink, which can lead to fuel leaks and other problems. In this article, we will explore the causes of flare in aluminum fuel lines and discuss various methods to prevent and fix this issue, ensuring your vehicle's fuel system remains reliable and efficient.
What You'll Learn
- Material Strength: Aluminum fuel lines offer high tensile strength, ensuring durability and resistance to pressure
- Corrosion Resistance: These lines are resistant to corrosion, preventing fuel degradation and maintaining system efficiency
- Flexibility: Aluminum's flexibility allows for easy installation and adaptability in various engine configurations
- Weight Reduction: Lighter than steel, aluminum lines reduce engine weight, improving performance and fuel efficiency
- Temperature Tolerance: Aluminum can withstand temperature fluctuations, making it suitable for a wide range of climates
Material Strength: Aluminum fuel lines offer high tensile strength, ensuring durability and resistance to pressure
Aluminum fuel lines are an excellent choice for automotive applications, particularly in high-performance vehicles and those requiring lightweight materials. One of the key advantages of using aluminum in fuel lines is its exceptional material strength. Aluminum fuel lines are engineered to provide high tensile strength, which is a critical factor in ensuring the durability and reliability of the fuel delivery system.
Tensile strength refers to the ability of a material to withstand pulling forces without breaking or deforming permanently. In the context of fuel lines, this property is vital as it directly impacts the line's ability to resist pressure and maintain its structural integrity. Aluminum fuel lines are designed to handle the demanding conditions of fuel transport, including varying temperatures, pressure fluctuations, and potential vibrations during vehicle operation.
The high tensile strength of aluminum is achieved through its unique crystalline structure and the alloying process. Aluminum alloys, such as those commonly used in fuel lines, are created by combining aluminum with other elements like copper, magnesium, or silicon. These alloys enhance the material's strength and hardness while maintaining its characteristic lightweight properties. The result is a fuel line that can withstand the rigorous demands of automotive use.
This strength is particularly important in preventing fuel leaks and maintaining a secure connection between the fuel tank and engine. Aluminum fuel lines can effectively resist the pressure generated by fuel injection systems, ensuring a tight seal and minimizing the risk of fuel escaping. Moreover, the durability provided by high tensile strength allows these lines to withstand the wear and tear of daily use, making them a long-lasting solution for fuel delivery systems.
In summary, the material strength of aluminum fuel lines, specifically their high tensile strength, is a significant advantage in the automotive industry. It enables these fuel lines to endure the challenges of fuel transport, providing a reliable and secure connection while maintaining the overall performance and longevity of the vehicle's fuel system. This feature, combined with aluminum's lightweight nature, makes it an ideal choice for applications where both strength and weight reduction are essential.
Choosing the Right Fuel Line: Size Matters!
You may want to see also
Corrosion Resistance: These lines are resistant to corrosion, preventing fuel degradation and maintaining system efficiency
Aluminum fuel lines are an excellent choice for many applications, especially in marine and aviation environments, where corrosion resistance is a critical factor. These lines are designed to withstand the harsh conditions that fuel systems often encounter, ensuring long-lasting performance and reliability. One of the key advantages of aluminum fuel lines is their inherent corrosion resistance, which is a result of the material's natural properties.
Corrosion is a natural process that occurs when a material reacts with its environment, leading to the deterioration of its structure and functionality. In the context of fuel lines, corrosion can cause significant issues, including fuel degradation, reduced system efficiency, and potential failures. Aluminum, however, has a unique composition that makes it highly resistant to corrosion. Its oxide layer, formed when exposed to air, acts as a protective barrier, preventing further oxidation and corrosion. This natural protection ensures that the fuel lines remain intact and functional over extended periods.
The corrosion resistance of aluminum fuel lines is particularly beneficial in marine environments, where saltwater exposure is common. Saltwater contains electrolytes that can accelerate corrosion, but aluminum's natural resistance helps mitigate this issue. By using aluminum fuel lines, marine vessel owners can ensure that their fuel systems remain efficient and reliable, even in the challenging conditions of saltwater environments.
Additionally, the corrosion-resistant nature of these lines contributes to the overall longevity of the fuel system. By preventing fuel degradation, the lines maintain the quality of the fuel, ensuring that it remains stable and suitable for combustion. This is crucial for optimal engine performance and can help avoid costly repairs or replacements due to fuel-related issues.
In summary, the corrosion resistance of aluminum fuel lines is a significant advantage, offering protection against fuel degradation and system inefficiency. This feature makes aluminum fuel lines an ideal choice for various applications, especially in corrosive environments, where maintaining system efficiency and reliability is essential. By understanding the benefits of corrosion resistance, users can make informed decisions when selecting fuel lines for their specific needs.
Fuel Line Spray: Normal or Cause for Concern?
You may want to see also
Flexibility: Aluminum's flexibility allows for easy installation and adaptability in various engine configurations
Aluminum fuel lines offer a unique advantage in terms of flexibility, which is a crucial factor in engine design and maintenance. This material's inherent pliability allows for easy installation and adaptation to various engine configurations, making it a preferred choice for many automotive enthusiasts and professionals. The flexibility of aluminum is particularly beneficial when dealing with complex engine layouts, tight spaces, or when retrofitting older vehicles with modern fuel systems.
One of the key advantages is its ability to conform to the engine's contours without putting excessive strain on the fuel lines. This is especially important in high-performance engines where fuel delivery needs to be precise and efficient. By using aluminum, you can ensure that the fuel lines are securely in place but also have the necessary give to accommodate any slight movements or vibrations during operation. This flexibility helps prevent fuel leaks and ensures a consistent fuel supply to the engine, even under demanding conditions.
In engine configurations with limited space, such as compact cars or motorcycles, aluminum's flexibility becomes even more critical. It allows for creative routing solutions, enabling mechanics to navigate around various components and fit the fuel lines into the available space. This adaptability ensures that the fuel system is not only functional but also aesthetically pleasing, maintaining the overall appearance of the vehicle.
Furthermore, aluminum's flexibility simplifies the installation process. Mechanics can quickly and efficiently route the fuel lines, secure them with clips or brackets, and ensure a tight fit without the risk of damage to the engine or surrounding components. This ease of installation can significantly reduce labor costs and time spent on assembly, making it an attractive option for both DIY enthusiasts and professional mechanics.
The flexibility of aluminum fuel lines is a game-changer for engine customization and repair. It empowers mechanics and enthusiasts to tailor the fuel system to their specific needs, whether it's retrofitting a classic car with a modern fuel injection system or modifying a high-performance engine for racing. This adaptability ensures that the fuel lines can be customized to fit the unique demands of each engine configuration, providing optimal performance and reliability.
Troubleshooting Fuel Line Issues: Signs and Solutions
You may want to see also
Weight Reduction: Lighter than steel, aluminum lines reduce engine weight, improving performance and fuel efficiency
The use of aluminum in fuel lines has become increasingly popular in the automotive industry due to its unique properties, particularly its ability to reduce weight without compromising strength. This is a significant advantage, especially in high-performance engines where weight reduction plays a crucial role in improving overall vehicle performance and fuel efficiency.
Aluminum fuel lines offer a substantial weight savings compared to traditional steel lines. Steel, being a denser material, contributes to a heavier engine system, which can lead to decreased acceleration and increased fuel consumption. By replacing steel with aluminum, engineers can achieve a lighter-weight solution without sacrificing the structural integrity required for fuel delivery. This reduction in weight translates to improved handling and a more responsive vehicle, allowing for quicker acceleration and better overall performance.
The benefits of weight reduction extend beyond the engine bay. Lighter fuel lines contribute to a more efficient vehicle as a whole. With reduced weight, the engine doesn't have to work as hard to propel the car, resulting in lower fuel consumption. This is particularly advantageous for high-performance vehicles that demand optimal power output while maintaining fuel efficiency. Additionally, the improved handling and responsiveness can enhance the overall driving experience, making the vehicle more enjoyable to operate.
In the pursuit of weight reduction, engineers have developed various techniques to ensure the structural integrity of aluminum fuel lines. These lines are designed with careful consideration of thickness and material composition to match or exceed the strength of steel lines. Advanced manufacturing processes, such as precision bending and welding, ensure that aluminum lines can withstand the pressures and temperatures encountered in an engine environment. This attention to detail allows for the realization of the weight-saving benefits of aluminum without compromising safety or performance.
Furthermore, the use of aluminum fuel lines can contribute to a more compact engine design. The reduced weight allows for more efficient packaging of components, potentially leading to a smaller engine footprint. This is especially valuable in modern vehicles, where engine space is often limited, and every inch of space is crucial for optimizing performance and aesthetics.
In summary, aluminum fuel lines offer a compelling solution for weight reduction in engines. Their lightweight nature, coupled with advanced manufacturing techniques, ensures that performance and safety are not compromised. By embracing aluminum, engineers can create more efficient, responsive, and compact vehicle designs, ultimately enhancing the overall driving experience.
Fuel Lines: Powering Your Snowmobile's Performance and Efficiency
You may want to see also
Temperature Tolerance: Aluminum can withstand temperature fluctuations, making it suitable for a wide range of climates
Aluminum's remarkable temperature tolerance is a key advantage when it comes to fuel lines, especially in applications where climate variations are common. This metal's ability to withstand extreme temperature fluctuations makes it an ideal choice for fuel lines in various environments, from cold, harsh winters to hot, arid deserts.
The temperature tolerance of aluminum is primarily due to its unique material properties. Aluminum has a relatively low melting point, which is around 660 degrees Celsius (1219 degrees Fahrenheit). This characteristic, however, is not a limitation but rather a feature that contributes to its versatility. When exposed to high temperatures, aluminum can maintain its structural integrity without softening or losing its shape. This is because aluminum has a high thermal conductivity, allowing it to quickly dissipate heat, preventing overheating and potential damage to the fuel line.
In contrast, other materials used for fuel lines, such as steel or certain plastics, may not offer the same level of temperature resilience. Steel, for instance, becomes brittle and prone to cracking when exposed to low temperatures, while some plastics can soften or even melt under high heat. Aluminum's ability to withstand these extreme conditions makes it a more reliable and durable option for fuel lines in a wide range of climates.
Furthermore, aluminum's temperature tolerance is not limited to its resistance to heat. It also excels in maintaining its flexibility and pliability even in extremely cold environments. This is crucial for fuel lines, as it ensures that the lines remain functional and do not become brittle or crack when exposed to sub-zero temperatures. This flexibility is particularly important in applications where the fuel lines need to navigate through tight spaces or make sharp turns.
In summary, aluminum's temperature tolerance is a critical factor in its suitability for fuel lines, especially in diverse climates. Its ability to withstand both high and low temperatures, coupled with its flexibility, makes it an excellent choice for ensuring the safe and efficient delivery of fuel in various environmental conditions. This property, combined with its lightweight nature and corrosion resistance, contributes to aluminum's widespread use in the automotive and aviation industries for fuel line systems.
Fuel Line Protests: Dakota's Burning Questions
You may want to see also
Frequently asked questions
A flare is a specialized fitting used to connect a fuel line to a fuel tank or another component in a vehicle's fuel system. It is designed to create a secure and leak-tight connection, ensuring the efficient and safe transfer of fuel. The flare for an aluminum fuel line is specifically engineered to work with aluminum materials, providing a reliable and durable connection.
If you are replacing or repairing an existing fuel line, it is essential to use the correct type of flare for the material. Aluminum fuel lines require a flare that is compatible with the aluminum material to ensure a proper fit and prevent leaks. Using the wrong flare can lead to fuel leaks, reduced performance, and potential safety hazards. Always refer to the vehicle's manual or consult a professional mechanic to determine the appropriate flare for your specific application.
It is not recommended to use a flare designed for a different material with an aluminum fuel line. Each material has unique properties and requires a specific type of flare to ensure a secure connection. Using a flare for a different material may result in an improper fit, reduced performance, and potential safety risks. Always choose the correct flare designed for the aluminum fuel line to guarantee a reliable and safe fuel system.