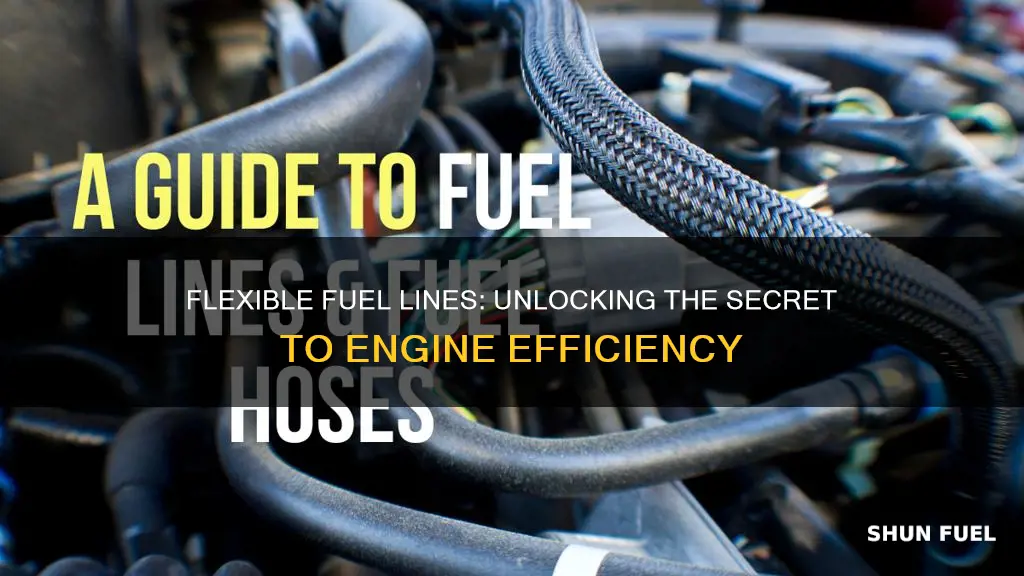
Flexible fuel lines are an essential component of modern vehicles, allowing for the efficient transfer of fuel from the tank to the engine. These lines are designed to withstand the rigors of everyday use, including temperature fluctuations and vibrations, while maintaining a tight seal to prevent fuel leaks. The word on flexible fuel lines is that they are a critical part of vehicle performance and safety, and their quality and installation can significantly impact a vehicle's reliability and longevity. Understanding the characteristics and maintenance requirements of these lines is crucial for vehicle owners and mechanics alike to ensure optimal performance and longevity.
What You'll Learn
- Material and Construction: Different materials and construction methods for flexible fuel lines
- Durability and Longevity: Factors affecting the lifespan of fuel lines
- Flexibility and Movement: Ability of fuel lines to withstand vehicle vibrations and movement
- Compatibility and Standards: Standards and compatibility with various fuel types and vehicle models
- Maintenance and Inspection: Recommended practices for maintaining and inspecting fuel lines
Material and Construction: Different materials and construction methods for flexible fuel lines
Flexible fuel lines are an essential component in the fuel delivery system of vehicles, particularly those with flexible-fuel capabilities. These lines are designed to transport fuel efficiently and reliably from the fuel tank to the engine, accommodating the unique requirements of different fuel types. The construction and material of these lines play a critical role in ensuring optimal performance and longevity.
One of the most common materials used for flexible fuel lines is rubber. Rubber is chosen for its inherent flexibility, durability, and resistance to fuel-related chemicals. Natural rubber or synthetic rubber compounds, such as neoprene or EPDM (Ethylene Propylene Diene Monomer), are often utilized. These materials can withstand the corrosive nature of various fuels, including gasoline, ethanol blends, and diesel. The construction involves layering the rubber with a reinforcing fabric or steel wire to enhance strength and flexibility, ensuring the line can handle the pressure and movement within the vehicle.
Another material gaining popularity is polyurethane. Polyurethane offers superior resistance to fuel degradation and temperature changes compared to rubber. It is an ideal choice for high-performance vehicles or those operating in extreme conditions. The construction process involves casting polyurethane around a braided or spiral-wound reinforcement, providing excellent flexibility and kink resistance. This construction method ensures the line can withstand repeated bending and movement without compromising its integrity.
In some cases, flexible fuel lines may also incorporate a blend of materials. For instance, a layer of rubber could be combined with a polyurethane outer covering. This hybrid approach leverages the benefits of both materials, providing excellent flexibility and fuel resistance. The construction technique involves carefully bonding the layers together to ensure a seamless and durable fuel line.
The construction methods also vary, with some manufacturers opting for a braided design. Braided fuel lines feature multiple layers of reinforcing material, often steel or polyester, braided together to form a strong and flexible structure. This design is particularly useful in high-pressure applications, ensuring the line can withstand the force without compromising its flexibility. Additionally, some lines may incorporate a spiral-wound construction, where a reinforcing material is wound around a core, creating a strong and flexible fuel line.
In summary, the material and construction of flexible fuel lines are crucial aspects that determine their performance and longevity. Rubber, polyurethane, and hybrid combinations offer unique advantages, ensuring compatibility with various fuels and operating conditions. The construction methods, such as braiding and spiral-winding, further enhance the line's strength and flexibility, making them essential components in modern vehicle fuel systems.
Understanding Fuel Line Sizes for Optimal Pump Performance
You may want to see also
Durability and Longevity: Factors affecting the lifespan of fuel lines
The durability and longevity of flexible fuel lines are crucial aspects to consider when it comes to vehicle performance and safety. These lines play a vital role in transporting fuel from the tank to the engine, and their quality and construction can significantly impact the overall lifespan of a vehicle. Several factors contribute to the wear and tear of fuel lines, and understanding these factors is essential for maintaining a reliable and efficient vehicle.
One of the primary factors affecting the lifespan of fuel lines is the material composition. High-quality fuel lines are typically made from durable materials such as rubber, silicone, or synthetic compounds. These materials offer excellent resistance to fuel degradation, temperature fluctuations, and chemical corrosion. For instance, silicone-based fuel lines are known for their superior flexibility, heat resistance, and ability to withstand extreme temperatures, making them a popular choice for high-performance vehicles. On the other hand, lower-grade materials may degrade faster, leading to cracks, leaks, and reduced performance over time.
Environmental factors also play a significant role in the longevity of fuel lines. Exposure to harsh weather conditions, such as extreme heat or cold, can cause the lines to become brittle or soft, respectively. Prolonged exposure to sunlight can lead to UV degradation, causing the lines to crack or become brittle. Additionally, fuel lines near the exhaust system or under the vehicle may experience accelerated wear due to heat and friction. It is essential to choose fuel lines designed to withstand the specific environmental conditions of the vehicle's intended use.
Regular maintenance and inspections are vital to ensuring the durability of fuel lines. Over time, fuel lines can develop cracks, leaks, or become susceptible to corrosion. Routine checks for any signs of damage, such as bulging, cracking, or discoloration, can help identify potential issues early on. Replacing fuel lines that show signs of wear or damage is crucial to prevent fuel leaks, engine misfires, or even fire hazards. Additionally, maintaining a clean fuel system by using fuel stabilizers and regular fuel system flushes can extend the life of the fuel lines.
Furthermore, the installation process and the overall vehicle design can impact the lifespan of fuel lines. Proper installation techniques, including the use of appropriate clamps and secure mounting, ensure that the lines remain taut and free from excessive stress. Poor installation or design flaws may lead to premature wear and potential failure. It is recommended to follow manufacturer guidelines and consult with experienced mechanics to ensure optimal installation and longevity.
In summary, the durability and longevity of flexible fuel lines are influenced by various factors, including material composition, environmental conditions, maintenance practices, and installation considerations. By choosing high-quality materials, considering the vehicle's operating environment, performing regular inspections, and adhering to proper installation techniques, vehicle owners can ensure the longevity of their fuel lines and maintain a reliable and safe driving experience.
1988 F150 Fuel Line Sizes: A Comprehensive Guide
You may want to see also
Flexibility and Movement: Ability of fuel lines to withstand vehicle vibrations and movement
The ability of fuel lines to withstand vehicle vibrations and movement is a critical aspect of automotive engineering, ensuring the efficient and safe operation of engines. Flexible fuel lines are designed to accommodate the dynamic nature of vehicles, providing a vital link between the fuel tank and the engine. These lines must be robust yet flexible to handle the various stresses and strains encountered during driving.
One of the primary considerations in designing flexible fuel lines is the material composition. Engineers often opt for high-quality, durable materials such as braided stainless steel or synthetic fibers. These materials offer excellent flexibility, allowing the fuel lines to move with the vehicle's components without becoming stiff or brittle. The flexibility is crucial in preventing excessive stress on the lines, which could lead to cracks, leaks, or even fuel contamination.
The construction of flexible fuel lines also involves careful attention to detail. Braided designs, for instance, provide a high level of flexibility by intertwining multiple layers of material. This construction method ensures that the fuel lines can bend and twist without compromising their structural integrity. Additionally, the use of protective coverings, such as rubber or plastic sheathing, adds further protection against wear and tear, especially in areas prone to vibration and movement, like the engine bay.
In the context of vehicle vibrations, flexible fuel lines must be able to absorb and distribute the energy generated by the engine and suspension. This is achieved through the use of specialized fittings and clamps that allow for controlled movement while maintaining a secure connection. The flexibility of the fuel lines ensures that they can adapt to the vehicle's natural vibrations, reducing the risk of damage and maintaining optimal fuel delivery.
Furthermore, the design of flexible fuel lines takes into account the varying temperatures and environmental conditions that vehicles experience. Materials and construction techniques are chosen to withstand these extremes, ensuring that the fuel lines remain flexible and functional in all weather conditions. This is particularly important in preventing fuel leaks and maintaining engine performance, especially in high-performance vehicles or those operating in challenging environments.
Understanding the Car's Fuel Line: A Comprehensive Guide
You may want to see also
Compatibility and Standards: Standards and compatibility with various fuel types and vehicle models
When it comes to flexible fuel lines, compatibility and standards play a crucial role in ensuring optimal performance and safety. These fuel lines are designed to handle different fuel types, such as gasoline, diesel, and even alternative fuels like liquefied petroleum gas (LPG) and compressed natural gas (CNG). The compatibility of these lines is essential to prevent fuel leaks, engine damage, and potential safety hazards.
One of the key standards to consider is the material composition of the fuel lines. Different materials are used depending on the fuel type and vehicle requirements. For example, gasoline fuel lines often use rubber or synthetic compounds, while diesel lines may require more robust materials like braided steel or stainless steel. The choice of material ensures flexibility, durability, and resistance to fuel degradation over time.
Vehicle manufacturers often provide specific guidelines regarding fuel line compatibility. These guidelines are essential to ensure that the fuel lines meet the required standards and are suitable for the particular vehicle model. For instance, some vehicles may have unique fuel system designs or require specific fuel line diameters and lengths. Adhering to these manufacturer's specifications is vital to avoid potential issues and ensure the longevity of the fuel system.
In addition to material compatibility, the standards also cover the design and construction of flexible fuel lines. These lines must be designed to withstand high-pressure fuel flow, temperature variations, and mechanical stress during vehicle operation. Manufacturers often specify the minimum burst pressure, flexibility range, and temperature resistance required for the fuel lines to ensure they can handle the demands of the fuel system.
Furthermore, the standards also address the testing and certification of flexible fuel lines. Reputable manufacturers often subject their fuel lines to rigorous testing to ensure compliance with industry standards. These tests may include pressure testing, flexibility assessments, and material durability evaluations. By adhering to these standards, consumers can have confidence in the quality and reliability of the fuel lines they purchase.
Permatex on Fuel Lines: A Carburetor Repair Hack or a No-Go?
You may want to see also
Maintenance and Inspection: Recommended practices for maintaining and inspecting fuel lines
Maintenance and Inspection: Recommended Practices
Regular maintenance and inspection of flexible fuel lines are crucial to ensure optimal performance and longevity of your vehicle's fuel system. Here are some recommended practices to keep in mind:
- Visual Inspections: Start by regularly examining the fuel lines for any signs of damage, wear, or deterioration. Look for cracks, brittleness, soft spots, or any visible damage. Pay close attention to areas where the lines connect to the fuel tank, pump, and engine. Even small tears or punctures can lead to fuel leaks, which are dangerous and costly to repair.
- Check for Leaks: A simple yet essential test is to spray a fine mist of soapy water onto the fuel lines and connections. If you notice any bubbles forming, it indicates a potential leak. Leaks can occur at fittings, connections, or where the lines are routed through the engine compartment. Address any leaks promptly to prevent fuel wastage and potential engine issues.
- Replace Worn Components: Over time, fuel lines can become brittle and prone to cracking, especially if exposed to heat or sunlight. If you notice any cracks or significant wear, it's best to replace the entire fuel line rather than just the damaged section. This ensures a thorough repair and maintains the integrity of the fuel system.
- Routine Fluid Changes: While not directly related to fuel lines, maintaining the engine's overall health is essential. Regular engine oil and coolant changes help prevent contamination and ensure efficient operation. Contaminated fuel can accelerate the degradation of fuel lines and other components.
- Use of Fuel Line Cleaner: Consider using a specialized fuel line cleaner during inspections. This can help remove any built-up deposits, varnish, or contaminants that may have accumulated over time. Cleaning the fuel lines can improve fuel flow, enhance engine performance, and extend the life of the fuel system components.
- Professional Maintenance: For complex inspections and repairs, it is advisable to consult a professional mechanic. They can provide expert advice, perform detailed inspections, and ensure that any necessary replacements or repairs are carried out correctly. Regular maintenance checks can identify potential issues before they become major problems.
Remember, flexible fuel lines are a critical component of your vehicle's fuel system, and proper care can prevent costly repairs and ensure reliable performance. By following these recommended practices, you can maintain a healthy fuel system and keep your vehicle running smoothly.
Air Bubbles in Diesel Fuel Lines: A Cause for Concern?
You may want to see also
Frequently asked questions
Flexible fuel lines are a type of hose used in vehicles to transfer fuel from the tank to the engine. They are designed to be flexible and durable, allowing for easy movement and bending without compromising the integrity of the fuel system. These lines are commonly made from materials like rubber, silicone, or a composite blend, ensuring they can withstand the pressure and temperature changes associated with fuel.
The primary difference lies in their flexibility and installation process. Traditional rigid fuel lines are stiff and straight, requiring precise routing during vehicle assembly. In contrast, flexible fuel lines are pliable, making them easier to install and adjust. This flexibility is especially beneficial in modern vehicles with compact engine compartments, where space is limited.
Yes, regular maintenance is essential to ensure the longevity and performance of flexible fuel lines. It is recommended to inspect these lines periodically for any signs of wear, cracks, or leaks. Over time, fuel lines can degrade due to exposure to fuel vapors, heat, and ultraviolet light. Cleaning the lines and replacing them if necessary can help prevent fuel leaks and maintain optimal engine performance.
While flexible fuel lines are versatile and widely used, their suitability depends on the specific vehicle model and fuel system design. Some vehicles may require specialized flexible lines due to unique engine configurations or fuel delivery systems. It is always best to consult the vehicle's manual or seek professional advice to ensure the correct type of fuel line is used for a particular make and model.