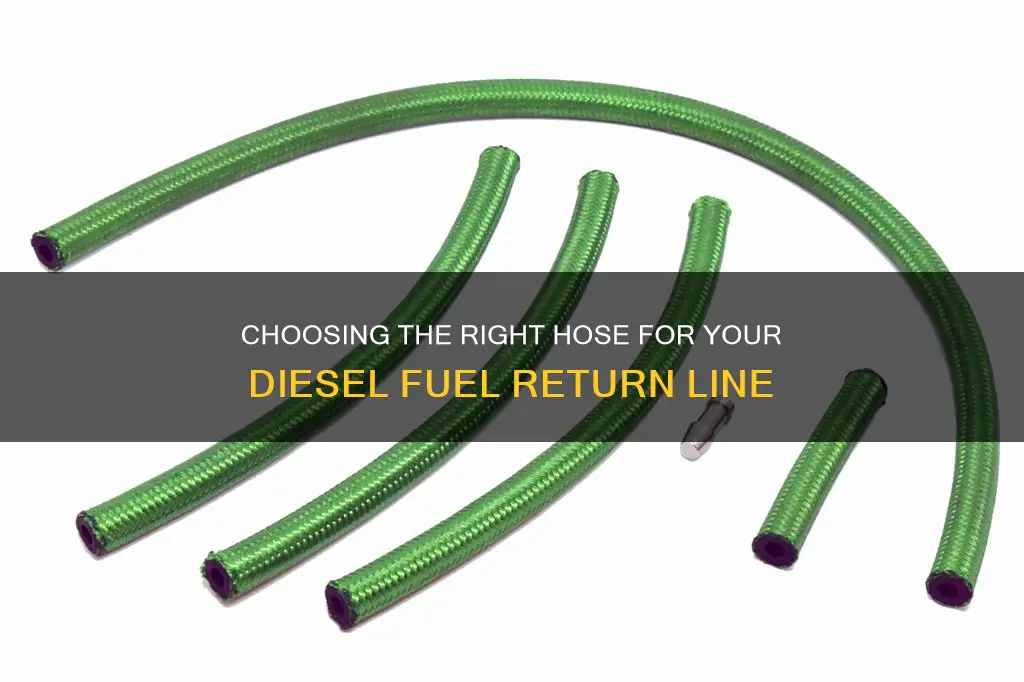
When it comes to choosing the right size hose for a return diesel fuel line, several factors come into play. The size of the hose is crucial for ensuring efficient and safe fuel transfer, as it directly impacts the flow rate and pressure. Factors such as the engine's power output, the distance between the fuel tank and the engine, and the overall system design all influence the hose's diameter. Understanding these considerations is essential for selecting the appropriate hose size to optimize performance and prevent potential issues in diesel fuel systems.
What You'll Learn
- Hose Diameter: Choose based on flow rate and pressure requirements
- Material: Select suitable material for durability and compatibility
- Length: Measure and specify the required length for the hose
- Fittings: Ensure compatibility with fuel system connectors and fittings
- Temperature Range: Consider operating temperatures to ensure hose longevity
Hose Diameter: Choose based on flow rate and pressure requirements
When selecting the appropriate hose diameter for a return diesel fuel line, it is crucial to consider the flow rate and pressure requirements of the system. The hose diameter directly impacts the capacity of the fuel to flow through it, and an incorrect choice can lead to inefficiencies or even system failures.
The flow rate, measured in gallons per minute (GPM) or liters per minute (LPM), represents the volume of fuel that needs to be transported through the hose. Higher flow rates typically require larger hose diameters to ensure smooth and efficient fuel transfer. For instance, if your diesel engine operates at a high power output, generating a substantial amount of fuel flow, you will need a hose with a larger diameter to accommodate this volume without causing pressure drops or restricting the flow.
Pressure requirements are another critical factor. Diesel fuel systems often operate under high-pressure conditions to ensure efficient combustion. The hose must be able to withstand these pressures without compromising its structural integrity. Thicker hoses with larger diameters can handle higher pressure differentials, ensuring a reliable and safe fuel return system. It is essential to consult the manufacturer's guidelines or specifications for the recommended hose size based on the expected pressure levels in your diesel engine.
Additionally, consider the material of the hose. Different materials have varying pressure and temperature tolerances, which can influence the hose diameter selection. For instance, rubber hoses might have different performance characteristics compared to silicone or polyurethane hoses. Always choose a hose material that meets or exceeds the pressure and temperature requirements of your diesel fuel system.
In summary, when determining the hose diameter for a return diesel fuel line, focus on the flow rate and pressure needs of your system. Larger diameters are generally required for higher flow rates and pressure differentials. Remember to consult manufacturer guidelines and consider the hose material's properties to ensure a safe and efficient diesel fuel return system.
Best Sealant for Home Heating Oil Fuel Lines: A Comprehensive Guide
You may want to see also
Material: Select suitable material for durability and compatibility
When it comes to selecting the appropriate material for a return diesel fuel line, several factors should be considered to ensure durability and compatibility. The primary goal is to choose a material that can withstand the harsh conditions of diesel fuel, including its temperature, pressure, and chemical composition.
One of the most commonly used materials for fuel lines is rubber, specifically natural or synthetic rubber compounds. These rubbers are known for their flexibility, resilience, and ability to withstand the corrosive nature of diesel fuel. Natural rubber, in particular, has excellent resistance to abrasion and fatigue, making it a popular choice for fuel lines. However, it's important to note that natural rubber may not be as resistant to high temperatures as some synthetic rubbers.
Synthetic rubbers, such as neoprene or EPDM (Ethylene Propylene Diene Monomer), offer improved temperature resistance compared to natural rubber. These materials can handle the higher temperatures associated with diesel fuel, making them suitable for a wide range of applications. Additionally, synthetic rubbers often provide better chemical resistance, ensuring that the fuel line remains intact even when exposed to various additives and contaminants in the fuel.
Another consideration is the use of reinforced materials. Some fuel lines may benefit from the addition of fabric or fiber reinforcements, such as braided nylon or steel wire. These reinforcements provide enhanced strength and flexibility, making the hose more durable and capable of withstanding higher pressure. Reinforced hoses are particularly useful in applications where the fuel line may be subjected to vibrations or extreme bending.
In addition to rubber and reinforced materials, certain types of plastics can also be suitable for diesel fuel lines. For example, PVC (Polyvinyl Chloride) and PVDF (Polyvinylidene Fluoride) are known for their excellent chemical resistance and can be used in high-temperature environments. However, it's crucial to ensure that the chosen plastic material meets the specific requirements of diesel fuel compatibility.
In summary, when selecting the material for a return diesel fuel line, it is essential to consider the properties of the fuel, such as temperature and chemical composition. Natural and synthetic rubbers are commonly used due to their flexibility and resistance to abrasion. Reinforced materials and certain plastics can also be considered for added strength and chemical compatibility. The choice of material should be based on the specific demands of the application to ensure the longevity and reliability of the fuel line.
Fuel Line Sizes for 200 Bonneville: A Guide to Fuel Pumps
You may want to see also
Length: Measure and specify the required length for the hose
When determining the length of a hose for a return diesel fuel line, it's crucial to measure carefully to ensure optimal performance and safety. The length should be tailored to the specific application and the layout of the fuel system. Here's a step-by-step guide to help you with this process:
- Identify the Source and Destination: Begin by clearly understanding the source and destination of the fuel line. Locate the return fuel pump, which is typically found near the engine, and identify the fuel tank or the point where the fuel is re-entered into the system. This will give you an idea of the hose's starting and ending points.
- Measure the Distance: Use a measuring tape or a flexible measuring tool to determine the straight-line distance between the source and destination. Measure along the path the hose will take, ensuring you account for any bends or turns. It's important to get an accurate measurement to ensure the hose is not too short or too long.
- Consider Hose Routing: Think about the route the hose will take. Will it be suspended above the ground, run along the floor, or be partially buried? The routing can impact the hose's length and the overall system design. For example, if the hose needs to cross a large gap or be routed around obstacles, you may need to add extra length to accommodate these factors.
- Add Allowance for Bends and Connections: When calculating the required length, account for any bends or turns the hose will make. Bends can restrict flow and may require additional hose material. Also, consider the locations of any valves, filters, or other fuel system components that will require connections. Allow for these connections to ensure the hose is long enough to accommodate the entire system.
- Specify the Length: Based on your measurements and considerations, specify the required length of the hose. It's generally recommended to have a slightly longer hose than the calculated length to allow for any adjustments or changes during installation. Ensure that the specified length is communicated to the manufacturer or supplier to ensure you receive the correct hose size.
Remember, accurate measurements and careful planning will contribute to a well-functioning diesel fuel system. Always refer to the manufacturer's guidelines and recommendations for the specific application to ensure compatibility and safety.
Unveiling the Materials Behind Fuel Tank Lines
You may want to see also
Fittings: Ensure compatibility with fuel system connectors and fittings
When it comes to choosing the right hose for your return diesel fuel line, one crucial aspect often overlooked is the compatibility of fittings. The fuel system's intricate network demands precise connections to ensure optimal performance and safety. Here's a detailed guide on why fittings compatibility is essential:
Understanding the Fuel System: Diesel fuel systems are complex, with various components working in harmony. The return fuel line connects the engine to the fuel tank, allowing used fuel to be recirculated and filtered. Any disruption in this process can lead to reduced engine performance and potential damage. Therefore, the hose and fittings must be designed to handle the specific requirements of diesel fuel.
Fitting Compatibility: Fittings play a pivotal role in connecting hoses to the fuel system. These connectors must be compatible with the hose's inner diameter and thread size to ensure a secure and leak-free connection. Inadequate compatibility can result in fuel leaks, which are not only dangerous but can also lead to engine misfires and reduced power output. It is essential to refer to the manufacturer's specifications and diagrams to identify the correct fitting types and sizes.
Material Considerations: The choice of material for fittings is another critical factor. Diesel fuel can be harsh on certain materials, leading to degradation over time. Common materials used for fuel system fittings include stainless steel and brass, which offer excellent corrosion resistance and durability. Ensure that the fittings are made from materials that can withstand the chemical properties of diesel fuel to ensure long-term reliability.
Installation and Maintenance: Proper installation of fittings is as important as their compatibility. When installing the hose, ensure that the fittings are securely tightened to avoid any potential leaks. Regular maintenance, including checking for signs of wear and corrosion, will help identify any issues early on. Over time, fittings may require replacement due to wear or damage, so having a supply of compatible spare parts is advisable.
By paying close attention to fitting compatibility, you can ensure that your diesel fuel system operates efficiently and safely. It is a critical aspect that, when overlooked, can lead to costly repairs and potential safety hazards. Always consult the manufacturer's guidelines and consider the specific requirements of your diesel engine when selecting and installing the appropriate fittings.
Unveiling Stihl Fuel Line Material: A Comprehensive Guide
You may want to see also
Temperature Range: Consider operating temperatures to ensure hose longevity
When it comes to selecting the appropriate hose for a return diesel fuel line, understanding the temperature range is crucial for ensuring the hose's longevity and optimal performance. Diesel fuel lines are exposed to varying temperatures, especially in different climates and operating conditions. The operating temperature of a diesel engine can range from extremely cold, especially in winter, to very hot, especially during prolonged operation or in high-performance engines.
The temperature range of the hose should match the expected operating conditions of the fuel line. For instance, in cold climates, the hose must be able to withstand sub-zero temperatures to prevent cracking or freezing, which could lead to fuel line blockages or damage. On the other hand, in hot climates or when the engine is running at high temperatures, the hose should be able to handle the heat without degrading or becoming brittle.
Hoses designed for diesel fuel lines often have specific temperature ratings. These ratings indicate the maximum and minimum temperatures the hose can endure without compromising its structural integrity. It's essential to choose a hose with a temperature range that exceeds the expected operating temperatures to ensure it can handle the most extreme conditions. For instance, a hose rated for -40°C to 120°C (-40°F to 248°F) would be suitable for a wide range of climates and engine operating conditions.
Additionally, the material of the hose plays a significant role in its temperature resistance. Different materials have varying temperature tolerances. For example, rubber hoses are generally suitable for a wide temperature range, while some synthetic hoses, like those made from fluoropolymers, can handle even more extreme temperatures.
In summary, when selecting a hose for a return diesel fuel line, it is imperative to consider the operating temperature range. Choosing a hose with a temperature rating that matches or exceeds the expected operating conditions will ensure the hose's longevity, maintain the quality of the fuel, and prevent potential issues caused by temperature extremes. This consideration is a critical aspect of maintaining a reliable and efficient diesel fuel system.
Fuel Lines: Powering Your Snowmobile's Performance and Efficiency
You may want to see also
Frequently asked questions
The size of the hose for a return diesel fuel line is crucial for efficient and safe fuel transfer. The primary factors to consider are the flow rate of the fuel, the pressure requirements, and the overall system design. For high-flow applications, larger hoses with a higher diameter are recommended to handle the increased volume of fuel. Additionally, the pressure rating of the hose should match or exceed the system's operating pressure to ensure optimal performance and prevent damage.
Selecting the correct hose diameter involves balancing flow rate and pressure considerations. As a general rule, a larger diameter hose will provide higher flow capacity, allowing for faster fuel transfer rates. However, it's essential to consider the available space in your vehicle's fuel system and the overall design. Consult the manufacturer's specifications or seek expert advice to determine the optimal diameter based on your specific diesel engine's requirements.
Industry standards and guidelines provide a framework for selecting the right hose size. For diesel fuel return lines, it is common to follow recommendations from the engine manufacturer or industry associations. These guidelines often suggest hose diameters based on the engine's power output and fuel system design. It's important to refer to the specific requirements of your diesel engine and consult relevant standards to ensure compliance and optimal performance.