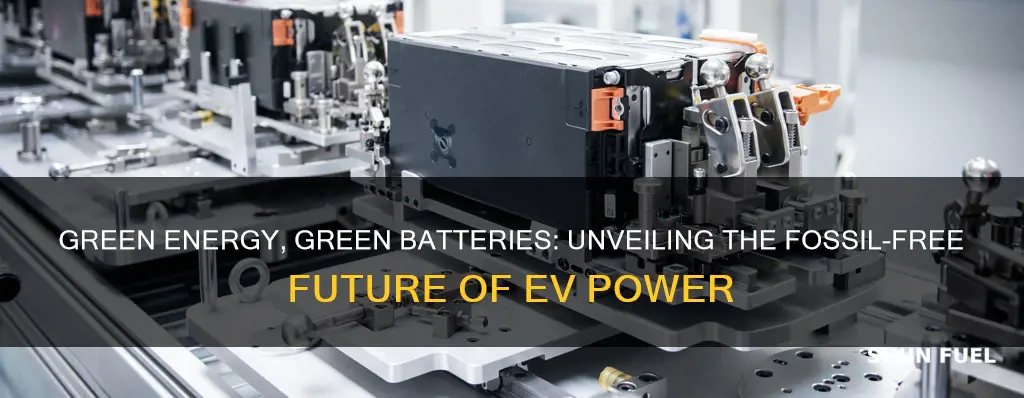
The production of electric vehicle (EV) batteries has sparked debates about its environmental impact, particularly regarding the use of fossil fuels. While EVs are known for their zero-emission driving experience, the manufacturing process of their batteries, which often involves rare earth metals and chemicals, has raised concerns. This paragraph aims to explore the relationship between electric car batteries and fossil fuels, examining whether the production of these batteries relies on non-renewable resources and the potential implications for the sustainability of the EV industry.
Characteristics | Values |
---|---|
Battery Type | Lithium-ion (Li-ion) |
Fossil Fuel Dependency | No, electric car batteries do not directly require fossil fuels for their manufacturing process. |
Raw Materials | Lithium, cobalt, nickel, manganese, graphite, and other minerals. |
Extraction and Processing | While the extraction and processing of these raw materials may have environmental impacts, they do not directly involve fossil fuels. |
Energy Source | The primary energy source for battery production is electricity, often generated from renewable sources like hydropower, wind, or solar power. |
Carbon Emissions | The manufacturing process of electric car batteries can have some carbon emissions, but it is significantly lower compared to traditional internal combustion engine vehicles. |
Recycling Potential | Electric car batteries can be recycled, and the recycling process can be more energy-efficient and environmentally friendly compared to primary production. |
Technological Advancements | Ongoing research and development aim to reduce the environmental impact of battery production, including the use of more sustainable materials and processes. |
What You'll Learn
- Battery Materials: Extraction of lithium, cobalt, and nickel from fossil fuel-dependent mining processes
- Refining Processes: Fossil fuels are used in refining and processing battery materials
- Energy-Intensive Manufacturing: Manufacturing electric car batteries requires significant energy, often from fossil fuels
- Carbon Footprint: The production of batteries contributes to greenhouse gas emissions
- Renewable Energy Transition: Shifting to renewable energy sources can reduce the reliance on fossil fuels
Battery Materials: Extraction of lithium, cobalt, and nickel from fossil fuel-dependent mining processes
The manufacturing of electric vehicle (EV) batteries relies on the extraction of critical materials such as lithium, cobalt, and nickel, which are often obtained through mining processes that have a significant environmental impact. These processes are indeed dependent on fossil fuels, which raises concerns about the sustainability and carbon footprint of EV battery production.
Lithium, a key component in lithium-ion batteries, is primarily extracted through a process called hard-rock mining. This method involves digging into the earth to access lithium-rich veins, often located deep underground. The mining process requires substantial energy, and the extraction and transportation of lithium-bearing ore are energy-intensive, typically relying on fossil fuels. The energy consumption in this stage contributes to the overall carbon emissions associated with lithium production.
Cobalt, another essential material for EV batteries, is predominantly sourced through mining in the Democratic Republic of Congo (DRC). The DRC's mining industry has been criticized for its heavy reliance on fossil fuels, particularly diesel, for both surface and underground operations. The extraction and processing of cobalt ore involve various stages, each demanding significant energy, often supplied by diesel generators. This fossil fuel-dependent process not only contributes to air pollution but also poses environmental risks, including water contamination and habitat destruction.
Nickel, a crucial component in the cathode of lithium-ion batteries, is also extracted through mining, with significant operations in countries like the Philippines and Indonesia. Similar to the cobalt mining process, nickel mining often utilizes diesel-powered equipment and transportation, leading to high energy consumption and associated carbon emissions. The extraction and refining of nickel require substantial energy, and the reliance on fossil fuels in these processes is a critical aspect of the environmental impact of EV battery manufacturing.
The extraction of these battery materials from fossil fuel-dependent mining processes has raised concerns about the long-term sustainability of the EV industry. As the demand for electric vehicles grows, so does the need for these materials, potentially increasing the environmental impact. Transitioning to more sustainable extraction methods, such as developing more efficient mining techniques and exploring alternative energy sources, is essential to reduce the carbon footprint of EV battery production.
88 Octane Fuel: Is It Safe for Your Car?
You may want to see also
Refining Processes: Fossil fuels are used in refining and processing battery materials
The manufacturing of electric car batteries involves a complex process that often relies on fossil fuels, particularly in the refining and processing stages of battery material production. This is an essential step in the supply chain, as it ensures the purification and transformation of raw materials into the high-performance components required for electric vehicle (EV) batteries.
One of the primary refining processes involves the extraction and purification of lithium, a critical element in lithium-ion batteries. The lithium extraction process typically starts with lithium-rich minerals, such as lithium carbonate or lithium hydroxide. These minerals are obtained from mining operations, and the initial refining step often utilizes fossil fuels to power the energy-intensive processes. For instance, the production of lithium carbonate from lithium ore requires significant energy, and this energy is often sourced from coal-fired power plants, which burn fossil fuels. This initial refining stage is crucial to obtaining the high-purity lithium needed for battery manufacturing.
Moving further in the refining process, the purified lithium is then processed into various forms suitable for battery production. This includes the creation of lithium metal, lithium salts, and lithium-based compounds. These processes often involve chemical reactions and energy-intensive steps, which are typically powered by fossil fuels. For example, the production of lithium metal involves electrochemical processes that require substantial energy input, often supplied by fossil fuel-based power sources.
Additionally, the manufacturing of other battery materials, such as cobalt, nickel, and manganese, also relies on fossil fuels. These metals are extracted from their ores and then refined to produce the high-purity materials needed for batteries. The refining processes often involve smelting, roasting, and other thermal treatments, which are energy-intensive and typically powered by fossil fuels. The use of fossil fuels in these refining stages is a significant consideration in the environmental impact of EV battery production.
In summary, the refining and processing of battery materials for electric car batteries are integral steps that often depend on fossil fuels. From lithium extraction to the production of various battery components, these processes contribute to the overall energy consumption and environmental footprint of EV battery manufacturing. As the demand for electric vehicles grows, it becomes increasingly important to explore and adopt more sustainable and renewable energy sources to reduce the reliance on fossil fuels in the battery production supply chain.
Fuel Treatments: Friend or Foe for Your Car's Health?
You may want to see also
Energy-Intensive Manufacturing: Manufacturing electric car batteries requires significant energy, often from fossil fuels
The production of electric car batteries is an energy-intensive process, and unfortunately, a significant portion of this energy still relies on fossil fuels. This is a critical aspect often overlooked in the broader discussion about the environmental benefits of electric vehicles (EVs). The manufacturing process involves multiple stages, each demanding substantial energy, and the sources of this energy can have a substantial environmental impact.
One of the primary reasons for the high energy requirement is the complex chemistry involved in battery production. Lithium-ion batteries, the most common type used in EVs, are made through a series of intricate chemical reactions. These reactions demand high temperatures and specific conditions, often provided by energy-intensive processes. For instance, the production of lithium-ion cells involves the use of heat treatment processes, which are typically energy-intensive and can be powered by fossil fuels, especially in regions where the electricity grid is not entirely renewable.
The manufacturing process also includes the extraction and processing of raw materials. Lithium, for example, is extracted through a process that often requires substantial energy input, and in some cases, this energy may still come from fossil fuel-based power plants. The same goes for the production of other critical components like cobalt and nickel, which are essential for the cathode and anode materials in batteries. The energy-intensive nature of these extraction and processing steps means that the environmental footprint of battery manufacturing is far from zero.
Furthermore, the infrastructure required to support the manufacturing process contributes to the overall energy demand. Building and maintaining the facilities, including assembly lines and chemical processing units, require significant energy. This energy is often sourced from power grids that may still rely on fossil fuels, especially in regions with a high demand for manufacturing capacity. As a result, the environmental impact of producing a single electric car battery can be substantial, especially when considering the entire lifecycle of the vehicle.
Addressing this issue requires a multi-faceted approach. Firstly, improving the efficiency of the manufacturing process can reduce energy consumption. Secondly, transitioning to renewable energy sources for powering these manufacturing processes is crucial. Many countries and companies are already investing in renewable energy infrastructure to support the EV industry, which is a positive step towards mitigating the environmental impact of battery production.
Glow Plug RC Car Fuel: Powering Your Next Adventure
You may want to see also
Carbon Footprint: The production of batteries contributes to greenhouse gas emissions
The manufacturing process of electric vehicle (EV) batteries is a complex and energy-intensive operation, which has raised concerns about its environmental impact, particularly in terms of carbon emissions. The production of these batteries, especially those used in electric cars, often relies on a supply chain that includes various fossil fuel-based processes.
One significant aspect is the extraction and processing of raw materials. Lithium, a key component in lithium-ion batteries, is primarily obtained through mining, a process that can be energy-intensive and often requires large amounts of electricity, some of which may still be generated by fossil fuels. For instance, the extraction and refining of lithium often involve the use of coal-fired power plants, contributing to greenhouse gas emissions. Similarly, the production of other battery materials, such as nickel, cobalt, and graphite, also involves energy-intensive processes, some of which are dependent on fossil fuel-based energy sources.
The manufacturing process itself is another area of concern. Battery production requires a significant amount of energy, often supplied by electricity grids that may still have a substantial reliance on fossil fuels. The production lines for batteries, including the assembly and the various chemical processes involved, can release substantial amounts of carbon dioxide and other greenhouse gases. This is particularly true for the older, less efficient production methods, which may have a higher environmental impact.
Furthermore, the transportation of raw materials and battery components over long distances can also contribute to the carbon footprint. The global supply chain for EV batteries is extensive, with materials sourced from various regions and then transported to manufacturing facilities worldwide. This transportation network often relies on fossil fuel-powered vehicles and shipping, adding to the overall emissions associated with battery production.
Addressing the carbon footprint of battery manufacturing requires a multi-faceted approach. It includes transitioning to renewable energy sources for both raw material extraction and manufacturing processes, improving energy efficiency in production, and optimizing supply chains to reduce transportation-related emissions. By implementing these strategies, the industry can work towards minimizing its environmental impact and contributing to a more sustainable future for electric vehicles.
Mastering the Art of Fuel Transfer: A Step-by-Step Guide
You may want to see also
Renewable Energy Transition: Shifting to renewable energy sources can reduce the reliance on fossil fuels
The transition to renewable energy sources is a crucial step in reducing our reliance on fossil fuels and mitigating the environmental impact of energy production. This shift is particularly important in the context of the transportation sector, where the widespread adoption of electric vehicles (EVs) has the potential to significantly lower carbon emissions. One area of focus in this transition is the manufacturing process of electric car batteries, as it has been a subject of debate regarding its energy requirements.
Electric vehicle batteries, primarily lithium-ion batteries, are complex systems that power these vehicles. The manufacturing process involves various stages, including raw material extraction, processing, assembly, and testing. Interestingly, the production of these batteries has traditionally relied on non-renewable energy sources, such as coal and natural gas, for electricity generation. This is a critical aspect that needs addressing to ensure the overall sustainability of the EV industry.
To address this challenge, the renewable energy transition plays a pivotal role. By shifting to renewable energy sources, such as solar, wind, and hydropower, the electricity used in battery manufacturing can be generated in a cleaner and more sustainable manner. Governments and industries are increasingly investing in renewable energy infrastructure, which can power the entire manufacturing process, from raw material extraction to the final assembly of batteries. This approach not only reduces the carbon footprint of the EV industry but also ensures a more consistent and reliable energy supply for the manufacturing sector.
The benefits of this transition are twofold. Firstly, it directly contributes to the reduction of greenhouse gas emissions, which is a primary goal in combating climate change. By using renewable energy, the manufacturing process becomes more environmentally friendly, minimizing the impact on air quality and ecosystems. Secondly, it promotes energy security and independence. With renewable energy sources, countries can reduce their reliance on finite fossil fuel reserves, ensuring a more sustainable and long-term energy supply for the EV battery production industry.
In summary, the renewable energy transition is a powerful strategy to address the environmental concerns associated with electric car battery manufacturing. By embracing renewable sources, the industry can significantly reduce its carbon emissions and contribute to a cleaner, more sustainable future. This shift also encourages innovation and investment in green technologies, fostering a more resilient and environmentally conscious economy. As the world moves towards a greener transportation system, the integration of renewable energy in battery manufacturing will be a key enabler in this transformative journey.
Fuel Injection and Aspiration: A Possible Hybrid?
You may want to see also
Frequently asked questions
No, electric vehicle (EV) batteries do not need fossil fuels for manufacturing. The production of lithium-ion batteries, which are commonly used in EVs, primarily involves the extraction and processing of raw materials such as lithium, cobalt, nickel, and manganese. These materials are sourced through mining and refining processes, which can be energy-intensive but do not directly depend on fossil fuels.
The materials for EV batteries are obtained through various mining and refining techniques. Lithium, for example, is often extracted from brine reservoirs or hard-rock mines. Cobalt and nickel are typically sourced from mineral deposits, while manganese can be obtained from various mineral sources. These raw materials are then processed to create the battery cells and components.
While the primary materials for EV batteries are not derived from fossil fuels, there can be indirect dependencies. The energy-intensive processes involved in refining and processing these materials may rely on electricity generated from fossil fuel-based power plants. However, many countries and regions are transitioning to renewable energy sources for electricity production, reducing the environmental impact of EV battery manufacturing.
Absolutely! The EV industry is actively working towards more sustainable practices. This includes developing recycling processes to recover materials from end-of-life batteries, reducing the environmental impact of mining, and transitioning to renewable energy sources for power generation. Additionally, research and development efforts focus on finding more efficient and environmentally friendly ways to produce battery materials, making the manufacturing process more sustainable over time.